Titel: | Ueber die Herstellung des Weissbleches. |
Fundstelle: | Band 267, Jahrgang 1888, S. 481 |
Download: | XML |
Ueber die Herstellung des
Weiſsbleches.
(Schluſs des Berichtes S. 9 d. Bd.)
Mit Abbildungen auf Tafel
24.
Ueber die Herstellung des Weiſsbleches.
e) Theorie der Verzinnung.
Bevor wir zu den Versuchen zur Verbesserung des gebräuchlichen Verzinnverfahrens in
5-Kesselherden übergehen, sei es gestattet, vorher einen Blick auf die Theorie der
Verzinnung zu werfen. Zur Klärung derselben wurden vom Verfasser Bleche aus dem
Grob-, Bürst-, Durchführ- und Walzkessel entnommen; aus dem Bürstkessel:
ungebürstete und gebürstete Bleche; diese Bleche wurden auf die Beschaffenheit ihrer
Verzinnung untersucht. Dabei wurden die Bleche in 1cm,5 breite Streifen geschnitten, geebnet und dann unter bei den einzelnen
Blechstreifen relativ gleichem Druck unter einem belasteten Schabemesser
hindurchgezogen. Die hierbei entfallenden Späne wurden auf ihren Eisengehalt
analysirt. Dabei zeigte sich, daſs sich beim Verzinnen von Eisen zwischen beiden
Metallen eine Legirung bildet, daſs aber dieselbe in Folge der verhältniſsmäſsig
niedrigen Temperatur, bei welcher beide Metalle zusammentreten, eine nur ganz
oberflächliche ist und daher nur eine äuſserst geringe Stärke hat (0mm,05 mit 0,03 Proc. Eisen). Sie genügt aber, um
beide Metalle fest mit einander zu verbinden. Diese Legirung beider Metalle kann, da
eine Lösung derselben in dem Zinnbade bezieh. eine Mehraufnahme von Zinn nicht
eintritt (das Zinn eines 28 Tage in Gebrauch befindlichen Grobkessels enthielt nur
0,03 Proc. Eisen), nur so viel Eisen aufnehmen bezieh. weiter in das Eisen
eindringen, als sie flüssig ist. Erstarrt sie, was je nach der Temperatur bei einer
Aufnahme bis zu 20 Proc. Eisen stattfindet, so hört eine weitere Aufnahme von Eisen
auf. Da nun aber Späne mit mehr als 20 Proc. Eisen gefunden wurden (die von auſsen
nach innen auf einander folgenden Späne enthielten z.B. beim Grobblech 0,03, 0,03,
0,03, 0,03, 0,03, 11,30, 74,69, 97,01 Proc. Eisen), so kann nur angenommen werden,
daſs das Zinn in die Poren des Eisens eindringt und die Wände derselben mit der
Legirung überzieht, dagegen das zwischen den Poren stehende Eisen ungelöst läſst.
Demnach bildet sich beim Eintauchen einer reinen Eisenfläche in geschmolzenes Zinn
sofort eine oberflächliche Legirung, welche um so tiefer in das Eisen eindringt
bezieh. um so mehr Eisen aufnimmt, je höher die Temperatur des Zinnes ist, und auf
welcher eine reine Zinnschicht durch Kohäsion haftet. Ein Beweis hierfür ist u.a.
