Titel: | Neuerungen in der Eisenerzeugung. |
Autor: | –r. |
Fundstelle: | Band 233, Jahrgang 1879, S. 42 |
Download: | XML |
Neuerungen in der Eisenerzeugung.
Mit Abbildungen auf Tafel 8.
Neuerungen in der Eisenerzeugung.
Ueber die Ausscheidung des Phosphors aus dem Roheisen.
Gleichzeitig mit den Untersuchungen von J. L. Bell über
die Ausscheidung von Kohlenstoff, Schwefel, Silicium und Phosphor (1877 225 264. 351. 1878 229 184.
290) hat A. Krupp in Essen durch Versuche in groſsem
Maſsstabe gezeigt, daſs beim Zusammenbringen von flüssigem Roheisen mit den Oxyden
des Eisens und Mangans Silicium, Schwefel, namentlich aber Phosphor aus dem Eisen
ausgeschieden und in die Schlacke übergeführt werden. Durch Anwendung von Mangan
haltigem Roheisen oder Mangan haltigen Oxyden wird der Angriff der Oxyde auf den
Kohlenstoff des Roheisens verzögert und dadurch den Oxyden mehr Zeit zum
Verschlacken der genannten Verunreinigungen des Eisens gegeben (vgl. 1879 231 275). Unter Benutzung dieser Reaction reinigt Krupp (*D. R. P. Nr. 4391 vom 2. Juli 1877) Phosphor
haltiges Roheisen vom Phosphor, gleichzeitig auch von Silicium, Schwefel und Mangan
in folgender Weise.
Flüssiges Roheisen, das entweder direct vom Hohofen oder aus einem Umschmelzofen
abgestochen werden kann, wird in einen rotirenden Ofen geleitet, dessen Futter aus
basischen Oxyden des Eisens oder Mangans oder aus einer Mischung von beiden besteht,
und in welchen überdies noch solche Oxyde in je nach der chemischen Zusammensetzung
des Roheisens verschiedener Menge als Zuschläge eingebracht werden. Dieses Roheisen
wird sodann während einer gewissen Zeit bei der nöthigen Temperatur der
beschriebenen Reaction ausgesetzt und, wenn der Kohlenstoff anfängt, angegriffen zu
werden, abgestochen und von den Schlacken getrennt; worauf es sofort in flüssigem
Zustande zu Stahl oder Eisen beliebiger Kohlungsgrade weiter verarbeitet werden
kann, indem es von dem Reinigungsofen durch Rinnen oder mittels einer Pfanne in den
Verarbeitungsapparat übergeführt wird. Selbstverständlich kann es auch in Masseln
gegossen und so zu späterer Weiterverarbeitung aufbewahrt werden.
Zur Ausführung dieses Processes werden rotirende Oefen verwendet, deren Herd mit
basischen Eisenoxyden und Manganoxyden ausgekleidet ist. Auſser dem um die Achse i (Fig. 1 und
2 Taf. 8) drehbaren Ofen von Pernot (*1874
213 126. 1875 217 426) und
dem Ofen von Howson und Godfrey (*1878 228 133) schlägt Krupp noch zwei andere Oefen vor, von denen der in Fig.
3 gezeichnete Ofen mit einer durchgehenden, der in Fig. 4 und
5 dargestellte Ofen mit einer zurückkehrenden Feuerung geheizt wird.
Beide sind je um eine horizontale Achse xy (welche
jedoch auch schräg gelegt werden kann) drehbar und haben einen ringförmig in sich
geschlossenen, mit den genannten Oxyden ausgekleideten Herd. Derselbe ruht wie der
Pernot'sche mit den Gleitringen b und b1, von denen b gleichzeitig als Zahnrad zum Drehen angenommen ist,
auf Leitrollen, welche auf einem zur Reparatur ausfahrbaren Wagen d gelagert sind. Das Füllen des Ofens erfolgt durch
eine durch die Thüren e und die Oeffnungen e1 im Herdkörper
eingeführte Rinne, oder bei ausgefahrenem Herd durch eine der Oeffnungen e1 allein, das
Entleeren durch den Abstich f. Der Herdkörper braucht
keinen kreisförmigen Querschnitt zu haben, derselbe kann vielmehr der besseren
Mischung wegen beliebig abgeändert werden.
