Titel: | Ueber Neuerungen im Hüttenwesen. |
Fundstelle: | Band 241, Jahrgang 1881, S. 56 |
Download: | XML |
Ueber Neuerungen im Hüttenwesen.
Mit Abbildungen auf Tafel 5.
(Fortsetzung des Berichtes S. 206 Bd.
240.)
Ueber Neuerungen im Hüttenwesen.
Der Schemnitzer Rundofen ist nach
einem Bericht von J. H. Langer (Oesterreichische Zeitschrift für Berg- und Hüttenwesen, 1880 S. 609) ein
8förmiger Rundofen nach dem Systeme Pilz, jedoch ohne
Mantel, mit eisernem, durch Wasser gekühlten Gestelle, hat einen Blei- und zwei
Lechabstiche, doppelte Schlackenrinnen, radiale Gasableitungen. Der obere Theil des
Ofens (Fig. 1 bis 4 Taf. 5)
ruht auf 8 durch Quadern festgelegten guſseisernen Säulen, die unter einander durch
Eisenplatten verbunden sind, welche den unterhalb des Kühlringes liegenden Ofentheil
umfassen; blos an der Brustseite unterhalb der Schlackenrinnen ist keine
Umfassungsplatte angebracht. Die 8 Säulen unterfangen den Tragring für das
Ofengemäuer. Für die Mauerung des Kernschachtes sowohl, als für die der übrigen aus
feuerfestem Material herzustellenden Ofentheile wurden aus Dillner Agalmatolith
hergestellte Ziegeln, für die Rauhmauerung gewöhnliche festgebrannte Mauerziegeln
verwendet. Zur Ableitung der Feuchtigkeit dienen kleine Kanäle. Der Abzug der Gase
erfolgt mittels 13 radialer Oeffnungen von 2cm ×
2cm innerem Querschnitt in einen ringförmigen
Kanal e von 27cm
Breite, 115cm Höhe durch den Hauptabzugkanal n von 84cm Breite und
40cm Höhe. Die Gicht ist offen und erfolgt die
Beschickung durch Hände mittels eigener Gefäſsen. Bei dem im Betriebe stehenden Ofen
hat man den über den Gichtboden hervorragenden Theil der Ofenmauerung ganz
zweckmäſsig mit einem guſseisernen Cylinder versehen, wodurch der sonst raschen
Abnutzung des Ziegelmauerwerkes wirksam begegnet wird.
Die 8 Formen des Ofens sind in den 8 Segmenten des Kühlringes angebracht. Die
Zuleitung des Windes erfolgt vom Hauptrohre A aus durch
das ringförmige Rohr B mittels der Rohrstutzen C in Düsen von 33mm
Durchmesser und geschieht die Regulirung mittels eines Schiebers i. Die horizontale Bewegung der Düsen mittels
Zahnstangengetriebe, sowie die verticale Verstellung vermöge der durch Schrauben
beweglichen, tubusartigen Einschaltung sind in Fig. 4
dargestellt. Schlackenrinnen, Lechabstiche, Bleiabstiche, Schlackentiegel und
Schlackenwagen sind in den diesem Ofensystem eigenthümlichen, allgemein
gebräuchlichen Formen ausgeführt.
Die Verarbeitung der angelieferten Gold, Silber, Blei und Kupfer führenden Geschicke
erfolgt im Pilz-Ofen in zwei von einander getrennten Gängen, dem Erz- und dem
Schlackenschmelzen. Zur Erläuterung dieser Arbeiten dienen folgende abgerundete
Angaben a u dem Betrieb des J. 1879:
Zu dem Einschmelzen gelangen – mit Ausnahme von geringen Mengen
beim Schlackenschmelzen verarbeiteter, kupferreicher Erze – die gesammten, theils im
Fortschaufler verrösteten, theils roh zur Verarbeitung gelangenden Erzgefälle. Im J.
1879 wurden hierbei in 159 24stündigen Schmelzerschichten über einer Zustellung
verarbeitet 8795t Gesammtbeschickung, mit einem
durchschnittlichen Gehalte von 0,0953 Proc. in Göldisch-Silber, 0,0209 Proc. in
Gold, 11,6 Proc. in Blei und 0,16 Proc. in Kupfer. In der Gesammtmenge waren
enthalten:
Geröstetes Erz
53,5
Proc.
