Titel: | Ueber Neuerungen in der Giesserei. |
Fundstelle: | Band 259, Jahrgang 1886, S. 300 |
Download: | XML |
Ueber Neuerungen in der Gieſserei.
(Patentklasse 31. Fortsetzung des Berichtes Bd.
257 S. 7.)
Mit Abbildungen im Texte und auf Tafel 20 ff.
Ueber Neuerungen in der Gieſserei.
Th. Nordenfelt in London und C.
G. Wittenström in Motala, Schweden (* D. R. P. Nr. 32959 vom 14. Oktober
1884) haben eine mit Deckel versehene Gieſspfanne
angegeben, bei deren Gebrauch (für Eisen, Stahl u. dgl.) eine Oxydation der
Metalloberfläche vermieden werden soll. Wie aus Fig. 8 und 9 Taf. 20 zu entnehmen
ist, besteht die Gieſspfanne aus einem Topfe a mit
Deckel b aus Eisenblech, welche innen ein feuerfestes
Futter besitzen. Diese beiden Theile sind durch Gelenke mit einander verbunden, so
daſs b nach hinten umgeklappt werden kann. An der
gegenüber liegenden Seite sind Topf und Deckel mit halbkreisförmigen Ausschnitten
versehen, welche zusammen den Gieſsmund k bilden. Der
Topf a hängt mittels Zapfen l in einem Rahmen mn, so daſs sich an der
entgegengesetzten Seite angeordnete Lappen auf die Schiene p stützen und den Topf in aufrechter Stellung erhalten. In dem Rahmen mn ist auf einer Achse lose der Aufhängebügel r drehbar und steckt dazwischen fest auf derselben
Achse die Kettentrommel t, welche mit Schneckenrad u und Schraube v umgedreht
wird. Die Kette der Trommel t ist an dem Boden der
Pfanne a befestigt. Man kann also a leicht und mit groſser Genauigkeit in jede Lage
bringen und dadurch den Ausguſs des Metalles beliebig regeln. In dem Deckel b ist ein Gasbrenner f
angeordnet, dem durch die Stutzen g und h Gas bezieh. Luft zugeführt wird. An diese Stutzen
werden die Schläuche angeschlossen, die zur Gasleitung bezieh. zum Gebläse führen.
Eine in dem Brenner f angebrachte Siebplatte befördert
die innige Mischung von Gas und Luft; das Gemenge wird in der Pfanne entzündet. Die
Verbrennungsgase treten durch das Mundstück k aus. Die
Flamme kann sowohl zum Vorwärmen der Pfanne, als zum Warmhalten des Metalles und
damit zur Verhinderung der Oxydation desselben dienen.
Zur Herstellung von cylindrischen oder kegelförmigen Hohlkörpern durch Centrifugalguſs (vgl. 1884
252 437) hat Jos.
Whitley in Leeds (* D. R. P. Nr. 32883 vom 7. December 1884) den in Fig. 10 Taf.
20 veranschaulichten
Apparat angegeben: ein Hohlkegel A, welcher auf das
Ende einer entsprechend gelagerten Hohlwelle J
befestigt und am äuſseren etwas weiteren Rande durch Rollen E unterstützt ist. In den Mantel A ist ein
zweiter mehrtheiliger Cylinder B eingesetzt und durch
Rippen in A genau eingepaſst. Das Innere von B ist vollkommen cylindrisch und wird mit Lehm
bekleidet, um das Anbacken des Guſsstückes zu verhindern. Die Theile A und B sind zum
Durchlassen der Gase mit zahlreichen Oeffnungen versehen. Das vordere Ende des
Mantels A ist durch eine innen ebenfalls mit Lehm
bekleidete Platte F geschlossen, welche die Länge des
Guſsstückes bestimmt und in der Mitte nur eine so groſse Oeffnung besitzt, um die
Guſsrinne L in das Innere einführen zu können. Ist der
Guſs bei schneller Drehung der ganzen Form vollzogen, so schraubt man nach
Entfernung der Platte F durch Drehen eines Handrades
die in der Hohlwelle J liegende Achse, an welcher die
Scheibe G befestigt ist, vor und schiebt dadurch das
Guſsstück mit dem Cylinder B aus dem Mantel A heraus, was vermöge der Kegelform von A leicht zu bewirken ist. Der mehrtheilige Cylinder B läſst sich nun leicht vom Guſsstücke abnehmen.