das Aussehen eines gebürsteten Bleches unter dem Mikroskop. Eine Schluſsfolgerung
hieraus ist, daſs die Stärke der Verzinnung von der Dauer des Eintauchens der Bleche
in das Zinnbad nicht abhängt, Wohl aber hängt die Reinheit der Verzinnung von der
Dauer des Eintauchens ab. Denn bei kurzbemessener Eintauchdauer haben die in den Poren des Eisens
sitzenden Körper (Luft, Wasser-, Säure-Dämpfe, Krätze) nicht Zeit, aus den Poren
trotz des sehr starken Auftriebes herauszutreten, damit das Zinn an ihre Stelle
tritt. In Folge dessen sehen die Bleche körnig aus. Unter dem Mikroskop bemerkt man
zahllose Erhöhungen und vulkanartige Gebilde. Reichen letztere bezieh. deren Krater
bis auf die legirte Schicht, oder sogar bis auf das Eisen, so tritt ein baldiges
Rosten des Bleches ein. Ebenso findet ein schnelles Rosten statt, wenn die unter den
Erhöhungen befindlichen bis auf das Eisen reichenden Hohlräume bloſsgelegt werden,
z.B. durch Verschleiſs der Zinndecke. Die vorerwähnten Gebilde treten aber ganz
besonders bei aus dem Bürstkessel genommenem und dann gebürstetem Blech auf, weil
durch das Bürsten jene Einschlüsse gelöst werden und dann an die Oberfläche treten,
um beim Durchführen des Bleches abgespült zu werden. Dies ist der Grund, weshalb
gebürstetes Blech immer glänzender und reiner ist als ungebürstetes. Alle Versuche
der Engländer, die so roh erscheinende Handarbeit des Bürstens, welche den
Verzinnungsprozeſs zu einem so umständlichen macht, fortzulassen oder durch eine
andere mechanische Arbeit zu ersetzen, sind bis jetzt noch fehlgeschlagen. Das
einzige Verfahren, was die Wahrscheinlichkeit eines Erfolges vielleicht für sich
hat, würde das mechanische Hin- und Herbewegen des Bleches im Zinn sein, wodurch das
Zinn selbst das Bürsten übernähme. Inwieweit dies aber
praktisch durchführbar ist, und ob das Verfahren von einem praktischen Erfolge
überhaupt begleitet ist, läſst sich bis heute noch nicht feststellen.
Bezüglich des Walzens des fertigen Weiſsbleches im Walzkessel ist zu erwähnen, daſs
dasselbe zur Regelung der Zinnstärke und zur Glättung der Zinnoberfläche dient.
Regel ist, daſs die Walzen um so dünner verzinnt bezieh. um so stärker gegen
einander gedrückt werden müssen, je schwächer der Zinnüberzug sein soll. Im Uebrigen
muſs das Blech sofort eine Temperatur unter dem Schmelzpunkt des Zinnes erhalten,
wenn es aus dem Fett des Walzkessels heraustritt. In Folge dessen muſs die
Temperatur des letzteren nur etwas höher als der
Schmelzpunkt des Zinnes liegen. Die auf jedem fertigen Weiſsblech bemerkbaren
Punktstreifen rühren von auf den Walzen sich festsetzenden Unreinigkeiten, besonders
Krätze her, weshalb für eine sorgfältige Reinhaltung der Walzen Sorge getragen
werden muſs.
f) Verbesserungen des üblichen
Verzinn-Verfahrens.
Nach diesen Auslassungen über die Theorie der Verzinnung wenden wir uns wieder zu den
Bestrebungen zur Verbesserung der 5-Kesselherde zurück. Dieselben fanden bis jetzt
nur bei den Engländern Ausdruck; aber trotzdem dieselben unendliche Anstrengungen
gemacht haben, ist es ihnen noch nicht gelungen, gute Glanzbleche anders als im
5-Kesselherd zu erzeugen. Das Handbürsten hat sich bis jetzt, wie schon früher erwähnt wurde, noch
durch keine andere Manipulation ersetzen lassen. Trotzdem läſst man es in England
vielfach fort, wenn für den Export bestimmtes minderwerthiges Blech erzeugt wird.
Die Folge hiervon war, daſs man die Zahl der Kessel in einem Herde verminderte. So findet man in England Verzinnherde mit 5, 4,
3, 2 und nur 1 Kessel.
Ein ausgezeichnetes Beispiel für 1 kesselige Herde gibt der Taylor-Leyshon-Herd (vgl. 1885 256 * 59).
Derselbe ist in England in einzelnen Hütten bis zu 20 Stück vertreten. Auch in
Deutschland ist er in einigen Hütten in wenigen Exemplaren eingeführt. Aber er macht
nur minderwerthige Bleche, welche keinen hohen Glanz haben und leicht rosten. In einem Herd können aber in 12 Stunden 35 bis 40 Kisten
530 × 380mm Weiſsblech oder 45 bis 50 Kisten
Mattblech erzeugt werden.
Eine sinnreiche Anordnung der Kessel, gewissermaſsen über einander, verdankt man den rastlosen englischen Erfindern Morewood und Rogers. Einen derartigen Herd zeigt Fig. 1 Taf. 24.
Derselbe enthält vor allem den „Fetttrichter“
F. (Eine besonders charakteristische Gestalt hat
derselbe in Fig.
