Titel: | Neuerungen in der Herstellung von Thonwaaren und Kohlenziegel. |
Autor: | H. F. |
Fundstelle: | Band 262, Jahrgang 1886, S. 157 |
Download: | XML |
Neuerungen in der Herstellung von Thonwaaren und
Kohlenziegel.
(Patentklasse 80. Fortsetzung des Berichtes Bd.
260 S. 164.)
Mit Abbildungen auf Tafel
11.
Herstellung von Thonwaaren und Kohlenziegel.
Der Abschneidetisch für Falzziegel von J. Schmidheiny in Heerbrugg (* D. R. P. Nr. 34411 vom
25. Januar 1885) kennzeichnet sich durch eine eigenartige Vorrichtung, vermöge
welcher in der beim Vorfahren des Wagens entstehenden Spalte des Rollenfeldes
selbstthätig Rollen eingeschoben werden, weiter durch die Einrichtung, welche
bezweckt, die einzelnen
Ziegel schonender als bisher auf Abheberähmchen legen zu können. Die erstere
Vorrichtung besteht aus senkrecht verschiebbaren Rollen, deren Lager auf den Enden
doppelarmiger Hebel ruhen, welche an ihren anderen Enden so gekrümmt sind, daſs eine
Achse des fahrbaren Tischtheiles die Hebel rechtzeitig niederdrückt, also die Rollen
gehoben werden. Das Abheberähmchen wird vor dem Zurückfahren des Wagens in das
Rollenfeld gelegt und zwar etwas tiefer als die Oberfläche des Rollenfeldes, so daſs
der Thonstrang während des Zurückfahrens nicht gegen das Rähmchen stöſst. Lage und
Länge des Rähmchens sind so gewählt, daſs die Abschneidedrähte dicht an den
Schmalseiten desselben niedergehen, wodurch ein reiner Schnitt gesichert werden
soll.
Bei der Vorrichtung zur Herstellung bogenförmiger
Backsteine von L. Scherrer I. in Pfungstadt (*
D. R. P. Nr. 35489 vom 27. Oktober 1885) wird der in gewöhnlicher Weise gebildete
Thonstrang nach Verlassen des Mundstückes zwischen liegenden und stehenden Rollen im
Bogen geführt bezieh. krumm gebogen und hierauf in der Richtung des
Krümmungshalbmessers in gewöhnlicher Weise zerschnitten.
W. Boulton in Burslem (* D. R. P. Nr. 36212 vom 31.
Oktober 1885) hat die in Fig. 9 bis 11 Taf. 11 in
Vorderansicht, Seitenansicht und im Grundrisse dargestellte selbstthätige Töpferscheibe angegeben. Mittels einer Schnur oder eines
Riemens werden mehrere (hier zwei) Töpferscheibenspindeln t und ferner eine senkrechte Spindel a
betrieben. Auf jeder Spindel t ist eine Metallhülse b befestigt, welche zur Aufnahme der Gypsform c geeignet ist. An einem doppelarmigen, um den Bolzen
d schwingenden Hebel e
sind zwei (oder mehrere) gleiche Lehren f befestigt,
welche den Thon gegen die Wandungen der Formen c
drücken sollen. Zu dem Ende wirkt auf das von den Lehren abgewendete Ende des Hebels
e ein Daumen g, dessen
Welle l durch einen auf a
befestigten Wurm angetrieben wird. Der Körper, in welchem der Bolzen d steckt, ist vermöge eines senkrechten Zapfens in der
Hülse h um einen kleinen Winkel drehbar. Durch
Auswüchse des Daumens g einerseits und des Hebels e andererseits wird diese Drehung herbeigeführt und
zwar, nachdem die Lehren f in ihrer tiefsten Lage
angekommen sind, so daſs der Thon recht fest gegen die Form gedrückt wird. An der
Achse i befinden sich die Abschneider k, welche ebenfalls in geeignetem Zeitpunkte und zwar
von einem zweiten Daumen der Welle l aus niedergesenkt
werden und dann den oberen Rand des thönernen Gegenstandes gestalten.