Jul. Möller in Würzburg (D. R. P. Nr. 32581 vom 27.
Januar 1885) schlägt zur Herstellung von
Fluſseisen-Guſsstücken eine Formmasse vor,
welche aus einer Mischung von 24 bis 30l scharf
gebrannten pulverisirten, vollkommen reinen, feuerfesten Thon mit 100cc Zucker, 2l
Wasser und 1/7l Paraffinöl besteht. Die Masse wird vor der
Verwendung mehrmals gesiebt, um eine gleichmäſsige Vertheilung der Feuchtigkeit zu
erlangen. Die Mischung muſs aber vollkommen frei von Kieselsäure, Kalk und Magnesia
sein, damit keine schmelzbaren Schlacken entstehen, welche an den Guſsstücken haften
bleiben; auſserdem darf die Mischung kein Holzkohlenpulver enthalten, weil dasselbe
an das Fluſseisen Kohlenstoff abgeben könnte und weil seine Asche Silikate enthält,
die eine Schlackenbildung befördern.
Die von Paul Zimmermann in Rathenow (* D. R. P. Nr.
33910 vom 19. Juni 1885) angegebene Kugelmühle zum
Zerkleinern von Formsand besteht, wie aus Fig. 7 Taf. 20
zu entnehmen ist, aus einem eisernen Cylinder H mit
Einfülltrichter J und Reinigungsthür K; oberhalb des Zylinders H ist die Antriebswelle gelagert, welche durch Kegelräder die senkrechte
Welle D im Inneren des Cylinders umdreht. Auf einem
Kreuze am Boden von H ist die Stahlplatte L befestigt, welche gleichmäſsig vertheilte, flache,
nach unten sich erweiternde, radiale Schlitze von 12 bis 15mm Länge und 1 bis 1mm,5 Breite hat. Dicht über dieser Stahlplatte bewegt sich, ohne einen
Druck auf L auszuüben, ein Doppelflügel B, ebenfalls aus Stahl, welcher an der Welle D befestigt ist. Die Flügel B sind gegen die Platte L im Winkel von 45°
geneigt und haben eine 40mm breite untere Fläche
und eine 12 bis 15mm breite obere Fläche. Zwischen
den Stahlflügeln liegen je zwei guſseiserne Kugeln, welche bei der Drehung der Welle
D auf der Platte L
herumgewälzt werden. Um ein Ueberspringen der Kugeln über die Flügel zu vermeiden,
sind auf der Welle Querstäbe G angebracht, welche die
Kugeln aufhalten und hierdurch einen gleichmäſsigen Gang herbeiführen.
Der zu mahlende und zu mischende Sand wird durch den Trichter J dem Cylinder H zugeführt; die Kugeln
zerreiben die Knollen und das so vorgearbeitete Mahlgut wird mittels der Stahlflügel
B und deren schräge Flächen durch die Schlitze der
Stahlplatte L hindurchgedrückt, wobei ein nochmaliges
Zerreiben des Sandes stattfindet. Steine oder andere harte Körper werden nicht
zerstört, sondern nur auf L herumgeschleudert und
können durch die Thür K entfernt werden.
Gust. Louis Robert in Stenay, Frankreich (* D. R. P. Nr.
