Titel: | Ueber die Anfertigung der Hartwalzen von Gußeisen, nach der Methode der kaiserl. russischen Gießerei zu Kamensk. |
Fundstelle: | Band 82, Jahrgang 1841, Nr. X., S. 31 |
Download: | XML |
X.
Ueber die Anfertigung der Hartwalzen von
Gußeisen, nach der Methode der kaiserl. russischen Gießerei zu Kamensk.
Aus dem Annuaire du Journal des mines de Russie. 1836, S.
145.
Mit Abbildungen auf Tab.
I.
Ueber die Anfertigung der Hartwalzen.
Bis zum Jahre 1830 goß die Gießerei zu Kamensk die Walzen für die Ekaterineburger
Münze in Sandformen und ließ das Metall von Oben in sie einlaufen; wenn die Walze
nach dem Herausnehmen aus der Form als gelungen erklärt wurde, so lieferte man sie
an die Münze ab. Der Hauptkörper und die beiden Hälse der Walze wurden alsdann auf
einer gewöhnlichen Drehbank abgedreht, und nachdem die Walze ihre richtige Form
erhalten hatte, wurde sie in ein Walzwerk eingelegt. Die nach diesem Verfahren
gegossenen Walzen waren aber nicht dauerhaft, und ihre Oberflaͤche nicht
gleichförmig; während des Walzens, wo sie der Einwirkung des in den Kupferstangen
enthaltenen Kupferoxyduls ausgesezt waren, verdarben sie bald, so daß sie nach jeder
Arbeitszeit von 12 Stunden und oft noch früher auf der Drehbank wieder abgerichtet
werden mußten. Dieser Umstand zog große Nachtheile nach sich; 1) der Dreher, welcher
die Ausbesserung derselben auf dem Walzengestelle selbst vornahm, war durch die
einzelnen Theile der Maschine, so wie auch durch die zur Reparatur bestimmte Zeit
gehindert, diese Arbeit mit der ganz besondern Genauigkeit vorzunehmen, welche bei
diesen Walzen durchaus erforderlich ist. 2) Wenn die Walzen auf dem Walzwerk
eingesezt werden, haben sie anfangs beide gleichen Durchmesser, durch die in der
Folge nothwendigen Reparaturen werden sie aber in verschiedenem Grade abgedreht und
behalten daher nicht mehr gleiche Dike, was der Regelmäßigkeit des Ganges der
Maschine schadet. 3) Jedes Walzenpaar wurde unbrauchbar, nachdem einmal 3000 bis 5000 Pud Kupfer
damit gewalzt waren, was die Kosten sehr steigerte.
Um diese Nachtheile zu beseitigen, schlug die Administration der Münze im Jahre 1830
vor, die Walzen in eisernen Formen zu gießenDas Gußeisen besizt bekanntlich die Eigenschaft, durch Abschreken, indem es durch plözliches
Abkühlen aus dem flüssigen Zustand schnell in den festen übergeht, dichter
und härter zu werden, und diese Eigenschaft desselben wurde auch schon
längst benuzt, um bei einzelnen Theilen einer Gußwaare diesen Zustand
hervorzubringen; den Engländern aber gebührt das Verdienst, diese Erfahrung
bei der Darstellung gegossener eiserner Walzen zuerst benuzt zu haben. Indem
sie zur Gußform des Walzenkörpers einen
hinreichend starken gußeisernen Cylinder anwandten, die Zapfen daran aber in der gewöhnlichen Formmasse
formten, erreichten sie den Zwek, den Zapfen und dem Kern des Walzenkörpers
die der Natur des zum Guß angewendeten Roheisens zukommende Festigkeit zu
erhalten, während die Oberfläche des Walzenkörpers durch das Abschreken
mittelst der gußeisernen Schale härter und dichter wird.A. d. R. und das flüssige Eisen von Unten in die Form zu führen. Fig. 9 zeigt einen
verticalen Durchschnitt der eisernen Form; Fig. 10 zeigt die Form
von Außen nebst ihren einzelnen Theilen.
a die gußeiserne Form.
b die Form von Oben angesehen.
c Ober- und Untertheil der Form; man füllt sie
mit Sand, um die Enden der Walze darin einzuformen.
d eine Oeffnung im untern Theile der Form, womit ein
Canal von Lehm verbunden ist, um das flüssige Metall in die Form zu führen.
f Scheiben von Gußeisen, welche von beiden Seiten auf
die Form geschraubt werden; der Durchmesser ihrer Oeffnungen ist so groß als
derjenige der Walzenzapfen.
k eine der Scheiben von Oben angesehen.
l ein Modell von Holz nach der Walze geformt; um das
Einformen zu erleichtern, ist einer der Zapfen zum Abnehmen gerichtet.