Nach Fertigstellung des Werkstückes werden die Gypsformen c aus den Hülsen b gehoben und durch andere
ersetzt. Dies geschieht im Wesentlichen selbstthätig auf folgende Weise: Auf einer
Platte m befinden sich Ringe n, welche, wenn sie gehoben werden, unter den überragenden Rand der
Gypsformen greifen. Die Platte m ist zunächst senkrecht verschiebbar;
sie wird gehoben durch den Daumen o der Welle l und die doppelarmigen Hebel p. Sobald das Ausheben der Formen stattgefunden hat, schiebt nun der
beaufsichtigende Arbeiter die Platte m in wagerechter
Richtung zur Seite, so daſs die benutzten Formen seitwärts von den Spindeln t, frische in die leeren Ringe der Platte m eingesetzte Formen aber über die Hülsen b der Spindeln zu stehen kommen. Der Tisch sinkt
nunmehr nieder und die Lehren wie Abschneider kommen aufs Neue in Thätigkeit.
Die Maschine enthält zweifellos manches Hübsche, dürfte aber eine gründliche
Durcharbeitung seitens eines Maschinenkundigen nöthig haben.
Die von M. Balcke in Düsseldorf (* D. R. P. Nr. 35416
vom 25. Juni 1885) in Vorschlag gebrachte Maschine zur
Herstellung der Preſsnuſskohle benutzt eine bekannte Meſsvorrichtung, um in
bestimmtem Verhältnisse mageren und fetten Kohlenstaub sowie flüssiges Bindemittel
in eine dem Mischen dieser Theile dienende Polterschnecke zu bringen. Neu ist die
Einschaltung einer Erweiterung in die Polterschnecke, zum Zwecke gründlichen
Durcharbeitens der zu mischenden Stoffe. Letztere werden sodann sogen.
Reibungspressen (vgl. Exter 1883 250 * 201) überantwortet, an welchen als neu eine Abschneidevorrichtung
hervorgehoben wird. Um nämlich den (etwa) ungetheilt aus den Mundstücken der Presse
hervorquellenden Strang zu zerlegen, befindet sich vor jedem Mundstücke ein Messer,
welches gegen den Strang verschoben wird, während der Preſskolben zu neuem Stoſse
ausholt.
Eine Einrichtung an Reibungspressen, um mittels derselben
halbe Kühlenziegel herzustellen, von F. A.
Schulz in Halle a. S. (* D. R. P. Nr. 34746 vom 18. Juli 1885) bezieht sich
auf die Einschaltung zweier kleinerer neben einander liegender Preſsmundstücke an
Stelle des den Exter'schen Reibungspressen eigenen
einzigen Mundstückes. Die oberen und unteren Mundstücktheile sind in bekannter Weise
gegen einander verstellbar (vgl. 1883 250 * 202). Auſser
diesen Mundstücktheilen nutzen sich die Seitentheile längs schmalen Flächen ab,
weshalb diese auswechselbar gemacht sind. a2 (Fig. 7 und 8 Taf. 11) ist z.B. ein
auswechselbares Zwischenstück, während a1 als der Abnutzung nicht unterliegend, nicht
ausgewechselt werden soll.
P. Servais in Ehrang (* D. R. P. Nr. 34413 vom 1. März
1885) hat eine Vorrichtung zum selbstthätigen Abheben der
Thonplatten u. dgl. von Preſsformen angegeben, welche den Zweck hat, in
geschlossener Preſsform gestaltete Gegenstände nach einem Orte zu tragen, von
welchem sie durch Arbeiter bequem und gefahrlos entfernt werden können (vgl. Schlickeysen 1884 251 154).
Voraussetzung ist, daſs man die Werkstücke mittels des Formbodens über den Rand der
Form zu heben vermag; nachdem sie hier angekommen, soll die in Fig. 12 bis 15 Taf. 11
dargestellte Vorrichtung in Thätigkeit treten.
