Titel: | Ueber die Herstellung von Leuchtgas. |
Fundstelle: | Band 248, Jahrgang 1883, S. 26 |
Download: | XML |
Ueber die Herstellung von Leuchtgas.
(Fortsetzung des Berichtes Bd. 247 S.
420.)
Patentklasse 26. Mit Abbildungen auf Tafel 3.
Ueber die Herstellung von Leuchtgas.
Die Münchener Generatoröfen (vgl. 1881 240 * 293) sind nach einem Berichte von N. H. Schilling und H.
Bunte im Journal für Gasbeleuchtung, 1882 S.
727 abermals verbessert. Die zur Vergasung der Kokes nöthige Luft tritt durch die
mit Schieber regulirbare Oeffnung A (Fig. 1 bis
5 Taf. 3) ein und mischt sich mit den aus dem Kasten B aufsteigenden Wasserdämpfen. Das Gasgemisch
durchzieht die Kanäle c bis c3, erwärmt sich an den durch die
abziehenden Rauchgase geheizten Kanalwänden, tritt unter dem Planrost D aus und gelangt durch den Aschenraum w in die Brennschicht. Die gebildeten Generatorgase
gehen durch den Kanal F zum Ofen und treffen in den
Brennern G mit der vorgewärmten Luft zusammen. Die
Verbrennungsgase durchziehen den Retortenofen in der Richtung der Pfeile, verlassen
denselben am Ende des Kanales z und treten in die
Regenerationsanlage. Die heiſsen Gase gehen durch die Kanäle o bis o3,
welche zwischen den Kanälen n bis n4 für Vorwärmung der
secundären Luft liegen, dann durch Kanal o4, durch dessen Wände das nach dem Generator
ziehende Gemisch von Luft und Wasserdampf erwärmt wird, treten bei r unter den Wasserkasten B
und gelangen durch s in den Rauchkanal O.
Zur rascheren Uebertragung der Wärme aus den Rauchgasen auf die zum Ofen ziehende
Luft und zur Erreichung eines festen Aufbaues und sicheren Fugenschlusses der
Regeneration sind die einzelnen Kanäle mit gelochten Steinen durchzogen, welche die
Wärme abgebende Fläche vergröſsern. Der Rauchschieber zur Regulirung des
Schornsteinzuges befindet sich hinter der Regeneration, nicht hinter dem Ofen, damit
die Druckdifferenz in den neben einander liegenden Kanälen möglichst gering gemacht
werden kann. Die Heizfläche des Wasserkastens unter dem Generator ist so gewählt,
daſs die für alle Fälle ausreichende Dampfmenge von 1000 bis 1300k erzeugt werden kann, um die Schlackenbildung
völlig zu verhindern. Um die Menge des entwickelten Dampfes reguliren zu können, ist
eine stellbare Klappe P vorhanden, durch welche kalte
Luft zu den Rauchgasen geleitet und so die Temperatur derselben entsprechend
ermäſsigt werden kann.
Hat sich bei Verwendung von Kokes mit 14 bis 16 Proc. Asche nach etwa 36 Stunden der
Aschenraum w mit Verbrennungsrückständen gefüllt, so
werden dieselben in folgender Weise entfernt: Durch die Oeffnungen e, welche für gewöhnlich dicht verschlossen sind,
werden Eisenstäbe gesteckt, um das im Generator befindliche Brennmaterial
abzufangen. Die Verschluſsdeckel R und S an der Brust des Ofens werden alsdann abgenommen und
die auf dem Rost liegende Asche mit einer Krücke entfernt, alsdann werden sämmtliche
Putzöffnungen wieder geschlossen.
Das im Kasten B verdampfte Wasser wird durch
ununterbrochenen Zulauf von v aus ersetzt; ein
Ueberlauf führt das überschüssige Wasser ab. Um ferner bei Inbetriebsetzung des
Ofens die Regeneration ausschalten zu können, sind Verbindungskanäle U angebracht, durch welche die Rauchgase aus dem Ofen
direkt in den Rauchkanal abgeleitet werden können.