Wenn man das Abformen beginnt, läßt man zuerst das Modell von Holz in die Form ein,
sezt die Scheiben und die Außentheile auf und richtet die Form, wenn alles durch
Schrauben verbunden ist, vertical; man formt nun die Zapfen der Walze ein, indem man
den Raum zwischen dem Holz und dem gußeisernen Aufsaze mit Formsand ausfüllt und
einstampft. Die gußeisernen Scheiben f dienen dabei dem
Sande als Boden. Hierauf nimmt man die Aufsäze zugleich mit den Scheiben von der
Form ab, zieht das Modell von Holz heraus und troknet die eingeformten Enden.
Nachdem die Aufsäze mit der Form wieder wie vorher verbunden worden sind, bringt man
mit der Oeffnung des untern Aufsazes den Canal e von
Lehm in Verbindung, und die Form ist bereit das Eisen aufzunehmen.
Im Jahre 1830 goß man zuerst ein Paar Walzen zum Feinwalzen in gußeiserne Formen;
ihre Zapfen waren so weich, daß man sie mit stählernen Meißeln abdrehen konnte, der
Walzenkörper selbst aber wurde vom Stahl nicht angegriffen und mußte mit Schmirgel
geschliffen werden. Diese günstigen Eigenschaften rechtfertigten die Anwendung der
gußeisernen Formen vollkommen, allein die Oberfläche der gegossenen Walzen war noch
immer unrein und mit ziemlich tiefen Gruben übersäet. Es ist klar, daß diese Fehler
durch die Unreinigkeiten entstanden, welche das flüssige Eisen bedekten; denn die
Eisenoxyde, ein Theil Schlaken und die Erdtheilchen, womit das flüssige Roheisen
beim Durchgang durch den Canal und durch den Sand des Untertheiles der Form in
Berührung kommt, befinden sich in Folge ihres specifischen Gewichtes auf der
Oberfläche des flüssigen Metalles, steigen zuerst in die Form und gehen durch die
ganze Höhe derselben; in dem Maaße aber, als das flüssige Metall steigt, hängen sich
diese Theile an den innern Wänden der Form an, so daß das Eisen, wenn es in die Höhe
steigt, die Seitenwände der Form von diesen Unreinigkeiten schon bedekt findet. Da
diese Unreinigkeiten zwischen der Seitenwand der Form und dem flüssigen Metall sizen
bleiben, so muß die Oberfläche der Walze sämmtliche Eindrüke derselben anfnehmen,
und also voller Gruben erscheinen.
Um während des Gießens den schädlichen Einfluß der fremden Körper, welche die
Oberfläche des flüssigen Metalles bedeken, zu vermeiden, schlug man vor, einen
Cylinder von dünnem Blech anzuwenden, welcher über dem untern Ende der Walze ins
Innere der Form eingesezt werden sollte. Die Oberfläche des Blechcylinders wurde mit
Löchern versehen, welche mit dem Meißel eingehauen wurden, damit das Gas, welches
sich während des Gießens entwikelt, durch sie entweichen konnte. Auf diese Art
wollte man den Schaum und alle Unreinigkeiten, welche sich auf der Oberfläche des
flüssigen Eisens befinden, nöthigen, nach dem Durchgehen durch die Sandform sich in
den Cylinder zu begeben, statt in die Form durchzudringen. In dem Augenblik, wo das
reine Metall anfängt in die Form einzutreten, erhebt man nach und nach den Cylinder
in dem Maaße als das Eisen in der Form steigt, und sobald dasselbe am obern Ende der
Form ankommt, hebt man schnell den Cylinder weg und mit ihm alle Unreinigkeiten,
welche sich darin angesammelt haben.