32939 vom 1. März 1885) wärmt die Sand- oder Lehmformen
dadurch an, daſs er in den Gieſstrichter der
zusammengesetzten Form ein Gasgebläse mit Gas- und
Luftzuführung einsetzt und nun die Flamme durch die Form hindurch treibt, so daſs
die Verbrennungsproducte aus den Luftkanälen der Form heraustreten. Man thut gut,
eine stark ruſsende Flamme zu erzeugen, um das Innere der Form zu schwärzen, was
eine Entfernung des Formsandes vom fertigen Guſsstücke erleichtert.
Nordenfelt und Wittenström
(* D. R. P. Nr. 32243 vom 14. Oktober 1884) stellen die Formen für kleinere Gegenstände, welche in groſsen Massen erzeugt werden,
aus Eisen her, so daſs beide Formhälften durch
Gelenkbänder mit einander verbunden sind und aus einander geklappt werden können.
Die Wände der Formhälften sind hohl und wird durch die Gelenkzapfen Dampf oder
Wasser in die Hohlräume ein- und ausgeleitet. Die Vorwärmung mittels Dampf bis auf
80 bis 100° geschieht vor dem Gusse, während die
Abkühlung durch Wasser während des Gusses geschehen
soll. Das Innere der Form wird durch Verbrennen von Naphta oder Steinkohlentheer
geschwärzt.
Die Formen werden aus grauem Guſseisen hergestellt, wenn sie zur Erzeugung gröberer
und einfacherer Gegenstände dienen. Für feinere Güsse mit dünnen vorspringenden
Ecken werden die Formen aus weichem Stahl gegossen, auf welchen die besonders zarten
Theile durch Schrauben befestigt werden. Eine sorgfältige Reinigung der Formflächen
von Rost ist unumgänglich nothwendig. Es hat sich ferner gezeigt, daſs derartige
Formen beim Vergieſsen Mangan armen Eisens und Stahles mehrere Tausend Güsse
aushalten, ohne schadhaft zu werden. Enthält dagegen das Eisen viel Mangan, so muſs
man den Einguſs, welcher besonders der Zerstörung unterworfen ist, durch eine
Schicht von Graphit schützen. Die Decken zur Bildung der Hohlräume zum Einleiten des
Dampfes und des Wassers bestehen aus schmiedeisernen Platten, welche auf die
äuſseren Flächen der eigentlichen guſseisernen Formhälften aufgeschraubt werden.
Beim Gieſsen von Eisenbahn-Wagenrädern aus Guſsstahl
wendet man gewöhnlich
Formen aus feuerfestem Thone an, welche scharf getrocknet werden und dann eine
solche Festigkeit besitzen, daſs sie beim Schwinden des Stahles von letzterem
zerdrückt werden. Geben die Formen dem Schwinden nicht nach, so verwirft sich das
Rad. Derartige Formen halten natürlich nur einen Guſs aus, sind in Folge dessen
theuer und ist ihre Verwendung sehr umständlich.
Will Sellers in Philadelphia (* D. R. P. Nr. 33887 vom
9. Juni 1885) schlägt deshalb eiserne Formen vor, deren
Wände nach dem Gusse ein ungehindertes Schwinden des
Metalles gestatten. In den beigegebenen Textfig.
1 und 2 ist das Rad mit ausgebohrter Nabe
und abgedreht in die Form eingelegt gezeichnet, um den für das Schwinden benöthigten
Zwischenraum zu zeigen. Der leere Raum über dem fertigen Rade zeigt die Menge
einzugieſsenden Metalles an, welche als verlorener Kopf dazu dient, den Radkranz vor
Höhlungen in Folge des Schwindens zu bewahren. Die Notwendigkeit eines verlorenen
Kopfes folgt daraus, daſs der Körper zwischen Kranz und Nabe in Folge seiner Dünne
eher als der Kranz zum Erstarren kommt.