Derartige Oefen sind seit dem J. 1881 auf der Gasanstalt München in regelmäſsigem
Betrieb. Bei einer Batterie von 6 Oefen wurde die Menge der destillirten Kohlen
(Saarkohle mit 10 Proc. Plattenkohle), das Gewicht der zur Heizung verbrauchten
Kokes und die erzeugte Gasmenge ermittelt, und zwar einige Monate nach der
Inbetriebsetzung im Oktober 1881 und am Schluſs des Betriebes im Februar und März
1882. Während des Sommers waren die Oefen auſser Betrieb. Im September wurden
dieselben ohne jede Ausbesserung wieder in Betrieb genommen und eine 3.
Beobachtungsreihe durchgeführt. Es ergaben sich folgende Resultate:
Gasausbeute für den Ofen in 24 Stunden
2300cbm
Kohlen destillirt in 24 Stunden in 8 Retorten
7350k
Kokesverbrauch für jeden Ofen in 24 Stunden
800
Gasausbeute auf jede Retorte in 24 Stunden
287cbm
Gasausbeute für Ofen und Ladung in 4 Stunden
383
Gasausbeute auf 100k
Kohlen
31
Kohlen destillirt auf 1 Retorte in 24 Stunden
919k
Kohlen destillirt für Retorte und Ladung
153
Kokesverbrauch (mit 14 Proc. Asche) auf 100k destillirte Kohlen
10,9
Kokesverbrauch (mit 14 Proc. Asche) auf 100cbm Gas
34,8
Die einzelnen Beobachtungen aus den verschiedenen Perioden gaben ein vollständig
übereinstimmendes Resultat; namentlich zeigte sich, daſs die Oefen durch
Auſserbetriebsetzung und erneutes Anfeuern an ihrer Leistungsfähigkeit nichts
verloren hatten. Der Aufbau der Regeneration und die Isolirung der einzelnen Kanäle
ist so angeordnet, daſs dieser Theil der Anlage von Temperaturunterschieden nicht leidet
und daſs der Einbau auf Jahre hinaus ohne jede Ausbesserung völlig unverändert
bleibt. Daſs dies bei der bezeichneten Construction in der That der Fall ist, hat
überdies eine nunmehr 4jährige Erfahrung in der Regenerationsanlage der älteren
Oefen gezeigt. Ebenso haben sich die Generatorschächte nach jahrelangem Betrieb
vollständig unverändert erhalten.
Die Generatorgase enthalten im Mittel 8,6 Proc. Kohlensäure, 20,6 Proc. Kohlenoxyd,
15 Proc. Wasserstoff und 55,8 Proc. Stickstoff. Dieselben treten mit etwa 1150° in
den Ofen. Die Verbrennungsgase enthalten 17 bis 19 Proc. Kohlensäure, mit etwa 2,5
Proc. Sauerstoff oder geringen Mengen von Kohlenoxyd. Sie verlassen den Ofen mit
etwa 1400°. Nachdem sie die Züge o bis o3 durchlaufen und
einen Theil ihrer Wärme an die in den zwischenliegenden Kanälen aufsteigende Luft
abgegeben haben, besitzen dieselben noch eine Temperatur von 900°, während die zum
Ofen tretende Verbrennungsluft vor ihrem Eintritt in die Brennerschlitze in den
Kanälen n bis n4 bis auf etwa 1000 bis 1100° sich erwärmt hat.
Weiter nach abwärts gehend umspülen die Rauchgase die Kanäle c bis c3 und
erwärmen die nach dem Generator ziehende Luft auf 350°; endlich erzeugen dieselben
beim Durchgang durch die Kanäle r den für den
Generatorbetrieb nöthigen Wasserdampf und treten mit etwa 550° in den
Rauchkanal.
