Titel: | Neuerungen im Eisenhüttenwesen. |
Autor: | W. Koort |
Fundstelle: | Band 272, Jahrgang 1889, S. 61 |
Download: | XML |
Neuerungen im Eisenhüttenwesen.
Mit Abbildung auf Tafel
4.
Neuerungen im Eisenhüttenwesen.
Der Martin-Prozeſs.
Während in der älteren Literatur meist von einem Siemens-Martin-Prozeſs die Rede ist, unterscheidet man jetzt streng
zwischen Siemens-Prozeſs und Martin-Prozeſs. Bei dem letzteren werden bekanntlich Schrot und Abfälle in
einem Roheisenbade gelöst, wohingegen Siemens Erze zum
Roheisen setzt und somit durch Eisenoxyde eine Oxydation des Roheisenbades bewirkt.
Der Siemens-Prozeſs oder die Herstellung von Siemens-Fluſseisen ist daher gleichbedeutend mit der
sogen. Erzstahlarbeit (vgl. Wedding, Schmiedbares Eisen
S. 492). Werden aber die Erze zunächst durch irgend eine Rennarbeit reducirt und der
erhaltene Eisenschwamm anstatt der Eisenoxyde zum Roheisen gesetzt, so ist dies der
sogen. Eisenschwammprozeſs (vgl. Wedding, Schmiedbares
Eisen S. 565). Letzterer ist von keiner wesentlichen Bedeutung, da es unnöthig
erscheint, die Erze zunächst zu reduciren, während man nach dem Vorgange von Siemens die Oxyde direct dem Roheisenbade zusetzen
kann.
Der Siemens-Prozeſs und der Martin-Prozeſs bilden den sogen. Flammofenfluſseisenprozeſs, sowie das Martin-Fluſseisen und Siemens-Fluſseisen den gemeinschaftlichen Namen Flammofenfluſseisen
führen. Kürzer bezeichnet man den Prozeſs als Herdschmelzprozeſs, indem man sich an
die englische Bezeichnung Open-hearth-process
anschlieſst und auch zuweilen von einem offenen Herde redet, obwohl eigentlich kein
offener Herd angewendet wird.
Der Herdschmelzprozeſs, namentlich der basische, scheint der Prozeſs der Zukunft zu
werden. In Stahl und Eisen 1887 Heft 6 findet sich ein
interessanter Entwurf einer neuen Martin-Stahlanlage
von Steffen. Nunmehr liegt ein Parallel-Entwurf vor,
welcher von W. Schmidhammer ausgearbeitet und in Stahl und Eisen 1888 S. 369 mitgetheilt ist.
Zur Entgasung der Kohle, welche mittels des Fülltrichters F (Fig.
4) aufgegeben wird, dient der Entgasungsraum E, der gleich senkrechten Verkokungskammern aus Façonsteinen errichtet
wird, die mit einer zweiten Gattung von Façonsteinen zugleich die Heizkanäle H bilden. Letztere münden in einen ringförmigen Raum
R, aus welchem eine Rohrleitung zur Düse G und in den unter dem Entgasungsraum befindlichen
Vergasungsraum V führt. Dieser letztere ist gegen den
Entgasungsraum bedeutend erweitert und wird durch einen Kühlkasten K von demselben getrennt; dieser Kühlkasten trägt
einestheils, indem er auf Flantschen der winkelförmigen Säulen S aufsitzt, das ganze obere Mauerwerk, dadurch den
unteren Theil entlastend, anderntheils dient er zugleich zu einer mäſsigen Erhitzung
des Windes; zu diesem Zweck wird der Wind durch die Leitung W zugeführt und durch die Rohre w und w1 abgeleitet; w führt zu den Düsen D,
von welchen auf jeder Seite der Düse G eine angeordnet
ist, und liefert den Wind zur Vergasung der Kohle. Die Leitung w1 führt zu den
injectorartig geformten Brennern i, welche die
Destillationsproducte aus der Entgasungskammer E
absaugen und zur Verbrennung bringen. Die gebildeten heiſsen Verbrennungsproducte
gelangen durch den Kanal R zur Düse G und zwischen den Winddüsen D in die glühende Kohle, wo sie zu Kohlenoxyd und Wasserstoff reducirt
werden sollen. Die Gase des Gaserzeugers werden durch das flache Rohr L in einen Reinigungskasten und von da durch das
Absperrventil mit Wasserverschluſs A in den
Gassammelkasten und zur Verbrauchsstelle geführt.