Rohes Erz
3,5
Lech, Krätz, Flugstaub
7,5
Bleiische Vorschläge
7,0
Eisen haltige Zuschläge: als
Diosgyörer Eisenerz, Schmöllnitzer Kiesabbrände
10,5
Schlacken eigener Arbeit
18,0
und entfallen auf 100k Erz:
Zugeschlagene Hüttenproducte
25,4
Eisen haltige Zuschläge
18,4
Schlacken
31,6
Ausgebracht wurden, ausschlieſslich der zurück
verarbeiteten Schlacken, 3598t,5 und zwar:
Reichblei
19
Proc.
Sonstige Zwischenproducte
21
Schlacken
60
Das Reichblei vom Erzschmelzen hatte:
Göldisch-Silbergehalt
0,8373
Proc.
Goldgehalt
0,0320
Sonstige Zwischenproducte
Schlacken
Göldisch-Silbergehalt
0,0140
bis
0,0693
Proc
0,0107
Proc.
Goldgehalt
0,0128
0,0068
Bleigehalt
14
bis
56
2
Kupfergehalt
1,1
Der Brennmaterialverbrauch betrug:
Für
10t
Erz und Schliech
11,3
Proc.
Kokes
„
„
Gesammtbeschickung
6,39
„
„
Aufgebracht wurden in 24 Stunden 15642k Erz und Schliech, 19439k
Gesammtbeschickung. Der Windverbrauch betrug in der Minute bei einer Pressung von
26mm Quecksilber bei 8 Formen mit 33mm Düsenöffnung 26cbm,32. Das Erzschmelzen schloſs ab mit einem Zugang von 9,70 Proc. Gold,
125,08 Proc. Kupfer und mit einem Abgange von 1,44 Proc. Silber und 9,47 Proc. Blei.
Bei dem Schlackenschmelzen wurden in 160 24stündigen Schmelzschichten 7960t an Gesammtbeschickung aufgebracht. Die
Beschickung bestand aus:
2,7
Proc.
an Kupfer reicheren Erzen mit 0,0369 bis 0,101 Proc.
Göldisch-Silber, 0,0186 bis 0,0268 Proc. Gold, bis 25 Proc. Blei
und3,4 bis 7,7 Proc. Kupfer,
15,0
Proc.
Hüttenproducten (Leche, Treibproducte, Krätz u. dgl.)
mit0,0328 bis 0,2632 Proc. Göldisch-Silber, 0,0013 bis 0,0328
Proc.Gold, 16 bis 85 Proc. Blei,
82,3
Proc.
Schlacken vom Erz- und Schlackenschmelzen mit 0,0018
Proc.Göldisch-Silber, 0,0104 Proc. Gold, 1 Proc. Blei.
Erzeugt wurden:
515t
Reichblei mit 0,3560 Proc. Göldisch-Silber, 0,0056
Proc. Gold,
490t
sonstiger Zwischenproducte mit 0,0094 bis 0,1271 Proc.
Göldisch-Silber, 0,0006 bis 0,0215 Proc. Gold, 18 bis 57 Proc. Blei
und2 bis 23 Proc. Kupfer.
Als Brennmaterial verwendet man Karwiner Kokes und erforderten
10t Gesammtbeschickung 7,33 Proc. derselben.
In 24 Stunden wurden 49t,8 durchgesetzt bei einem
Windverbrauche von 20cbm,32 von 16mm Pressung. Das Schlackenschmelzen schloſs mit
einem Zugange von 10,44 Proc. in Gold, 16,75 Proc. in Silber, 2,89 Proc. in Blei und
mit einem Abgange von 2,92 Proc. in Kupfer ab.
Zur Herstellung von Zink aus
gemischten Erzen befolgt die Swansea Zink Ore Company
folgendes von E. A. Parnell in der Chemical News, 1880 Bd. 42 S. 201 empfohlene Verfahren.
Die vorzüglich in Verwendung genommenen Erze, von denen keines der Aufbereitung
unterzogen werden kann, enthalten als Sulfide:
ZinkProc.
BleiProc.
KupferProc.