Einer Abgangstemperatur der Rauchgase von 1400° würde ohne Regeneration ein Verlust
von etwa 64 Procent vom Heizwerth der Kokes entsprechen; durch die
Regenerationsanlage werden die Rauchgase auf 550° abgekühlt und dadurch der Verlust
auf etwa 25 Proc. ermäſsigt. Die auf solche Weise gewonnene Wärme wird dem Ofen
wieder zugeführt und zwar etwa 20 Proc. durch die erhitzte Verbrennungsluft, 6 Proc.
durch die vorgewärmte Generatorluft; etwa 5 Proc. werden zur Wasserverdampfung
benutzt, während der Rest durch Leitung und Strahlung der Anlage nach auſsen
verloren geht.
E.
Langen in Cöln (* D. R. P. Nr. 18352 vom 24. Mai 1881) construirte einen Ofen zur ununterbrochenen Herstellung von Leuchtgas oder
Heizgas. Das im Generator D (Fig. 13
Taf. 3) erzeugte Gas steigt aufwärts durch Oeffnungen e
in den concentrischen Heizraum H, während das im
Destillationsraume C erzeugte Leuchtgas durch
Oeffnungen o in den den Füllraum A umgebenden Mantel c
tritt, von wo es durch ein Gebläse abgesaugt wird.
Zur Nutzbarmachung der in den Verbrennungsgasen enthaltenen Wärme führen Abzugskanäle
n vom unteren Theil des Heizraumes H in den Regenerator. Durch diesen ziehen die
Verbrennungsgase in den Schornstein M, indem sie die
Platten s heizen. Durch die Luftkanäle r strömt die durch die heiſsen Platten s erhitzte Luft in den Heizraum H unmittelbar neben dem Heizgas.
Ein anscheinend dem Münchener ähnlicher Generatorofen auf dem
Pforzheimer Gaswerk verbraucht, um aus 100k Kohlen 30cbm Gas zu erzeugen, nach
Mittheilungen von H. Brehm im Journal für Gasbeleuchtung, 1882 S. 558 nur 11k Kokes.
Nach dem Betriebsberichte des städtischen Gaswerkes in
Bonn betrug im Berichtsjahre 1881/82 die
Gasproduction 1530919cbm. 100k Kohlen lieferten im Durchschnitt 28cbm,02 Gas; die durchschnittliche Gaserzeugung für
Retorte und Tag betrug 187cbm. Die Ofenfeuerung
erforderte 1020409k oder 27,46 Procent der
erzeugten Kokes, die Dampfkesselfeuerung 182500k.
Zur Entgasung von 100k Kohlen waren 18k,07, zur Erzeugung von 100cbm Gas 66k,65
Kokes erforderlich. 100k Kohlen gaben 5k,05 Theer und 10k,02 Ammoniakwasser. Für je 100cbm
erzeugtes Gas waren für 4,458 M. Kohlen erforderlich; dagegen wurden 2,262 M. für
Kokes, 0,748 M. für Theer und 0,464 M. für Ammoniakwasser eingenommen.
Versuche, die Leuchtkraft des Gases durch rheinische
Schieferkohlen zu verbessern, muſsten des hohen Schwefelgehaltes wegen
wieder aufgegeben werden. Bei Versuchen mit dem Verfahren von Riebeck (1881 241 323),
welches anfangs recht günstige Resultate lieferte, trat später der Uebelstand ein,
daſs bei schärferem Betriebe unter Anwendung höherer Hitzegrade eine zu frühe
Zersetzung des Oeles stattfand, so daſs sich wohl eine starke Gasausbeute – etwa
100cbm für 100k –, aber keine Vermehrung der Leuchtkraft ergab; eine Aufbesserung von
mehr als 1 ½ Lichtstärken konnte überhaupt nicht erzielt werden (dieselbe fand bei
etwa 1,25 bis 1,5 Proc. statt) und wirkte ein gröſserer Zusatz selbst nachtheilig
auf die Leuchtkraft des Gases ein. Ziemlich dasselbe Resultat ergab die Anwendung
von Steinkohlenziegeln, die mit Harz und Braunkohlen theerölen getränkt waren.