Die Versuche, welche auf diese Art gemacht wurden, lieferten Walzen mit ebener
Oberfläche, sie ergaben aber auch, daß man den Cylinder während des Gießens
unmöglich aus der Form ziehen kann, sondern daß derselbe in der Mitte der Walze
steken bleibt und Lüken und Gruben im Innern derselben erzeugt.
Dadurch kam man auf die Idee, statt des Cylinders zu demselben Zwek eine Vorrichtung
anzuwenden, deren Gestalt das Herausziehen aus der Form begünstigen würde. Man nahm
dazu einen abgestuzten Kegel, als am meisten geeignet, den vorgesezten Zwek zu
erfüllen, und seit dieser Zeit bedient man sich desselben mit dem besten Erfolg. Der
Kegel m ist in Fig. 9 dargestellt; er
wurde aus dünnem Blech gemacht. Auf seiner Seitenfläche sind mit dem Meißel kleine
Löcher eingehauen; der Durchmesser der großen Basis n
des Kegels ist etwas größer als der untere Durchmesser o
des Walzenzapfens, und kleiner als der Durchmesser des obern Endes p; r ist ein Steg von dünnem Eisen, welcher an der obern
Basis des Kegels fest ist. An diesem Steg ist eine Eisenstange q befestigt, damit der Kegel seine verticale Stellung
nicht verliert.
Wenn das Ganze zusammengestellt ist, schreitet man zum Gießen. Das für die Walze
bestimmte flüssige Gußeisen, indem es durch den Lehmcanal und die Lehmform am untern
Theile der Walze geht, treibt die erdigen Theile, welche sich mit den Metalloxyden
und einem Theil Schlake auf seiner Oberfläche befinden, vorwärts. Diese fremden
Körper erheben sich bis in die Mitte der Form und steigen dann in den schüzenden
Kegel empor, welcher sie rings umhüllt und sie dadurch verhindert, mit den
Seitenwänden der Form in Berührung zu kommen. So wie das Eisen sich dann nach und
nach erhebt, treibt es die Unreinigkeiten, welche in dem Kegel eingeschlossen sind,
in die Höhe, und in dem Augenblik, wo der Hauptkörper der Walzenform mit Metall
gefüllt ist, hebt man schnell den Kegel an der Eisenstange heraus, und die fremden
Körper, welche dem Gusse schaden können, und die der Kegel aufgenommen hat, gehen
mit ihm heraus. Alsdann kommt das flüssige Metall erst in Berührung mit der Kapsel,
welche vollkommen rein geblieben ist, und nimmt beim Erkalten eine so glatte Fläche
wie sie an. In dem Maaße als das Eisen sich erhebt, drükt es gegen die innere
Oberfläche des abgestuzten Kegels und nöthigt diesen zu steigen, wodurch es das
Herausziehen desselben erleichtert.
Die so mittelst Anwendung des abgestuzten Kegels aus Roheisen gegossenen Cylinder
erfüllen alle Bedingungen, welche man von den Walzen für die Strekwerke der Münzen
etc. fordert; ihre Zapfen bestehen aus weichem Roheisen und lassen sich mit
stählernen Meißeln drehen, daher das Einpassen derselben in ihre Zapfenlager und in
die Zahnräder des Walzwerkes sehr leicht ist. Der Walzenkörper selbst wird seiner
großen Härte wegen mit Schmirgel behandelt; seine glatte Oberfläche erfordert
geringere Zeit zum Poliren und verursacht folglich keine großen Kosten zu ihrer
Vollendung; eine ganz vollendete Walze für das Feinwalzwerk in der Münze mit Einschluß der
Fabricationskosten und dem Ankaufe des Eisens kommt auch wirklich nur auf 42 Rubel
und 3 Kopeken zu stehen.
Die nach dem beschriebenen Verfahren bisher verfertigten gußeisernen Walzen, welche
zum Streken kleiner Kupferstäbe auf dem Feinwalzwerke angewendet wurden, haben sich
als merkwürdig dauerhaft gezeigt. So wurden auf einer derselben in 138 Arbeitstagen
(zu 12 Stunden) 73600 Pud Kupferzaine und auf einer anderen in 196 Arbeitstagen
78400 Pud bearbeitet.
Nachdem man sich von der anhaltenden Dauerhaftigkeit der in Kapseln gegossenen
Walzen, welche bei dem Feinwalzwerke angewendet wurden, überzeugt hatte, ließ man
zum erstenmale im Jahre 1835 nach demselben Verfahren vier Walzen gießen, um
glühende Kupferbarren auf dem Grobwalzwerk damit zu walzen; nach 156 Arbeitstagen
waren sie noch ganz unversehrt.
