Titel: | Neuerungen an Apparaten zur Erzeugung von Wassergas. |
Fundstelle: | Band 264, Jahrgang 1887, S. 26 |
Download: | XML |
Neuerungen an Apparaten zur Erzeugung von
Wassergas.
Patentklasse 26. Mit Abbildungen auf Tafel 3.
Neuerungen an Apparaten zur Erzeugung von Wassergas.
Leitet man Wasserdampf durch glühende Kohlen, so entsteht bekanntlich durch
Zersetzung des Dampfes ein Gemisch von Kohlenoxyd, Wasserstoff und Kohlensäure,
welches in herkömmlicher Weise „Wassergas“ genannt wird (vgl. 1887 263 108). Die ältesten Einrichtungen zur Erzeugung von
Wassergas stammen aus Nordamerika. In neuerer Zeit sind jedoch auch in Deutschland
verschiedene Constructionen für Wassergasapparate vorgeschlagen worden.
Die Europäische Wassergas-Actiengesellschaft in Dortmund
hat in Deutschland die nachfolgend angeführten vier Patente, welche Einrichtungen an
Wassergasapparaten betreffen, erworben.Diese Patente datiren sämmtlich vom 13. December 1885 und führen folgende
Ueberschriften. Nr. 35934: Umschaltvorrichtung für
Wassergasapparate. Kr. 36431: Einrichtung
an Wassergasgeneratoren zur Abdestillirung des frischen
Brennmaterials. Nr. 36665: Anordnung zur
Dampferzeugung bei Wassergasapparaten. Nr. 36712: Neuerungen an Wassergasapparaten zum Zwecke der
Dampfezeugung.
Nach dem Patente Nr. 36431 sollen bei der Verarbeitung von Steinkohle auf Wassergas die flüchtigen Bestandtheile der Kohle dadurch
ausgetrieben werden, daſs man mittels des beim Warmblasen aus dem Brennmateriale
entstehenden Gases einen „Regenerator“ heizt, mit Hilfe der in letzterem
aufgespeicherten Wärme Wasserdampf überhitzt und nun einen Theil dieses Dampfes
durch das frische Brennmaterial streichen läſst, während der andere Theil desselben
wie gewöhnlich zur Wassergasbereitung dient. Das auf diese Weise gewonnene
Kohlenwasserstoffgas kann entweder als Leuchtgas Verwendung finden, oder man mischt
es mit demjenigen Dampf, welcher zur Erzeugung von Wassergas aus dem festen
Brennmateriale dient, und leitet das Gemisch durch den erhitzten Regenerator, um die
Kohlenwasserstoffe neben dem festen Brennmateriale zur Gewinnung von Wassergas zu
benutzen.
Wie aus Fig. 1
Taf. 3 zu ersehen, wird zur Ausführung genannten Verfahrens bei Wassergasgeneratoren
der Generator D über den zum Regenerator B führenden Kanal S hinaus
verlängert, so daſs ein Raum E entsteht, welcher zum
Austreiben der flüchtigen Bestandtheile des Brennmaterials dient und daher mit einem
Ableitungsrohre R versehen sein muſs. Beim Beginne des
Prozesses werden die Gasschieber G und O im Rohre P bezieh. R geschlossen, dagegen der Windschieber L in der Rohrleitung K,
das Ventil J zwischen Regenerator und Winderhitzer C und der in der Oberwindleitung M befindliche Hahn geöffnet. Alsdann durchdringt der
durch die Rohrleitung K strömende Wind die Kohle im
Generator D bis zur Höhe des Kanales S. Das bei der theilweisen Verbrennung der Kohle
entstehende Generatorgas tritt in den ringförmigen Kanal F und von da durch Kanal S in den Regenerator
B, um daselbst mittels des durch M eintretenden Oberwindes verbrannt zu werden. Die
Verbrennungsgase geben ihre Wärme an den Regenerator oder auch an den Winderhitzer
C ab und entweichen durch N in den Schornstein.
Sobald Brennmaterial und Regenerator genügend erhitzt sind, werden Windschieber L, Ventil J und Windrohr
M geschlossen. Nachdem der Raum E mit frischer Kohle beschickt und der Gasschieber G geöffnet ist, wird durch das Rohr H Dampf in den Regenerator geblasen. Derselbe tritt aus
letzterem überhitzt nach der Kohlensäule D und
verwandelt sich dort in Wassergas, welches durch P
entweicht. Wenn das Material in D zur Wassergasbildung
zu sehr abgekühlt ist, schlieſst man G, öffnet O und treibt den Dampf durch E zur Entfernung der flüchtigen Bestandtheile, welche, wie oben angegeben,
verwerthet werden.