Zur Inbetriebsetzung des Gaserzeugers ist es vorerst nöthig, die Entgasungskammer
heiſs zu bekommen. Zu dem Zweck wird erst in dem Vergasungsraum V Feuer gemacht und bei geschlossenem Ventil A das Mauerwerk incl. des Entgasungsraumes soweit
heiſsgeblasen, als es mit Rücksicht auf den nur durch Wind gekühlten Kühlkasten
angeht; dabei läſst man die Verbrennungsproducte durch die offenen Putzlöcher P des Ringkanals R
entweichen. Kommen bei höherer Kohlenschüttung schon unverbrannte Gase zu den
Brennern i, so können sie, wenn die Brenner schon etwas
warm sind, mit Wind verbrannt werden, bis die Heizkanäle H in guter
Hitze sind. Ist dies bei allmählicher Anfüllung des Entgasungsraumes erreicht, so
können sofort das Ventil A geöffnet und die Putzlöcher
geschlossen werden, und der Apparat ist in voller Thätigkeit. Sollten Festsetzungen
der Kohle trotz der nach unten erweiterten Form des Entgasungsraumes vorkommen, so
können diese mit Hilfe von Stangen durch die an den kurzen Seiten des Füllkastens
angebrachten Löcher behoben werden.
Von den Gaserzeugern gelangen die Gase in die Wärmespeicher (Fig. 1 und 2). Zur Regulirung für die
zuströmenden Gase und die Luft dienen einfache Tellerventile. Die Umschaltung beim
Regenerativofen erfolgt ebenfalls mit Ventilen, die aber mit Wasser gekühlt sind;
die Ventilkästen sind, wenn nöthig, ausgemauert und reichlich mit Putzöffnungen
versehen. Durch einen Kettentrieb werden sämmtliche acht Ventile, die zur
Umschaltung nöthig sind, von einem Handrad aus mit einem Male gestellt. Alle Ventile
sind mit Zeigern in Verbindung, die ihre Stellung genau angeben. Bei den
Regulirventilen sind die Ständer der Stellräder überdies mit den Ventilsitzen in
starrer Verbindung, damit die Einstellung des Ventils immer genau erfolgen kann.
Sämmtliche Ventile sind leicht und rasch auswechselbar. Von den Umschaltungsventilen
führen geräumige Kanäle, welche als liegende Wärmespeicher dienen und daher mit
einem Ziegelgitter ausgefüllt sind, unter die senkrechten, in Blechcylindern von
2m Durchmesser eingebauten freistehenden
Wärmespeicher. Diese sind am Umfang auf 300mm
ausgemauert (Fig.
2a); die Ausfüllung ruht auf einem gewölbartig hergestellten Gitter von
Chamottesteinen und besteht aus Façonsteinen, welche senkrecht durchgehende, runde
Schächtchen von 135mm Durchmesser bilden; diese
sind überdies durch enge quadratische, horizontale Kanälchen untereinander in
Verbindung, welche in ihrer Uebereinanderfolge senkrechte quadratische Schächtchen
von 50mm Seitenlänge bilden. Diese Ausfüllung
besteht aus einer einzigen Gattung von Façonsteinen und ist unverrückbar, da die
Steine mit Vorsprüngen ineinandergreifen. Der Uebergang von dem liegenden in den
stehenden Wärmespeicher wird durch einen 1m hohen
leeren Raum gebildet, der den Gasen und der Luft bezieh. den Verbrennungsproducten
Gelegenheit bietet, sich zu sammeln und über den ganzen Querschnitt des zu
durchstreichenden Wärmespeichers gleichmäſsig zu verbreiten. Die senkrechten
Wärmespeicher sind oben durch einen ausgemauerten Blechconus abgeschlossen, der am
abgestutzten Ende sich in das zum Brenner führende Rohr fortsetzt. Die wagerechten
Wärmespeicher sind oben mit Chamotteplatten gedeckt, die auf den die Schlichtung
bildenden Längsmauern ruhen. Darüber kommen Eisenplatten und zum Schutz gegen zu
groſse Ausstrahlung eine Sandschicht. So sind sie am besten von oben zugänglich.
Die Heizfläche eines senkrechten Wärmespeichers beträgt 67qm, die des wagerechten für Gas 69, der Luft 138qm, so daſs für die Gase in Summa 136, für die
Luft 205qm Heizfläche vorhanden sind, was
jedenfalls reichlich bemessen und für lange Umsteuerungsperioden geeignet ist. Die
Anordnung wagerechter Wärmespeicher neben den senkrechten ermöglicht eine
entsprechende Vergröſserung der Heizfläche und hat den Vortheil, die nicht zu
umgehenden groſsen Kanalräume, welche bei jedem Umsteuern einen bestimmten
Gasverlust bedingen, wenigstens für die Wärmeausnützung in geeigneter Weise
heranzuziehen.