Das Verfahren beim Gießen der Walzen zu den Grobwalzwerken ist ganz ähnlich dem zum
Gießen der Feinwalzen angewandten, mit der Ausnahme, daß die Grobwalzen größer sind,
und daher Formen von größeren Dimensionen erfordern. Uebrigens soll die untere
Walze, um das erste Einführen der Kupferzaine zu erleichtern, genau in der Mitte
einen kleinen Einschnitt von 2 1/2 Werschoks Breite und 1/8 Werschoks Tiefe haben,
dem eine Erhöhung auf der innern Fläche der Kapsel entspricht. Deßwegen mußte die
eiserne Form aus zwei Theilen gemacht werden, welche die Form eines Cylinders haben,
der durch eine durch seine Achse gehende Ebene in zwei gleiche Theile zerschnitten
ist. Zur Zeit des Gießens werden die beiden Formhälften durch Schrauben mit Muttern
zusammengehalten. Die obere Walze des Grobwalzwerkes hat hingegen eine vollkommen
ebene Oberfläche und wird gerade so in eine ganze Form gegossen, wie die Walzen zu
den Feinwalzwerken.
Zusaz.
Die Engländer haben sich bekanntlich zuerst damit beschäftigt, Walzen zu allen Arten
von Blechwalzwerken in Kapseln von Gußeisen zu gießen; es ist jedoch nicht bekannt
geworden, welche Mittel sie anwenden, um die Oberflächen glatt und ohne Poren zu
erhalten.
Im Jahre 1820 sezte der Verein zur Beförderung des Gewerbfleißes in Preußen einen
Preis von 200 Thlr. und einer goldenen Denkmünze für die Lösung der Aufgabe:
fehlerfreie Hartwalzen zu gießen, aus. Von der Zeit an wurden nun in vielen
Gießereien Versuche zu diesem Zweke angestellt; sie führten aber Jahre lang zu
keinem günstigen Resultate, weil man die auf dem Eisen schwimmenden Unreinigkeiten von der innern
Oberfläche der Form nicht abzuhalten vermochte, bis es endlich im Jahre 1831 einem
geschikten Formermeister der königl. Eisengießerei zu Berlin, Namens Erhard, gelang, durch ein höchst einfaches Verfahren,
welches von dem oben beschriebenen, in Rußland angewandten ganz abweicht, diese
Schwierigkeit zu beseitigen. Er erzeugte nämlich durch eine Abänderung der
Einmündung des Eingusses in dem aufsteigenden flüssigen Eisen eine kreisende
Bewegung, wodurch die auf der Oberfläche schwimmenden Unreinigkeiten von den Wänden
der Kapsel ab und in die Mitte getrieben wurden.
Nach einer Reihe von VersuchenSie sind ausführlich beschrieben in einer Abhandlung des Hrn. Berghauptmanns
Martins in den Verhandlungen des preußischen
Gewerbevereins 1834, S. 66, aus welcher das Nachfolgende gezogen
ist. gelang es dem königlichen Ober-Bergamt für die
brandenburg-preußischen Provinzen, mit Hülfe dieses Verfahrens vollkommen
reine und rizenfreie Hartwalzen zu gießen.
Die Figuren 1
bis 7 auf Tab.
I zeigen die Form mit allen einzelnen Theilen, welche zum Gießen einer 10 Zoll
langen Hartwalze angewandt wurde.
Fig. 1 die
gußeiserne cylindrische Kapsel; die Ringe a und b sind von Schmiedeisen und werden glühend aufgetrieben,
um das Zerspringen der Kapsel zu verhüten. Die Lappen c,
c dienen zur Verbindung des obern Formkastens mit der Kapsel.
Fig. 2 der
obere Formkasten zum Einformen des obern Walzenzapfens und des verlornen Kopfes, in
Sand.
Fig. 3 der
untere Formkasten, aus zwei Theilen a und b bestehend.
Fig. 4 das
hölzerne Gestell, welches beim Einformen in die Kapsel gestellt wird.