2 bei „h“.) Letzterer gestattet, an
der Stelle, wo die Bleche in den Zinnkessel eintreten, eine hohe Fettschicht zu
erhalten, während die Höhe der Fettschicht an den übrigen Stellen der Zinnoberfläche
das gewöhnliche Maſs nicht zu übersteigen braucht; da das specifische Gewicht des
Zinnes zu dem des Fettes sich ungefähr wie 8 : 1 verhält, so kann die im Trichter
befindliche Fettsäule ungefähr 8mal höher sein, als die auſserhalb des Trichters
stehende Zinnschicht, vermehrt um die niedrige, lediglich die Oxydation verhindernde
Fettschicht, ohne daſs ein Austreten des Fettes unter den Rand der Wand K des Trichters zu befürchten wäre. Gleichzeitig hält
man dadurch das schaumige, unreine Fett der Eintrittsstelle von dem der
Austrittsstelle fern. Da an letzterer die Fettschicht gewöhnlich nur eine geringe
Höhe hat, so kann man hier die Zinnasche leichter entfernen. Das im Trichter
befindliche Fett wird durch die Berührung mit dem Metallbade an der unteren Oeffnung
des Kastens F flüssig erhalten. Je groſser die Oeffnung
ist, um so schneller findet die Temperaturausgleichung zwischen Fett und Zinn statt.
Der Weg, welchen das Blech beim Durchgang durch den Fetttrichter zurücklegt, ist so
lang, daſs man bei manchen Apparaten den Fettkessel als überflüssig ganz fortläſst.
Die Durchgangsdauer kann durch die Anordnung von Walzen v geregelt werden.
Im Uebrigen besitzt der Herd Fig. 1 einen geheizten
Fettkessel, welcher aber bei gröſserer Höhe von F auch
fortbleiben kann, und daneben den Zinnkessel. Die Feuerungen sind wie gewöhnlich
einrichtet. Der Zinnkessel hat im oberen Theil eine Scheidewand K, welche etwa 2 bis 3cm in das Zinnbad eintaucht und den oberen mit Fett gefüllten Kesseltheil
in 2 Räume scheidet. Der rechts der Scheidewand K
gelegene Theil dient als Fetttrichter; das unreinere Fett desselben steht mit dem reinen Fett des
linken Raumes nicht in Verbindung. Am Fetttrichter ist ein zum Fettkessel führender
Ueberlauf l, und im Zinnkessel sind ein Paar Walzen v und eine Hebevorrichtung cf angeordnet. Die Tröge T tauchen mit ihren
unteren Enden etwas in das Zinn ein, sind im Uebrigen aber bis zum Rande von Fett
umgeben. Die Arbeit geht in der Weise vor sich, daſs die im Fettkessel getrockneten
und vorgewärmten Bleche einzeln zwischen die ganz im Fett liegenden Walzen v eingesteckt werden, diese führen sie nach unten und
lassen sie endlich in das Zinnbad auf die Arme c
fallen. Nunmehr drückt man den Hebel f nach unten,
wirft dadurch das auf c stehende Blech auf die andere
Seite gegen die Führungen a und hebt es zwischen die
Trogwalzen. Zwischen diesen findet das Abquetschen des überschüssigen Zinnes und das
Ueberziehen mit reinem Zinn, mit welchem die Tröge gefüllt sind, statt. Behufs
Reinhaltung der zwischen den Trögen befindlichen Zinnoberfläche ordnet man an den
Kopfwänden des Kessels kleine Vorherde z an, durch die
man die Krätze mittels einer gebogenen Krücke abzieht. Fetttrichter und Trogwalzen
der angegebenen Art findet man bei den meisten Herden mit weniger als 5 Kesseln und
auch bei den Verzinnmaschinen. Unter letzteren versteht man Verzinnherde, bei
welchen das Blech nicht auf und ab gehend durch das Zinn geführt wird, sondern in
mehr horizontaler Richtung von Transportwalzen durch das Zinn gezogen wird. Die
ebenfalls von Morewood und Rogers gemachte Erfindung
datirt aus dem Jahre 1843 und ist seitdem erheblich ausgebildet worden.
Ein neuerer Herd dieser Art ist in Fig. 2 Taf. 24 abgebildet.