Von den Wärmespeichern führen je zwei gekrümmte Rohre in gleicher Höhe zu den
Brennern, welche in der Hauptsache aus einem 1,4m
weiten wagerechten Blechstutzen bestehen, der durch eine wassergekühlte Scheidewand
in zwei Theile getheilt wird. Auſsen- und Scheidewand sind mit feuerfestem Material
bekleidet. Die Scheidewand ist so windschief gewunden, daſs Gase und Luft von rechts
und links eintreten, das Gas aber unter der Luft in den Ofen gelangt. Der ganze
Brenner ist mit dem Wärmespeicher und dem Ofen nur in losem Contact und ruht in
einem Lager, das mit Hilfe eines Handrades und Excenters um etwa 40mm vom Ofen weggerückt werden kann, sobald
derselbe gedreht werden soll. In Folge dieser losen Anordnung können die Brenner
auch ohne Umstände mit Hilfe von Erahnen abgehoben, durch neue ersetzt und in Muſse
ausgebessert werden. Der Ofen selbst besteht aus einem mit zwei conischen Ansätzen
versehenen Blechcylinder von 3m Durchmesser und
5,4m Gesammtlänge (Fig. 1 und 2). Der cylindrische
Mitteltheil ist 3,5m lang und an seinen zwei Enden
mit kräftigen Winkelringen versehen. Mit diesen Ringen ruht der Ofen auf vier
kräftigen, solide gelagerten Rollen, die alle vier zu gleicher Zeit von einer
Transmission aus mittels Schneckengetrieben gedreht werden können und welche auf
diese Art den Ofen auch drehen.
Die Blechumhüllung, die überdies mit T-Eisen versteift ist, wird auf 300mm Stärke ausgemauert und zwar mit gut gebrannten
Magnesitziegeln (Dingler 266 S. 258). An den conischen
Enden befinden sich die Oeffnungen für die Gas- und Lufteinströmung mit einem
Durchmesser von 750mm, ferner an einer Seite zwei
runde Thüröffnungen von 800mm Durchmesser und auf
der anderen Seite in der Mitte eine thürähnliche Oeffnung von 350mm Weite zum Entleeren des Stahles. Der Boden ist
über die Magnesitausmauerung von Dolomit aufgestampft. Die eigenthümliche Form des
Ofens ist eine Folge der Absicht, denselben drehbar einzurichten. Das Drehen des
Ofens soll folgende Vortheile bieten: Da die Beschickung durch Drehen des Ofens
entleert werden kann, entfällt jede Arbeit am Stichloch, es kann daher auch nicht
durch Versagen des Stichloches eine Störung eintreten; ferner, und das ist die
Hauptsache, läſst sich der Boden am besten erhalten. Am verderblichsten für den
Boden sind die kleinen Reste von Metall und Schlacke, welche in den Grübchen des
Bodens immer zurückbleiben; diese fressen sich immer mehr ein; und wenn die Grübchen
auch mit neuer Bodenmasse ausgefüllt und ausgebessert werden, so bleibt doch
unterhalb immer etwas Stahl oder Schlacke. Läſst sich der Boden soweit neigen, daſs
Metall und Schlacke abflieſsen können, so ist der basische Boden von unbegrenzter
Dauer. Ferner ist der ganze Ofen leicht auswechselbar. Dazu ist nur ein kräftiger
Wagen nöthig, auf dem vier hydraulische Hebevorrichtungen stehen, deren Plunger von
Hand aus durch kleine Pumpen gehoben werden kann. Zwei Plunger tragen je einen
Träger, welche den Ofen aufnehmen.
Die Eisenconstruction des Ofens, der für 12 bis 15t
Beschickung berechnet ist, wiegt etwa 6000k und
die Ausmauerung noch 12000k. Wenn die vier Plunger
je einen Durchmesser von 250mm haben, die kleinen
Pumpenpistons 20mm und 110mm Hub, so können bei einer Hebelübersetzung von 1
: 5 vier Mann leicht den ganzen Ofen um 250mm in
13 Minuten heben. Mit Hilfe einer Locomotive oder des fahrbaren Guſskrahns wird das
Ganze zur Reparaturstätte gefahren. Daneben ist eine Feuerung anzuordnen behufs
Vorwärmung des Reserveofens, indem derselbe zwischen die Feuerbrücke und die
Fuchsöffnung eingeschaltet wird. Dieser Reserveofen wird mit demselben Wagen in
ähnlicher Weise von der Feuerung weg und zwischen die Brenner gefahren und mit den
hydraulischen Hebevorrichtungen in die Lagerrollen eingesenkt.