In dem Patente Nr. 36665 ist der Generatorschacht A
(Fig. 2
Taf. 3) gleichfalls nach oben zu verlängert, wodurch ein aus feuerfesten Steinen
gebildeter und mit gelochtem Wasserrohr F versehener
Raum B geschaffen ist, welcher den zur Erzeugung von
Wassergas nothwendigen Dampf ohne Anwendung eines
Dampfkessels liefern soll. Durch die von unten aus der Windleitung C in die glühende Kohlenmasse dringende Luft wird
Generatorgas erzeugt, welches oberhalb der Kohlen durch die gleichfalls aus C kommende Luft verbrannt wird. Die entstandene Wärme
wird gröſstentheils von den Steinen im Raume B
aufgenommen. Sobald die Temperatur des Kohlenschachtes hoch genug ist, wird der Wind
abgestellt, der Kaminschieber geschlossen, der das Rohr E absperrende Hahn geöffnet und durch Hahn K
und Rohr F Wasser eingelassen; letzteres verwandelt
sich in Dampf, welcher dann die glühenden Kohlen in A
durchstreicht und sich in Wassergas verwandelt.
Eine andere Einrichtung zur Dampferzeugung besteht (nach
D. R. P. Nr. 36712) darin, daſs der Generator D (Fig. 3 Taf. 3)
derart in einen mit Feuerbüchse A versehenen
Dampfkessel verlegt wird, daſs die Büchse den Mantel des Generators bildet. Der im
Generator über dem Brennmateriale frei bleibende Raum dient dann als Feuerraum des
Kessels und dessen
Wandung als Dampf erzeugende Fläche, welche noch durch Einfügung von Field-Röhren
vergröſsert werden kann. Das Rohr M liefert die zur
Verbrennung erforderliche Oberluft, während das Rohr b
während der Periode des Warmblasens erwärmte Luft in den Raum G führt und das Rohr H den
für die Wassergasbildung nothwendigen Dampf zuleitet. Eine besondere Vorrichtung
dient zur getrennten Abführung der Verbrennungsgase und des Wassergases aus der
Feuerbüchse. Das Rohr M ist mit dem Raume B in Verbindung gesetzt, welcher sich in dem die
Beschickungsöffnung Z umgebenden ringförmigen Aufsatz
befindet. Die obere Mündung dieses Aufsatzes, der Fuſs des Schornsteines C und der die Oeffnung Z
während der Gasbereitung verschlieſsende Schieberdeckel sind so zu einander
angeordnet, daſs, wenn der Schornstein über der Oeffnung Z steht, der Kanal B für den Lufteintritt
offen ist, daſs dagegen der über die Oeffnung Z
geschobene Deckel auch den Kanal B schlieſst,
Endlich ist noch eine Umschallvorrichtung (D. R. P. Nr.
35934) für solche Wassergasapparate zu erwähnen, bei denen das Brennmaterial durch
dieselbe Oeffnung aufgegeben wird, welche auch zur Abführung der Verbrennungsgase in
den Schornstein dienen muſs. Die Einrichtung besteht im Wesentlichen darin, daſs
mittels einer durch einen Steuermechanismus zu bewegenden Platte ein Schornstein,
ein Fülltrichter und ein Deckel über die Beschickungsöffnung geschoben werden
können. In Verbindung damit ist ein Dampfhahn in Anwendung, welcher aus einem
feststehenden unteren Theil besteht, der einen Hahnkegel und zugleich den Drehzapfen
für genannte Platte bildet, ferner aus einem Hahngehäuse mit Küken als drehbarem
Mitteltheile und aus einem feststehenden Gehäuse.