SilberUnzenin 1t
Zusammengesetztes Erz von Cavalo in Algier
17
16
–
20
Kupfer haltige Blende von Ain Barbar in Algier
23
–
6
6
Erze aus Italien
20
12
5
Spur
Blauerz von Anglesea
28
12
Gold u.Kupfer
12
Erze von Constantine in Algier
12
5
1,5
12
Die Erze werden geröstet und mit verdünnter Schwefelsäure behandelt. Aus der Lösung
wird das Kupfer durch Eisen, Zink oder Schwefelwasserstoff gefällt, die
zurückbleibende Lösung von schwefelsaurem Zink wird eingedampft und der Rückstand
mit gepulverter Zinkblende erhitzt. Nach der Zersetzungsgleichung 3ZnSO4 + ZnS = 4ZnO + 4SO2 entweicht Schwefeldioxyd, welches zur Herstellung von Schwefelsäure
verwendet wird, während das zurückbleibende Zinkoxyd auf Zink verarbeitet wird. Der
in Schwefelsäure nicht gelöste Rückstand wird in gewöhnlicher Weise auf Blei und
Silber verarbeitet.
C. Wernicke in Stadt Königshütte (* D. R. P. Kl. 80 Nr.
11 676 vom 8. Februar 1880) beschreibt ein Verfahren zur Herstellung von Muffeln für den Zinkhüttenbetrieb durch Aufstampfen
derselben in verkehrter Stellung zwischen Mantel und Kern, nebst Vorrichtungen zur
sicheren Feststellung und leichten Entfernung des Kernes.
Zink und Zinkweiſs läſst
H. Harmet in Denain, Frankreich (* D. R. P. Kl. 40
Nr. 11197 vom 23. März 1880) in Schachtöfen herstellen. Die vorher gerösteten Erze,
die Zuschläge und das Brennmaterial werden in geeigneten Mengen mit Hilfe eines
Aufgebetrichters in die Mitte des Schachtes C (Fig.
5 Taf. 5) eingebracht; der Trichter ist zur Vermeidung von Gasverlusten
mit doppelten Verschlüssen versehen. Man regelt die Menge des zugeführten
Brennmaterials und des Windes durch die oberen Düsen a
dergestalt, daſs man unten im Schachte eine vollständige Reduction erzielt und daſs
der unumgänglich nöthige Ueberschuſs von Brennmaterial erhalten bleibt, durch
welchen im Gestell A die zur Verflüchtigung nöthige
Temperatur erzielt werden soll. Beim Verlassen des Schachtes begegnet die
niedergehende Masse den aus dem Gestell A aufsteigenden
gasförmigen Producten. Alle verflüchtigten Stoffe, einschlieſslich des metallischen
Zinkes, werden mit fortgerissen und durch die Oeffnungen o abgeführt; die festen Massen dagegen sinken herab und gelangen vor die
Düse T, wo die Beschickung unter vollständiger Verbrennung des
Brennmaterials geschmolzen wird.
Wenn nur die Fabrikation von Zinkweiſs bezweckt wird, so
kann man ohne Nachtheil die Höhe des Gestelles dahin verringern, daſs man die
Oeffnungen o der Oxydationszone der unteren Düse T näher bringt. Bei ihrem Austritt aus den Oeffnungen
o bestehen die fortgeführten Stoffe der Hauptsache
nach aus Kohlenoxydgas, Kohlensäure, Zinkdämpfen und verschiedenen Staubmassen, die
schon etwas Zinkweiſs enthalten, wenn die Herddüsen T
den Gasentweichungsöffnungen sehr nahe sind. Jede Oeffnung o führt in eine groſse Heizkammer D, die mit
feuerfesten Steinen ausgesetzt ist und in der durch mehrere in verschiedenen
Richtungen einmündende Düsen t vorzugsweise kalte und
feuchte Luft zur Verbrennung des Zinkes und des Kohlenoxydes unter genügendem Drucke
eingeführt wird, um die Producte fortzuführen und in gewöhnlichen Kammern
abzulagern. Der Druck im Innern des Ofens, in den Leitungen und den
Ablagerungskammern ist groſs genug, um die gasförmigen Producte durch die
Leinensäcke hindurch zu treiben, mit denen die Ablagerungskammern abgeschlossen
sind, ohne daſs man hierzu noch Gebläse zu Hilfe nehmen muſs.
