Titel: | Ueber Neuerungen in der Giesserei. |
Fundstelle: | Band 255, Jahrgang 1885, S. 318 |
Download: | XML |
Ueber Neuerungen in der Gieſserei.
(Patentklasse 31. Fortsetzung des Berichtes Bd.
253 S. 363.)
Mit Abbildungen auf Tafel
23.
Ueber Neuerungen in der Gieſserei.
Ernst Körting in Hannover (* D. R. P. Nr. 29840 vom 25.
Juni 1884) hat ein Formverfahren angegeben, welches für
die Herstellung von Säulen, Trägern, Röhren, überhaupt von solchen Gegenständen,
welche bei groſser Längenausdehnung eine nahezu gleichbleibende Querschnittsform besitzen, von
Wichtigkeit erscheint. Das Verfahren besteht darin, daſs der Formsand, welcher bis
jetzt meistens durch Stampfen gegen das Modell gedrückt wird, durch zwei nach
einander zu benutzende Walzen gegen das Modell gepreſst wird. Die zuerst arbeitende
Walze hat die Form eines Rotationskörpers, dessen Erzeugende sich dem abzuformenden
Gegenstande möglichst anschlieſst, jedoch unter Beibehaltung eines stets
gleichbleibenden Zwischenraumes zwischen Modell und Walze, der beim Formen durch den
gesiebten Formsand ausgefüllt wird. Die zweite Walze ist eine gewöhnliche
Flachwalze. Beim Formen wird das Modell wie gewöhnlich mit gesiebtem Sande bedeckt,
dann der Kasten bis zu einer gewissen, für das gleiche Modell immer gleichen Höhe
mit Sand voll geschaufelt und nun die erste Walze eingelegt und einige Mal hin und
her gerollt. Vermöge ihres Profiles drückt die Walze den Sand allmählich in einer
gleichdicken Schicht um das Modell herum an und zwar bei wiederholtem Abformen des
gleichen Modelles auch immer mit der gleichen Kraft, was bei Massenfabrikation, um
Ausschuſs zu vermeiden, besonders zu beachten ist. Ein weiterer Vortheil, welchen
die Anwendung der Profilwalze gegenüber dem Stampfen noch hat, ist der, daſs es dem
Former unmöglich gemacht wird, auch beim nachläſsigsten Arbeiten das Modell zu
beschädigen, da die Walze dasselbe nicht berühren kann. Nachdem durch die Profil
walze der Sand in gleichmäſsiger Stärke um das Modell herumgepreſst ist, wird Sand
in den Kasten nachgefüllt und nun gewöhnlich gleich so hoch im Kasten angehäuft,
daſs der Sand im festgewalzten Zustande denselben mehr als ausfüllt. Die Profilwalze
wird dann mit einer genügend schweren Flachwalze vertauscht, der Sand flach
abgewalzt und die über den Kasten noch vorspringende Sandmasse abgestrichen, so daſs
der Kasten fertig ist.
Erfahrungsmäſsig walzen bei günstigen Modellen 2 Mann so viele Kasten ohne
Anstrengung fertig, wie 6 geübte Former mit Aufbietung aller Kräfte aufstampfen
können, und während das Stampfen geübte zuverlässige Handwerker erfordert, kann die
Walze von gewöhnlichen Tagelöhnern bedient werden. Die Firma Gebrüder Körting benutzt dieses Verfahren seit Mitte vorigen Jahres zum
Formen ihrer Rippenheizkörper. Dieselben lassen an
Sauberkeit und Genauigkeit der Ausführung nichts zu wünschen übrig. Die Arbeit zum
Kerneinlegen und Fertigstellen der Kasten zum Gusse liefert jeder Arbeiter an
Rippenheizkörpern (Röhren und Heizelementen) – nach gef. Mittheilung der Fabrik –
etwa 500k im Tage von 10 Arbeitsstunden mit
ungefähr 10 Proc. Ausschuſs, trotzdem sämmtliche Formen naſs gegossen werden.