Er enthält Fett-, Grob-, Durchführ- und Walzkessel in einem einzigen Kessel
vereinigt. Der bis 2m lange und 1m breite Kessel ist durch einen Kanal a in 2 Hauptabtheilungen geschieden, die in Folge der
unter a angeordneten Einbiegung des Kesselbodens durch
eine nur enge Oeffnung in Verbindung stehen. Beide Abtheilungen haben besondere
Feuerungen, deren beide Feuerthüren auf einer Langseite des Kessels liegen. Der Zug
jeder Feuerung geht einmal quer unter dem Boden, dann ein kurzes Stück an der
Längswand hin und kehrt quer unter dem Boden wieder zurück, um in die Esse zu
entweichen. Die Feuerung rechts wird aber nur beim Inbetriebsetzen des Herdes
benutzt. Ist das Zinn im Kessel durch beide Feuerungen auf die erforderliche
Temperatur gebracht, so benutzt man nur die linke Feuerung, so daſs dann der linke
Kesseltheil auf einer höheren Temperatur erhalten wird, als der rechte. Zur Regelung
der Hitze dienen die Kanäle a und b, durch welche man eben so wohl wie durch die rechte
Feuerung nach Bedarf kalte Luft strömen läſst. In dem Kessel sind 3 Paar Lagerböcke
c, d, e eingesetzt, welche die gleich groſsen und
mit gleicher Geschwindigkeit angetriebenen 5 Walzenpaare aufnehmen. Zur Führung der
Bleche von einem Walzenpaar zum anderen dienen die an den Lagerböcken angegossenen Rippen r. Die Einstellung der Walzen geschieht durch
Schrauben, der Antrieb durch die Zahnräder s, t unter
Einschaltung von Zwischenrädern passender Gröſse. Der Fetttrichter h, dessen untere Oeffnung, um eine zu hohe Erhitzung
des Inhaltes zu vermeiden, nur schmal ist, ist mit einem Gemisch von Harz (67
G.-Th.), Talg (23 G.-Th.) und Palmfett (10 G.-Th.) gefüllt. In dem Trichter sind 3
feste Führungen angeordnet, zwischen denen je 2 um o
drehbare federnde Führungen p liegen. Zwischen diesen
und den festen Führungen wird je ein Blech eingesetzt und werden diese in bestimmter
Reihenfolge nach einander dadurch in das Zinnbad hinabgelassen, daſs man die
betreffenden Führungen etwas zur Seite drückt, so daſs die unteren Enden derselben
den Mund des Trichters freigeben. Die leere Abtheilung wird dann sofort wieder mit
einem neuen Blech besetzt. Die Bleche bleiben bei diesem Verfahren längere Zeit in
dem heiſsen Fett und haben so Gelegenheit zu trocknen und vorgewärmt zu werden. Der
mit Fett gefüllte Walzkessel f enthält 3 Paar Walzen,
von denen das oberste Paar in Trögen mit reinstem Zinn gelagert ist. Die Einstellung
der Trogwalzen erfolgt durch Federhebel, die der unteren Walzen durch
gemeinschaftliche Federn t, welche durch Schrauben g direkt angespannt werden. Die Walzen werden durch
Zahn- oder Schneckenräder umgedreht. In letzterem Falle haben die linken Walzen
Schneckenräder, in welche eine gemeinschaftliche, senkrecht stehende Schneckenwelle
eingreift. Bei allen Walzen liegen die Zahnräder auſserhalb der Lagerböcke, und zwar
die Räder, welche ein Walzenpaar unter sich treiben, auf der einen, die übrigen
Räder auf der anderen Seite. Fällt aus dem Fetttrichter h ein Blech zwischen die obersten Walzen, oder wird dasselbe durch ein
darauf gesetztes Blech zwischen dieselben gestoſsen, so fassen diese es und führen
es weiter durch das Metall hindurch, welches im Hauptkessel bis über die obersten
Walzen steht, so daſs diese frei von Krätze bleiben. In dem linken hocherhitzten
Kesseltheil (welcher dem Grobkessel entspricht) überziehen sich die Bleche mit
Metall und gelangen dann in den nicht so heiſsen rechten Raum, welcher bezüglich der
Temperatur dem Durchführkessel entspricht. Dem Bleche auf der oberen Seite etwa
anhaftende Aschetheilchen können hier nach oben steigen und werden durch die
schrägen Flächen des Kanales b vom Eintritt in den
Walzkessel f abgehalten. Die Temperatur in letzterem
ist am niedrigsten und entspricht der des Walzkessels der gewöhnlichen Verzinnherde.