Die Arbeit beim Ofen wird nun in folgender Weise ausgeführt: Die Materialien werden
in kleinen Wagen von etwa 2t durch einen Elevator
gehoben und dann zur Einsatzthür auf der Arbeitsbühne gebracht. Bei Verwendung
flüssigen Roheisens wird es in einer Pfanne vom Hochofen oder Cupolofen zugebracht
und dann durch den Elevator gehoben, und darauf zur Ausgieſsöffnung geschoben, wo es
mit einer beweglichen Rinne eingegossen werden kann. Zu gleicher Zeit wird von der
Arbeitsseite her eingesetzt. Der Elevator kann zwei Oefen bedienen. Für schwerere
Stücke bedient man sich zweckmäſsig Welman'scher
Krahne, die zu beiden Seiten des Ofens stehen müssen.
Beim Abziehen der Schlacke muſs der Ofen soweit geneigt werden, daſs dieselbe bei der
Ausgieſsöffnung in einen untergestellten Schlackenwagen ablaufen kann. Der Stahl
wird durch rasche Drehung des Ofens in die Pfanne des Guſskrahnes ausgegossen. Zur
Bedienung der Gieſsgrube dienen die üblichen Blockkrähne.
Die Arbeitsbühne ist möglichst geräumig angelegt. Zwischen je zwei Oefen wird immer
je ein Wärmeofen aufgestellt. Ueberhaupt werden alle Einrichtungen dahin getroffen,
daſs alle durch Maschinen ausführbaren Arbeiten auch durch diese zur Ausführung
gelangen.
Der Entwurf ist einer fachmännischen Kritik durch Steffen unterzogen worden (vgl. Stahl und
Eisen 1888 S. 836). Vgl. auch R. M. Daelen's
Ansichten über beide Entwürfe in Stahl und Eisen 1888
S. 447.
In Stahl und Eisen 1888 S. 873 berichtet Dr. Leo nach Jernk. ann.
1888, VII. über die
Vorgänge bei schwedischen Martin-Oefen mit neutralem
(Chromerz) Futter.
Auf Trollhätta-Martinhütte bestand das Chromerz aus Stücken von etwa ¼ Fuſs Gröſse,
gemengt mit vielem Erzklein und Staub. Das gröbere Erz wurde zur Herstellung der
Wände verwendet, aus Erzklein und Erzstaub wurde der Herd hergestellt. Als Mörtel
bediente man sich eines etwa 0,5 Proc. SiO2 haltigen
Kalkes, mit Erzstaub zur Hälfte gemischt. Der Anstrich wurde aus Chromerz und
Steinkohlentheer ausgestampft und der Ofen vorsichtig angeheizt.
Das Frischen ging unter höchst stürmischem Kochen vor sich. Beim Abstich und in den
Coquillen kochte das Metall gewaltig, ergab aber dennoch volle und sehr zähe
Blöcke.
Bei einem Versuch zu Kolsva, wo nur der Herd und eine Längswand aus gröſseren Stücken
aufgemauert wurden, vollzog sich der Prozeſs ohne auffallende Vorgänge beim Abstich.
Die Ofenwände standen auſserordentlich gut und wurden nicht im Geringsten
angegriffen, während das Dinasgewölbe theilweise abschmolz und an den Wänden
herablief. Der Herd zeigte sich aber gleich nach dem ersten Einsatz erweicht und
wurde schlieſslich so weich, daſs man mit einem Haken die Erzstücke darin umrühren
konnte, während das Eisen geschmolzen darüber stand. Wenn der Ofen eine Zeit lang
leer stand, so wurde der Herd wieder fest. Man will für den Vorgang eine Erklärung
darin finden, daſs der im Chromerz enthaltene Serpentin mit dem etwas
kieselsäurehaltigen Kalk eine Verbindung eingeht, die, wenn auch schwer schmelzbar,
doch in der gröſsten Hitze des Ofens erweicht. Beim leeren Ofen ist die Hitze am
geringsten. Eigenthümlich bleibt es, daſs das Metall nicht in den Herd eindringt,
während in den Ofen geworfenes Chromerz doch auf dem Bade schwimmt.
Aus den Versuchen hat sich ergeben, daſs man für die Ofenwände nie ein besseres
Futter als Chromerz finden kann, da es weder schmilzt noch von der Schlacke
angegriffen wird. Für den Herd aber muſs ein anderes Material gefunden werden.
