Titel: | Brückner's Cylinderofen zum Rösten von Silbererzen. |
Fundstelle: | Band 224, Jahrgang 1877, Nr. , S. 603 |
Download: | XML |
Brückner's Cylinderofen zum Rösten von Silbererzen.
Mit Abbildungen auf Taf.
XIII [d/4].
Brückner's Cylinderofen zum Rösten von Silbererzen.
Der bereits von Fr. Bode (* 1876 219 53) in günstiger Weise besprochene mechanische Röstofen von H. Brückner — eines deutschen Landsmannes —
wird jetzt im Territorium Colorado, wo der Ofen, nach im Engineering, December 1876 S. 515 veröffentlichten ausführlichen
Mittheilungen von Dr. Th. Egleston, anfänglich zum Rösten von göldischen Erzen bestimmt, im J. 1867
eingeführt wurde, bei der Amalgamation der dortigen Silbererze (nach dem sogen.
Reese-River-Verfahren) nach zahlreichen Versuchen mit andern bald aber
wieder verworfenen Oefen jetzt fast ausschließlich angewendet wird; die 13 derzeit
dort im Betriebe stehenden derartigen Oefen haben etwa die Hälfte des daselbst im J.
1875/76 producirten Silbers geliefert. Ursprünglich experimentirte Brückner mit einem im Wesentlichen aus zwei mit einander
verbundenen abgestumpften kegelförmigen Behältern bestehenden Apparate, in welchem
das Röstgut vom Ende eines jeden Kegels aus in den andern und wieder zurückfallen
mußte, so daß eine ununterbrochene Bewegung des Erzschliechs durch mechanische
Mittel gesichert wurde. Dieser Apparat führte ihn auf die Construction seines
„Cylinderofens“, den man sich als aus zwei solcher Kegeln
zusammengesetzt denken kann, in welchen der (jetzige) Scheider die Kreuzung der
Röstguttheile in den verschiedenen Umdrehungsstadien der Kegel vermittelt.
Der Cylinderofen in seiner jetzigen Gestalt besteht aus einem aus Kesselblech
angefertigten, 12 Fuß engl. (3m,66) langen und 5 bis 6 Fuß (1m,52 bis 1m,83) im Durchmesser haltenden, an beiden
Enden mit Boden geschlossenen Cylinder. Jeder Boden hat in seiner Mitte eine mit
Flansche versehene, 2 Fuß (0m,61) weite Oeffnung, von denen die eine mit dem Feuerraume, die
andere mit einer Flugstaubkammer in Verbindung steht. Anstatt der bei seinen ältern
Cylinderöfen rechtwinklig zum Cylindermantel gestellten Böden und den an diese
letztern gleichfalls unter 90° sich anschließenden Flanschen gibt Brückner jetzt den Cylinderenden, zur Vereinfachung der
innern Einrichtung des Ofens, eine conische Form. Beide Constructionsweisen sind aus
den Abbildungen Fig. 15 bis 18 ersichtlich.
Etwa in seiner Mitte hat der Cylinder eine mit Thür verschließbare, zum Eintragen des
Röstgutes dienende Oeffnung, und auf seiner Außenseite sind zwei mit Rädern
versehene, auf je zwei den Cylinder tragenden Frictionsrädern laufende Leitkränze
festgebolzt; der hintere derselben ist zur Vermeidung von seitlichen Verschiebungen
genau in die zu diesem Zwecke mit Flanschen versehenen Rädern eingepaßt, während der
andere einfach auf den Rollen läuft. Das ganze Getriebe ist so eingerichtet, daß es
zweierlei, in verschiedenen Stadien des Röstprocesses erforderliche
Umdrehungsgeschwindigkeiten zuläßt, und daß man bei dem Vorhandensein mehrerer
Röstcylinder jeden einzelnen derselben, ohne die andern anhalten zu müssen, zum
Stillstand bringen kann. Zur Correction etwaiger Senkungen werden sämmtliche
Lagerpfannen der Frictionsräder durch Stellschrauben in ihrer Lage erhalten, so daß
sie sowohl seitlich, als auch in verticaler Richtung verstellt werden können.