Das Einlassen des Roheisens in den Reinigungsofen erfolgt, nachdem die Temperatur desselben
so weit gesteigert ist, daſs die das Futter bildenden Oxyde zu schmelzen anfangen
und die als Zuschläge eingebrachten Materialien zusammengesintert sind. Die Zeit,
während welcher das Roheisen der Reaction ausgesetzt wird, ist je nach der
chemischen Zusammensetzung und der Menge des zu reinigenden Roheisens verschieden;
bei einer Beschickung von 5t beträgt sie 5 bis 15
Min. Sobald der Kohlenstoff des Roheisens angegriffen wird, was man an dem Auftreten
von Blasen in der Masse erkennt, wird das Eisen abgestochen und von der Schlacke
getrennt; ersteres behält dabei völlig die chemische und physikalische
Eigenthümlichkeit eines gefeinten Eisens und es wird namentlich seine Flüssigkeit
nicht beeinträchtigt.
Die Trennung des Roheisens von der Schlacke, welche die Unreinigkeiten in sich
aufgenommen hat und welche von bedeutend geringerem specifischem Gewichte ist, läſst
sich auf verschiedene Weise leicht bewirken. Wenn das gereinigte Metall durch Rinnen
abgeführt wird, so läſst sich die Schlacke unterwegs abfangen; wenn es in eine
Pfanne abgestochen wird, so kann es unter Zurücklassung der Schlacken durch den
Boden der Pfanne abgezapft werden.
Die Weiterverarbeitung des flüssigen Productes zu Stahl, Fluſseisen und ähnlichen
Endproducten kann auf irgend eine der bekannten Methoden geschehen.
Da von den Gegnern der Patentertheilung behauptet worden war,
daſs eine Entphosphorung ohne Entkohlung nicht möglich sei, so begaben sich A. W. Hofmann und H.
Wedding im Auftrage des deutschen Patentamtes an Ort und Stelle, um sich
von der Richtigkeit der Angaben zu überzeugen. Nach dem vorliegenden BerichtVerhandlungen des Vereines zur Beförderung des
Gewerbfleiſses, 1879 8. 201. wurde (auf Anregung des
Ingenieurs Narjes) am 16. März 1877 von Krupp die erste Entphosphorung mit 4t Eisen ausgeführt. Das Verfahren auf der Hütte in
Essen war sehr einfach. Die 5t Roheisen wurden im
Cupolofen geschmolzen und in den in Fig. 1 und
2 abgebildeten Pernot'schen Ofen mit Generatorgasfeuerung abgestochen.
Derselbe hat einen äuſsern Herddurchmesser von 3m,75, eine lichte Weite von 3m, eine äuſsere
Bordhöhe von 0m,9 und eine lichte Tiefe von 0m,61; die Neigung ist 1 : 10. Der Herd ist mit
ebenem Boden und etwas gerundeter Kante aus Eisenerzen etwa 0m,29 dick bei hoher Temperatur aufgeschmolzen und
wird vor jeder Hitze mit 700 bis 800k Erz
beschickt, welches ebenfalls bis zu starker Sinterung erhitzt wird, ehe das aus dem
Cupolofen abgestochene Eisen einflieſst. Die Temperatur ist also (im Gegensatze zu
Bell) starke Weiſsglut. Anfangs macht der durch
eine Dampfmaschine bewegte Ofen 2, bald 5 Umdrehungen in der Minute. Nach etwa 5
(höchstens 10) Minuten ist die Entkieselung und Entphosphorung vollendet und der
Beginn eines Blasenwerfens mit Kohlenoxydflämmchen zeigt den Eintritt der
Entkohlung, worauf sofort der Abstich in die vorgewärmte Pfanne erfolgt, welche das
gereinigte Eisen in flüssiger Form zu den Flammöfen führt, wo in üblicher Weise die
Entkohlung durch Erze, die Desoxydation durch Mangan bis zum guſsfertigen Fluſseisen
oder Stahl erfolgt.