Nach der Patentschrift hat der zur Ausführung des Verfahrens construirte Apparat die
in Fig. 1 und
2 Taf. 23
dargestellte Einrichtung: Auf dem Tische T ruht das
halbe Modell A des Muffenrohres, umgeben vom Formkasten
B. Parallel mit den Seitenwänden des Kastens liegen
die Schienen s, welche an dem einen Ende um einen
festen Zapfen drehbar und auf ihrer Oberfläche mit Zähnen versehen sind. Zwischen
diesen Schienen ruht auf einer Achse a die Profilwalze
C, welche also durch die Kurbel k mittels der in die Zahnstangen eingreifenden
Zahnräder r gleichmäſsig über das Modell hinweg gerollt
werden kann. Da nun die Schienen s an ihren freien
Enden nicht unterstützt sind, so ist klar, daſs die Walze C mit ihrem ganzen Gewichte auf den über dem Modelle im Formkasten
befindlichen Sand preſst und denselben gleichmäſsig zusammendrückt. Da aber die
Walze immer nur auf einen kleinen Theil der Sandoberfläche wirkt, so wird die
Pressung groſs genug sein, um feste Formen zu erhalten.
M. R. Moore in Indianapolis, Nordamerika (Englisches
Patent, 1884 Nr. 10436) bringt eine Formmaschine in
Vorschlag, bei welcher, wie in Fig. 3 Taf. 23 angedeutet
ist, der Druckkopf J zum Feststampfen des Formsandes
aus einer gröſseren Zahl von verschiebbaren Stempeln besteht, die auf eigentümliche
Weise der verschiedenen Begrenzung der Modelle entsprechend der Höhe nach so
eingestellt werden, daſs die Druckplatte unter sich überall gleich hohe
Sandschichtdicke vorfindet. Die Druckstempel J werden
von einem Ringe r zusammen gehalten; an r ist ein Rahmen r1 befestigt, welcher unten durch eine elastische
Haut G o. dgl. und oben durch den Kolben K luftdicht abgeschlossen ist. Zwischen Kolben K und Haut G wird durch
den Hahn g Preſsluft o. dgl. eingelassen und dann der
Kolben K durch einen Kurbelmechanismus H in Gang gesetzt, so daſs der ganze Druckkopf J auf und ab bewegt wird und dabei auf den Formsand
einwirkt, welcher auf die Modelle C in möglichst
gleichförmiger Schicht aufgetragen ist und somit gleichmäſsig zusammengedrückt
wird.
Zum Formen von Maschinentheilen verschiedener Höhe, besonders
Riemenscheiben u. dgl. (vgl. auch Hertzog 1884 252 * 454),
schlägt Jul. Wurmbach in Bockenheim-Frankfurt a. M. (*
D. R. P. Nr. 29457 vom 2. Mai 1884) die in Fig. 4 bis 6 Taf. 23 veranschaulichte
Einrichtung vor. In dem Formtische a ruht ein Einsatz,
welcher aus auf dem vierarmigen Kreuze k befestigten
concentrischen Ringen b besteht. Zwischen den Armen
dieses Kreuzes k kann ein gegen ersteres versetztes
vierarmiges Kreuz d mittels der Schraube f auf und ab bewegt werden. In die Zwischenräume r der concentrischen Ringe b wird das Modell des Riemenscheibenkranzes eingesetzt und dasselbe durch
Heben oder Senken des Armkreuzes d mehr oder weniger
hoch über die Oberfläche des Einsatzes b eingestellt.
Hiernach richtet sich auch die Breite des fertigen Riemenscheibenkranzes. Hat man
von diesen Einsätzen 2 Stück, bei denen die Zwischenräume des einen den
concentrischen Ringen des anderen entsprechen, so genügen diese zur Herstellung von
in sehr weiten Grenzen verschiedenen groſsen Riemenscheiben. Die Befestigung der
Kranzmodelle auf dem Armkreuze d geschieht mittels
Hilfe eines Bajonnetverschlusses, indem die wagerechten Rippen e der Arme d in am Modelle
angebrachte Unterschneidungen eingreifen.