Fig. 1., Bd. 259, S. 303Fig. 2., Bd. 259, S. 303 Die eigentliche Form besteht aus 5 Haupttheilen: dem Kasten A, dem oberen Nabenstücke F, dem unteren Nabenstücke G, dem oberen und
unteren beweglichen Ringstücke J und K. Der Kasten A sitzt auf
dem unteren Rahmen B und trägt seinerseits den oberen
Rahmen C. Diese 3 Theile werden in ihrer Lage zu
einander durch die Flanschen a am Kasten A gehalten und durch vier umlegbare Bügel zusammen
geschlossen; die Bügel sind durch Drehbolzen an dem unteren Rahmen B befestigt und werden über am oberen Rahmen
angegossene Vorsprünge geschoben, so daſs alsdann der Kasten A fest zwischen den beiden Rahmen eingeklemmt ist. Die Vorsprünge dienen
auch als Handhaben beim Auseinandernehmen der Form behufs Herausnahme des gegossenen
Rades. Im oberen Rahmen C ist ein Kranz E befestigt, welcher zur Aufnahme des oberen
Nabenstückes F der Form dient und so weit ist, daſs
dieses sich mit seitlichem Spiel darin bewegen kann. Dasselbe ist mittels der
Ringplatte b und der Schrauben d am Kranze E befestigt. Das untere
Nabenstück G der Form sitzt ebenfalls mit seitlichem
Spiel auf dem oberen Rande eines ähnlichen Kranzes H im
unteren Rahmen B. Die Nabenstücke Fund G tragen am unteren und oberen Rande Flanschen.
Dieselben sind abgeschrägt und bilden die Auflager für die Ringstücke J und K der Form, welche
beim Schlieſsen den Zwischenraum zwischen den Nabenstücken und dem Kasten A ausfüllen. Der obere Ring J wird an vier Stellen von dem oberen Rahmen C getragen und zwar so, daſs er mittels je zweier Bügel c auf die Daumenscheiben zweier im Rahmen C gelagerter Achsen L
gehängt ist. Je nach der Drehung der letzteren wird also der Ring gesenkt oder
gehoben. Damit beide Achsen gleichzeitig in Drehung versetzt werden, ist auf die
eine ein Kurbelarm f, auf die andere ein Handhebel
aufgekeilt und sind diese beiden Theile unter einander durch die Stange g verbunden. Die Bügel c
sitzen an Blöcken Af, deren Arme durch Schlitze im Rahmen C nach auſsen treten.
Das untere Ringstück K der Form wird
vom unteren Rahmen B ebenfalls an vier den
Aufhängepunkten des oberen Ringstückes J entsprechenden
Stellen mittels der um feste Bolzen am Rahmen B
drehbaren Hebel N getragen. Das eine Ende jedes Hebels
N liegt in einem Schlitze eines für diesen Zweck
auf der unteren Seite des Rahmens angegossenen Vorsprunges, während an dem anderen
Ende ein Bügel drehbar befestigt ist, welcher über den vorstehenden Arm des Blockes
M geschoben wird, so daſs beide gleichzeitig gegen
und aus einander bewegt werden können. Die beiden Ringstücke J und K sind mit Flanschen h versehen, welche das obere Nabenstück F und den Kasten A
übergreifen und den genauen Schluſs der Form herbeiführen.
Innerhalb des unteren Nabenstückes G
der Form wird ein Metallblock von solcher Gröſse eingesetzt, daſs er die Wärme des
Gusses schnell genug ableitet und dieser erkaltet, ehe er noch Zeit gewinnt, die
Form zu erweichen, oder gar zu durchdringen. Die senkrechte Lage dieses Blockes
bestimmt die Länge der unteren Radnabe. Das obere Nabenstück F der Form ist so lang zu machen, daſs auſser der verlangten Länge der
Radnabe noch ein entsprechend groſser Kopf hergestellt werden kann.
