Titel: | Ueber die Entphosphorung des Roheisens. |
Fundstelle: | Band 243, Jahrgang 1882, S. 42 |
Download: | XML |
Ueber die Entphosphorung des
Roheisens.
Mit Abbildungen auf Tafel 5.
Ueber die Entphosphorung des Roheisens.
Wie auf der Versammlung des Iron and Steel
Institute am 11. October 1881 zu
London von S. G. Thomas
hervorgehoben wurde, sind augenblicklich 36 Bessemerbirnen im Betrieb, 30 im Bau,
ausschlieſslich für den basischen Proceſs.Die Patente von S. G. Thomas haben nach Kupelwieser folgende Werke erworben: Die
Angleur-Stahlwerke, die Eisenwerke in Ars an der Mosel, die Athus-Werke, die
Burbacher Gesellschaft, der Bochumer Verein, die Chatillon- und
Commentry-Gesellschaft, die Denain-Werke, Dietrich in Niederbronn, die Dillinger Gesellschaft, die
Dortmunder Werke, die Gutehoffnungshütte, der Hoerder Verein, die Ilseder
Hütte, das Hüttenwerk in Kladno, in Longwy, die Maximilian-Hütte, die
Gesellschaft von Montataire, die Hütte zu Ougree, Phönix in Ruhrort, Rothe
Erde bei Aachen, die Rheinischen Stahlwerke, Schneider in Creuzot, Schneider und
de Wendel in Joeuf, Stumm in Neunkirchen, die Gesellschaft von St. Chamond, die
Société de Nord et de l'Est, die Teplitzer, Warschauer, De Wendel'schen
Werke, die Witkowitzer Hütte u.a.
Nach den auf derselben Versammlung gemachten Mittheilungen von P. Kupelwieser ist die verhältniſsmäſsig geringe
Dauerhaftigkeit des feuerfesten Futters unbestritten der wunde Punkt des Processes. Ungeachtet aller
zahlreichen Versuche, welche mit anderen Materialien in einigen Fällen mit guten
Resultaten gemacht worden sind, gebrauchen die Werke, soweit bekannt, noch die
ursprünglich von Thomas vorgeschlagenen basischen
Ziegel oder die Mischung von gebranntem Kalk oder Theer. Auf manchen Werken werden
gemahlene basische Ziegel mit 5 bis 10 Proc. Theer sowohl für das Futter, als auch
für Nachbesserungen angewendet. Basische Düsen sind, soweit bekannt, obschon man
dieselben an manchen Orten erzeugt und versucht hat, jetzt nicht in ständigem
Gebrauche. Als Birnenböden werden solche gebraucht, bei denen um eiserne Rundstäbe
herum, welche die Windöffnungen bilden sollen, die Masse gestampft wird, oder der
Düsenboden, in welchem gewöhnliche feuerfeste Düsen eingesetzt sind und der übrige
Boden entweder mit basischen Ziegeln, oder mit gestampfter Masse ausgefüllt ist. Der
auswechselbare Boden von Holley (1881 239 * 465) ist in
nahezu allen basischen Betrieben im Gebrauch. Derselbe dürfte in neuen Werken mit
groſsem Vortheile angewendet werden.
Sowohl bei zum basischen Processe umzubauenden vorhandenen Bessern er werken, als
auch bei neuen ist es wünschenswerth, daſs die Gieſsgrube etwas von den
Bessemerbirnen entfernt liegt, um genügenden Raum zum Einbringen der basischen
Zuschläge und zum Fortschaffen der diesem Processe eigenthümlichen groſsen Menge von
Schlacken an denselben zu haben. Deshalb wird gewöhnlich die Gieſspfanne durch eine
mechanische Vorrichtung oder eine kleine Locomotive aus der unmittelbaren
Nachbarschaft der Birne zu einer getrennten Gieſsgrube gebracht, wo das Gieſsen,
Putzen und das Herausnehmen der Guſsblöcke geschieht.
Die Kosten des basischen Processes werden wahrscheinlich immer etwas höher sein als
die des sauren; jedoch wird das zu ersterem verwendete Roheisen wenigstens so viel
billiger bleiben, um die höheren Kosten aufzuwiegen. Dagegen ist der basische
Proceſs mit Rücksicht auf die Qualität seiner Producte nicht allein dem sauren
gleich, sondern sogar überlegen.