Fig. 5 die
hölzernen Formmodelle: a zu den obern Zapfen und dem verlornen Kopfe, b zu dem untern Walzenzapfen, c zu dem untern Kuppelungszapfen, d zu der Verbindungsröhre.
Fig. 6
Grundriß, welcher die Gestalt des Eingusses sehen läßt.
Fig. 7
Längendurchschnitt der Gußvorrichtung.
Fig. 8 die
fertige und abgedrehte Walze.
Die Kapsel A wurde in der Gestalt eines hohlen 10 Zoll
langen Cylinders von gutem grauem, weichem Kohks-Roheisen gegossen und zu
einem Durchmesser von 5 5/16 Zoll ausgebohrt; nach der Vollendung hatte sie 1 3/8
Zoll Eisendike, an jedem Ende aber auf 1 1/2 Zoll Länge einen Einschnitt von 1/4
Zoll, um welchen ein 1 1/2 Zoll breiter, 1 7/8 Zoll starker Ring von zähem Schmiedeisen gelegt
wurde; die angeschmiedeten Lappen c, c hatten Löcher von
3/4 Zoll Durchmesser zur Verbindung mit dem obern Formkasten; in den untern Ring
wurden drei Löcher d von gleichem Durchmesser 1 Zoll
tief gebohrt, in welche drei aus der Dekplatte des untern Formkastens emporstehende
correspondirende Stifte paßten (Fig. 1).
Der obere cylindrische Formkasten von Gußeisen, bestimmt für die vereinigte Form des
obern Zapfens und des verlornen Kopfs, Fig. 2, hatte 10 Zoll
Höhe, 8 Zoll Durchmesser im Lichten und 1/2 Zoll Eisenstärke; an jedem Ende war er
im Guß mit einem 3 Zoll breiten, 5/8 Zoll starken Rande versehen; durch den untern
Rand wurden vier Löcher von 1/2 Zoll Durchmesser, correspondirend mit den Löchern
des obern Kapselrings gebohrt. Vier geschmiedete Bolzen machten die Verbindung des
Formkastens mit der Kapsel; der 1/2 Zoll starke Hals der Bolzen paßte genau in die
Löcher am Rande des erstern, und, über denselben hinaus mit einem Schraubengewinde
versehen, wurde er mittelst einer Mutter daran festgeschraubt; der untere 3/4 Zoll
starke, mit einem Splintloch versehene Theil der Bolzen wurde beim Aufsezen des
Formkastens auf die Kapsel durch die in den Lappen des obern Kapselrings
angebrachten Löcher hindurchgelassen, und die Verbindung zwischen Kapsel und
Formkasten durch Vorschlagung der Splinte vollendet. Das in diesen Formkasten
einzuformende Modell hatte die Gestalt eines abgestumpften Kegels von 4 3/4 Zoll
unterm und 4 Zoll oberm Durchmesser und 10 Zoll Höhe, wovon nach Abzug von 5 1/2
Zoll für den Walzen- und Kuppelungszapfen noch 4 1/2 Zoll für den verlornen
Kopf blieben.
Der untere Formkasten von Gußeisen (Fig. 3) hatte im
Durchschnitt der Höhe die Gestalt eines länglich-vierekigen Rahmens von 20
3/4, Zoll Länge, 15 3/4 Zoll Breite und 1/2 Zoll Eisenstärke; der Höhe nach
getheilt, war der für den untern Walzenzapfen und den Einguß bestimmte obere Theil 2
3/8 Zoll hoch, am obern Rand in der Mitte jeder Seite mit einem Lappen, am untern
Rande an jeder langen Seite mit zwei Lappen versehen; durch jeden Lappen ein Loch
gebohrt. Eine Dekplatte, welche mittelst vier Schraubensplintbolzen auf die vorher
bemerkte Weise auf dem obern Formkastentheil befestigt wurde, war an der für die
Form des Wellzapfens bestimmten Stelle von einer 6 1/2 Zoll weiten runden Oeffnung
durchbrochen, um welche im Dreiek drei hervorstehende Stifte eingeschraubt waren,
die, wenn die Kapsel aufgesezt wurde, in die vor deren untern Stirn eingebohrten
drei correspondirenden Löcher paßten. Vom Mittelpunkt jener Oeffnung 8 1/2 Zoll
entfernt, war der Mittelpunkt einer zweiten kleinern runden Oeffnung von 3 Zoll
Durchmesser in der Dekplatte, um die Verbindungsröhre des Einfallrohrs mit dem Einguß
hindurchzulassen. Der untere Theil des Formkastens, 6 Zoll hoch, für den untern
Kuppelungszapfen bestimmt, hatte, correspondirend mit den vier Lappen am untern
Rande des obern Theils, am obern Rand ebenfalls vier Lappen, durch deren Löcher der
Hals von Schraubensplintbolzen hindurchgelassen und von Unten mittelst
Schraubenmuttern befestigt wurde, während der stärkere Theil des Bolzens über dem
Lappen emporstand, um beim Aufsezen des obern Formkastentheils durch die erwähnten
vier Lappenlöcher desselben hindurchzureichen, und mittelst vorgeschlagener Splinte
beide Formkastentheile miteinander zu verbinden.