Durch den Cylinder gehen von der einen Seite zur andern sechs parallel zu einander
gelegte, einen rostförmigen Scheider im Ofen bildende und zur Drehungsachse
desselben unter 15° geneigte Röhren, welche, wie Figur 14 zeigt,
gleichzeitig zur Ebene dieser Achse einen Winkel von 30 bis 35° machen, durch
die Böden hindurchtreten und außen offen sind, so daß beständig Luft in ihnen
circulirt. Vergeblich hoffte man, mit Hilfe dieser Luftkühlung und der durch
dieselbe vermittelten Bildung eines Glühspanüberzugs, die Röhren von der Wirkung der
Röstdämpfe und -Gase schützen zu können. Der Scheider bezweckt eine
continuirliche Vor- und Rückwärtsbewegung des Röstgutes aus einem Ofen in den
andern; indessen fällt bei der von Cone herrührenden
neuesten Construction des Brückner-Ofens nach Egleston's Mittheilungen diese Einrichtung gänzlich weg. Der ganze
Cylinder ist mit einer Schicht von gewöhnlichen, flach in einen aus 1 Th.
feuerfestem Thon und 2 Th. Chamottepulver durch sorgfältigstes Mengen hergestellten
Mörtel gelegten Ziegelsteinen ausgefüttert. Auf der Pelican-Mill ist dieses
Futter mittels eiserner Bolzen mit dem Cylindermantel verankert und auf der einen
Seite in Form eines vollständigen Gewölbes ausgeschnitten; auf der
Niederland-Mill dagegen ist das Futter ohne Anlauf eingesetzt, und jeder
Halbcylinder desselben wird durch den Scheider gehalten, so daß eine weitere
Verankerung nicht erforderlich ist, da dort die Futtersteine besonders geformt
werden. Die Dauer des Futters wird hauptsächlich durch die auf seine Herstellung
verwendete Sorgfalt bedingt; bei guter Arbeit hält es gewöhnlich 1½ Jahre.
Bei den ältern Oefen werden die Cylinderenden mit rechteckigen Masseblöcken
geschlossen, welche man dann bis auf die erforderliche Futterstärke conisch
ausschnitt, was viel Arbeit und häufige Reparaturen verursachte; jetzt werden die an
sich schon conisch geformten Enden auf die gewöhnliche Weise gleichmäßig stark
ausgefüttert, wodurch eine bedeutende Verminderung des Ofengewichtes und bedeutende
Ersparnisse an Reparaturen erzielt werden.
Bei den älteren Oefen stand der Cylinder auf einem gemauerten Fundamente und die
Frictionsrollen ruhten auf einem Balkengerüste; jetzt wird dagegen der ganze Apparat
auf einen sorgfältig zusammengepaßten Gußeisenrahmen gelagert, wodurch seine
Aufstellung auf den Hüttenwerken sehr vereinfacht wird und die früher so häusigen
Betriebsstörungen wegfallen. Die vordere Flansche des Cylinders tritt frei in den
Feuerraum, die andere in den zu den Gestübbekammern und zur Esse führenden Fuchs,
auf dessen Sohle ein geneigt liegender Schuh angebracht ist, der etwa hinabfallenden
Röststaub dem Cylinder wieder zuführt. Der hintern Cylindermündung gegenüber ist
eine zum Schauen und Probeziehen dienende, mit einer Thür verschließbare Oeffnung
angebracht. Der Feuerraum wird entweder durchweg aus Mauerwerk, oder an den Seiten
aus verankertem, mit Chamotte gefüttertem Kesselblech, im Gewölbe aber gänzlich aus
Mauerwerk, bis auf die Ankerstangen, ohne alles Eisen construirt und erhält 6 Fuß
(1m,83) Länge, und
3 Fuß 2 Zoll (0m,96)
Breite, während seine Höhe zwischen Rost und Gewölbe an der Schürthür 2 Fuß 2 Zoll
(0m,66) und an der
6 Zoll (0m,15) über
dem Roste liegenden, runden und mit Chamotte gefütterten Feuerbrücke 3 Fuß 8 Zoll
(1m,12) beträgt.
Gewöhnlich hält der Feuerraum 6 bis 8 Monate; die eisernen Herdplatten (Zacken)
brauchen gewöhnlich erst nach 2 Jahren ausgewechselt zu werden, brennen jedoch in
einzelnen Fällen in Folge nachlässiger Behandlung schon nach kürzerer Zeit
durch.
