Titel: | Die Fabrikation von Kunstsandstein im Anschlusse an Dampfziegeleien; von Dr. Zernikow zu Oderberg i. d. Mark. |
Autor: | Zernikow |
Fundstelle: | Band 232, Jahrgang 1879, S. 75 |
Download: | XML |
Die Fabrikation von Kunstsandstein im Anschlusse
an Dampfziegeleien; von Dr. Zernikow zu Oderberg i. d. Mark.
Mit einer Abbildung auf Tafel 8.
Zernikow's Fabrikation von Kunstsandstein.
Mit der Kunstsandstein-Fabrikation wird der Zweck verfolgt, in der Bautechnik die
natürlichen Sandsteine zu ersetzen. Insofern es sich beim fabrikmäſsigen Betriebe
hauptsächlich um Massenproduction handelt, soll nachstehend diese Fabrikation,
soweit sie die Herstellung glatter Bauglieder von
prismatischer Form betrifft, als da sind: Gittersehwellen, gerade
Treppenstufen, Thür- und Fenstereinfassungen, Verdachungen, Fuſs-, Brust- und
Hauptgesimse u. dgl., näher erläutert werden (D. R. P. Nr. 502 vom 2. Juli 1877.
Vgl. 1878 228 182).
Die Rohmaterialien zur Herstellung des Kunstsandsteines sind: Sand und gelöschter
Kalk. Aller Sand ist hierzu gut, welcher mit gelöschtem Kalke gemengt einen gut
bindenden Mörtel gibt. Am besten ist der feine, möglichst viel Kieselsäure haltende
Sand. In all den Verhältnissen, welche bei der Mörtelmischung zulässig sind, können
auch die Rohmaterialien zur Herstellung des Kunstsandsteines gemengt werden. Im
Allgemeinen wird aber dieser Stein um so härter, je magerer der Mörtel ist; darum
geben 4 bis 6 Th. Sand und 1 Th. gelöschter Kalk ein recht gutes Fabrikat.
Die Rohmaterialien, Sand und gelöschter Kalk, müssen innig gemengt werden, um eine
recht gleichmäſsige Masse zu bilden. Die in gröſseren Städten gebräuchlichen
Mörtelmaschinen, und auch die guten Thonschneider auf den Ziegeleien, sind
ausreichend für diesen Zweck. Wird nun der so hergestellte magere Mörtel einige Tage
im geschlossenen Dampfkessel gekocht, so wird unter dem Einflüsse der Temperatur
(über 100°) und des Druckes (über 1at) an den
Berührungspunkten des Sandes mit dem Kalkhydrate eine dünne Schicht kieselsaurer
Kalk gebildet, welcher bei der Abkühlung unter 100° unter gleichzeitiger Abnahme des
Druckes die Erhärtung der Masse einleitet. Die Erhärtung ist bei der Abkühlung bis
zu 40°, selbst wenn sie unter Wasser erfolgt, so groſs, daſs aus dem weichen,
plastischen Mörtel ein starrer, zusammenhängender, fester Körper gebildet wird. Da
nicht alle Kalktheilchen zur Bildung von kieselsaurem Kalk verbraucht werden, so
findet an der Luft in Folge der Aufnahme von Kohlensäure noch ein bedeutendes
Nachhärten statt, welches in einigen Wochen dem Kunststein den Härtegrad gibt, wie
er bei guten natürlichen Sandsteinen anzutreffen ist. Das patentirte Verfahren
beruht demnach im Wesentlichen auf „Nutzbarmachung der Dampfkraft zur schnellen
Versteinerung des Mörtels“, und dürfte der so hergestellte Kunstsandstein
dem natürlichen Sandstein sehr nahe stehen, welcher als Bindemittel auch Kalk
enthält.
Der in Fig. 6 Taf. 8 dargestellte Apparat soll die fertige Masse in die
Ziegelmaschine abgeben, welche am oberen Ende mit einem Deckel verschlossen und
durch eine Röhre oder durch einen Elevator mit dem Durchlaſsrohr E in Verbindung gebracht wird. Das Mundstück der
Ziegelmaschine muſs einen Ansatz erhalten, welcher der gewünschten Schablone
entspricht. Da es sich um die Herstellung voller und Meter langer Stücke handelt, so
ist der Abschneidapparat bei Seite zu stellen.
Das Kochen kann zweckmäſsig durch Dampf aus dem Betriebskessel bewirkt werden, damit
die Anlage einer besonderen Feuerung für den Kochapparat nicht nothwendig wird. Da
die chemische Verbindung von Kieselsäure und Kalk nur an der Berührungsfläche und
deshalb nur allmälig vor sich geht, so muſs der Kochproceſs eine gewisse Zeit
andauern.
Die Mörtelmasse wird durch das Mannloch H in den
stehenden Kessel A gebracht und darauf das Mannloch
geschlossen. In der Achse des Kessels steht eine hohle Welle C, welche am oberen Ende durch die Stopfbüchse b mit dem Dampfzuleitungsrohre a, am unteren
Ende mit den schraubenförmig stehenden Flügeln D und
mit den daran befestigten Dampfeinleitungsröhren d in
Verbindung steht.