Zur Darstellung von metallischem Zink ist eine
Vergröſserung der Höhe des Gestelles A erforderlich
(vgl. Fig. 6 Taf. 5), damit die Gasableitungsöffnungen o von der Oxydationszone, welche die Düsen T
im Herde umgibt, durch eine reducirende Zone getrennt werden und die Ableitung bei
sehr hoher Temperatur vor sich geht. Die verflüchtigten Producte treten durch die
Oeffnungen o aus, werden durch zwei lange cylindrische
Kammern k geleitet, welche mit Holzkohle gefüllt sind
und in denen sich bei sehr hoher Temperatur die vollständige Umwandlung der
Kohlensäure in Rohlenoxyd und die Reduction von Spuren von Zinkoxyd vollzieht,
welche mit fortgerissen sein können. Durch die Schürlöcher r, welche gewöhnlich mit Lehmpfropfen verschlossen gehalten werden, kann
man den unteren Theil des Brennmaterials öfters auflockern und die Schlacke in das
Gestell abflieſsen lassen. Der Gasdruck in diesen Kammern muſs beträchtlicher als
der atmosphärische Druck sein, damit jeder Luftzutritt verhindert wird. Die
Temperatur wird durch den Strom der verflüchtigten Massen von selbst genügend hoch
gehalten; letztere treten durch die schrägen Leitungen V aus und gehen in den Condensator, welchem man mit Vortheil eine
Ablagerungskammer anfügen kann. Hier wird das Zink von Kohlenoxyd getrennt, das
sodann in Schmelzöfen oder in Regeneratoren Verwendung findet.
Um ein Entweichen der Zinkdämpfe aus der Schüröffnung der
Blechballons zu verhindern, ist dieselbe nach H.
Bugdoll in Godullahütte bei Morgenroth (* D. R. P. Kl. 40 Nr. 11545 vom 6.
Februar 1880) mittels einer sich nach innen öffnenden Klappe geschlossen. Am Ende
des Ballon befindet
sich eine Oeffnung und über derselben eine Tülle mit fest geschlagener Baumwolle,
welche ein Abziehen der Gase, nicht aber ein Durchtreten der entwickelten Zinkdämpfe
gestattet.
E. Ch. Hegeler und F. W.
Matthiessen in La Salle, Illinois, Nordamerika (* D. R. P. Kl. 40 Nr. 10
009 vom 19. October 1879) beschreiben Neuerungen an
Zinkdestilliröfen, welche in mehreren unter einander verbundenen
Retortenkammern zum Durchströmen der Feuergase mit Einlassen zur Luftzuführung
bestehen. Sie verbinden eine Reihe Retortenkammern von vorzugsweise rohrartiger
Gestalt, welche senkrecht, zickzackartig oder horizontal so angeordnet sind, daſs
die theilweise verbrannten Gase, welche vom Generator aus oder direct von der
Rostfeuerung zugeführt werden, diese Rohre entlang strömen, um vollständig verbrannt
zu werden und die Retorten zu heizen. Die Gase werden ferner auf ihrem Wege die
Retortenreihe oder die Kammern entlang dadurch noch weiter verbrannt, daſs, wie
bereits von Hauzeur (1880 235 * 221) empfohlen, Luft zwischen die Retorten oder in bestimmten
Abständen der Länge der rohrartigen Kammern nach oder auf beide Arten eingeführt
wird, so daſs in der letzten Abtheilung oder in der Nähe des äuſseren Endes der
rohrartigen Kammern die Verbrennung dieser Gase vollständig erfolgt.
Die Retorten werden an dem einen Ende auf Vorsprüngen in der Hinterwand, an dem
vorderen Ende durch Tragstücke gehalten. Die im Generator A (Fig. 7 bis
14 Taf. 5) entwickelten, im Kanal B durch
bei C eintretende Luft theilweise verbrannten Gase
treten in die Kammer F, gehen über und zwischen die
Luftretorten G und durch die Durchlochungen o derselben hindurch. Die heiſsen Gase kommen mit der
Auſsenfläche des einen Theiles der zunächst liegenden, mit Erz gefüllten Retorte E in Berührung, wodurch das Erz geschmolzen wird. Die
Temperatur der Gase wird beim Weiterströmen zwischen den Retorten E vermindert; wenn die Gase aber bis an die
Luftretorten G gelangt sind, so wird eine Erhöhung des
Wärmegrades dadurch erzielt, daſs eine kleine Menge heiſser Luft durch die Löcher
o der Retorten G zu
den Gasen tritt. Dies wird bei den nächsten Luftretorten G so lange wiederholt, bis die Feuerungsgase vollständig verbrannt
sind.