Schon bei den ersten Versuchen mit dem basischen Proceſs, welche vor 2 Jahren in
Witkowitz angestellt wurden, erkannte man, daſs der Hauptwerth des neuen Verfahrens
für die Hütte nicht darin liege, daſs sie, wie anderwärts, einen billigeren Stahl
herstellen könne, sondern darin, daſs sie mit den vorhandenen Materialien ein
Product zu erzielen im Stande wäre, welches in Bezug auf seine Reinheit sich mit den
berühmten Qualitäten der Steierischen Werke messen könne. Da das vorhandene, vor 15
Jahren erbaute Bessemerwerk sich nicht zu einem schnellen Betriebe des basischen
Processes eignete, so wurde anfangs die Aufmerksamkeit nur auf die Herstellung von
Bessemerfluſseisen für Bleche gerichtet; als jedoch im März 1881 die beiden Birnen der neuen speciell
für das Thomas-Gilchrist-Verfahren erbauten Anlage in Betrieb kamen, wurde die
Nachfrage nach dem basischen weichen Fluſseisen so groſs, daſs man sich entschied,
die neue Anlage einzig zur Herstellung von entphosphortem weichem Metall und die
alte zur Herstellung von Schienenstahl nach dem alten Bessemerproceſs zu betreiben.
Bei dem Ausbau der neuen Anlage durch zwei weitere Bessemerbirnen an Stelle der
kleinen alten besteht die Absicht, nichts anderes als basischen Stahl zu machen.
Witkowitzer Fluſseisen des basischen Processes hat sich bewährt zur Herstellung von
Kesselblechen, von denen viele Tausend dem Röhrenwalzwerke von Huldschinsky und Söhne in Gleiwitz zur Fabrikation von
geschweiſsten Locomotivröhren geliefert sind und den aus dem besten schwedischen
Material gewalzten gleich befunden wurden. Besonders bemerkenswerth sind jene
Versuche, bei welchen durch einen Rohrausweiter die absolute Festigkeit der
Schweifsstelle gezeigt wurde, wobei ohne Riſs an derselben eine weite Ausdehnung von
9 bis 17mm bei einem ursprünglichen Durchmesser
von 48mm entsprechend einer Ausdehnung von 20 bis
36 Procent des Materials an dem Umfang erreicht wurde. Die Röhren können mit groſser
Leichtigkeit kalt oder warm umgebörtelt und ohne zu reiſsen gebogen werden. Die
Leichtigkeit, mit welcher entphosphortes Eisen schweiſst, ist daraus zu erkennen,
daſs die Scherabschnitte paketirt und zu Rundeisen ausgewalzt werden, welches ein
vorzügliches Nieteisen gibt. Wenn die Blechabfälle mit Luppeneisen paketirt und zu
Blechen ausgewalzt werden, so erhält man Schweiſseisenbleche, welche in Bezug auf
Zugfestigkeit und Ausdehnung die besten Bleche dieser Art übertreffen. Dünne Bleche
aus entphosphortem Eisen werden zur Fabrikation von gestanzter Waare verwendet.
Die elektrische Leistungsfähigkeit des basischen Eisens übertrifft die des
schwedischen. Die nachfolgenden Tabellen und Analysen geben eine Vorstellung von dem
verwendeten Rohmaterial und dem hieraus gewonnenen Producte:
Festigkeitsproben.
1) Mäſsig harterSchienenstahl
2) Härtere Sorte fürBleche, Achsen,
Winkel-und Nieteisen
3) Weichstes Eisen fürTelegraphendrahtund
Stanzwaare
Zugfestigkeit
58,4 bis 63,1
45 bis 50
36 bis 39k/qmm
Contraction
51,5 bis 36,9
64 bis 55
77 bis 72%
Dehnung
20 bis 20,5
25 bis 20
37 bis 33%
Zusammensetzung des Stahles.
Stahl Nr. 1
2
3
Kohlenstoff
0,45
0,19
0,06
Mangan
–
0,34
0,30
Silicium
Spur
Spur
0,00
Phosphor
0,04
0,04
0,02
Schwefel
0,06
0,04
0,03
Kupfer
0,07
0,20
–
Zusammensetzung des verwendeten Roheisens.
Silicium
0,54
0,11
0,62
Mangan
1,00
1,16
1,38
Phosphor
1,95
3,46
2,00
Schwefel
0,23
0,09
0,08
Kupfer
0,06
0,20
0,09
Zusammensetzung der gebrauchten wiederkohlenden Zuschläge.
1) Spiegel,0,6 Proc. vomRoheisen
2) Graues Bessemer-roheisenWovon 7,5 Proc. verwendet wurde, anstatt des Spiegels für
Schienenstahl, wenn die Beschickung über 1 Proc. Mangan
enthält.
Ferro-mangan mit 2verwendet biszu 0,6
Proc.
Silicium
0,18
1,43
–
Mangan
13,80
2,51
73
Phosphor
0,11
0,15
–
Der bei Stahl Nr. 2 gegebene Zuschlag betrug 1 Proc. von
50procentigem Ferromangan.