Jeder Cylinder hat seine eigene Flugstaubkammer, die sonntäglich gereinigt wird. Auf
der Niederland-Mill tritt das feine Gestübbe aus der Kammer in einen 40 Fuß
(12m,19) langen, 6
Fuß (1m,83) hohen und
7 Fuß (2m,13) weiten
Canal, während der gröbere Staub in einen zu diesem Zwecke neben dem Ofen
angebrachten besondern Behälter fällt und aus diesem in einen tiefer stehenden
Kasten gezogen wird. Der erwähnte Canal läuft unter der Sohle des Trockenofens hin,
indem er an dieselbe einen Theil der zu ihrer Heizung erforderlichen Wärme abgibt;
in ihm sammeln sich monatlich etwa 10t an und in der Kammer selbst ungefähr
die gleiche Menge von feinem Flugstaub mit einem durchschnittlichen Silbergehalt von
32 Unzen (988g) auf
1t an, während
sich in dem gedachten Behälter während des gleichen Zeitraumes etwa 5t gröberer Staub
absetzt, welcher in den Ofen zurückkommt, wohingegen der feinere, sobald von ihm die
für eine Charge genügende Menge vorräthig ist, mit Zuschlag von Kochsalz und etwas
rohem Erzschliech
für sich behandelt wird. Auf der Pelican-Mill beträgt seine Menge für jedes
Cylinderpaar beim Rösten „schwerer“ (d. h. geschwefelter) Erze
wöchentlich 680k, bei
„leichten“ (hauptsächlich oxydischen) Erzen 10 Proc.
weniger. Hier und da läßt man Wasserdampf in die Kammern eintreten, um den
vollständigen Absatz des feinen Röftstaubes zu befördern.
Die liegende Triebwelle des Ofens muß etwa 23 Umdrehungen in der Minute machen, wozu
für jeden Cylinder ungefähr 3e erforderlich sind. Der letztere muß möglichst durchgängig aus
Schmiedeisen angefertigt werden, da Gußeisen bei größerm Gewichte weniger
widerstandsfähig ist und seine Anwendung die Anlagekosten in schwer zugängigen
Oertlichkeiten bedeutend vermehrt. Das Gesammtgewicht der Eisentheile, welche
sämmtlich in Chicago und Cincinnati gearbeitet und den Hüttenwerken zugeführt
werden, beläuft sich auf 726k.
Brückner's Cylinderofen läßt sich für die verschiedenartigsten Erzsorten benutzen;
indessen je kies- und blendereicher dieselben sind, desto weniger Gut läßt
sich binnen 24 Stunden fertig rösten, zumal da bei vielen Colorado-Erzen eine
große Neigung zum Sintern oder Zusammenfritten beim Rösten sich geltend macht,
weshalb auch sämmtliche Erze als feiner Schliech in den Ofen gebracht und während
des Abröstens mit steter Aufmerksamkeit behandelt werden müssen. Sobald eine
abgeröstete Erzpost ausgetragen worden, ist der Ofen für die Aufnahme einer frischen
Charge fertig, insofern er von der letzten Operation her noch rothglühend ist, oder
wenn erforderlich wieder zur Rothglut erhitzt wird, während man ihn eine halbe bis
eine ganze Umdrehung in der Minute machen läßt; ist dann die Eintragsöffnung nach
oben gekehrt, so gibt man das in Kisten magazinirte Röstgut mit Hilfe einer
biegsamen Rohrleitung durch einen Rumpf in den Cylinder auf. Das Gewicht einer
Röstpost ist der Beschaffenheit der Erze entsprechend sehr verschieden; auf der
Niederland-Mill in Carabo, wo dieselben 5 Proc. Bleiglanz, 4 Blende, und 2
Kupferkies, im Ganzen also 11 Proc. Sulfurete enthalten, beläuft sich das
Maximalgewicht einer Charge auf 1680k; der Pelican-Mill dagegen, wo
das Rösten der 15 bis 16 Proc. Bleiglanz und Kiese, sowie bis 15 Proc. Blende
führenden Erze wegen ihres hohen Gehaltes an letzterer sehr schwierig ist, beträgt
das Gewicht einer Charge selten über 1580k, oft noch bedeutend weniger. Indessen
steht die Größe der Röstposten keineswegs in nothwendigem Verhältnisse zum
Fassungsraume des Cylinders, denn die zu ihrer Behandlung erforderliche Zeit ist je
nach der auf die Arbeit verwendeten Sorgfalt sehr verschieden und nimmt mit
wachsendem Schwefelgehalte zu. Bei sehr leichten Erzen kann man große Röstposten in ungefähr 4
Stunden abrösten; auf der Niederland-Mill gebraucht man dazu 8 Stunden. Bei
schweren Erzen, wie auf der Pelican-Mill, sind zur Ausführung des Processes
mindestens 12 bis 13, zuweilen sogar 20 Stunden erforderlich.