Im Walzkessel wird durch die 4 unteren Walzen der Ueberzug geregelt und dann dem
Blech durch die beiden obersten Walzen eine glänzende Verzinnung gegeben. Bei dieser
Maschine fehlt aber das Bürsten und sie kann deshalb nur minderwerthige Bleche
geben. Zur Herstellung von Mattblech wird sie aber in England vielfach verwandt.
Eine neueste Verzinnmaschine ist diejenige der Duffryn-Werke bei Swansea (Fig.
3 und 4 Taf. 24, vgl. auch * D. R. P. Kl. 7 Nr. 38158 vom 18. März 1886 von D. Edwards, E. Lewis und Ph. Jones in Duffryn Iron and
Tin Plate Works bei Swansea). Der obere Theil des Zinnkessels ist durch eine
Scheidewand a in 2 Abtheilungen geschieden. In der
linken ist ein Fetttrichter b mit 4 Paar Glättwalzen
angeordnet. Um das darin befindliche Fett leicht höher erhitzen oder abkühlen zu
können, steht der um 3 Seiten des Trichters geführte Zug c durch eine Wechselklappe (bei d) sowohl mit
der Hauptfeuerung als auch mit einer nach auſsen führenden Oeffnung in Verbindung,
so daſs der Fetttrichter entweder von heiſsen Gasen oder kalter Luft umzogen wird.
Die Detaileinrichtung des Walzenkessels ist aus den Skizzen zu ersehen. An der
unteren Seite desselben ist eine schräge Wand e
befestigt, welche bis auf den Boden des Kessels reicht. In der rechten Abtheilung
sind an der Stange f 2 senkrechte Wände g derart aufgehängt, daſs sie mit ihren horizontalen
Flanschen auf den Rändern des Kessels aufliegen. Auf den einander zugekehrten
Flächen der Wände g sind gebogene Führungsrippen h angeordnet, deren Zwischenräume sich nach links
verjüngen und nahezu in die Richtung der schrägen Wand e bezieh. der Walzenmittellinie auslaufen. Der Kessel wird bis etwas über
(das unterste Walzenpaar mit Zinn, im Uebrigen aber mit Palmfett gefüllt. Hat das
Bad die erforderliche Temperatur, so steckt man ein Blech zwischen die vordersten
Führungsrippen h der Wände g und stöſst es mit der Zange bis an die Wand e vor. Das Blech liegt dann ganz im Zinn. In derselben Weise füllt man die
übrigen Führungen h mit im Ganzen 7 Blechen. Ist dies
geschehen, so stöſst man das erste Blech vor, bis seine linke Kante, von der
schrägen Wand e geführt, zwischen die untersten
Glättwalzen gelangt und von diesen erfaſst wird. Während dieses Blech durchgewalzt
wird, setzt man ein neues Blech an die leere Stelle und stöſst dann das zweite Blech
zwischen die Walzen u.s.f. Der ununterbrochene Betrieb ist also gewahrt und trotzdem
ein längerer Aufenthalt der Bleche im Zinnbade erreicht. Behufs Verzinnung schmaler
Bleche verstellt man die Wände g nach innen. Ob sich
die Maschine praktisch bewährt, ist noch nicht näher bekannt geworden.
Es erübrigt nun noch die Erwähnung der Massen-Verzinn-Maschinen. Dieselben bezwecken
die gleichzeitige Verzinnung einer groſsen Masse Bleche, die dann in irgend welchen
anderen Herden ohne Fett-, Grob-, Bürst- und Durchführkessel, die also nur einen
Walzkessel besitzen, weiter behandelt bezieh. fertig gestellt werden können.
Das interessanteste Beispiel dieser Art ist die Maschine von Madge und Jenkins (Englisches Patent Nr. 954 vom Jahre 1871). Die Maschine
Fig. 5 und
6 Taf. 24
hat einen halbkreisförmigen Zinnkessel, bestehend aus einem äuſseren Halbkreismantel
a, den beiden flachen Seiten b und dem inneren Halbkreismantel c, in welchem sich um eine horizontale Mittellinie eine
Trommel d dreht. Dieselbe wird aus 2 Ringscheiben gebildet, die durch
Bolzen e mit einander verbunden sind. Die Trommel wird
von Rollen f geführt und von der Schnecke g, welche in eine Kronenverzahnung der Trommel
eingreift, angetrieben. In den beiden Wänden der Trommel d sind Ausschnitte h mit gezahnten Rändern
angeordnet, in welche die Bleche, während sich die betreffenden Ausschnitte
auſserhalb des Zinnbades befinden, von der Seite eingeschoben werden. Die Bleche
verbleiben bei der ununterbrochenen Umdrehung der Trommel eine bestimmte, von der
Schnelligkeit der Umdrehung abhängende Zeit im Zinnbade und werden beim Verlassen
des Bades von der Seite herausgenommen. Die Kanäle i
sind zur Einführung von Zinnbarren in das Bad bestimmt. Auch über diese Maschine
sind praktische Ergebnisse nicht zu erlangen gewesen.