Die Schlacke, welche in den Hochöfen verhüttet wird, um den Phosphorgehalt des
Roheisens zu erhöhen und um als Fluſsmittel zu dienen, hatte folgende
Zusammensetzung:
Vor dem Zusätze
Kieselsäure
7,00
4,75
Eisenoxydul
17,44
18,04
Thonerde
Spur
Spur
Manganoxydul
3,33
4,70
Kalk
53,32
50,06
Magnesia
0,78
0,76
Phosphorsäure
16,83
22,00
Phosphor
7,30
9,54
Schwefel
0,72
–
Um einen genügend heiſsen Stahl zu erhalten, soll in der Regel die Summe des
Siliciums und des Phosphors im Roheisen mindestens 2,5 Proc. betragen. Es ist aber
auch Roheisen, welches von dieser Regel bedeutend abweicht, vortheilhaft verhüttet
worden. Zur Ausfütterung sind mit Kalkstein ebenso wie mit Dolomit gute Resultate
erzielt worden. Kupelwieser ist jedoch der Meinung,
daſs das Futtermaterial nur einen geringen Gehalt an Kieselsäure haben darf;
dasjenige von Witkowitz ist aus Kalkstein hergestellt, welcher 1 bis 1,5 Proc.
Kieselsäure enthält. Die Ziegel, welche in Witkowitz gebraucht werden, um die Birnen
auszukleiden und die Böden zu machen, bestehen vornehmlich aus Kalk mit ein wenig
Magnesia und ungefähr 2,5 bis 3 Proc. Kieselsäure. Die aus diesen Ziegeln
hergestellten Böden halten 30 und mehr Hitzen aus, wenn die Düsen nach 5 bis 8
Hitzen ausgewechselt werden und um dieselben neues basisches Material eingebracht
worden ist. Zu diesem Zwecke wird der Boden vom Birnenkessel getrennt. Das Abnehmen
der Böden, das Ausbrechen der alten Düsen, das Einsetzen der neuen und das
Einstampfen von neuem Material um dieselben herum dauert 1 bis 3 Stunden, so daſs
der in Stand gesetzte
Boden nach dieser kurzen Unterbrechung wieder gebraucht werden kann. Die Düsen sind
aus saurem Material hergestellt und halten 5 bis 8 Hitzen aus. Die gänzliche
Erneuerung der Böden findet statt, nachdem dieselben im Durchschnitt 5 oder 6 mal
ausgebessert worden sind. 6 Böden sind für einen ununterbrochenen Betrieb von 150
bis 200 Hitzen genügend, oder für so viele Hitzen, wie 2 Birnen gewöhnlich ohne
Erneuerung des Futters aushalten. Es folgt hieraus, daſs für sehr groſse
Productionen 4 Birnen beim basischen Processe nothwendig sind. Es hat sich
herausgestellt, daſs der Abbrand beim basischen Proceſs von 15 bis zu 17 Proc.
wechselt; es tritt der gröſsere Verlust dann ein, wenn eine sehr weiche gute
Qualität erblasen wird. Da der höhere Abbrand in diesem Falle verhältniſsmäſsig
unwichtig ist, so ist es üblich, mehr Kalk zu verwenden, als wirklich nothwendig
ist. Für Schienenstahl wird weniger Kalk gebraucht und es ist der Abbrand, da das
Nachblasen kürzer ist, geringer.
Die seit dem Frühjahr 1881 in Betrieb gesetzte Anlage ist in Fig. 9 und
10 Taf. 5 veranschaulicht. Die beiden Birnen C, zu beiden Seiten des Cupolofens A, sind
eiförmig und von vollkommen symmetrischer Gestalt mit der Oeffnung an der Spitze,
wenn sie vertical stehen. Senkrecht über dem Munde ist ein beweglicher Kamin K, um die aus der Birne emporsteigenden
Verbrennungsproducte zu entfernen. Die Anlage ist so eingerichtet, daſs die Birnen
auf beiden Seiten ihren Inhalt ausgieſsen können. Es ist erwiesen, daſs die Seite,
auf welcher bei geneigter Lage der Birne das Metall nach dem Nachblasen liegt, durch
die Anhäufung der feuerfesten basischen Schlacke beständig enger wird, während die