Der berühmteste schwedische Ingenieur für Martinstahlproduction, Odelstjerna, gibt (Stahl und
Eisen 1888 S. 875) Schwedens Production an Martinstahlblöcken in den Jahren
1884, 1885, 1886 und 1887 zu je 23699, 28914, 33643 und 40461t an, woraus hervorgeht, daſs die Production in
diesem Lande mit jedem Jahre gestiegen ist.
Mit Hilfe von Chromroheisen wird nach Jernk. ann. 1887,
V. in Schweden vielfach ein ausgezeichneter Martinstahl dargestellt, der angeblich
mit dem besten englischen Tiegelstahle wetteifern kann.
Direkte Eisen- und Stahlerzeugung.
Die Verfahren zur direkten Gewinnung des schmiedbaren Eisens, die sogen.
Rennarbeiten, haben trotz vieler Aufwendungen an Zeit, Kraft und Kapital bis auf die
Gegenwart keine nennenswerthen Fortschritte gemacht. Man ist nämlich noch immer
nicht im Stande, mit wirthschaftlich befriedigendem Erfolge sowohl die Reduction des
Erzes als auch die Trennung des reducirten Eisens von den übrigen Bestandtheilen
ohne Anwendung von Roheisen zu ermöglichen.
Nur die in neuerer Zeit entstandene Methode zur direkten Eisenerzeugung von Husgafvel scheint Aufmerksamkeit zu verdienen. Im
Jahrgange 1887 263 477 und 266
388 ist bereits über das betreffende Verfahren nebst dem zugehörigen Ofen Bericht
erstattet worden. Nunmehr liegen bedeutend bessere Betriebsresultate vor als
anfänglich- dieselben sind in Dobriansky in einem Husgafvel'schen Ofen mit Magneteisensteinen von Maloblagodatj erzielt
worden (vgl. Stahl und Eisen, 1889 S. 35 und 121) und
sollen hauptsächlich daher rühren, daſs jetzt harte und stahlartige Luppen
hergestellt werden, während früher vorzugsweise weiche Luppen hergestellt wurden.
Auſserdem wird das Erz auf maschinellem Wege fast pulverförmig zerkleinert, wodurch
die Reduction des Eisens aus dem Erze vollständiger ausgeführt wird. Der Gebläsewind
wird zudem höher erhitzt, und durch Umgebung des Ofenmantels mit schlechten
Wärmeleitern vermindert sich der Wärmeverlust. Betriebsresultate:
I.
Resultate mit Magneteisensteinen und mit Walzsinter 1887.
Mit ungeröstetem feinzerkleinertem Fe3O4
Mit Walzsinter
Bei Darstellung vonEisen
Wenn weichesEisen erzeugtwurde
Wenn hartesEisen erzeugtwurde
Mit Fichten-kohlen
Mit gemischtenFichten-
undBirkenkohlen
Mit Fichtenkohlen
In 24 Stunden gehämmerte Luppen Pud
147,52
181,95
162,78
164,22
Mit einem Korob (2cbm,153) Holzkohlen
10,38
14,61
12,87
13,51
pro Pud Holzkohlen
0,69
0,69
0,86
0,90
Ausbringen an gehämmerten Luppen
50,71
51,27
54,11
61,04
Das Gewicht jeder Gicht, Holz- kohle russ.
Pfund
100
140
100
100
Das Gewicht jeder Gicht, der Möllerung
140 – 156
200 – 220
180 – 185
165 – 170
Gichtenwechsel in 24 Stunden
81,3
71,84
71,04
68,74
Durchschnittl. Gewicht einer Luppe Pud
18,6
21,9
18,5
22,2
Windpressung, in Linien Quecksilber
6 – 16
10 – 18
10 – 15
10 – 15
Windtemperatur, ° C
207
230
225 – 230
150 – 260
„ maximum.
234
300
–
–
Ueber die weitere Bearbeitung der im Husgafvel-Ofen
gewonnenen Luppen geben die nachfolgenden Tabellen Auskunft:
II und III.
Auswalzen von Rohschienen aus Luppen, aus in dem Husgafvel-Ofen
dargestelltem Walzsinter, und Auswalzen von Flachstäben aus den aus dem
Moloblagodatjschen Erze dargestellten Luppen am 17. und 18. September 1887.
Textabbildung Bd. 272, S. 68
Ueber das Auswalzen von Dachblech aus Luppen, welche im Husgafvel-Ofen aus Magneteisen dargestellt waren, sowie über das Hämmern
von Rothblech aus Husgafvel-Metall werden genaue und,
wie es scheint, befriedigende Mittheilungen gemacht; desgleichen sind die Resultate
über Schlag- und Biegeproben mitgetheilt, aus welchen wohl der Schluſs gezogen
werden dürfte, daſs die Gewinnung von schmiedbarem zur Walzung geeigneten Eisen nach
dem Systeme Husgafvel keine Schwierigkeit mehr biete,
namentlich, daſs es möglich sei, für den Martin-Ofen
bestimmte Husgafvel-Luppen mit einem beliebigen Gehalte
an Kohlenstoff darzustellen.