Die Zusammenstellung der Form erfolgt in der Weise, daſs man den
Kasten A zwischen die beiden Rahmen B und C mittels der Bügel
einspannt und die an den äuſseren Enden der Hebel N
befestigten Bügel über die Arme der Blöcke M schiebt,
worauf man durch entsprechendes Drehen der Achsen L die
Formringstücke J und K auf
die Formnabenstücke F und G und den Kasten A aufsetzt. Nun wärmt man
die geschlossene Form leicht an, um ein zu schnelles Heiſswerden derselben durch das
einflieſsende Metall zu verhüten; letzteres wird dann rasch durch F eingegossen. Die Fugen zwischen den Ringstücken und
den übrigen Theilen werden gewöhnlich nicht so dicht sein, daſs sie das Entweichen
der in der Form eingeschlossenen Luft verhindern; um jedoch den Austritt dieser Luft
für alle Fälle zu ermöglichen, kann man in den betreffenden Theilen einige kleine
Oeffnungen vorsehen.
Ist der Guſs ausgeführt, so läſst man die Form ungefähr 1 bis 1½
Minute stehen, d.h. so lange, bis sich der Guſs mit einer Haut bedeckt hat, worauf
man die Achsen L zurückdreht, d.h. die Ringstücke vom
Gusse abhebt, damit das Schwinden sich ungehindert vollziehen kann. Nach dem
Zurückziehen der Ringstücke bleibt der Guſs von dem unteren Nabenstücke und der
Flansche des Kastens A gestützt, so daſs er sich durch
sein Gewicht nicht verwerfen kann. Die Zeitdauer, während welcher die Formringstücke
auf dem Gusse zu belassen sind, ändert sich etwas mit der Gröſse des Rades; es ist
indeſs nur erforderlich, mit dem Abheben so lange zu warten, bis sich auf dem Gusse
eine so starke Haut gebildet hat, daſs das im Inneren befindliche flüssige Metall
dieselbe nach dem Entfernen, der Ringstücke nicht mehr sprengen kann. Dagegen ist es
nothwendig, daſs sie vom Gusse zurückgezogen werden, bevor sie noch dem Schwinden
desselben einen fühlbaren Widerstand entgegensetzen können. Sobald das Metall so
weit erkaltet ist, daſs man das Herausnehmen des Gusses ohne Gefahr von Verwerfungen
ausführen kann, schlägt man die Bügel herunter, hebt den oberen Formrahmen mit den
daran befestigten Theilen der Form ab und nimmt den Guſs an der Nabe heraus. Die
Form kann alsdann sogleich wieder zusammen gestellt, geschlossen und für einen neuen
Guſs benutzt werden. Das aus der Form genommene Rad bringt man sofort in den
Kühlofen; nach dem Kühlen schneidet man die Angüsse an Kranz und Nabe weg, bohrt
letztere aus und dreht das Rad ab.
Fig. 3., Bd. 259, S. 305 Beim Gusse von Röhren und Cylindern benutzt
J. Chambers in Stanton, England (* D. R. P. Nr.
33327 vom 18. April 1885) zusammenklappbare Kerne,
welche nach dem Gusse von der Innenwandung abbewegt und dann aus der Röhre
herausgezogen werden. Jeder Kern besteht nach Textfigur
3 aus 4 Theilen, die zusammen eine glatte cylindrische Mantelfläche
bilden. Die Theile a und a1 sind mit a2 in der gezeichneten Art verfalzt und
durch Querbolzen c verbunden. Zwischen a und a1 liegt eine Keilleiste b, welche mittels Fig. 3. der Glieder d an den Bolzen c drehbar
befestigt ist. Stellt man die Glieder d senkrecht zur
Mittellinie des Kernes, so nimmt b die gezeichnete
Stellung ein, d.h. seine dünne Seite vergleicht sich mit der Mantel-flache von a und a1. Die 4 Kerntheile bilden dann ein fest
zusammenhängendes Ganze und werden als solches in die Form eingesetzt. Ist der Guſs
fertig, so schlägt man auf das eine Ende der Keilleiste b, so daſs die Glieder d eine schräge
Stellung zur Mittellinie des Kernes einnehmen. Man kann dann a und a1
gegen einander bewegen, a2 herausnehmen, dann a und a1 zusammenklappen und
alle Theile aus dem Rohre entfernen.
