Titel: | Maschinen zur Verfertigung hölzerner Wagenräder. |
Fundstelle: | Band 249, Jahrgang 1883, S. 487 |
Download: | XML |
Maschinen zur Verfertigung hölzerner
Wagenräder.
Mit Abbildungen auf Tafel 33.
Maschinen zur Verfertigung hölzerner Wagenräder.
Ueber einen ganzen Satz zur Fabrikation von Wagenrädern bestimmter Maschinen, welche
von der bekannten Maschinenfabrik Périn, Panhard und
Comp. in Paris gebaut werden, bringt die Revue
industrielle, 1882 S. 314 unter Beigabe von Abbildungen Beschreibungen,
denen nachfolgender Auszug entnommen ist. Ohne auf den Arbeitsgang bei der Herstellung hölzerner
Wagenräder näher einzugehen, in welcher Beziehung auf einen früheren Artikel über
die entsprechenden Maschinen von Guilliet (vgl. 1872
206 * 5) verwiesen wird, sollen im Folgenden nur die
Eigenthümlichkeiten der Périn und Panhard'schen Specialmaschinen hervorgehoben
werden.
Die Maschine zur Formgebung der Speichen ist im
Wesentlichen eine 4 fache mit Fräsen arbeitende Copirmaschine. Die vorgeschnittenen
bezieh. gespaltenen Hölzer werden, in einem Schlitten eingespannt, unter
gleichzeitiger Drehung in ihrer Längenrichtung unter den Fräsern hingeführt. Diese
sind mit ihrer gemeinschaftlichen Achse in einem um eine horizontale Achse
schwingendem Rahmen gelagert, dessen Hebung und Senkung entsprechend der Form der
Speichen durch ein diesen congruentes und in ganz gleicher Weise unter dem Rahmen
durchgeführtes Guſsmodell bewirkt wird. Die Maschine bedarf zur Fräsung von 4
mittelgroſsen Speichen nur 6 bis 7 Minuten, so daſs sich ihre tägliche Leistung
unter Berücksichtigung der unvermeidlichen Arbeitspausen auf 250 bis 300 Stück
beläuft. (Vgl. Guilliet 1872 206 * 6 bez. J. Gilchrist 1861 161 * 87.)
Das Anschneiden der Zapfen an die Speichen geschieht auf
der in Fig. 1 und 2 Taf. 33
abgebildeten Fräsmaschine. Zunächst werden die in die
Nabe einzupassenden Zapfen ausgebildet, indem die Speichen in den Support A eingespannt und mit ihren Innenenden an der senkrecht
gelagerten Frässcheibe B vorübergeführt werden. Mit
derselben Frässcheibe werden aber auch die äuſseren Enden der Speichen, nachdem
letztere in die Nabe eingefügt sind, bearbeitet. Zu diesem Zwecke wird die Nabe auf
die Spindel C aufgesetzt und nach und nach jede Speiche
der Frässcheibe B dargeboten. Auf diese Weise erhalten
die Speichen eine genau gleiche Länge. Ober- und Untermesser des Fräskopfes B sind entsprechend der gewünschten Stärke der Zapfen
achsial verschiebbar.
Zum Zurichten der Felgen dient gleichfalls eine
besondere Maschine, welche in Fig. 3 und
4 Taf. 33 dargestellt ist. Zum Bearbeiten der Seitenflächen wird das
Felgenstück A in den pendelnden Rahmen B eingespannt und mit diesem zwischen den beiden sich
entgegengesetzt drehenden Parallelfräsen C
durchgeführt. Die Dicke der Felgen ist demnach abhängig vom Abstande der Fräsköpfe
C und von ihren Durchmessern. Auf welche Weise
jedoch die Maschine den verschiedenen Felgenstärken angepaſst wird, ist nicht
mitgetheilt. Behufs des Fräsens der gekrümmten Flächen der Felge A wird dieselbe auf einer Schablone S (Fig. 12
Taf. 33) von entsprechender Krümmung aufgespannt und mit deren Hilfe an einem der
beiden Fräsköpfe C derart vorbeigeführt, daſs der
Schnitt stets mit der Faser erfolgt und ein Ausreiſsen des Holzes nicht eintreten
kann. Zum Betriebe der Maschine sind etwa 2e
nöthig. (Vgl. Guilliet 1872 206 6.)
Die nächste Arbeit besteht in dem Einstemmen der
Speichenzapfenlöcher in die Felge, welches auf der in Fig. 5 und
6 Taf. 33 dargestellten Maschine geschieht. Die Felge A wird auf einem Supporte B fest eingespannt
und von der Auſsenseite her durch den von der Maschine angetriebenen und von Hand
mittels des Hebels E vorgeschobenen Bohrapparat C das Zapfenloch vorgebohrt, worauf das genaue
Ausstemmen desselben von der inneren Seite der Felge aus durch die Stemmvorrichtung
D bewirkt wird. Der Support ist mit solchen
zweckdienlichen Stellvorrichtungen versehen, welche es ermöglichen, allen
Zapfenlöchern die genau gleiche Form und Stellung zu ertheilen.
Für kleinere Werkstätten wird die Maschine in etwas veränderter Ausführung
hergestellt, so daſs dieselbe auch zum Stemmen der
Zapfenlöcher in den Radnaben verwendet werden kann, sofern der Durchmesser
der letzteren 300mm nicht überschreitet. Zu diesem
Zwecke bedarf es nur eines etwas veränderten Supportes.