Nochmals muſs aber hier hervorgehoben werden, daſs mit allen diesen Apparaten und
Maschinen Glanzbleche nicht erzeugt werden können. Sie sind in England allerdings
stellenweise in Gebrauch, aber fast nur zur Erzeugung von minderwerthigen
Exportblechen. Gute Glanzbleche werden immer in dem alten 5-Kesselherd erzeugt.
g) Das Putzen des Weiſsbleches.
Da die Bleche beim Verzinnen mit Fett in Berührung kommen, so sind sie nach der
Verzinnung ausnahmslos mit Fett überzogen, welches bei Glanzblechen möglichst
beseitigt werden muſs. Hierzu benutzt man Kleie, Kalk oder Sägemehl, in welche die
Bleche noch warm wiederholt eingesteckt werden, so daſs alle Punkte des Bleches
damit in Berührung kommen. Die genannten Stoffe saugen das in Folge der Wärme der
Bleche noch flüssige Fett auf; sind die Stoffe vollgesogen. so sind sie verbraucht
und müssen durch frische Stoffe ersetzt werden. Von denselben empfiehlt sich am
meisten die Kleie, weil sie am wenigsten nachtheilig für die Gesundheit der Arbeiter
ist und weil sich die verbrauchte Kleie als Viehfutter wohl verwenden läſst,
wenigstens bekommt den Schweinen das in der Kleie enthaltene Palmfett ganz gut. Ganz
zu verwerfen ist das Putzen mit zu Pulver gelöschtem Kalk wegen des starken Staubes,
welchen derselbe verursacht und die Athmungs- und Sehorgane der Arbeiter ganz
erheblich angreift. Obschon dieser schädliche Einfluſs auch den anderen Stoffen
innewohnt, so ist doch der Grad der Schädlichkeit ein bedeutend geringerer, wenn sie
auch immer noch vorhanden ist.
In England ist man schon seit Langem bestrebt gewesen, die Handarbeit durch Maschinen
zu ersetzen, bis jetzt aber noch ohne Erfolg. Zwar wird jedes Jahr von einer oder
der anderen englischen Maschinenfabrik behauptet, sie habe eine praktische
Weiſsblech-Putzmaschine erfunden, bis jetzt hat sich aber noch immer erwiesen, daſs
dies nicht der Fall war. In englischen Patenten sind viele Maschinen bereits
beschrieben; da sie in Deutschland noch gar nicht bekannt sind, so möge hier die kurze Beschreibung
einiger derselben folgen. Die meisten Maschinen besitzen Förderwalzen, welche die
Bleche den Putzorganen zuführen bezieh. sie aus denselben heraus befördern. Die
Walzen bestehen aus Holz oder Eisen und sind mit irgend einem weichen Stoff, Leder,
Filz, Kautschuk, überzogen, um die Bleche nicht zu beschädigen und um dieselben
leichter und fester fassen zu können. Als Putzorgane dienen feststehende Bürsten,
rotirende Bürsten walzen und gegen einander bewegte Flächen, welchen das
Putzmaterial, Kleie, auf irgend eine Weise zugeführt wird, oder genuthete Walzen,
welche in dem Putzmaterial rotiren und dabei letzteres in den Nuthen mitnehmen und
gegen die Bleche drücken. Einige, und zwar die besseren Maschinen besitzen besondere
Putzorgane überhaupt nicht und ahmen dann die Handarbeit nach, indem sie die Bleche
durch das Putzmaterial, welches ruht oder eine rüttelnde Bewegung macht, wie bei der
Handarbeit hindurchführen. Die Anwendung von Bürsten irgend welcher Form und von
gegen einander reibenden Flächen (Filz, Schaffell, Leder u.s.w.) zum Putzen in
Maschinen ist aber ganz zu verwerfen. Ihre Wirkung nimmt in demselben Maſse ab, wie
die Räume zwischen den Borsten, Haaren und die Poren sich mit Fett und Kleie
verstopfen – verschmieren. Ist dies aber eingetreten, so hört jede putzende Wirkung