Anfangs beurtheilte man das Product aus dem Husgafvel-Ofen nach dem Verhalten der Luppen bei dem Zangen, indem man annahm,
daſs die Luppe, welche hart (dicht) war und zum Ausschneiden in die für das
Auswalzen passende Form harter Hammerschläge bedurfte, ein hartes oder stahlartiges
Eisen wäre und daſs wiederum die Luppen, welche sich beim Zangen als weich erwiesen,
dem erwünschten weichen Eisen entsprächen. Diese Annahme stellt sich als irrig
heraus, indem man bei der erst später vorgenommenen weiteren Bearbeitung der Luppen
zu Flachstäben und fertigen Dachblechen bemerkte, daſs ein Theil derselben beim
Auswalzen zu Flachstäben bei gelber Glut Risse bekam. Bei erneuerten Schweiſs- und
Schmiedeproben mit den Luppen wurde die Bemerkung gemacht, daſs das Eisen auffallend
schlackenfrei war und daſs nach wiederholtem Erwärmen und Hämmern auch Luppen
gröſserer Dimensionen beim Schmieden bröckelig wurden.
Stahl und Eisen theilt auſserdem 32 Bestimmungen mit,
welche zur Untersuchung der Luppen auf ihren Kohlenstoff-, Schwefel- und
Siliciumgehalt vorgenommen wurden. Von diesen Bestimmungen weisen 20 Proben einen
Kohlenstoffgehalt von weniger als 0,10 Proc. und unter diesen 6 einen solchen von
nur 0,01 Proc. auf, sind also fast frei von Kohlenstoff. Dieses kohlenstoffarme
Eisen besteht aus geschweiſsten Luppenstücken, die aber vor dem Schweiſsen nicht auf
ihren Kohlenstoffgehalt untersucht sind, so daſs nicht angegeben werden kann, um wie
viel der Kohlenstoffgehalt sich beim Schweiſsen verringert hat.
Bis jetzt wird der Prozeſs vorzugsweise mit kleineren einzelnen Oefen betrieben. Man
glaubt jedoch, daſs der Betrieb sich noch wirthschaftlich befriedigender gestalten
würde, wenn eine gröſsere Anzahl von Oefen neben einander angewendet würde; in
letzterem Falle soll die Husgafvel-Methode dem Herd
frisch- und dem Puddelprozesse gegenüber Vortheile besitzen, indem der Aufwand an
physischer Kraft geringer sein würde als bei den genannten Prozessen.
Um eine jährliche Production von 4500l Luppen aus
schwer reducirbarem Erze (Fe3O4) in Oefen von so kleinen Dimensionen wie in
Dobriansky zu erzielen, würden 5 bis 6 Oefen zum Preise von je 5000 Rubel nöthig
sein. Vergröſsert man indeſs die Oefen für eine Production von 4,5 bis 5t in 24 Stunden, so könnte man obige Jahresproduction mit fünf Oefen
herstellen, deren Preis sich auf je 8000 Rubel belaufen würde, wobei allerdings zu
befürchten ist, daſs bei den gröſseren Oefen leicht Roheisenbildung eintreten kann.
In Dobriansky ist diese Bildung mit einem Ofen von etwa 400 Cubikfuſs vermieden
worden, weshalb man schon zu einem Ofeninhalte von 1000 Cubikfuſs bei Neuanlagen
übergehen will.
Die vergröſserten Oefen haben auch dazu beigetragen, den bedeutenden Eisenverlust
durch die Schlacke zu vermindern. Dieser Verlust betrug bei Darstellung von Luppen
aus Seeerzen in den alten Luppenöfen in Finnland 40 bis 50 Proc., welcher allmählich
bis auf 12 Proc. von dem Eisengestelle des Erzes hinabgegangen ist. In Anbetracht
aber, daſs die Luppen bis 15 Proc. Schlacke enthalten, stellt sich der Eisenverlust
in Wirklichkeit höher.
Bei einem Ofen in Kontsche Osero von 520 Cubikfuſs Rauminhalt, welcher ärmere Seeerze
als wie die finnischen verarbeitet, hat sich der Verlust an Eisengehalt des Erzes
unter Berücksichtigung des Schlackengehaltes der Luppen auf etwa 20 Proc. gestellt.