In Essen, auf dem Werk von Schulz, Knaudt und Comp. ist
ein Wassergasapparat, welcher im Wesentlichen nach amerikanischem System (Strong) gebaut wurde, in Betrieb gesetzt (vgl. Stahl und Eisen, 1886 * S. 3. Zeitschrift des Vereins deutscher Ingenieure, 1886 * S. 407). In den
Schacht des eigentlichen Gasgenerators (Fig. 4 Taf. 3) wird
abwechselnd von unten Wind eingeblasen, um die aufgegebenen Kokes durch Verbrennen
des unteren Theiles derselben zum Glühen zu bringen. Nach Abstellung des Windes wird
von oben Dampf eingeblasen, welcher durch einen doppelten Regenerator erhitzt worden
ist; letzterer wird nun durch die Abhitze der während des Warmblasens im Generator
erzeugten Gase erhitzt. Man hat davon Abstand genommen, die letzteren, obgleich sie
mit gewöhnlichem Generatorgas übereinstimmen, vor ihrem Eintritte in den Regenerator
durch Zuführung von Oberwind zur Verbrennung zu bringen, weil hierdurch die Hitze im
Regenerator so hoch steigt, daſs die Steine unter Mitwirkung der Flugasche sehr
rasch der Zerstörung anheimfallen. Es wird somit die gesammte Windmenge zum
Warmblasen verwendet. Die Erzeugung von Wassergas ist hierdurch von 120cbm auf 250 und 300cbm in einer Stunde gestiegen, ohne daſs ein merklicher Mehrverbrauch von
Brennstoff stattgefunden hätte.
Wie aus Fig. 4
Taf. 3 ersichtlich, ist im Generator der Rost beseitigt (vgl. auch Fig. 1 und 3) und an seiner Stelle
ein mit Wasser gekühlter Ring eingeführt, welcher den ganzen oberen Ofenschacht
trägt. Da dieser Schacht im Inneren etwas vorspringt, bildet sich unter demselben
ein ringförmiger freier Raum E, in welchen die
Gebläseluft eintritt und aus dem bei der Gasbereitung das Wassergas austritt. Die
Schlacke bildet auf der kegelförmigen Böschungsfläche des Brennstoffes einen Mantel,
welcher bis in die ringförmige Oeffnung (des Wasserringes) reicht und durch
Reinigungsöffnungen mit Morton-Verschluſs ohne Schwierigkeit entfernt wird. Von hier
tritt das Wassergas durch einen Wasserabschluſs F in
eine Reinigungsöffnung ein, aus einem sogen. Scrubber G
bestehend, aus welchem es in den Gasometer gelangt. Im Anfange der Gasbereitung ist
das Gas frei von Kohlensäure und Wasserdampf; in dem Maſse, wie sich die Kohlen
abkühlen, enthält es gröſsere Mengen von beiden. Der Wassergehalt wurde nicht über 4
Proc. beobachtet.
Um die Gefahr zu beseitigen, daſs während des Warmblasens Wind in den Gasometer oder
während der Gasbereitung Gas in die Windleitung eintrete, wodurch die Bildung von
Knallgas möglich wäre, wird ein eigenthümlicher Schieber angewendet, welcher sammt
seinem Gehäuse mit Wasser gekühlt ist. Windventil, Gasventil, Kaminschieber und
Dampfzulaſshahn müssen offenbar in bestimmter Aufeinanderfolge geöffnet und
geschlossen werden. Um dabei von der Aufmerksamkeit des Arbeiters unabhängig zu
sein, werden alle diese Organe von einer Steuerwelle bewegt, welche durch ein
Steuerrad, rechts und links gedreht, alle Schieber und Ventile in richtiger
Reihenfolge öffnet und schlieſst.
Der Ofen erzeugt bei einer Blasezeit von 10 und einer Gasbereitungszeit von 5 Minuten
250 bis 300cbm Wassergas stündlich mit einem
Kohlensäuregehalte von nicht über 4 Proc., so daſs er ein Gas liefert, welches
(auſser 5 Proc. Stickstoffgehalt) 4 Proc. Kohlensäure, 41 Proc. Kohlenoxyd und 50
Proc. Wasserstoff enthält.
Die deutschen Apparate stimmen im Wesentlichen mit den amerikanischen überein. Die
vorhandenen Unterschiede werden in erster Linie durch die Natur des Brennmaterials
und in zweiter Linie durch die Art der Verwendung des Wassergases bedingt. In
Nordamerika, dem eigentlichen Vaterlande des Wassergases, wird Anthracit in
erbsengroſsen Stücken verwendet; derselbe gibt beim Verbrennen nahezu keinen Staub
und keine Schlacke. Die Folge davon ist, daſs die Regeneratoren, deren gröſster
Feind bekanntlich die Flugasche ist, sich gut halten. Auch können die sich bildenden
unbedeutenden Schlackenmengen mit Leichtigkeit entfernt werden.