auf. Die beste aller Maschinen ist die in Fig. 7 Taf. 24 skizzirte
(vgl. Englisches Patent Nr. 4264 vom Jahre 1877). Sie besitzt einen zwischen 2
Förderwalzenpaaren a durch eine Kurbel Vorrichtung
geradlinig hin und her geschobenen Kleienkasten b mit
Schlitzen an den Längsseiten. Die Länge derselben muſs gleich der Breite des Bleches
sein, vermehrt um die Länge des vom Kasten zurückgelegten Weges. Die Bleche werden
von den Förderwalzen durch die Kleie hindurchgeführt, während diese sich mit dem
Kasten hin und her bewegt. Dadurch, daſs man die Drehgeschwindigkeit der Walzen oder
die der Kurbel ändert, kann man die Länge des von den Blechen in der Kleie
zurückgelegten Weges beliebig ändern. Die Kleie drückt auf die Bleche von oben in
Folge ihrer Schwere, und von unten in Folge der lebendigen Kraft, welche die Kleie
bei der Umkehr der Bewegung des Kastens nach allen Seiten, also auch von unten nach
oben, zusammendrückt. Dabei findet, während kein Blech durch den Kasten geht, ein
Durcheinanderrütteln der Kleie statt, so daſs die ganz Masse der Kleie gleichmäſsig
verbraucht wird und immer wieder neue Kleietheilchen mit den Blechen in Berührung
kommen. Sollte es sich herausstellen, daſs die Bleche schon zu kalt sind, ehe sie
mit der Kleie in Berührung kommen, so könnte man vielleicht die Kleie durch
eingelegte Dampfschlangen erwärmen. Die Bewegung des Kastens geschieht am besten
ruckweise. Es lohnte sich der Mühe mit der Maschine, die in Deutschland nicht
patentirt ist, hier Versuche zu machen. Bei der Einfachheit des Gegenstandes können
dieselben viel Geld nicht kosten.
h) Allgemeines.
Zuweilen wird das fertige Weiſsblech zwischen Hartguſswalzen kalt einmal
durchgewalzt, um ihm eine besonders glänzende Oberfläche zu geben. Es geschieht dies
besonders bei Blechen, welche nachher mit Nickel, Messing, Bronze auf galvanischem
Wege überzogen werden.
Das Verpacken der Bleche geschieht in Weidenholzkisten. Eisenblechkisten haben sich
in England nicht bewährt. Die Holzkisten erhalten die Bezeichnung der Bleche
aufgebrannt. Für letztere sind der Ursprung der Schwarzbleche, die Zusammensetzung,
das Aeuſsere, die Stärke der Verzinnung und die Stärke und Gröſse der Bleche
maſsgebend. Die Zeichen, welche in den einzelnen Ländern üblich sind, sind aber so
verschieden, daſs es ganz unmöglich ist, allgemein gültige Grundsätze für die
Klassificirung aufzustellen. Die beste Bezeichnung scheint diejenige zu sein, welche
die Widerstandsfähigkeit der Bleche gegen gewisse Bearbeitungsverfahren (Umbiegen,
Falzen, Stanzen, Pressen, Ziehpressen), die Stärke und das Aussehen der Verzinnung
enthält. Die ersten Vorschläge in dieser Richtung sind von den Amerikanern
ausgegangen. Ob die von Stercken vorgeschlagenen
Verbesserungen der Vorschläge sich in dem internationalen Verkehr einbürgern, muſs
abgewartet werden. Nach Lage der Sache scheint wenig Aussicht dazu vorhanden zu
sein.
Die Erzeugungskosten des Weiſsbleches sind in Oesterreich und Frankreich höher als in
Deutschland, in letzterem aber höher als in England. Letzteres ist eben durch die
kolossale Massenfabrikation minderwerthigen Bleches im Vortheil, der sogar die um 25
Proc. höheren Arbeitslöhne mehr wie aufwiegt. Denn der Verkaufspreis des deutschen
Bleches ist um 20 Proc. höher als derjenige des englischen Bleches.