Bei drei mit verschiedenen Roheisensorten ausgeführten
Operationen wurden vor und nach der beschriebenen Entphosphorung je 2 Proben
entnommen und von Prof. Finkener untersucht; dieselben
enthielten Procent:
Kohlenstoff
Phosphor
I
II
I
II
1)
Vor dem Proceſs
3,99
3,98
0,632
0,629
Desgl. nach demselben
3,75
3,77
0,131
0,133
2)
Vor dem Proceſs
3,81
3,78
0,450
0,445
Desgl. nach demselben
3,56
3,57
0,108
0,106
3)
Vor dem Proceſs
3,17
3,16
1,223
1,218
Desgl. nach demselben
3,02
3,04
0,303
0,301
In ähnlicher Weise will J.
Berchelmann in Pfungstadt (* D. R. P. Nr. 3022 vom 21. November 1877)
Roheisen mit basischen Oxyden des Eisens oder Mangans behandeln, um es von Phosphor,
Silicium, Schwefel und Mangan zu reinigen. Der betreffende Apparat ist in Fig.
6 bis 8 Taf. 8 in
verschiedenen Schnitten dargestellt. Der um die beiden Zapfen c und d drehbare Apparat
besteht aus einem an beiden Enden geschlossenen, mit einem Stutzen b versehenen runden Gefäſse a aus starkem Eisenblech, welches mit einem feuerfesten, möglichst wenig
Kieselsäure haltigen Futter versehen ist. Mittels des Rades am Zapfen c kann das Gefäſs nach beiden Richtungen gedreht
werden. Durch den zweiten Zapfen d führt ein getrennter
Gas- und Luftkanal in das Innere des Gefäſses, um während der Operation die
erforderliche Hitze zu erhalten. Gegenüber dem Stutzen b ist aus demselben feuerfesten Material eine Brücke e aufgeführt, welche zur etwa erforderlichen Kühlung
mittels einer durch den Zapfen c geführten Leitung mit
Wasser versorgt werden kann. Zur Erneuerung des feuerfesten Futters können die
beiden Deckel h abgenommen werden.
Die Reinigung des Eisens hat nun nach Angabe Berchelmann's folgenden Verlauf:
Zuvörderst wird das feuerfeste Futter angewärmt, was zweckmäſsig
geschehen kann, indem das Gefäſs in horizontale Lage gebracht und durch die beiden
Oeffnungen g Gas und Luft – oder nur Luft, wenn Kokes
angewendet – eingeführt wird. Alsdann wird das erwärmte Gefäſs in die verticale
Stellung zurückbewegt, und nimmt daſselbe dann durch die Einfluſsöffnung das
flüssige Eisen, entweder direct vom Hohofen oder von einem Umschmelzofen, sowie die
in einem besonderen Ofen geschmolzene basische Schlacke auf. Hierauf wird das Gefäſs
in der dem Zufluſs entgegengesetzten Richtung um 180° gedreht. Während der ersten
Hälfte dieser Drehung flieſst bei genügender Höhe der Brücke nur die Schlacke in die
andere Abtheilung des Gefäſses, bei der weiteren Drehung folgt das Eisen und wird
auf diese Weise gezwungen, durch die Schlacke zu treten, wodurch eine innige
Berührung zwischen den beiden Flüssigkeiten stattfindet. Alsdann wird das Gefaſs wieder um 180°
zurückgedreht, und wiederholt sich diese Operation so oft, bis der Kohlenstoff aus
dem Eisen zu entweichen beginnt, worauf das Abstichloch f geöffnet wird. Das Eisen flieſst zuerst aus; sobald die Schlacke kommt,
wird man das Gefäſs etwas drehen und derselben dadurch eine andere Richtung geben,
so daſs sie von dem Eisen geschieden wird. Man wird die Oxyde auch in festem,
entweder kaltem oder rothwarmem Zustand einbringen und durch das flüssige Eisen
auflösen lassen können.
Erfahrungen über die Verwendbarkeil dieses Apparates liegen noch nicht vor.