Für einen ausgedehnteren Betrieb wird jedoch für das Einarbeiten der Zapfenlöcher in die Nabe eine besondere Maschine gebaut,
welche in Fig. 10 und
11 Taf. 33 abgebildet ist. Die vorher abgedrehte Radnabe N wird zwischen 2 Docken auf dem Supporte A drehbar gelagert. Mittels des Klinkenhebels B kann dieselbe nach Fertigstellung eines Zapfenloches
genau um die erforderliche Theilung gedreht und in der neuen Lage festgestellt
werden. Jedes Zapfenloch wird zunächst mittels der wagerecht angeordneten, von Hand
anstellbaren Bohrvorrichtung C vorgebohrt und, nachdem
dasselbe bei wiederholter Schaltung der Nabe in die höchste Stellung gelangt ist,
durch die vertikale Stemmmaschine fertig ausgestemmt. Das allmähliche Vorschieben
des Stemmeisens D wird durch die mittels des Handhebels
E verstellbare Tasche J und eine Verschiebung des Supportes in der Längenrichtung durch das
Handrad E bewirkt. Die mittels des Rades G bethätigte Schraube F
erlaubt, dem Supporte mit der Nabe verschiedene geringe Neigungen zu ertheilen,
entsprechend der Schrägstellung der Zapfenlöcher, c ist
die Antriebsriemenscheibe für die Bohrvorrichtung C
deren Spindel mit Nuth und Feder in der hohlen Nabe von c geführt wird, d ist das Riemenscheibenpaar
für die Stemmmaschine, bei welcher ein gleichmäſsigerer Gang durch das Schwungrad
e erzielt wird. (Vgl. Goſs 1878 229 * 514.)
Nachdem die einzelnen Bestandtheile der Räder in beschriebener Weise hergestellt
sind, kann das Zusammensetzen erfolgen. Die für diese
Arbeit bestimmte Maschine besteht aus einer kräftigen Guſseisenplatte (Fig.
9 Taf. 33), welche in der Mitte einen Dorn zur Aufnahme der Nabe besitzt,
während an dem Umfange sieben nach dem Mittelpunkte gerichtete hydraulische
Preſscylinder in gleichen Abständen angebracht sind. Zunächst wird eine Speiche nach
der anderen in die auf dem Dorne durch eine Mutter festgehaltene Nabe gesteckt und
mit Hilfe eines Preſscylinders fest hineingedrückt. Die ganze Arbeit dauert etwa 5
bis 8 Minuten. Schlieſslich werden die Felgen auf die Speichenzapfen aufgebracht und
das ganze Rad 5 Minuten lang dem gleichzeitigen Drucke aller 7 Preſscylinder
ausgesetzt. Auf das derart stark zusammengedrückte Rad kann alsdann der Reifen
aufgelegt werden, wobei derselbe einer nur geringen Erwärmung bedarf, um doch
genügend fest zu sitzen (Tel Colas 1869 194 * 24.)
Die beschriebenen Arbeitsmethoden gewähren zwar eine recht groſse Genauigkeit;
dennoch ist eine geringe Excentricität der Nabe gegen den Kranz der Natur des Holzes
gemäſs nicht ganz ausgeschlossen. Um ein völlig genaues Rundlaufen des Rades zu
erreichen, wird daher das Ausbohren der Nabe und das
Einsetzen der Badbüchse ganz zuletzt auf einer besonderen Maschine (Fig.
7 und 8 Taf. 33)
vorgenommen. Zu dem Ende wird das Rad, nachdem sowohl der Reifen, als auch die
Nabenringe aufgezogen sind, auf die wagerechte Platte A
aufgelegt und durch drei sich gleichmäſsig gegen den Mittelpunkt bewegende Backen
E festgehalten und gleichzeitig genau centrirt, so
daſs sich der Mittelpunkt des Rades genau über dem der Scheibe befindet. Hierauf
wird der Ausleger einer Krahnbohrmaschine über das Rad gedreht, bis die Bohrspindel
genau conachsial zur Achse des Rades steht, und in dieser Stellung durch eine Klinke
festgehalten. Nachdem die Nabe ausgebohrt ist, wird die Bohrmaschine wieder bei
Seite gedreht und mittels einer unter der Platte A
befindlichen hydraulischen Presse D die Achsbüchse c in die Nabe C
hineingezogen.
Tafeln
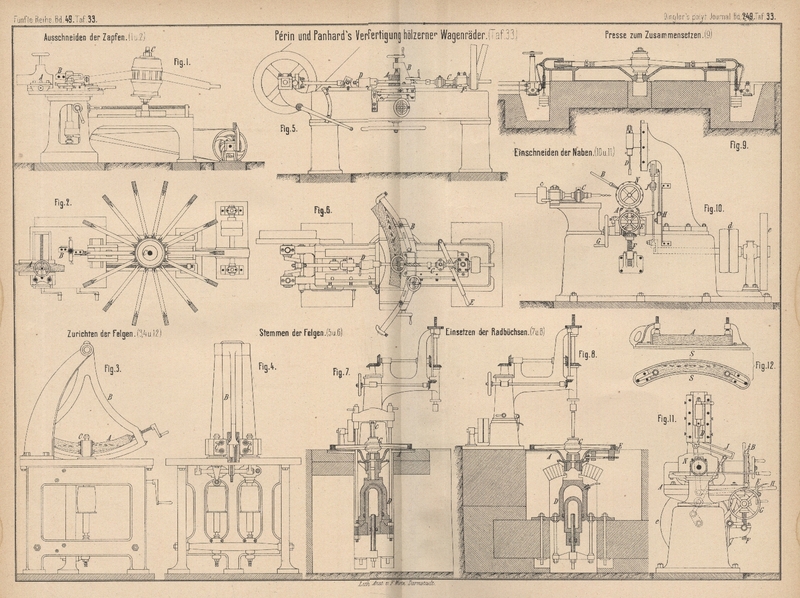