In den vier Cylinderöfen der Niederland-Mill wurden 1875/76 fast 4000t Silbererze
verröstet. Der Fassungsraum der für die verschiedenen Erzsorten bestimmten Cylinder
wurde von Cone in der Weise bestimmt, daß er so lange
Röstgut in den Cylinder brachte, bis dasselbe, nachdem es zu seinem Maximum
aufgequollen war, aus der hintern Ofenöffnung heraustrat.
Ist der Cylinder (bei geschlossenem Schieber des Fuchses) gefüllt, so wird der Rumpf
abgesperrt, die Ofenthür geschlossen und der Ofen selbst zu einer Umdrehung in zwei
Minuten angelassen. Bei schweren Erzen muß der Cylinder beim Eintragen des Röstgutes
sehr heiß sein, um den Schwefel möglichst bald zum Brennen zu bringen, wozu etwa 1
Stunde erforderlich ist; leichte Erze werden einfach erhitzt und dann chlorirt,
wobei zuweilen — wie auf der Niederland-Mill — das Kochsalz
gleichzeitig mit dem Erzschlieche aufgegeben wird. Den Schwefel läßt man bei nunmehr
geöffnetem Fuchs unter möglichst reichlichem Luftzutritt, während man das Feuer nur
eben nicht abgehen läßt, vollständig abbrennen, was bei schweren Erzen 3 bis 5
Stunden andauert, und schürt erst wieder an, nachdem der Schwefel zu brennen
aufgehört hat, worauf man zur Vervollständigung der Röstung noch 5 bis 6 Stunden
lang feuert und den Ofen während dieser Zeit zum Rothglühen bringt. Während des
ganzen Röstprocesses wird die Röstpost mittels des Scheiders ununterbrochen
vor- und rückwärts geworfen und fällt continuirlich durch denselben hindurch,
so lange es noch Schwefel enthält; sobald dieser aber wegzubrennen beginnt, so backt
der Schliech zu Klümpchen zusammen, welche indessen in Folge der Bewegung des
Cylinders bald wieder zerfallen. 10 bis 12 Stunden nach dem Eintragen ist die
Röstpost für den Zusatz des Kochsalzes fertig; dasselbe wird dem Cylinder durch
einen Rumpf zugeführt. Auf eine Röstpost von 1580k sind der Haltigkeit des Erzes
entsprechend 90 bis 115k davon erforderlich. Bald nach dem Salzzusatze nimmt das Erz in
Folge der Zersetzung der beim Rösten entstandenen Sulfate unter Chlorentwicklung
schwammförmigen Zustand an; nach erfolgter Chlorirung hört der Schwefligsäuregeruch
auf; die Röstpost muß vielmehr vor dem Auskrählen etwa ½ Stunde lang einen
reinen Chlorgeruch von sich geben. Durch die erwähnte, im Fuchse angebrachte
Schauthür, auch wohl durch die Eintragsthür des Cylinders, aus welcher man während
der Umdrehung des
letztern etwas Röstgut in den Wagen fallen läßt, werden die nöthigen Proben gezogen.
Die Chlorirung schwankt nach der Beschaffenheit der Erze und der auf die Operation
verwendeten größern oder mindern Sorgfalt zwischen 85 und 95 Proc. Wird fortwährend
ein und dasselbe Erz verhüttet, so werden diese Proben nicht immer ausgeführt,
sondern die Beurtheilung des Grades der Chlorirung wird dem Arbeiter nach dem äußern
Ansehen und dem Geruche überlassen, eine übrigens durchaus verwerfliche Praxis.
Stets sollte die Beschickung in den verschiedenen Stadien des Processes mit
unterschwefligsaurem Natrium probirt werden.
Ist die Charge fertig (was gewöhnlich nach Verlauf von 4 bis 13 Stunden nach dem
Eintragen der Fall), so wird ein eiserner Transportwagen unter den Cylinder gefahren
und dem letztern bei geöffneter Eintragsthür die rascheste Bewegung gegeben, wobei
die Charge in den Wagen fällt und nun auf die aus Ziegelsteinen hergestellte
Kühlsohle gestürzt wird. Auf andern Werken wird das chlorirte Erz in einen unter dem
Cylinder stehenden Rumpf gezogen, an dessen Boden eine die Charge in einen mit
Wasser gekühlten eisernen Trog fördernde Schraube oder endlose Kette angebracht ist
— eine Einrichtung, durch welche beim Abkühlen Zeit und Arbeit gespart wird.