Hat man nun das Kranzmodell in der richtigen Höhe eingestellt, so legt man auf den
Einsatz b um und in das Modell Blechplatten m und n und befestigt
diese auf b mittels Stifte. Diese Theile bilden also
auf diese Weise die Modellplatte, auf welcher der Sand festgestampft wird. Auf m wird dann das Modell der Nabe und der Speichen
befestigt und nun der Kasten aufgesetzt und festgestellt. Hat man denselben voll
Sand gestampft, so zieht man das Kranzmodell durch Drehen der Schraube f langsam nach unten hinaus und hebt den Kasten von dem
Einsatze ab.
Zum Zusammenhalten der Kastenhälften verwendet Wurmbach
statt der sonst üblichen festen Führungsstifte auf- und abschiebbare Riegel, welche
beim Aufsetzen der Kasten an Knaggen aufgehängt, nach dem Zusammensetzen der
Kastenhälften aber herabgezogen und mit ihrem oberen Hakenende unter die Knaggen
eingerückt und gegen Rückverschiebung gesichert werden.
Bei der Herstellung der Form für Riemenscheiben mit zwei Armreihen wird, wie Fig. 6 zeigt,
die innere Blechplatte m und ihre halbe Armreihe so
viel gehoben, als der halbe Abstand der beiden Armreihen betragen soll, und durch
den Untersatz t, welcher nebst der aufliegenden
Blechplatte m genau eingestellt ist, in dieser Lage
gehalten. Auf die äuſsere, auf dem Formtische liegen bleibende Platte n wird dann eine Formkastenhälfte aufgesetzt,
aufgestampft und dann abgehoben. Die zweite Formkastenhälfte wird in gleicher Weise
aufgestampft. In jeder Kastenhälfte verbleibt also eine der Höhe des Untersatzes i entsprechende Aussparung. Der Untersatz wird nun
entfernt, die Platte m unmittelbar auf den Tisch
gelegt, der Modellring c genau so hoch eingestellt, als
die Höhe des Untersatzes i beträgt, im Inneren auf
ganze Höhe voll
gestampft und dann der Sand genau auf Oberkante des Ringes abgestrichen. Durch
Hinunterziehen des Modellringes c erhält man dann einen
Sandcylinder, welcher genau in die Aussparung einer Formkastenhälfte paſst und so in
dieselbe eingesetzt wird, daſs die in der Kastenhälfte und dem Mittelstücke
geformten halben Armreihen sich genau decken. Ein solches Mittelstück muſs demnach
für jede Formkastenhälfte hergestellt werden.
Um diese Mittelstücke bequem handhaben zu können, wird ein zerlegbarer Sandträger in
dieselben eingestampft, welcher nach dem Gusse leicht aus einander genommen und
zwischen den Armreihen in Theilen hervorgeholt werden kann. Zu diesem Zwecke besteht
der Sand träger aus zwei mittels Keilbolzen zu verbindenden Ringhälften und einer
Anzahl einzelner Arme, welche in die schwalbenschwanzförmigen Nuthen an der
Auſsenseite des Ringes eingesetzt und durch Holzkeile festgehalten werden.
Die gebräuchlichsten Zahnräderformmaschinen zerfallen in zwei Hauptgruppen, in
freistehende versetzbare Maschinen und in Bockmaschinen.
Bei den freistehenden versetzbaren Maschinen liegt die Form unbeweglich im Fuſsboden,
am Formkasten kommt nur ein Obertheil zur Anwendung und die auf einem Dorne ruhende
Maschine wird nach dem Formen der Zähne fortgenommen. Diese Maschine ist für
kleinere Zahnräder sehr gut brauchbar; für groſse Raddurchmesser angewendet, ist sie
aber nicht fest genug, so daſs infolge dessen die Formen nicht mehr genau werden.