Bei Verarbeitung des Magneterzes von Maloblagodatj mit einem Eisengehalte von 58
Proc. hat man zu Dobriansky 51 Proc. gehämmerte Luppen erhalten, was einem Verluste
von 12,07 Proc. vom Eisengehalte des Erzes entspricht.
Angenommen, daſs der Verlust beim Puddelprozesse 10 Proc. ausmacht, so verliert man
bei der direkten Methode bei eisenarmen Erzen 10 Proc. mehr als bei dem combinirten
Hochofen- oder Puddelprozesse; bei reicheren Erzen dagegen wird dieser Verlust mit
dem zunehmenden Eisengehalte des Erzes verringert und macht bei obigem Magneterze
nur 2,07 Proc. mehr als beim Puddeln aus.
Kostet nun beispielsweise ein Erz mit 36 Proc. Eisen 7 Kopeken das Pud, so wird der
Werth von 1 Pud Eisen im Erze \frac{1\,.\,100\,.\,7}{36}=19,5
Kop. Verliert man von diesem Eisen 10 Proc., so wird der Verlust 1,95 Kop. für 1
Pud.
Ferner sei der Preis des 58 Proc. Eisen enthaltenden Magneterzes bei der Hütte 9 Kop.
für 1 Pud, so würde in diesem Falle 1 Pud Eisen im Erze
\frac{1\,.\,100\,.\,9}{58}=15,5 Kop. kosten. Wenn man bei
direkter Production mit diesem Erze sogar bis 5 Proc. mehr, als der Abbrand beim
Puddeln ist, verlieren würde, so repräsentirt der Verlust doch nicht mehr als 0,775
Kop. Durch den Eisenverlust in der Schlacke werden also die Darstellungskosten von 1
Pud nach der direkten Methode erzeugten Eisens 1,05 Kop. bezieh. 0,775 Kop. mehr
betragen, wogegen man aber, indem man einen ganzen Prozeſs umgangen, alle mit dem
Roheisen frischen verbundenen Kosten erspart, welche, die Amortisirung des Werkes und die Generalkosten
eingerechnet, für den Puddelprozeſs 35 bis 45 Kop. für 1 Pud Eisen ausmachen.
Wenn man nun bedenkt, daſs diese Methode nur die Hälfte von der für die
Roheisenerzeugung nöthigen Menge Zuschlag erfordert, welcher manchmal in gleichem
Preise steht wie das Erz, so ist der Erzverlust in diesem Falle nicht gerade
bedeutend.
Es sei noch erwähnt, daſs die Anlage einer Trockenanstalt für die zu verwendende
Kohle dem Betriebe zu groſsem Nutzen gereichen wird.
Bei der Berechnung der Productionskosten muſs man unterscheiden, ob arme oder reiche,
phosphorhaltige Erze zu einem Materiale für den Martin-Prozeſs verarbeitet werden sollen, oder ob Luppen für direkte weitere
Verarbeitung aus genügend reinen und eisenreichen Erzen dargestellt werden
sollen.
Für den ersteren Fall sei eine jährliche Production von 4500t Luppen aus Seeerzen mit Holzkohle angenommen.
Die Anlagekosten für Gebäude, 3 Oefen (35000 Rubel), Dampfkessel, Trockenapparat für
Kohle u.s.w. würden sich dann auf 90000 Rubel belaufen.
Die Darstellung von 1t Luppen aus 36procentigem
Seeerze mit 30 Proc. Ausbringen, einem Verbrauche von 1 Gew.-Th. Holzkohlen auf 1
Gew.-Th. Luppen und einer Aufwendung von 2 Rubel 40 Kop. für Arbeitskräfte beträgt
25,10 Rubel.
Für den zweiten Fall würden bei gleicher Jahresproduction die Anlagekosten für drei
Oefen (je 28cbm) mit Gasfang, Gebläsemaschine,
Gichtaufzug, Kohlentrockenanstalt, Röstöfen (Westman),
Erzquetsche Dampfhammer zum Zangen und Zerschroten der etwa 50 Pud schweren Luppen
und Dampfmaschine in einem schon bestehenden Eisenwerke etwa 100000 Rubel betragen.
Der Kohlen verbrauch soll sich auf 1,2 Gew.-Th. auf 1 Gew.-Th. gehämmerter Luppen
und die Arbeitskraft auf 3,5 Rubel auf die Tonne Luppen belaufen.