Ein von Herm. Winnesberg in Saarn a. d. Ruhr (* D. R. P.
Nr. 32380 vom 19. Februar 1885) angegebenes Verfahren bezweckt den Guſs von Rohrkrümmern mit gleichmäſsiger Wandstärke ohne
Anwendung von Kernstützen. Man verfertigt zu diesem Zwecke einen Kern,
dessen Dicke dem inneren Durchmesser der Rohre entspricht, als einen in sich geschlossenen Ring, so daſs der Halbmesser desselben dem
Krümmungshalbmesser des Rohrbogens entspricht. Die Seele dieses Kernes bildet man
aus einem Strohseile, über und unter welches sich behufs Verstärkung zwei leicht aus
einander zu nehmende oder zu zerschlagende Eisenbänder legen. Auf diesen Kern
gruppirt man nun gleichmäſsig die getheilten Modelle der Rohrkrümmer, so daſs die
Flanschen derselben etwas von einander abstehen. In die Zwischenräume bringt man im
Kerne bis auf das Strohseil reichende Kanäle an, um die sich beim Gusse im Kerne
entwickelnden Gase abzuführen. Man formt nun den Kern und die Modelle in getheilten
Formkasten ein, nimmt dann beide heraus und legt den Kern wieder in den Formkasten,
wonach der Guſs beginnen kann.
Bei der Röhrenformpresse von J.
M. Laski in Hamburg (* D. R. P. Nr. 31563 vom 22. November 1884) wird das
Rohrmodell C (Fig. 11 bis 13 Taf. 20) in
einen feststehenden Kasten a gelegt und darin durch die
umlegbaren Hebel m in einer solchen Lage unterstützt,
daſs genau die obere Hälfte des Modelles über den oberen Rand von a vorsteht. Man stülpt nun über den Kasten a einen zweiten Kasten d,
dessen lichte Weite der äuſseren Breite entspricht, so daſs d dicht schlieſsend auf a auf- und abbewegt
werden kann. An den Kopfenden besitzt d
zwei Arme e mit Schraubenmuttern, in welche 2 Schraubenbolzen f eingreifen, die gleichzeitig und gleichmäſsig in
Umdrehung versetzt werden. Nachdem man d in der in Fig. 11
gezeichneten Stellung über dem Modelle C mit Formsand
gefüllt hat, setzt man auf d die eigentliche
Formkastenhälfte q und befestigt sie an d mit Schrauben. Nun senkt man d über a nach unten durch Drehung der
Schrauben f, bis sich die oberen Kanten von a und d vergleichen (Fig. 12). Der
Sand ist dann aus d nach q
gelangt und ist um das Modell festgepreſst worden. Das Modell C wird dann durch Umlegen der Hebel m gesenkt und q mit der
Sandform abgenommen, wonach die Herstellung der anderen Formhälfte vorgenommen
werden kann. Die Bewegung des Kastens d kann auch durch
Preſswasser erfolgen, oder es kann auch a bewegt
werden, während d und q
feststehen.
Im Techniker, 1885 * S. 285 ist ein federnder, sich teleskopartig in einander schiebender
Formkasten beschrieben, welcher von Ed. Frieſs
in Louisville angegeben, für Deutschland an Friedr.
Hahn in Laaspke, Westfalen (* D. R. P. Nr. 32580 vom 23. Januar 1885)
patentirt ist und sich hauptsächlich zur Herstellung von Formen für Massenartikel in Formpressen eignet.