Dieses Maschinensystem hat ferner den Nachtheil, daſs beim Formen der Räder ein
Zeitverlust entsteht, weil man zur Herstellung des Obertheiles der Form erst ein
Lager bereiten muſs, welches dann wieder beseitigt wird.
Die Bockmaschinen stehen fest und erfordern vollständige Formkasten, welche bei Seite
gesetzt werden, sobald die Zähne geformt sind, um anderen Formen Platz zu machen.
Groſse und schwere Formen erfordern hier aber kostspielige Formmaschinen und die
Fortschaffung der ersteren bietet bedeutende Schwierigkeiten.
Diese Nachtheile beseitigen Briegleb, Hansen und Comp.
in Gotha (* D. R. P. Nr. 28591 vom 26. Februar 1884) dadurch, daſs sie die
Formkasten auf einer Grundmauer festlagern und die fortnehmbare Maschine mit ihrem
breiten Fuſse im Inneren des Formkastens stehend auf der Bodenplatte befestigen, so
daſs ein genaues Formen der Zähne selbst bei groſsen Rädern ermöglicht ist.
Die starke sternförmige Bodenplatte A (Fig. 7 und 8 Taf. 23) ist auf der
Grundmauer B fest verankert und trägt die
Formkastenuntertheile a, b und c, welch letztere die Mittelkasten d, e und
f aufnehmen. Die Räderformmaschine F ist in die Mitte des Formkastens hineingestellt und
mit dem breiten Fuſse C auf dem Kastentheile a durch übergreifende Flanschen unverrückbar befestigt.
Die Formkastenuntertheile a, b und c
werden fast immer liegen
bleiben können, während der Mittelkasten d nur
herausgenommen wird, wenn gröſsere Räder Von mehr als einer gewissen Zahnbreite
geformt werden. Ist mit Hilfe des Zahnmodelles das Rad vollständig geformt, so wird
die Maschine herausgehoben.
Herm. Leopold in Berlin (* D. R. P. Nr. 28032 vom 22.
Januar 1884) stellt die Theilfuge von Riemenscheiben,
welche in den Armen getheilt sind, auf die Weise her, daſs das Sprengen derselben
wesentlich erleichtert wird. Zu diesem Behufe ordnet man die Theilfuge a (Fig. 9 Taf. 23) concav an,
so daſs die beiden Hälften gewissermaſsen nur an Berührungslinien zusammenfallen.
Das Formen des Hohlraumes A wird durch Einlegen eines
Kernes ermöglicht; dieser Kern würde jedoch wegschwimmen, wenn er nicht eine
entsprechende Auflage erhielte. Diese Auflage wird nun durch Verbindung des Kernes
A mit den Nebenkernen h erzielt, welche letzteren gleichzeitig dazu dienen, die Schraubenlöcher
herzustellen, die zum Zusammenschrauben der beiden Guſshälften nach dem Sprengen
dienen. Ferner legt sich der Kern A noch an den
mittleren Kern B der Nabe bei c an. Hierdurch wird auſser einem genauen Auflager noch erreicht, daſs
auch das Material, mit welchem beide Scheibenhälften in der Nabe zusammenfallen,
geringeren Querschnitt erhält und in Folge dessen das Sprengen erleichtert.
Um möglichst wenig Modelle für guſseiserne Fensterrahmen
zu gebrauchen, stellen Potthoff und Flume in Louisenhütte bei Lünen a. d. Lippe (* D. R. P.
Nr. 28795 vom 10. April 1884) Modelle her, bei welchen der äuſsere Rahmen, der Bogen
und die Längssprossen fest mit einander verbunden sind, während die Quersprossen,
deren unterste den Wasserschenkel bildet, in der Richtung der Längssprossen
verschiebbar sind. Nach der bestimmten Höhe und Theilung des Rahmens werden die
Quersprossen durch Schrauben befestigt. Die überstehenden Enden werden in der
Sandform, nachdem das Modell daraus entfernt ist, mit Sand gefüllt.