Das Modell zum untern Kuppelungszapfen hatte die Gestalt einer vierseitigen Säule von
2 1/2 Zoll Breite der Seiten und 4 Zoll Höhe, ließ also von der 6zölligen Höhe des
untern Kastentheiles noch 2 Zoll für die untere Massedike der Form; das Modell zu
dem untern Wellzapfen, die Gestalt eines abgestumpften, umgekehrten, 3 Zoll hohen
Kegels, dessen kleinerer Durchmesser 3 1/2 Zoll, der größere 1 3/4 Zoll, gleich dem
zu dem obern Wellzapfen, betrug. Die Formen zu beiden Wellzapfen erhielten also da,
wo sie sich an die 5 5/16 Zoll weite Kapsel anschlossen, einen um 9/16 Zoll
geringern Durchmesser, als leztere, welcher beim Guß dem Eisen in den Zapfenkegeln
einen hinreichenden Spielraum übrig ließ, um dem in der Kapsel früher und stärker
schwindenden Eisen des Walzenkörpers zu folgen. Dem Gestell Fig. 4, welches beim
Formen der Zapfen in die Kapsel gestellt wird, war nur gerade die Höhe der leztern
gegeben; es wurde also kein Theil des Walzenkörpers, wie bei den größern Hartwalzen,
in Masse geformt, weil bei der geringern Länge desselben kein Theil des
Walzenkörpers der Abschrekung entzogen werden durfte. Die Formmasse wurde aus fünf
Maaßtheilen Lehm und zwei Maaßtheilen etwas grobkörnigen Sand zusammengesezt.
Beim Einformen des oberen Formkastens wurde die eiserne Kapsel auf eine horizontale
Unterlage gestellt, das hölzerne Gestell Fig. 4 eingesezt; der
Zapfen-Formkasten mittelst der Bolzen und Splinte auf der obern Stirn der
Kapsel befestigt; das mit hölzernen Zapfen am Boden versehene Modell zu dem
Walzen- und Kuppelungszapfen Fig. 5a, mittelst der in correspondirende Löcher der obern
Gestellscheibe passenden Zapfen e, e, auf der leztern in
die richtige, genau senkrechte Stellung gebracht und durch ein Gewichtstük
beschwert; der Raum zwischen dem Modell und dem Formkasten mit einer aus der Hälfte
Lehm und der Hälfte groben Mauersand zusammengesezten, nicht zu fetten Formmasse,
die in Schichten von 4 bis 5 Zoll Höhe eingetragen und mittelst eiserner
Stampfkeulen fest eingestampft wurde (wobei man jede Schichte durch Auflokern der Oberfläche mit der
folgenden verband) ausgefüllt und die Oberfläche ganz glatt ab-, auch um das
Modell herum noch besonders mit dem Streichblech festgestrichen. Weil die Formmasse
nicht zu feucht seyn darf, so pflegt man, damit sie besser an den Wänden des
Formkastens hafte, diese vor dem Aufsezen des leztern mittelst eines Pinsels mit
Wasser zu benässen. Der eingeformte Formkasten wurde dann von der Kapsel abgehoben,
wobei das Modell in der Form verbleibt; hierauf wurde die Kapsel selbst, mit dem
darin befindlichen Gestell, umgekehrt auf dieselbe Unterlage gestellt.