Werden dann die Kosten der unmittelbaren Darstellung der Luppen und deren Auswalzen
zu Rohschienen mit denjenigen der von demselben Erze unter vollkommen gleichen
Verhältnissen mittels des Hochofen- und Puddelprozesses gewonnenen Rohschienen
verglichen, so soll sich ein Unterschied von 16 Rubel 53 Kop. für die Tonne zu
Gunsten der direkten Darstellung ergeben.
Luppen für den Martin-Prozeſs sollen etwa den
Productionskosten von Roheisen gleichkommen, welches unter ganz gleichen Bedingungen
hergestellt ist.
Es erscheint vortheilhaft, die hier besprochenen Luppen sowohl beim basischen als
auch beim sauren Martin-Prozesse anzuwenden.
Direktor O. Mürisier vom Alexandrowsky-Stahlwerke zu St.
Petersburg theilt bereits Betriebsergebnisse über Verwendung von Husgafvel-Eisenluppen beim basischen Martin-Prozesse mit.
Die Martin-Einsätze enthielten:
1
2
3
Phosphor
0,80
0,78
0,83
Schwefel
Spuren
0,013
0,013
Silicium
0,56
0,82
0,76
Mangan
1,65
0,92
0,80
Die Husgafvel-Luppen von Kontschosero enthielten:
1
2
Phosphor
0,34
0,38
Schwefel
Spuren
0,012
Der Kohlenstoffgehalt der Beschickungen wurde im Mittel zu 0,7 Proc. angenommen. Mit
diesem Materiale wurden vier Hitzen im basischen Martin-Ofen auf Erzeugung von Fluſseisen gemacht. Jede Beschickung (8t) enthielt nach Berechnung ungefähr
Folgendes:
CProc.
PProc.
SiProc.
MnProc.
Beschickung
Nr.
1332
2
0,56
0,30
0,46
„
„
1341
1,74
0,52
0,236
0,362
Die vier Beschickungen setzten sich aus folgenden Materialien zusammen:
Nr. der Beschickung:
1332
1330
1340
1341
Olonetz-RoheisenHusgafvel-Luppen
kg30304504
kg32764258
kg26204914
kg23755160
Zuschlage
Maryport-RoheisenFerromangan (50 Proc. Mn)
491 94
491 94
524 94
393 90
8119
8119
8152
8018
Aus diesen vier Beschickungen gingen 2880k gute
Fluſseisenblöcke hervor. Der Verlust bei der Schmelzung durch Abbrand und Abfall
betrug somit 11½ Proc. der Einfüllung. Wegen des hohen Kohlenstoffgehaltes der
Luppen dauerten die Beschickungen etwa 10 Stunden.
Das erhaltene Fluſseisen wurde zu Winkel- und Profileisen für Schiffsbau verwalzt, Es
soll wegen des geringen Schwefelgehaltes ein vorzügliches Schweiſsmaterial
liefern.
Es sei denn, daſs es möglich wäre, den Eisenschrot oder die Abfälle beim Martiniren
durch Husgafvel-Luppen zu ersetzen, sonst werden die
deutschen Eisenhüttenleute trotz aller Anpreisungen mit Kopfschütteln an der Husgafvel'schen Rennarbeit vorübergehen.
W.
Koort.
Tafeln
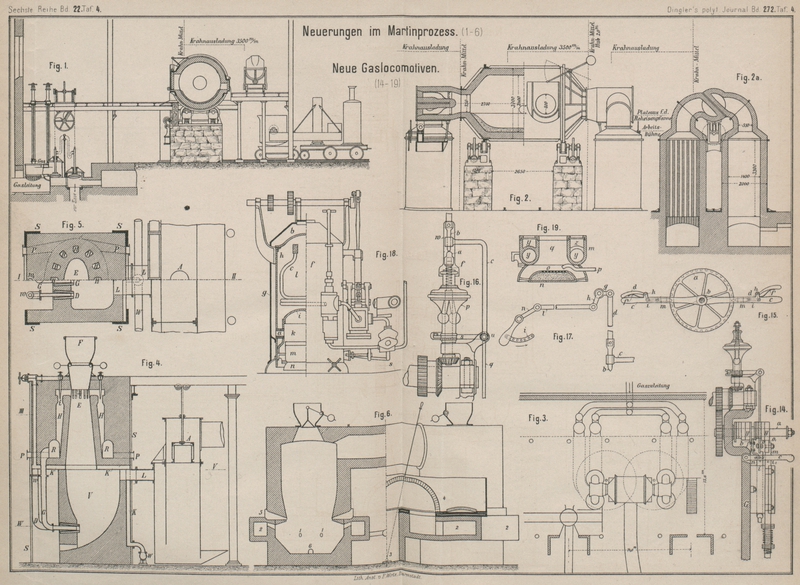