L. GrunerBulletin de la Société d'Encouragement, 1879 Bd.
6 S. 27. erinnert daran, daſs es gelingt, durch den Puddelproceſs
80 Procent des im Roheisen enthaltenen Phosphors abzuscheiden, wenn der Herd und die
Wände des Ofens aus Eisen hergestellt und mit Eisenoxyd besetzt werden und wenn die
anfangs gebildete, an Kieselsäure reiche Schlacke entfernt wird. Früher wurde der
Puddelproceſs in einem Ofen ausgeführt, dessen Herd mit einem thonigen Sand
ausgefüllt war, so daſs die erhaltene Schlacke derartig reich an Kieselsäure war,
daſs die Oxydation des Phosphors und theilweise auch des Siliciums dadurch gehindert
wurde. Aus demselben Grunde kann man auch zum Bessemer- und zum
Siemens-Martin-Proceſs nur Roheisen mit wenig Phosphor verwenden, da die erhaltene
Schlacke mindestens 45 Proc. Kieselsäure und in Folge dessen nur Spuren
Phosphorsäure enthält. Die Entfernung des Phosphors aus dem Eisen ist nicht von der
Temperatur abhängig, wie Bell meint, sondern von der
mehr oder weniger basischen Natur der Schlacke.
Der Auskleidung der Bessemer- und der Siemens-Martin-Apparate mit reichen Eisenoxyden
steht die Schmelzbarkeit derselben entgegen. Die von Tessie
du Motay in Terre-Noire versuchte Auskleidung einer Bessemerbirne mit
Magnesia wurde des hohen Preises wegen aufgegeben, der von C. W. Siemens versuchte Bauxit war zu reich an Kieselsäure. Auf den
Vorschlag von Gruner kleideten nun S. G. Thomas und P. C.
Gilchrist auf dem Blänavon-Eisenwerke in Südwales eine kleine Bessemerbirne
mit einem Gemisch von Kalk und Natronwasserglas aus; die Phosphorausscheidung war
zwar befriedigend, die Auskleidung aber zu hinfällig. Nun wurden aus einem sandigen
Dolomit unter starkem Druck Steine geformt und bei möglichst hoher Temperatur
gebrannt.Die beim Glühen der genannten Dolomitsteine beobachtete Bildung von Pyroxen
wurde bereits (1879 232 282) kurz erwähnt; die
Krystalle hatten folgende Zusammensetzung:Kieselsäure52,6Thonerde 0,0Eisenoxyd 0,3Kalk27,8Magnesia18,9–––– 99,6.Diese Austreibung der Thonerde, welche hier demnach
die Rolle einer Säure gespielt hatte, ist für die Frage über die chemische
Constitution der Thonerde haltigen Gläser bemerkenswerth.
Dieselben hatten bei 2,8
sp. G. folgende Zusammensetzung:
Kalk
49,3
Magnesia
25,2
Thonerde
11,2
Eisenoxyd
1,5
Kieselsäure
12,3
––––
99,5.
Mit diesem festen, an der Luft keine Feuchtigkeit anziehenden
Silicoaluminat von Kalk und Magnesia wurde die Birne ausgekleidet, auſserdem jeder
Beschickung etwas Kalk und Eisenoxyd zugefügt. Das verarbeitete Roheisen enthielt
1,4 bis 1,5 Proc. Phosphor. Folgende Versuche zeigen den Einfluſs des
Kieselsäuregehaltes der Schlacke:
I
II
III
Schlacke
KieselsäurePhosphorsäureKalk und Magnesia
25,111,540,0
18,814,4–
15,911,7–
Proc.
Phosphorgehalt des Bessemereisens
0,85
0,5
0,08
Beim Versuch I und II waren die Zuschläge nicht genügend, Versuch III war gut
durchgeführt. Ein andere Schlacke einer guten Operation hatte folgende
Zusammensetzung:
Kieselsäure
20,30
Thonerde
3,60
Kalk
30,30
Magnesia
5,30
Eisenoxydul
25,20
Manganoxydul
3,10
Phosphorsäure
11,80
Vanadinsäure
0,36
Schwefel
–
–––––
99,96.
Die hohe Temperatur des Bessemerprocesses hindert demnach nicht die Ausscheidung des
Phosphors, wenn nur dafür gesorgt wird, daſs die Schlacke weniger als 20 Proc.
Kieselsäure enthält und nicht mehr als 11 bis 12 Proc. Phosphorsäure aufzunehmen
braucht. Beim Puddelproceſs kann der Kieselsäuregehalt der Schlacke bis 30 Proc.
betragen. Ueber das Verfahren von S. G. Thomas und P. C. Gilchrist wurde Bd. 232 S. 451 berichtet.