Wie in Fig. 4 und 5 Taf. 20 veranschaulicht
ist, besteht jede Formkastenhälfte aus einem einfachen Streifen b von Stahl- oder Eisenblech, welcher zu einem Ringe
zusammen gebogen ist, dessen Enden sich federnd gegenüber stehen. Dieser offene Ring
kann durch einen Haken a geschlossen werden. Damit das
Einpressen des Sandes in diesem Kasten mittels einer Druckplatte gleichmäſsig vor
sich gehe, ist in dem federnden Blechringe b noch ein
zweiter ähnlicher Blechring c, aber ohne Schluſshaken,
eingesetzt, welcher sich aus ersterem etwas herausziehen läſst. Wird nun in die
ausgezogenen Blechringe Sand eingefüllt und der Formkasten in eine Presse gebracht,
so wird der Sand zusammengedrückt, wobei der innere Blechring sich in den äuſseren
hineinschiebt. Da der Sand vorher eben über dem inneren Ringe abgestrichen wurde, so
geschieht das Zusammendrücken desselben gleichmäſsig, was bei dünnen und besseren
Güssen sehr wichtig ist.
Um nun beim Einfüllen des Sandes ein Maſs zu haben, wie weit der
innere Blechring aus dem äuſseren herausgezogen werden soll, ist der innere Ring mit
drei nach auſsen übergreifenden Führungsbolzen d
versehen, welche an dem äuſseren Ringe in Oesen geführt sind und deren Länge
(entsprechend der gewünschten Ausziehlänge des inneren Ringes) nach Belieben gewählt
werden kann. Der obere und der untere Kasten sind in dieser Beziehung völlig gleich
eingerichtet. Um dieselben nun mit der dazwischen liegenden Modellplatte e genau über einander zu halten und später, nach
Entfernung der Modelplatte, wieder genau in dieselbe Stellung bringen zu können,
sind am Unterkasten zwei lange Bolzen f befestigt, an
welchen der Oberkasten sich mit einem Paar Furchen führt.
Bei der Benutzung wird zuerst der mit einem Haken geschlossene
Unterkasten auf dem Preistische aufgestellt und mit Sand gefüllt, wobei man den
inneren Ring in der gewünschten Höhe auszieht. Dann legt man die Modellplatte auf
den Unterkasten und setzt auf diese den geschlossenen Oberkasten, welcher mit Sand
aufgefüllt wird, nachdem der innere Ring so weit, wie gewünscht, ausgezogen ist.
Beim Pressen werden die inneren Ringe in die äuſseren eingedrückt, so weit es der
Sand erlaubt. Hierbei hat man den Vortheil, daſs der Druck auf beiden Seiten der
Modellplatte gleich ist und also ein Verbiegen derselben und eine unregelmäſsige
Sandform möglichst vermieden wird. Nachdem die Sandformen fertig gepreſst sind, wird
die Modellplatte herausgenommen und der Oberkasten wie vorher auf den Unterkasten gesetzt.
Um die runden Blechkästen mit den inneren Ringen von den Sandformen zu entfernen,
braucht man nur die beiden Haken a an den Blechringen
b zu öffnen. Die Blechringe springen dann durch
ihre Elasticität auf und lassen sich nun leicht abnehmen, während die Sandformen
stehen bleiben und auf einer Unterlage in den Gieſsraum getragen werden können. Das
Arbeiten mit diesen runden, aufgeschlitzten elastischen Blechkästen soll mit groſser
Leichtigkeit und Schnelligkeit von statten gehen.
Eine einfache Formmaschine bringt K. Reuſs auf Adolfshütte bei Dillenburg, Nassau (* D.
R. P. Nr. 31910 vom 12. September 1884) in Vorschlag. Bei derselben wird die
Formplatte a (Fig. 6 Taf. 20) auf den
Tisch b geschraubt, welcher in Führungen innerhalb des
Tischrahmens d auf- und abbewegt werden kann. Die
Formkasten e sind auf der Stoſsfläche eben
zusammengerichtet und haben je zwei an den Endpunkten einer Diagonalen stehende
gedrehte Stifte und je zwei entsprechende, auf der anderen Diagonalen befindliche
Löcher. Auf diese Weise passen die Formkastenhälften auf einander und in die Löcher
der Formplatten. Die untere Flansche des Formkastens deckt die Fuge zwischen dem
festen Rahmen d und dem auf- und abbeweglichen Tische
b und bewirkt, daſs der Formkasten von der
Formplatte beim Pressen des Sandes mit nach oben genommen wird, dagegen beim
Herablassen des Tisches bezieh. der darauf befestigten Modellplatte sich auf den
festen Rahmen aufsetzt und die Modellplatte frei gibt.