In Deutschland werden vorzugweise Kleinkokes oder Schröber (Abfallkokes) oder
Gaskokes verwendet. Der Aschengehalt beträgt bis zu 30 Proc., was eine reichliche
Bildung von Schlackenmassen zur Folge hat. Ferner können wir in Deutschland nicht
soviel Kohlensäure im Wassergas dulden als in Amerika, da dieselbe nicht wie dort
beim Carburiren wieder zersetzt wird, sondern durch kostspielige Kalkreinigung
entfernt werden müſste. In Nordamerika wird das Wassergas vorzugsweise zu
Leuchtzwecken benutzt und daher mit Hilfe von schweren Kohlenwasserstoffen,
namentlich von Erdölrückständen, carburirt. Dieses Carburiren geschieht, indem man
entweder dem Wassergase schwere Kohlenwasserstoffe zusetzt und das Gemisch in einem
Regenerator hoch erhitzt (Lowe'sches Verfahren), oder
indem man das Wassergas durch eine Reihe hoch erhitzter Retorten treibt, in welche
man die Kohlenwasserstoffe vorher eingetragen hat (Tessié de
Motay), oder endlich, indem man den Wasserdampf vorher in einem Regenerator
erhitzt und dann, mit schweren Kohlenwasserstoffen gemischt, durch die glühende
Kohle treibt (Strong).
In Deutschland ist das Wassergas bisher fast nur und zwar mit gutem Erfolge zu
Schmelz- und Heizzwecken verwendet worden, indem uns jene billigen
Carburirungsmittel fehlen. Doch scheint auch bei uns das Wassergas noch eine
besondere Rolle auf dem Gebiete des Beleuchtungswesens spielen zu sollen, seitdem
durch Fahnehjelm (1886 259 *
413. 261 * 526) und Auer v.
Welsbach (1886 261 * 527) jene Glühkörper
erfunden worden sind, mittels deren bei Verwendung von Wassergas sich hohe
Lichtwirkungen erzielen lassen.
Im Oesterreichischen Ingenieur- und
Architektenverein zu Wien hat Ingenieur Jos. R. v.
Langer über die Wassergasanlage zu Witkowitz
nähere Mittheilungen gebracht, denen nach der Wochenschrift, 1887 S. 26 folgender Auszug entnommen ist.
Die Wassergasanlage zu Witkowitz besteht aus dem Generator- und
Scrubberhause, der Kesselanlage, dem Maschinenhause, dem Gasometer und dem
Reinigerhause.
Im Generatorhause stehen zwei Generatoren mit wassergekühltem
Ringe, ein Generator, bei welchem die Schlacke flüssig abgestochen wird, zwei
Kokesscrubber, ein Rohrencondensator und zwei Reinigungskästen.
Die Kesselanlage besteht aus vier Cornwallkesseln mit je 120qm Heizfläche, welche durch die Siemens-Gase
geheizt werden. Die Siemens-Gasleitung vom Generatorhause zur Kesselanlage hat
800mm Lichtweite. Der erzeugte Dampf wird
theilweise zum Betriebe der Wassergasanlage verwendet, zum gröſseren Theile jedoch
von der Walzhütte verbraucht.
Im Maschinenhause befinden sich zwei Paar Doppelgebläse, welche in
der Stunde 5000cbm Luft liefern können; dieselben
laufen mit etwa 2000 Umgängen. Die Betriebsdampfmaschine, welche mit etwa 20 Pferd
arbeitet, bethätigt mit Riementriebwerk diese Flügelgebläse. Eine Kaltwasserpumpe,
welche im Stande ist, in der Minute 1cbm,5 Wasser
zu liefern, befördert das Kühlwasser in einen Behälter, welcher sich am Arbeitsboden
des Generatorhauses befindet und 16cbm Fassung
besitzt. Auſserdem befinden sich in diesem Raume die Speisepumpen für die
Kessel.
Der Gasometer hat 1200cbm
Fassung, gibt 120mm Druck, die Einströmung beträgt
350mm, die Ausströmung 400mm; der Wasserbehälter ist gemauert. Aus dem
Behälter geht eine 400mm weite Leitung in die
Hütte, eine 200mm weite Leitung in das Reinigerhaus, wo
sich 4 Reinigungskästen mit je 7cbm,8 Inhalt
befinden, eine Gasuhr für 247cbm Durchgang in der
Stunde und ein Druckregulator. Das gereinigte Gas wird zur Beleuchtung und Beheizung verwendet.