obere Seite der Birne einer bedeutenden Abnutzung unterliegt. Bei dem abwechselnden
Gebrauche der beiden Seiten sichert man sich eine gröſsere Dauerhaftigkeit des
Futters, während der Schlund vollkommen rein bleibt. Diese Einrichtung hat ihrem
Zweck vollständig entsprochen. Wegen dieser Eigenthümlichkeit der Construction ist
eine doppelt wirkende Dampfmaschine zum Drehen der Birnen gewählt; es sind 2
Wendemaschinen m, Aufzug n
und Gieſsvorrichtungen g vorhanden. Jede Birne hat eine
lange Gieſsgrube auf jeder ihrer beiden Seiten in der Richtung ihrer Achse. Auf der
Kante der Gruben liegen Schienen, welche die an den entgegengesetzten Seiten
liegenden Gruben mit einander verbinden. Anstatt mittels eines Drehkrahnes wird die
Gieſspfanne, welche auf einem Wagen ruht, durch Heben und Senken des Geleises, auf
welchem derselbe läuft, in die Stellung gebracht, welche zum Eingieſsen des Metalles
nothwendig ist. Zu diesem Zwecke befindet sich unter der Birne ein hydraulischer
Kolben, welcher oben ein Kreuzstück trägt, auf dem die Enden der beiden Geleise
ruhen, welche von den beiden Gieſsgruben hier zusammenlaufen, ohne jedoch mit
einander verbunden zu
sein. Ein jedes dieser Geleise ist auf 6m
Entfernung von jeder Seite der Birne auf starken Trägern befestigt. Während nun die
Enden des Geleises, welche unter der Birne sich befinden, mittels des Kolbens
gehoben werden, ruhen die anderen Enden auf 6m von
der Birne entfernten Zapfen und nimmt das Geleise eine geneigte Stellung an. Auf
diese Weise wird der Wagen mit der Gieſspfanne unter den Mund der Birne durch die
Aufwärtsbewegung des Geleises gebracht, wenn dieselbe geleert werden soll. Wird das
schräge Geleise beim Drehen der Birne gesenkt, so wird die Gieſspfanne nicht allein
gesenkt, sondern bewegt sich noch in horizontaler Richtung, um ihre Stellung unter
dem Schlünde der Birne zu behalten, bis die Entleerung derselben beendigt ist.
Das Fortnehmen und Einsetzen der auswechselbaren Böden, welche sich auf dem über dem
Kolben stehenden Wagen befinden, geschieht durch dieselbe Vorrichtung; es stehen
alsdann je zwei Räder des Wagens in gleicher Entfernung vom Mittelpunkte auf einem
jeden beweglichen Geleise. Auf diesem unter der Birne herlaufenden Geleise bewegen
sich besondere Wagen, welche zur Aufnahme der vor dem Spiegeleisenzusatze
herausgeworfenen Schlacke bestimmt sind, und es wird die Schlacke unmittelbar von
hier zum Hochofen zur weiteren Verwendung befördert. Die Gieſspfanne läuft vorwärts
und rückwärts, die Schlacke wird fortgeschafft, der Guſsblock wird geputzt und
schlieſslich die Auswechslung der Böden bewerkstelligt; dies Alles geschieht auf
demselben Geleise und versieht eine kleine 10e-Locomotive diesen ganzen Betrieb.
Die Darstellung des sehr weichen Eisens wird einigermaſsen schwierig und
verhältniſsmäſsig kostspielig gemacht durch die Unruhe beim Gieſsen der weichsten
Qualitäten. Die während des Abkühlens in den Gieſsformen stattfindende heftige
Gasentwicklung verursacht bis jetzt selbst beim sorgfältigsten Gieſsen
beträchtlichen Verlust an schlechten Köpfen. Dieser Abfall vergröſsert, obgleich er
ein ausgezeichnetes reines Material für den Siemens-Martin-Proceſs ist, den Verlust
bei Herstellung dieser weichsten Qualitäten erheblich.
Tafeln
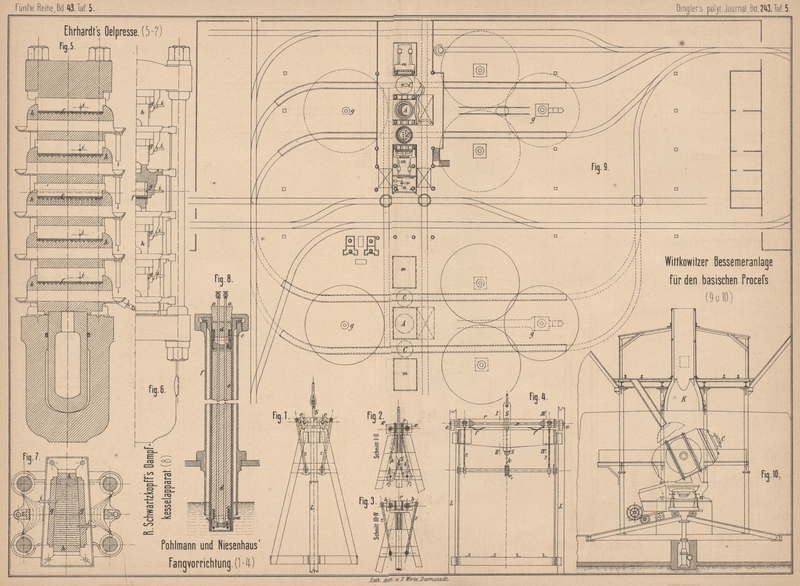