Die Druckplatte f ist in den Führungen g nach vorn und hinten verschiebbar und wird nur behufs
Pressung des Sandes über den Formkasten gestellt, wobei der Druckrahmen h und der Druckklotz i in
Anwendung kommen.
Beim Formen wird der Hebel k in die
mittlere Lage eingeklinkt, wodurch die Modellplatte genau in die Fläche des Rahmens
d festgestellt wird. Die eine Formkastenhälfte wird
nun aufgesetzt, die Modellplatte in üblicher Weise gestäubt, Modellsand aufgesiebt
und der Druckrahmen h voll Sand gefüllt. Dieser wird
mit den Händen ein wenig geebnet und eingedrückt und dann die Druckplatte mit dem
daran befestigten Druckklotze vorgezogen, wobei letzterer den überstehenden Sand
abstreicht. Nun wird der Hebel nach vorn kräftig angezogen, wodurch mittels des
excentrischen Hebedaumens n und der Druckstange o der bewegliche Tisch mit sammt der Formplatte und dem
mit Sand gefüllten Formkasten und Druckrahmen nach oben gegen den Druckklotz
gepreſst wird. Sodann wird der Hebel wieder in der mittleren Stellung eingeklinkt,
die Druckplatte mit dem daran befestigten Druckklotze nach hinten geschoben, der
Druckrahmen abgenommen und der Sand mit einem eisernen Lineal abgestrichen. Hierauf
wird der Hebel langsam nach hinten geschoben, wodurch sich die Modellplatte senkt
und die fertigen Formkasten zum Wegsetzen auf dem festen Rahmen stehen läſst. In
gleicher Weise wird der Oberkasten mit dem Eingüsse eingeformt, wofür zweckmäſsig
eine zweite Maschine verwendet wird, wenn sich die Modelle nicht, wie z.B.
Thürdrücker, Handräder, in zwei Hälften theilen lassen.
(Schluſs folgt)
Tafeln
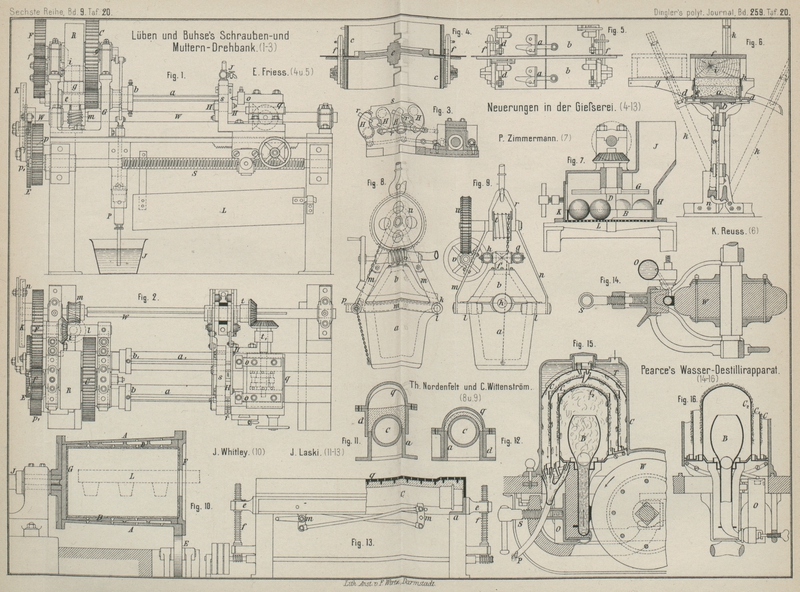