Bei dem in Fig. 6 und
7 Taf. 3 dargestellten Scrubber von O. Mohr in Dessau (*D. R. P. Nr. 18842 vom 11. November
1881) geht das bei g eintretende Leuchtgas bei e in den inneren Cylinder A einer sich drehenden Trommel, welche mit den Durchgang des Gases
gestattenden Ringen a ausgefüllt ist. Nachdem es hier
groſse benetzte Oberflächen berührt hat, geht es bei o
in den Cylinder B, dann in die ebenfalls mit Ringen
ausgesetzte Trommel C und entweicht schlieſslich durch
die Oeffnungen d. Das bei c eintretende, zur Wäsche verwendete Wasser kann gleichzeitig zum Betriebe
eines Zellenrades dienen, welches die Scrubberachse antreibt.
Der Condensator von O. Mohr
(* D. R. P. Nr. 19986 vom 20. April 1882) besteht, wie Fig. 8 Taf.
3 andeutet, aus zwei Gehäusen, zwischen denen das von a
nach b ziehende Gas hindurchgeht. Beide Gehäuse sind
zur Vermehrung der Oberfläche mit Rippen e versehen.
Zur Kühlung werden die Condensationsflächen aus den Siebröhren v und w mit Wasser
berieselt. Auſserdem soll durch das Blech n die Luft
gezwungen werden, an den Condensationsflächen aufzusteigen.
Der in Fig. 9 bis 12 Taf. 3
veranschaulichte Waschapparat von C. Walker in Lilleshall und W. T.
Walker in Highgate (* D. R. P. Nr. 18 249 vom 16. September 1881) wird aus einer Reihe von
Behältern C gebildet, welche, aus Metallblechen
gebogen, die Form von umgekehrten Trögen haben. Unten sind dieselben mit Schlitzen
a versehen; ihre mit b
bezeichneten Enden sind geschlossen; der obere innere Theil steht aber mit dem Räume
D in Verbindung. Das durch Rohr d zugeführte Gas tritt von D aus durch Oeffnungen e in die Behälter C, und durch die die Schlitze a bedeckende Waschflüssigkeit in den oberen Theil n des Waschapparates, um schlieſslich in dem Scrubber B aufzusteigen.
Tafeln
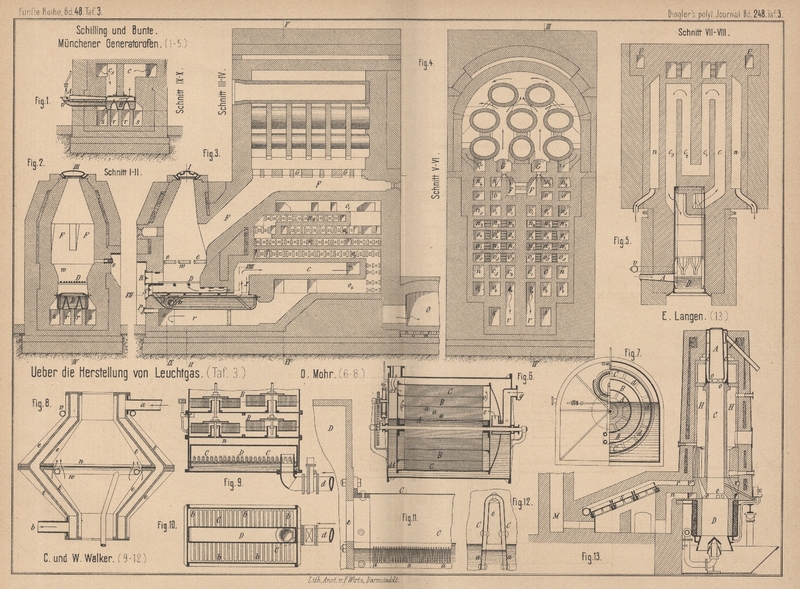