Der Generator mit Schlackenabstich kommt hier nicht zur
Beschreibung und ist bei den nachstehenden Berechnungen nicht einbezogen. Die beiden
Generatoren mit Kühlring arbeiten vollständig zufriedenstellend. Ihre Form und die
Art wie mit denselben im Allgemeinen gearbeitet wird, ist oben beschrieben. Bei der
Entfernung der Schlacke durch die Morton-Thüren wird ziemlich viel Kokes mitgezogen;
auch muſs während des Schlackens der Generator vollständig eingestellt werden und
dies ist der Grund, warum auf laufenden Schlackenabstich hingearbeitet wurde. Jeder
Generator hat etwa 10cbm nutzbaren Inhalt.
Um die Generatoren in Betrieb zu
setzen, wird Holzfeuer in denselbem angezündet, auf dasselbe werden 700k Kokes beschickt, worauf mit 50mm Wasserpressung zu blasen begonnen wird. Mit der
Brennstoffsäule erhöht man die Windpressung. Bei regelrecht gefülltem Apparate bläst
man mit 300mm Pressung (gemessen unter dem
Kühlringe). Sobald der Brennstoff in den obersten Schichten rothwarm ist, wird
umgestellt und Gas gemacht, d.h. Dampf eingelassen. Der Druck im Generator wird
oberhalb der Brennstoffsäule auf 700mm Wassersäule
gehalten. Abwechselnd wird 5 Minuten Gas gemacht und 10 Minuten warm geblasen. Alle
2 Stunden wird die Schlacke gezogen (bei gutem Brennstoffe dauert dies 20 Minuten),
hierauf der Generator auf regelrechte Höhe beschickt und warm geblasen, wozu 15
Minuten erforderlich sind. Wenn der Generator rein ist, d.h. nach dem Schlacken,
werden in demselben in 5 Minuten 180cbm Gas
gemacht, knapp vor dem Schlacken 110cbm.
Dieses Gas eignet sich zur Heizung von Siemens'schen Regenerativöfen ganz vorzüglich. Bei der Dampfkesselheizung
in Witkowitz gibt dieses Gas 60 bis 70° seiner Wärme an die Kessel ab. Die
Gasfeuerung der Kessel ist ähnlich durchgeführt wie bei Kesselanlagen, welche mit
Hochofengasen geheizt werden. Jeder Kessel besitzt überdies einen 2qm,5 groſsen Planrost. Diese Kessel geben bei
reiner Gasfeuerung nur 12 bis 14k Dampf für 1qm. Dieses geringe Ergebniſs hat seinen Grund in
der Construction der Kessel, welche für unmittelbare Verbrennung durchgeführt wurde.
Die Anwendung dieses vorzüglichen Siemens-Gases zur Kesselfeuerung ist nicht
zweckentsprechend, da ein solcher Brennstoff zur Dampferzeugung überhaupt zu theuer
ist.
Die Witkowitzer Anlage wird mit Würfel- und Nuſskokes, zu gleichen
Theilen gemengt, betrieben. Am 7. Juli 1886 wurden davon in zwei Apparaten 12080k durchgesetzt, wobei 17760cbm Wassergas erzeugt wurden. Auf Apparat und
Stunde entfallen 370cbm, wobei auf 1cbm Wassergas 5cbm Generatorgas entfallen. Auf 100k
verbrauchten Kohlenstoff entfallen 89cbm und auf
100k verbrauchten Kokes 71cbm,4 Wassergas. Da von 100k verbrauchten Brennstoff 21k,2 zur Wassergas-Erzeugung und 78k,8 zur Siemens-Gas-Erzeugung verwendet werden, so
ist es klar, daſs es nur dann denkbar ist, Wassergas zu hüttenmännischen Zwecken zu verwenden, wenn das Generatorgas gut
ausgenutzt und bezahlt wird. Geschieht letzteres, so ist die Erzeugung von Wassergas
neben Generatorgas mit so groſsen Vortheilen verbunden, daſs es um so mehr in kurzer
Zeit allgemein werden muſs, da ohne Zweifel Wassergas auch in entsprechenden
Generatoren aus Steinkohle, Braunkohle und Torf neben Generatorgas erzeugt werden
kann. Der beste Kokesgenerator, welcher sein Gas mit etwa 500° an den
Regenerativofen abgibt, bleibt, selbst unter Annahme, daſs das Siemens-Gas aus den
Wassergas-Generatoren völlig kalt verwendet wird, um 8 Proc. mit seinem Nutzeffecte
hinter dem Wassergas-Generator zurück.