Ueber die Verwendung des Weiſsbleches ist, weil sie allgemein bekannt ist, nichts
weiter zu sagen. Daſs aber dieselbe in Amerika um so viel gröſser ist als in Europa,
hat darin seinen Grund, daſs drüben ganz kolossale Mengen Weiſsblechgeschirre für
die Einwanderer, für die groſsen Fleisch-, Pflanzen- und Frucht-Conservefabriken,
für die Petroleum-Industrie und zum Eindecken von Dächern verwandt werden. Dieser
Verbrauch wird in Europa und auch in keinem anderen Lande jemals erreicht werden,
wenn er auch hier zu Lande fortwährend steigt.
In England waren im J. 1750 4 und im J. 1880 106 Weiſsblechwerke mit 400 Walzwerken
vorhanden. Dieselben haben in den letzten Jahren eine solche Ueberproduction
bewirkt, daſs der englische Weiſsblechmarkt augenblicklich schwer daniederliegt. In
Amerika ist, trotzdem es der gröſste Verbraucher von Weiſsblech ist, bis jetzt noch
keine Weiſsblechindustrie vorhanden- es ist dies die Folge des niedrigen
Eingangszolles, gegen welchen die hohen Arbeitslöhne nicht ankommen können.
Deutschland hat 5, Oesterreich 8 und Frankreich 14 Weiſsblechfabriken. Ganz neuerdings ist auch in
Ruſsland (Warschau) eine Weiſsblechfabrik gegründet worden.
Es betrugen
die Production
Ausfuhr und
Einfuhr
im J. 1885
in t à 1000k
in t à 1000k
in t à 1000k
in Deutschland
13258
186
5989
in England
417450
297728
–
in Oesterreich
3510
?
?
in Frankreich
17280
?
?
Die Zukunft der deutschen Weiſsblechindustrie ist im Hinblick auf das ausgezeichnete
Material, welches die deutschen Fabriken im basischen Fluſseisen besitzen und auf
die verhältniſsmäſsig billigen Arbeitslöhne, eine hoffnungsreiche, wenn es gelingt,
die deutschen Eisenbahnen zu einer Frachtermäſsigung zu bewegen. Dieselbe müſste von
den Productionsorten (Letmathe, Arnsberg, Neuwied, Dillingen, Hayingen) bis zu
denjenigen an schiffbaren Flüssen gelegenen Orten und bis zu deutschen Hafenplätzen
eintreten, in welchen das deutsche Blech in Folge des jetzt erforderlichen
Eisenbahnfrachtzuschlages mit dem englischen Fabrikat nicht mehr concurriren kann.
Hierdurch würde es möglich sein, das englische Blech gänzlich vom deutschen Markt zu
verdrängen und die heimische Industrie direkt zu heben. Ob diese dann im Stande ist,
auf dem Weltmarkte neben England aufzutreten, hängt von der weiteren Entwickelung
der Industrie in beiden Ländern und auch in Amerika ab.
Tafeln
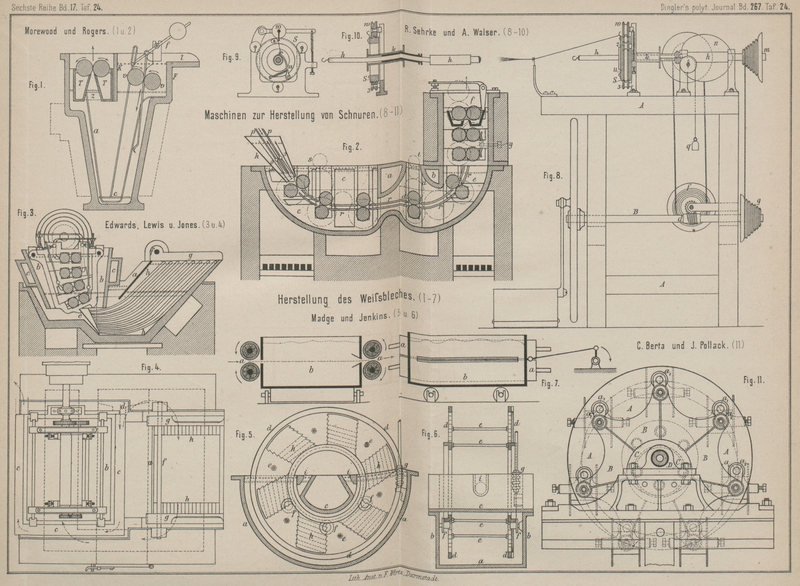