F.
Kokesofen von R. Wintzek in Morgenroth. Das wesentlich
Neue an diesem jüngst patentirten und durch Fig. 9 bis
20 in verschiedenen Ansichten und Schnitten wiedergegebenen Kokesofen (*
D. R. P. Nr. 2005 vom 20. Januar 1878) besteht in der Art der Bodenerhitzung. Die
Sohle des Ofens ist, abweichend von allen anderen Systemen, durch eine Reihe
schmaler Schlitze r durchlocht, und steht dadurch die
Ofenkammer a mit einem darunter liegenden Luftkanal h in Verbindung, welcher aus den an den Kopfenden des
Ofens befindlichen Eingangsöffnungen
i mit atmosphärischer Luft gespeist wird. Aus h tritt letztere in hoch erhitztem Zustand durch die
Schlitze r in die Ofenkammer, durchdringt den dort
lagernden, etwa 0m,6 dicken Kohlenkuchen und
veranlaſst in diesem eine lebhafte Grasverbrennung, heftiger als dies in jedem
anderen Kokesofen möglich ist. Durch diese Einrichtung soll jede selbst die magerste
Kohle eine dichte, brauchbare Koke liefern. Im Uebrigen ist die Ofenconstruction
vielen bis jetzt angewandten Systemen ähnlich. Der Ofen wird durch zwei im Gewölbe
befindliche Oeffnungen b gefüllt und wie üblich
planirt. Die Gase treten durch die beiden seitlich im Gewölbe ausgesparten
Oeffnungen c in einen Seitenkanal und aus diesem,
nachdem sie ihn schlangenförmig durchzogen haben, in einen unter dem Luftkanal
befindlichen Bodenkanal l, welcher durch eine Zunge
derart getheilt ist, daſs die Gase ihn zwei Mal in der Längenrichtung durchstreichen
müssen, und steigen schlieſslich in der Ofenmitte durch die senkrechten Schächtchen
f in den zu dem Schornstein führenden Hauptkanal
g. In letzterem liegen die Steinschieber e zur beliebigen Ueberdeckung der Schächtchen f, wodurch der Ofenzug regulirt werden kann. Zur
Einführung noch weiterer Verbrennungsluft sowohl in die Ofenkammer, als in den
Seitenkanal dienen die im Ofengewölbe und in den Kopfenden des Seitenkanales
befindlichen Oeffnungen k. Der untere Theil des Ofens
ist, zur besseren Erhitzung des Bodens vom Seitenkanal aus, conisch ausgeführt.
–r.
Tafeln
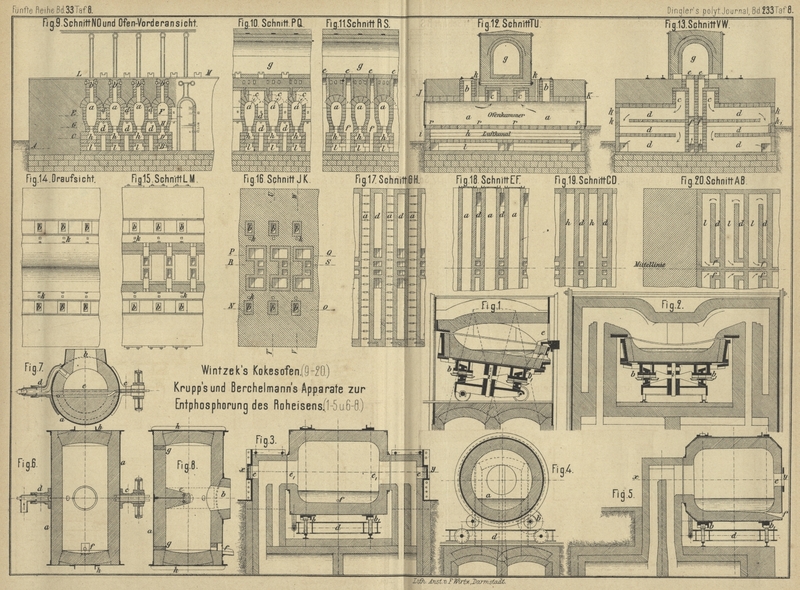