Anwendung von Wassergas zum Schweißen und
Martiniren: Der Schweiſsofen war ein Versuchsofen, die Ueberhitze wurde in
einem stehenden Kessel ausgenutzt, das Gas, sowie die Luft standen unter Pressung
und waren kalt. In 12 Stunden wurden durch diesen Ofen durchgesetzt 8000k kalter Stahlknüppel zu 50 bis 80k. Der Gasverbrauch betrug in der Minute 6cbm, für 100k
Einsatz 27cbm, was 8k Kohle entspricht.
In derselben Zeit lieferte ein gewöhnlicher Planrost-Schweiſsofen
4500k gleichen Materials bei 40k Kohlenverbrauch auf 100k Einsatz (Stahlknüppel).
Es verbrauchte also der Wassergas-Schweiſsofen nur 58 Procent
jener Wärmemenge, welche der gewöhnliche Planrostofen für diese Arbeit erforderte.
Die Zustellung des Schweiſsofens machte in keiner Weise auf Vollkommenheit Anspruch.
Gegenwärtig ist dieser Ofen nicht mehr im Betriebe, da die Martinöfen das Gas
verbrauchen.
Der Martinofen für Wassergas erzeugt in 24 Stunden 10000k Stahl und verbraucht in der Minute 8ckm Gas. Die Feuerung ist ein sehr zweckmäſsiges
Regenerativsystem. Die Luft wird auf 1200 bis 1400° erhitzt und steht so wie das Gas
unter 110mm Wasserdruck. Die Temperatur ist nahe
der Platinschmelzhitze; die Verbrennungsgase haben hinter den Regeneratoren noch 400
bis 500°.
Auf 100k Stahl entfallen 60cbm Wassergas oder 19k Kohle. Anheizen und Einschmelzen des Bodens ist hierbei mit
einbezogen.
In einem gewöhnlichen Siemens-Martinofen werden in Witkowitz auf
100k Stahl 50k Kohle verwendet. Zu gleicher Leistung braucht der Wassergas-Martinofen
nur 47,8 Procent derjenigen Wärmemenge, welche der gewöhnliche Siemens-Martinofen
verwendet.
Die Erzeugungskosten des Wassergases
stellten sich im Durchschnitte des ersten Halbjahres, wobei in vieler Beziehung noch
sehr ungünstig gearbeitet wurde, auf 0,5 kr. für 1cbm Wassergas und 0,17 kr. für 1cbm
Siemens-Gas, oder für 10000c in Wassergas auf 1,77
kr. und für 10000c in Siemens-Gas auf 1,72 kr.
100k verbrauchter Brennstoff kosteten 48
kr.
Da die Wassergasöfen um etwa 50 Proc. günstiger arbeiten als die
Siemens-Regenerativöfen, so ist es ersichtlich, daſs das Wassergas sich im Betriebe
billiger stellt als das Generatorgas und somit auch die Wassergasgeneratoren
vortheilhafter arbeiten als irgendwelche bisher bekannte Generatoranlage. Nebenbei
sind die Wassergasöfen einfacher als die Siemens-Regenerativöfen und geben mit
groſser Sicherheit jede erforderliche Temperatur.
Tafeln
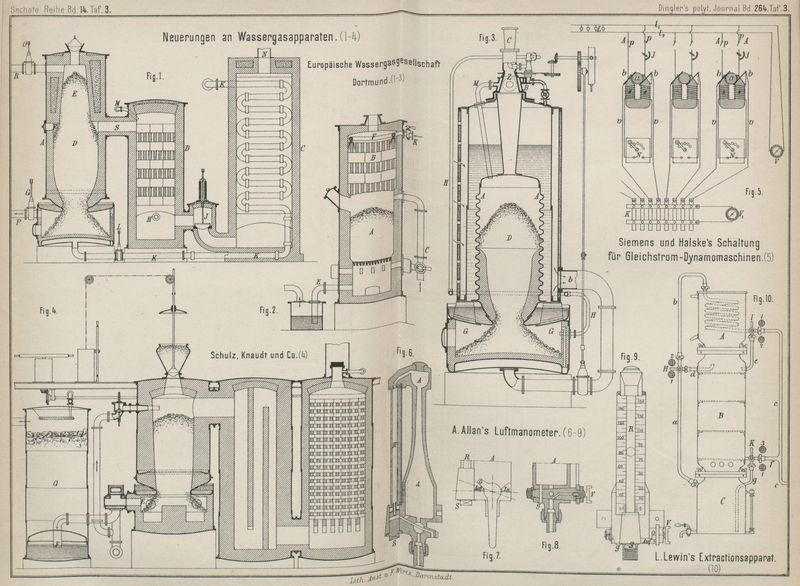