Zum Einformen des untern Formkastens wurde zuerst dessen oberer Theil Fig. 3a mit der daran befestigten Dekplatte f auf die mit dem Gestell versehene Kapsel gelegt, und unter dem Theil,
welchen die Oeffnung für die Verbindungsröhre enthält, durch einen Holzkloz von
gleicher Höhe mit der Kapsel unterstüzt. Die runde Verbindungsröhre Fig. 5d von 1 1/4 Zoll Durchmesser wurde, gleich Wie der Kegel Fig. 5b zur untern Walzenzapfenform, über ein
Holzmodell in Masse eingeformt und, nachdem die Oberfläche der Masse in der Höhe des
obern Kastentheils mit dem Streichbrett gerade abgestrichen, und mit dem
Streichblech geglättet worden, der untere Kastentheil Fig. 3b auf den obern befestigt, das mit Zäpfchen versehene Holzmodell
zu dem Kuppelungszapfen Fig. 5c, auf die mit correspondirenden Löchern versehene Stirnfläche
des Walzenzapfenmodells aufgesezt, beschwert, die Massefläche des obern Kastentheils
mit trokenem Streusand bestreut, und das Kuppelungszapfenmodell eingeformt.
Nach Vollendung dieser Form wurden die beiden Kastentheile von einander genommen, die
Holzmodelle mittelst einer starken eisernen Holzschraube durch sanftes Klopfen
vorsichtig gelöst und herausgezogen. Hierauf wurde in der noch feuchten Masse, auf
der untern Fläche des obern Kastentheils, von der Verbindungsröhre aus in einer
sanften Krümmung nach den beiden entgegengesezten Seiten der Wellzapfenform, die
Canäle zu den tangirenden Eingüssen mit einem Messer vorgerissen, ausgeschnitten und
sorgfältig geglättet; von einer Breite von 2 1/2 Zoll und Tiefe von 1 Zoll an der
Stelle, wo die Verbindungsröhre einmündete, verengten sich diese Canäle allmählich
bis auf 1 1/2 Zoll Breite und 1/2 Zoll Tiefe, womit sie in die Wellzapfenform
traten. Fig. 6
zeigt einen tangentirenden Einguß in vergrößertem Maaßstabe.
Durch diese tangentirende Richtung der Einmündung des Eingusses in die untere
Zapfenform, statt der bisherigen Richtung auf den Mittelpunkt derselben, wird das
einströmende Eisen genöthigt, an der Form und Kapselwand der Kreisform derselben zu
folgen, und, indem es am Schlusse des ersten, weitesten Kreises dem zufließenden
Strom begegnet, in gleicher Richtung einen innern Kreis und so fort mit zunehmender
Geschwindigkeit eine Schnekenlinie, und im Mittelpunkt derselben einen Strudel oder
Trichter zu bilden, welcher den Schaum und andere Unreinigkeiten, da er sie in die
viel dichtere und specifisch schwerere Masse des flüssigen Eisens nicht hineinziehen
kann, über sich concentrirt und im fortwährenden Aufsteigen emporträgt; dabei wird
die Geschwindigkeit des einströmenden Eisens durch die Verkleinerung des
Querschnittes der Einmündung in die Form, und die Geschwindigkeit der kreisenden
Bewegung in derselben überdieß noch dadurch vermehrt, daß der Einguß nicht auf einem
Punkt, sondern auf zwei einander entgegenstehenden Punkten an der Kreiswand, in
correspondirender Richtung tangentirend, in die Form des untern Walzenzapfens
mündet.
Die fertigen Masseformen wurden 12 Stunden in der verschlossenen, durch Steinkohlen
und Torffeuer stark erhizten Darrkammer vollkommen ausgetroknet, die Gußflächen der
Masseformen noch warm mit einer aus Weizenmehl und Kohlenstaub in Wasser gekochten,
dann mit Wasser verdünnten Schwärze, mittelst eines starken Pinsels überzogen, und
bleiben dann bis zur Zusammenstellung der Gußform in der noch warmen Darrkammer,
worin auch die Kapsel handwarm durchwärmt wurde. Die Gußform wurde bis zur obern
Kante des obern Formkastens in den Formherd eingesenkt, das aus drei ineinander
geschobenen gebrannten Lehmröhren von 1 3/4 und 1 1/4 Zoll Durchmesser gebildete
Einfallrohr, in einer von der senkrechten um 25° abweichenden Richtung, auf
die Verbindungsröhre gestellt und beides mit Herbsand eingedämmt. Vor dem
Einfallrohr wurde im Herdsande ein kleiner Tümpel gebildet, dessen Sohle gegen die
Mündung des ersten etwas vertieft war, damit das Eisen aus der Pfanne sich nicht
unmittelbar in das Rohr ergießen konnte, sondern erst den Tümpel füllen und aus
diesem in das Rohr überfließen mußte, so daß das Zurükhalten von Unreinigkeiten
erleichtert wird.