Das Patent * Nr. 28454 vom 15. Januar 1884 von J. P.
Goulson und Adolf Spiel in Berlin betrifft
einen zerlegbaren Metallkern und eine zerlegbare Form zum Gieſsen von Geruchverschlüssen aus Blei. In Bezug auf die Form der einzelnen Theile
muſs auf die Patentschrift verwiesen werden.
Fr. Bankloh in Witten (D. R. P. Nr. 28267 und 28314 vom
30. December 1883) bestreicht die Guſsstahl-Formen,
nachdem das Modell herausgenommen ist, mit einer Masse aus 25 Proc.
Tiegelschalenmehl, 46,5 Proc. Chamottesteinmehl, 12,5 Proc. grünem Formsand, 12,5
Proc. gemahlenem weiſsem Thon und 3,5 Proc. Pottloh. Alsdann werden die Formen 5
Minuten lang getrocknet und dann mit einem Spatel polirt; hierauf erwärmt man die
Formen 12 Stunden lang in einem Wärmofen, reinigt dieselben von Staub und trägt eine
dünnere Streichmasse auf, welche besteht aus:
Chamotte
12,5
Proc.
Chamottesteinmehl
50
Kokesmehl
12,5
Gemahlener weiſser Thon
12,5
Gyps
6,25
Pottloh
6,25
C. M. Pielsticker in London und Friedr. C. G. Müller in Brandenburg (* D. R. P. Nr. 29548 vom 8. Februar
1884) lieſsen sich ein Verfahren und einen Apparat patentiren, um Draht, Stangen, Platten, Schienen u. dgl. unmittelbar
aus geschmolzenem Eisen beliebigen Kohlenstoffgehaltes
herzustellen.
A (Fig. 10 Taf. 23) ist ein
aus Stahlblech hergestellter, mit dem Deckel F
verschlieſsbarer Cylinder. Cylinder wie Deckel sind inwendig mit einem 200mm dicken Futter feuerfesten Materials D ausgekleidet. Der Deckel enthält ein Mannloch H; ebenso befindet sich nahe dem Boden des Cylinders
ein Mannloch K. Gegenüber K befindet sich in der Wand des Cylinders A,
sowie in seiner Auskleidung D eine runde Oeffnung,
welche in den guſseisernen Hohlcylinder B führt. In B paſst der cylindrische Hohlkörper c aus Guſseisen, welcher in seiner Achse die Röhre d enthält; letztere ist aus Stahl oder Bronze
hergestellt, inwendig polirt oder auch mit einem harten, nicht metallischen Stoff
ausgekleidet; ihr Profil ist gleich oder annähernd gleich demjenigen des zu
erzeugenden Gegenstandes.
Der die Röhre d umschlieſsende Hohlkörper c ist an seiner abgerundeten Stirnfläche cylindrisch
ausgedreht, um das Mundstück m aufzunehmen, welches aus
einem möglichst dichten und chemisch widerstandsfähigen feuerfesten Materiale
gebrannt ist und eine Durchbohrung besitzt. In den um die Röhre d innerhalb c
verbleibenden Hohlraum kann eine Kühlflüssigkeit eingeleitet werden. Bevor das
Kühlrohr c eingesetzt wird, wird es vorn mit breiiger
feuerfester Masse umgeben, wodurch nachher ein dichtes Zusammenschlieſsen mit der
Fütterung des Raumes A gesichert ist.