In diesem Zeitpunkte befindet sich das Werkstück A in
der durch
Fig. 15
veranschaulichten Lage gegenüber den beiden Greifern f;
diese bilden zwei Schaufeln, welche sich mit den Achsen e in Augen der Schrauben d zu drehen
vermögen. Die Schrauben d sind in zwei Schienen b von hakenförmigem Querschnitte, welche das Querstück
c mit einander verbindet, befestigt und bilden mit
diesem zusammen den auf Schienen a, die auf dem Rande
der Preſsform befestigt sind, verschiebbaren Schlitten. Die Verschiebung desselben
findet von dem Preſsstempel aus statt und zwar unter Vermittelung geeignet
angebrachter Ketten und Gegengewichte. Auf den Achsen e
der Greifer sind Zapfenstücke g so angebracht, daſs
dieselben sich in der Achsenrichtung nicht zu verschieben, aber um die Achse längs
eines kleinen Winkels zu drehen vermögen, wie durch Vergleichung der Fig. 14 und 15 ersichtlich
ist. Die Enden g1
dieser Zapfen g sind so gestaltet (vgl. Fig. 12), daſs sie an den
Rändern der Schienen h verhältniſsmäſsig gut zu gleiten
vermögen; da die Schienen h mittels der Stehbolzen i an den festen Schienen a
der Presse befestigt sind, so erfolgt bei Verschiebung des Schlittens bezieh.
vermöge Einwirkung der Schienen h zunächst ein Drehen
der Zapfen g um die Achsen e und sodann ein Heben bezieh. Senken der Greifer f. In der durch Fig. 12 bis 14 Taf. 11
wiedergegebenen Stellung der einzelnen Theile ist das Werkstück A von den Greifern f
erhoben und wird, bei Fortbewegung des Schlittens in der Pfeilrichtung der Fig. 12
getragen, bis die Zapfenenden g1 die rechts liegenden Enden der Schienen h überschritten haben. Die schwereren Greifer fallen
alsdann nieder und lassen A an dem neuen Platze liegen.
Nunmehr findet die Verschiebung des Schlittens in entgegengesetzter Richtung statt,
die Zapfenenden g1
bewegen sich über den Schienen h hinweg und werden durch diese mehr gehoben, als die Greifer verlangen
(was wegen der geringen Drehbarkeit der Zapfen g auf
den Greiferwellen e möglich ist), so daſs nach
Eintreffen des Schlittens am Endpunkte seiner rückläufigen Bewegung die Zapfenenden
g1 links von den
Schienen in Bezug auf Fig. 12 so weit
niederfallen, um sie bei dem Vorwärtsgange des Schlittens unter die Schienen h zu zwingen. Die
Begrenzung des Schlittenweges bewirken die Knaggen t,
gegen welche die Buffer k stehen. In der Ruhelage, d.h.
während des Pressens wird der Schlitten vermöge der Schiene n von einer Klinke o (Fig. 15) festgehalten.
Sobald der gepreſste Gegenstand über den Rand der Form erhoben ist, ist auch die
Klinke o ausgelöst, so daſs die mit Gewicht belastete
Kette, welche an dem Querstücke c des Schlittens
angreift, die Vorwärtsbewegung des Schlittens ausführen kann. Bedenken erregt die
leichte Abnutzbarkeit der Theile dieser Vorrichtung und die Thatsache, daſs die
gepreſsten Gegenstände seitens der Greifer beschädigt werden.
H. F.
Tafeln
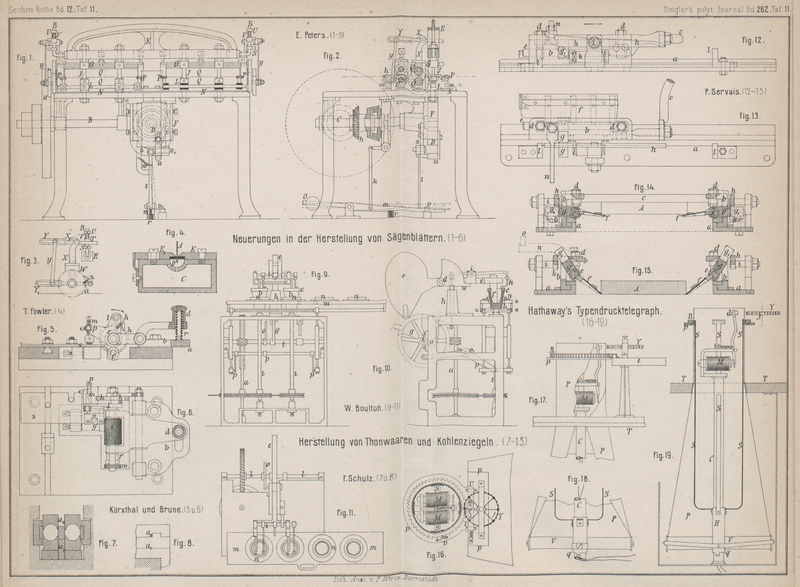