Um zu ermitteln, welche Sorte Eisen sich zum Gießen von Hartwalzen am besten eignet,
so wie auch, um die nöthige Stärke für die anzuwendende Kapsel zu erhalten, wurde
eine Reihe von Versuchen angestellt. Das Resultat dieser Abschrekungsversuche ergab:
daß Roheisen, welches mit Holzkohlen bei einem regelmäßigen Gang des Hohofens aus
Erzen gewonnen ist, welche ein derbes festes, haltbares Eisen liefern, nachdem es
hienächst im Flammofen noch einmal umgeschmolzen worden, sich zum Hartwalzenguß am
besten eignet. In Bezug auf die Stärke der Kapseln läßt sich anführen, daß je diker
die Masse des
abzuschreienden flüssigen Eisens ist, um so diker muß auch die Masse des
abschrekenden Eisens seyn, wenn ein gleicher Grad der Abschrekung bewirkt werden
soll. Da mit der Größe der Walze zugleich auch die Forderungen an die Haltbarkeit
der Kapsel steigen, so kann man als Schlußresultat der Versuche annehmen: daß bei
Hartwalzen von einem und demselben Durchmesser die Dike der Kapsel zur Verstärkung
der Abschrekung nichts beiträgt; daß aber, um einen gleichen Grad der Abschrekung,
der Härte der Oberfläche, bei Hartwalzen von verschiedenem Durchmesser
hervorzubringen, die Dike der Kapsel mit der Größe des Durchmessers verstärkt werden
muß. Ferner hält man es für rathsam, der Kapsel mindestens 1/3 des Durchmessers der
Walze zu geben.
Ein ganz vollendetes Paar kleiner Hartwalzen, wie Fig. 8, wog 1 Cntr. und
58P fd.; der Verkaufspreis dafür ist auf 70 Thlr. für den Centner gesezt, welches
auf das Paar 106 Thlr. 27 Sgr. 3 Pf. und für das Stük 53 Thlr. 13 Sgr. 8 Pf.
beträgt.
D. Red. d. polyt. Journals.
Tafeln
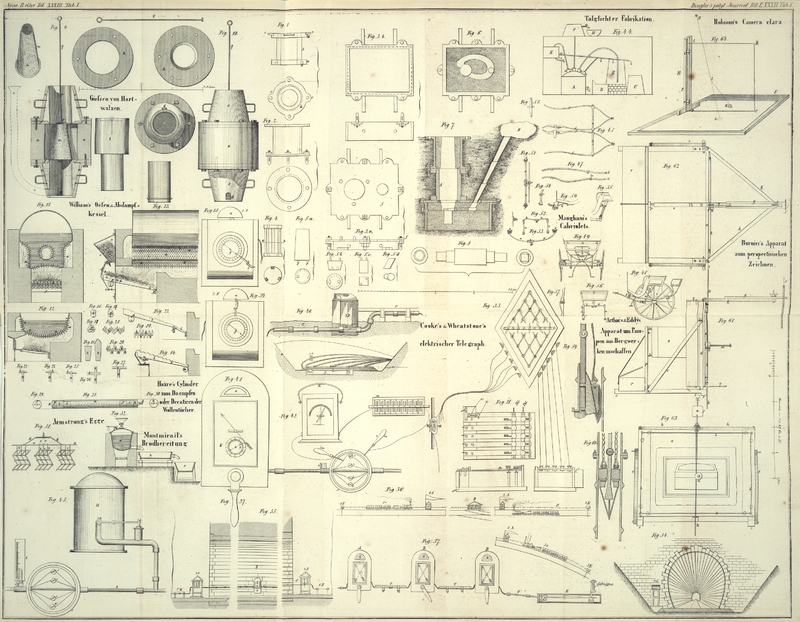