Der Betrieb des Apparates gestaltet sich, wie folgt: Zuerst steckt man durch die Form
d einen ihrem Querschnitte genau entsprechenden
Eisenstab, dessen Enden sowohl in den Raum A, als auch
nach auſsen hervorragen. Darauf wird der Raum A bei
geöffneten Mannlöchern durch Gas oder Kohle gehörig vorgewärmt. Nachdem dann das
Mannloch K geschlossen und Kühlflüssigkeit durch c geleitet ist, wird A mit
möglichst hitzigem Eisen oder Stahl durch die Oeffnung H vollgegossen. Kurze Zeit darauf wird der in der Form d steckende Eisenstab vorwärts gezogen, das in A enthaltene flüssige Metall folgt dem Stabe, erstarrt
innerhalb der Form d, bildet mit dem zuvor
abgeschmolzenen Stabe einen zusammenhängenden prismatischen Körper, welchen man
ununterbrochen aus der Form zieht, bis der Inhalt von A
erschöpft ist. Die Kraft, welche den eingeführten Stab und darauf den neu entstandenen
prismatischen Eisenkörper aus der Form zieht, geht von einem oder mehreren unter
passenden Winkeln aufgestellten Walzenpaaren aus, deren Kaliberöffnung in der
verlängerten Achse von d liegt. Die Geschwindigkeit der
Walzen wird so geregelt, daſs der Metallfaden hellroth glühend aus der Röhre d tritt. Scharfe Kanten darf letztere nicht haben;
diese müssen in dem Walzwerke hergestellt werden. Die Zugkraft braucht dagegen nicht
von den Walzen auszugehen. Man kann den Draht auch durch 2 Walzen in einem
entsprechenden Kaliber, welches den Drahtquerschnitt noch vermindert, hindurch ziehen.
Um Gasausscheidungen aus dem Metalle im Behälter A zu
verhindern, läſst man in den oberen Theil desselben flüssige Kohlensäure
eintreten.
Die Herstellung schwerer prismatischer Eisenkörper soll nach diesem Verfahren, so
lange es sich um einfache und volle Profile handelt, wegen des verhältniſsmäſsig
kleineren Reibungswiderstandes weniger Schwierigkeiten bieten als leichtere Stäbe.
Der Apparat bleibt dem zuvor beschriebenen, abgesehen von den Abmessungen,
gleich.
Der Sammelraum A kann, namentlich bei dichtem Stahl, zu
einem bloſsen Einguſstrichter zusammenschrumpfen, welcher durch eine gewöhnliche
Gieſspfanne stets voll gehalten wird. Die Form erhält zweckmäſsig eine Neigung,
damit etwaige Gasblasen aus dem noch flüssigen Metalle aufsteigen können.
Handelt es sich um die Herstellung prismatischer Körper verwickelten Profils, z.B.
Schienen, oder um hohle Körper, wie Röhren, so ist die Anwendung des Walzwerkes sehr
erschwert oder gänzlich ausgeschlossen. Das Fabrikat muſs also mit seinem
endgültigen Profile aus der Form kommen. Die bewegende Kraft kann in diesem Falle
durch Hebel, hydraulische Vorrichtungen oder irgend welche anderen Mechanismen
geliefert werden. Es ist hier eine absetzende Bewegung angezeigt, in der Art, daſs
man während einer Ruhepause den ganzen Inhalt der Form erstarren läſst, dann den
gebildeten prismatischen Körper nahezu um die Länge der Form schnell vorzieht,
wodurch sich in letztere wieder flüssiges Metall ergieſst, um nach der nächsten
Pause als starrer Körper hervorgezogen zu werden.
Um Hohlkörper zu erzielen, muſs die Form d einen
gekühlten Kern erhalten. Derselbe besteht aus einer vorn geschlossenen Stahlröhre,
welche im Bodengemäuer des Sammelraumes A so
eingebettet ist, daſs ihr vorderes Ende conachsial in der Form d steht. Das hintere offene Ende geht durch die
gegenüber liegende Wand von A. Durch ein dünnes, bis
vorn hinein zu führendes Rohr kann der Kern mit Kühlflüssigkeit versehen werden. Die
Einfluſsmündung des Mundstückes liegt dann schräg nach oben. Da in den zuletzt
berührten Fällen der Körper lediglich durch einen Gieſsprozeſs fertig gestellt wird,
so muſs das verwendete Metall dichte Güsse liefern, andererseits aber im gegossenen
Zustande die Festigkeit und Zähigkeit besitzen, welche man zu Bauzwecken verlangt. Ein solches
Metall wollen Pielsticker und Müller in dem mit Silicium-Spiegeleisen hergestellten Fluſsstahl mit 0,3
bis 0,4 Proc. Kohlenstoff gefunden und durch zahlreiche Versuche dargethan haben,
daſs dieser Stahl in gegossenem Zustande fast die nämlichen Gütezahlen gibt, wie
nach dem Schmieden oder Walzen, namentlich auch hinsichtlich der Contraction.