Das Ausziehen der Charge nimmt 1 bis 1½ Stunden in Anspruch.
Vor dem Chloriren zeigen die Colorado-Erze eine grauliche Färbung, nach der
Operation erscheinen sie bräunlichroth. Die ganze Kunst des Chlorirens besteht in
dem rechtzeitigen Zusetzen von Kochsalz, so lange das Röstgut noch etwas Schwefel
enthält; es soll dann ein sammtartiges Ansehen haben und gänzlich frei von Klümpchen
sein. Die Temperatur des Ofens darf nie so hoch steigen, daß Sinterung eintritt, was
auch wohl nur bei noch unerfahrenen Arbeitern stattfindet. Ein Zusammenbacken und
Ansetzen des Röstgutes an die Cylinderwandungen läßt sich dagegen nie gänzlich
vermeiden; diese Antheile werden abgekratzt und müssen nochmals vermahlen und von
Neuem chlorirt werden, zu welchem Zwecke der Cylinder mit 1360k, von denen 227k rohe Schlieche sein
müssen, und mit 72k
Salz beschickt wird. Vor der Amalgamation wird das Gut auf der Kühlsohle gesiebt.
Die schweren Erze backen bei längerm Liegen auf der letztern leicht zusammen. Das am
Schlusse der Woche aus den fünf Cylindern gesammelte Gekrätz, dessen Menge übrigens
vom Bleigehalte der Erze bedingt wird, reicht gewöhnlich für eine ganze Charge hin;
bei leichten Erzen kommt öfters binnen 14 Tagen gar kein Gekrätz vor. Das letztere
wird mit der Siebgröbe
zusammen vermahlen und dieses Gemenge wird stets für sich besonders zu gute
gemacht.
Auf der Pelican-Mill sind etwa 6cbm (1½ Klafter) Holz für den 24
stündigen Betrieb von zwei Röstcylindern bei sehr schweren Erzen, also 3cbm auf 1360k mehr als
hinreichend; auf der Niederland-Mill gebraucht man nur 6cbm auf 5t der allerdings sehr
„leichten“ Erze. Nach Brückner
hat man gewöhnlich auf ordinäre Erze 3cbm Holz oder 0t,375 Steinkohle zu rechnen. Meist brennt
man Fichtenholz (die Klafter zu 5 Dollars oder 21,50 M.) oder Bastardfichtenholz (zu
4 Doll. oder 17,20 M.); ersteres gibt ein rasches Feuer und, was für einen guten
Röstbetrieb wichtig ist, viel Flamme. Je fünf Oefen erfordern einen Röster und einen
Rostgehilfen für eine 12 stündige Schicht. Es ist sehr fraglich, ob bei einem so
ununterbrochene Aufmerksamkeit beanspruchenden Hüttenprocesse so lange Schichten
vortheilhaft sind; bei 8 stündigen Schichten würden die Arbeiter weit weniger
angestrengt werden und Besseres leisten.
Auf verschiedenen Werken stellen sich die Röstkosten etwas verschieden; die Röstung
erfolgt sehr gleichmäßig, erfordert weniger Zeit und ist weit billiger als das
Rösten in Flammöfen. Reparaturen werden nur an der Feuerbrücke und am Scheider
nöthig; die erstere muß gewöhnlich alle 6 bis 8 Wochen ausgebessert werden. In
Colorado werden die Gußeisentheile aus mehrfach umgeschmolzenem Alteisen aller Art,
aus abgenutzten Maschinenstücken, abgeworfenen Oefen u. dgl. ohne große Rücksicht
auf Qualität hergestellt. 1k dieses sehr harten und kohlenstoffarmen Materials kostet 17
Cents (73 Pf. ) und ist so schlecht, daß die Werke den Bezug bessern Eisens aus dem
Osten beabsichtigen. Die vom Schwefelgehalte des Röstgutes abhängige Dauer des
Scheiders beträgt gewöhnlich 4 bis 5 Monate bei schweren und 1 Jahr bei leichten
Erzen; bricht ein Rohr desselben, so wird es erst Sonntags, wenn die Oefen behufs
der erforderlichen Reparaturen kalt gelegt sind, gegen ein neues ausgewechselt,
während man den Cylinder die laufende Woche hindurch noch im Betriebe erhält.