Wird nun der Hahn a1
geöffnet, so strömt Dampf aus dem Kessel durch die Röhre a in die Stopfbüchse b, durch die hohle Welle
C in die Siebröhre d
und tritt von hier zur Erwärmung in die Mörtelmasse. Das aus dem einströmenden
Dampfe erhaltene Condensationswasser wird, weil specifisch leichter, in die Höhe
steigen und sich an der Oberfläche der Mörtelmasse, bei w, sammeln. Von hier aus wird es durch einen Hahn l abgelassen und dann zweckmäſsig zur späteren Mörtelfabrikation, für
welche es Wärme und einige aufgelöste Kalktheilchen mitbringt, verwendet.
Das Manometer k, welches auf dem Deckel des Kessels A angebracht ist, läſst den Zeitpunkt erkennen, bei
welchem die Erhitzung der
Masse so weit fortgeschritten ist, daſs der zuströmende Dampf Wärme nicht weiter
abgibt; dann wird die directe Dampfzuleitung unterbrochen und der Hahn a1 geschlossen.
Jetzt kommt es darauf an, die Masse einige Tage lang bei der vorhandenen
Dampfspannung und Temperatur zu erhalten. Darum ist der Kessel A von einem Mantel B, in
einem Abstande von 40 bis 80mm, eingeschlossen.
Der Zwischenraum ist oben abgeschlossen und steht durch die Röhre e mit dem Dampfzuleitungsrohre a in Verbindung. Wird der Hahn e1 geöffnet, so wird der Zwischenraum mit Dampf
gefüllt, welcher jede Abkühlung des inneren Kessels unmöglich macht. Der einhüllende
Dampf wird durch Wärmeabgabe nach auſsen theilweise niedergeschlagen. Das
Condensationswasser, dessen Stand an dem Glas g zu
erkennen ist, kann durch Oeffnung des Hahnes f1 unter Vermittlung der Röhre f wieder nach dem Dampfkessel zurückgeleitet
werden.
Das Kochen der Masse wird zweckmäſsig einige Tage dauern (bei 3 bis 4at etwa 3 Tage); es ist einestheils an der
Oberfläche der Sandkörner kieselsaurer Kalk zu bilden und anderntheils durch das
längere Kochen die physikalische Beschaffenheit des Quarzsandes zu verändern,
welcher dadurch an Härte und Sprödigkeit verliert und so eine mehr plastische Masse
bildet.
Die stehende Welle C kann durch Vermittlung der
Riemenscheibe o in Drehung versetzt werden. So lange
die Masse im ersten Theile des Kochprocesses sich befindet, läſst man die Welle
langsam und nicht andauernd laufen; schneller und ununterbrochen müssen die
Umdrehungen sein, wenn die Masse durch Oeffnung des Ausfluſsrohres E in die Ziegelmaschine gedrückt werden soll.
Die Masse, im Wesentlichen aus Kieselerde, kieselsaurem Kalk, Kalkhydrat und Wasser
bestehend, läſst bei Oeffnung des Hahnes i im Deckel
des Apparates so viel Wasser ab, daſs dadurch leicht ein Sinken der Temperatur unter
100° und die zugehörige Spannungsverminderung des beigemengten Wassers, sowie jeder
wünschenswerthe Grad der Trockenheit der Masse erreicht werden kann, so daſs
dieselbe durch die Ziegelpresse später noch gerade formbar genug, anderntheils aber
so cohärent wird, daſs sie die erhaltene Form auch beibehält.
Der skizzirte Apparat hat 1m,56 Durchmesser und
kann bis 3m,48 Höhe gefüllt werden, faſst also
6cbm,653 Masse. Dieselbe würde ausreichend
sein, um Fenstereinfassungen von 18cm Breite und
13cm Dicke in der Länge von 285m, also, bei 1m
Fensterbreite und 2m Fensterhöhe, etwa für 50
Fenster die Einfassungen in 3 Tagen zu liefern.
Tafeln
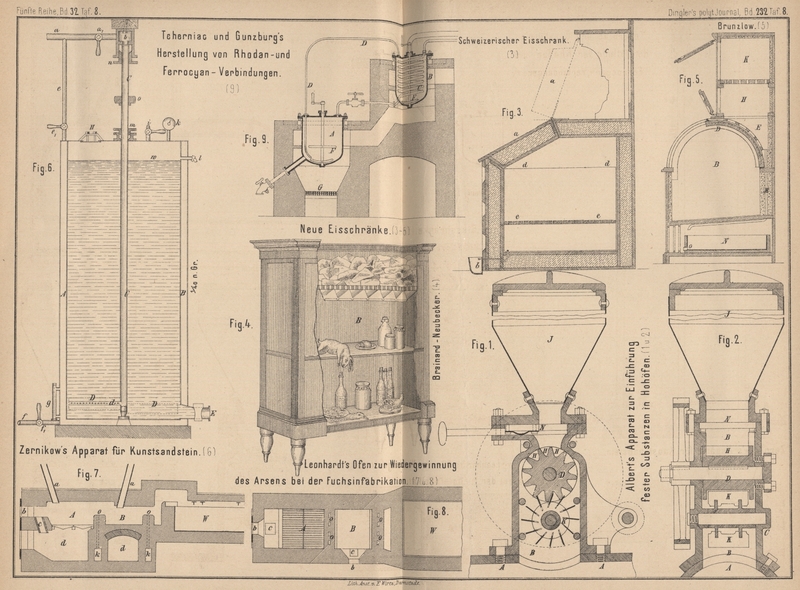