Statt des zusammengesetzten Kühlrohres c kann bei der
Erzeugung von Draht u. dgl. einfach ein voller Stahlblock mit achsialer Durchbohrung
oder eine mit Guſseisen umgossene Stahlröhre in Anwendung kommen, wobei dann die
Wärme des einflieſsenden Eisens von der schweren Metallmasse aufgenommen wird.
Innerhalb der Metallmasse können sich auſserdem noch Kanäle befinden, durch welche
Kühlwasser flieſst.
Statt des Sammelgefäſses A, in welches das flüssige
Metall übergeführt wird, kann auch irgend ein geeigneter Ofen (z.B. ein Siemens'scher Ofen) benutzt werden, worin das Metall
durch die Wärme einer Feuerung beliebig lange in geschmolzenem Zustande erhalten
werden kann. Der Ofen kann auch zur Bereitung des Metalles gedient haben. An Stelle
der gewöhnlichen Abstichöffnung wird das Kühlrohr c
eingesetzt und im Uebrigen verfahren, wie oben beschrieben.
Zur Herstellung von schmiedbarem Guſs schlägt Friedr. E. Paul in Radebeul (* D. R. P. Nr. 27981 vom
30. December 1883) einen sich drehenden Cylinder vor, welcher in dem Flammraume
eines Ofens mit 2 Feuerungen gelagert ist und dem durch die beiden hohlen
Lagerzapfen Luft zu- bezieh. abgeführt wird. Zur gleichmäſsigen Vertheilung der Luft
im Cylinder sind innerhalb desselben an beiden Enden Siebe angeordnet; zwischen
diese werden die zu entkohlenden Gegenstände eingepackt.
Tafeln
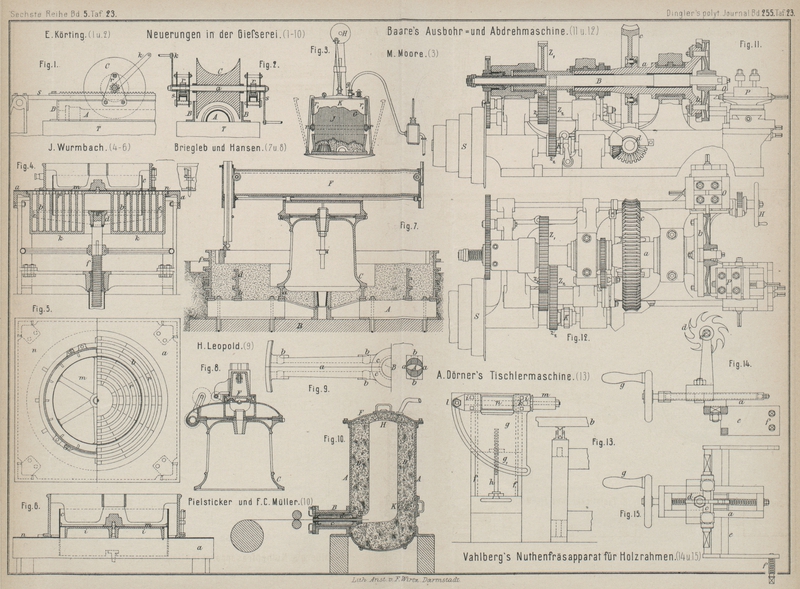