Anfänglich legte man auf eine gute Instandhaltung des Scheiders großes Gewicht, fand
aber daß die Oxyddecke, auf deren schützende Wirkung man gehofft hatte, nicht immer
entstand, daß die Röhren fortwährend leckten und gegen neue ausgewechselt werden
mußten. Cone auf der Niederland-Mill, durch diese
und ähnliche unerquicklichen Erfahrungen veranlaßt, entschloß sich, versuchsweise
ganz ohne Scheider zu rösten, und fand bald, daß der
Gang des Ofens ein ebenso guter und, insofern sich in den Kammern weit weniger
Flugstaub ansammelt, sogar ein Vortheilhafterer ist, und behielt diese
Einrichtung bei. Allem Anscheine nach ist die rotirende Bewegung des Cylinders zur
Erzielung einer vollständigen Röstung des Erzes vollkommen genügend.
Der Anschaffungspreis eines vollständigen Cylinders einschließlich aller
Maschinentheile und des ganzen Eisenwerkes und der Abgaben beträgt in Cincinnati
etwa 2000 Doll. (8600 M.), so daß ein einzelner Ofen in Colorado, der leichtern oder
schwierigern Zugängigkeit der zu seiner Aufstellung bestimmten Oertlichkeit
entsprechend, auf 2500 bis 3000 Doll. (10 750 bis 12 900 M.) zu stehen kommt. Die
wiederholt herabgesetzten Abgaben auf den Cylinderofen betrugen im J. 1874 1000
Doll. (4300 M.)
Die Vorzüge dieses Ofens, dessen rascherer Verbreitung anfänglich der Umstand, daß
man (wie dies bei praktisch werthvollen Erfindungen so häufig der Fall ist) von
vornherein mehr von ihm erwartete, als er zu leisten im Stande war, auf kurze Zeit
hindernd in den Weg trat, bestehen, kurz zusammengefaßt, in folgendem: Die Röstung
erfolgt vollständig und gleichförmig und der Röstproceß kann durch den Arbeiter
ununterbrochen überwacht werden; sie erfordert einen verhältnißmäßig geringen
Arbeits- und Brennstoffaufwand; bei genügender Aufmerksamkeit und Sorgfalt
erfolgt eine sehr hochprocentige Chlorirung; die Arbeit wird leicht eingeübt und die
ganze maschinelle Einrichtung ist ziemlich einfach, so daß sie nicht leicht in
Unordnung kommt und in vorkommenden Fällen leicht reparirt werden kann.
H. H.
Tafeln
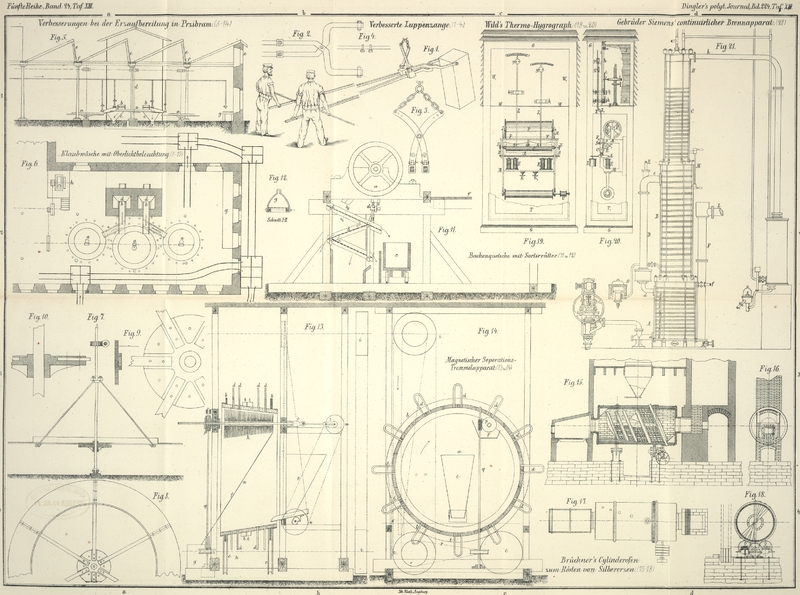