Die verbrauchten Feuerungsgase werden durch den Kanal H
von dem äuſseren Ende der kanalartigen Retortenkammer F
nach der Kammer J des Heiſsluftapparates geleitet, wo
sie die Thonrohre j und die Eisenrohre k erhitzen und von hier aus durch den Kanal L in den Schornstein M
entweichen. Durch das Rohr N (Fig. 10 und
12) mit Ventil O tritt kalte Luft oder von
einem Gebläse gelieferter Wind in das Eisenrohrsystem k
und geht dann von hier aus durch die Rohre j, um auf
einen hohen Hitzegrad gebracht zu werden. Die Rohre k
und j
sind an jedem Ende offen
und ragen durch die Wände oder den Boden, durch welche sie gehalten werden, bis in
die offenen ober- und unterhalb derselben befindlichen Räume N1 hinein. Ein Kanal P steht mit der letzten Abtheilung N1 in Verbindung und
führt die Luft von hier in den Kanal Q hinein, welcher
den ganzen Ofen entlang unterhalb der vorderen Enden der Luftretorten G hinläuft. Aus dem Kanal Q wird ein Theil dieser erwärmten Luft durch die Kanäle R bis U (Fig. 7) vor
oder hinter die Luftretorten geführt. Diese Kanäle stehen durch die kleinen Kanäle
r bis u mit jeder der
Luftretorten in Verbindung, von welchen aus die heiſse Luft durch die Oeffnungen o in den Ofen hineingeht, um die Verbrennung der
Feuerungsgase zu unterstützen. Der Kanal Q steht ferner
durch den kurzen Kanal C mit dem Graskanal B in Verbindung, um hier eine zu regulirende Menge Luft
einzuführen. In der Nähe der Abtheilungen N1 steht der Kanal P mit
einem mit Ventil v versehenen Kanal V in Verbindung (Fig. 10 und
12), so daſs die Menge der in die Kammer W
(Fig. 11 und 12)
eingeführten heiſsen Luft regulirt werden kann. Durch die Kammer W geht die heiſse Luft in den Gasregenerator A, wo dieselbe statt kalter Luft zur Gaserzeugung
angewendet wird.
Fig.
15 Taf. 5 zeigt einen gewöhnlichen belgischen Ofen mit dieser Vorrichtung.
Die Feuerungsgase von dem Roste A oder von einem mit
einem Generator verbundenen Gaskanal treten unten in die Kammer F, wo sie einer gewissen Menge durch die unteren
Luftretorten G und den Kanal Q zugeführten Luft begegnen, steigen weiter nach oben, wo sie von neuem
Luft durch die zweiten Retorten G zugeführt erhalten,
strömen nun bis unterhalb des Bogens und erhalten durch die Oeffnungen e eine fernere Menge Luft zugeführt. Von hier aus gehen
die Gase nach unten durch die zweite Kammer F, wo bei
G Luft zugeführt wird, gelangen von hier aus durch
den Abfluſskanal und hierauf nach dem Schornstein oder Heiſsluftapparat.
Tafeln
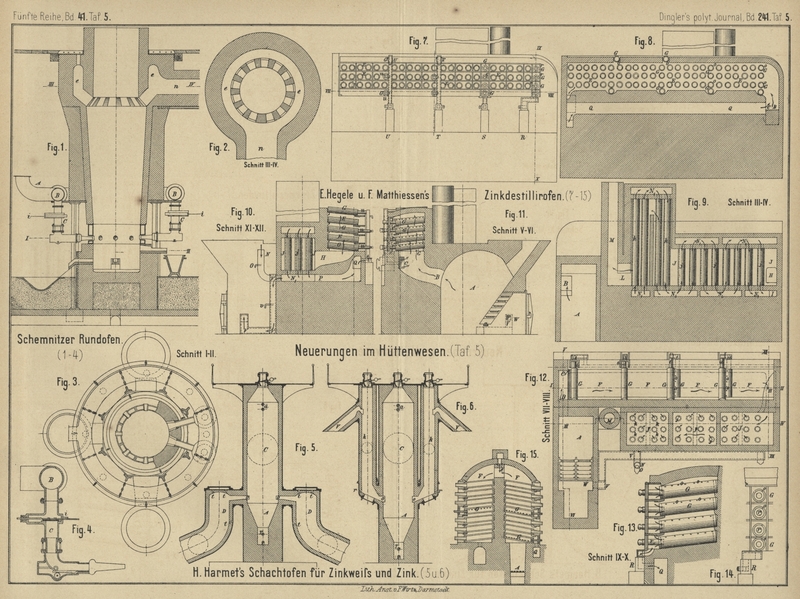