Titel: | Neuere Cupolöfen. |
Fundstelle: | Band 274, Jahrgang 1889, S. 163 |
Download: | XML |
Neuere Cupolöfen.
Mit Abbildungen auf Tafel
10.
Neuere Cupolöfen.
Die Bestrebungen auf dem Gebiete der Gieſserei waren in den letzten Jahren sehr
lebhaft und sowohl darauf gerichtet, die Arbeit des Formens mehr und mehr den
Maschinen zu überweisen – ein Bestreben, welches wohl in erster Reihe durch die
mannigfachen Ausstände der Former angeregt worden ist – als auch darauf, dem
Betriebe durch Verbesserung der Schmelzvorrichtungen und Betriebsweisen
wirthschaftlich aufzuhelfen und auf diese Weise den sehr gedrückten
Unternehmergewinn nach Möglichkeit zu heben.
Zu diesem Zwecke wurde in erster Reihe eine bessere Ausnutzung des Brennmaterials angestrebt. Die nach dieser Richtung
erzielten Ergebnisse wurden mitunter so betont, daſs es fast schien, als ob es die
erste Aufgabe des Cupolofens sei, ein möglichst geringes Maſs von Koks zu
verbrennen. Natürlich hat dies an sich ja zu rechtfertigende Bestreben sofort ein
Ende, wenn das erzielte Guſsmaterial minderwerthig wird. Dem Anscheine nach ist man
bei den Versuchen der Grenze der möglichen Ersparniſs sehr nahe gekommen, und hat
allerdings einen bedeutenden Minderverbrauch erzielt. Wenn hin und wieder die Grenze
überschritten wurde, so machte sich auch bald der nöthige Rückschlag bemerkbar. Die
Richtung der einschläglichen Bestrebungen war eine mehrfache, und entweder darauf
gerichtet, die Bildung des Kohlenoxydes möglichst zu verhindern, oder, wenn sich
dasselbe gebildet hatte, es möglichst vortheilhaft zu verwerthen; ferner suchte man
das genannte Ziel durch Vorwärmen des Windes zu erreichen.
Ganz besonders wurde das von Herbertz wieder angeregte
und von ihm erst lebensfähig gemachte System des Saugegebläses (Woodward) ausgebildet. Die Ergebnisse der Schmelz- und
Betriebsweise der Herbertz'schen Oefen waren so
günstig, daſs in kaum drei Jahren allein in Deutschland an 150 Oefen dieser Art
aufgestellt worden sind. Auch für andere Oefen, zu metallurgischen Zwecken, zum
Rösten, zum Glasschmelzen u. dgl., hat sich die Herbertz'sche Bauweise eingeführt; sogar hat der zu Grunde liegende
Gedanke neuerdings auf Kesselfeuerungen, unter Wegfall der Roststäbe, Anwendung
gefunden. Auf letztere Feuerungen hoffen wir in kurzem unter Mittheilung von
Betriebsergebnissen zurückkommen zu können.
Die auſser dem Herbertz'schen Ofen zur Zeit wohl am
weitesten verbreiteten Oefen von Greiner und Erpf
(vertreten durch Lürmann), sowie die von Ibrügger und Krigar sind
auf einen so hohen Leistungsgrad gebracht worden, daſs die Wahl in erster Reihe wohl
von örtlichen Verhältnissen bedingt ist. Bei Gelegenheit der am 6. September 1887 in
Coblenz stattgehabten Versammlung des Vereins deutscher Bisengieſsereien wurden
(nach Stahl und Eisen, Oktoberheft S. 743) die
Leistungen von Cupolöfen besprochen, und berichteten mehrere Theilnehmer über ihre
Erfahrungen bei Anwendung Lürmann'scher, Herbertz'scher und Ibrügger'scher Cupolöfen. Herr Bergrath Jüngst erwähnt, daſs er den früher befolgten Grundsatz, möglichst viel
Kohlen zu sparen, aufgegeben habe. Nach seinen Erfahrungen sei die Behauptung, daſs
bei dem Lürmann'schen Ofen eine auſserordentliehe
Kohlenersparniſs zu erzielen sei, nicht zutreffend; das Eisen sei bedeutend besser
geworden und der Procentsatz an Ausschuſs ganz erheblich gesunken, seitdem man bei
dem Betriebe nicht mehr auf Kohlenersparniſs sehe.
Herr Ingenieur Sahler, Oberingenieur der Firma F. A. Herbertz, theilt mit, daſs mit dem Herbertz'schen Ofen in dem Etablissement der Firma F. A. Herbertz zu Cöln bereits seit drei Jahren
gearbeitet werde. Der Ofen habe während dieser Zeit alle Phasen der Entwickelung
durchgemacht und Erfolge erzielt, wie sie bei keinem der Oefen anderer Systeme zu
erzielen seien. Bei einmaliger Koksfüllung bedürfe der Ofen 5 Proc. Satzkoks und
ergebe eine Abbrandersparung gegenüber den Oefen mit gepreſstem Winde von 3 bis 5
Proc. Der wesentlichste Vortheil des Herbertz'schen
Ofens liege indessen hauptsächlich in der Erzeugung eines dichten und weichen
Gusses, auch aus geringen Roheisenmarken, was darin seinen Grund habe, daſs durch
die gleichmäſsige, rings um den Schacht gehende Oeffnung für die Lufteinströmung die
äuſserste atmosphärische Luft mit ganz geringer Spannung in den Ofen trete, die Koks
dicht über der Lufteinströmungsöffnung unter Bildung von Kohlensäure zur Verbrennung
bringe und ein Schmelzen des Eisens, unter möglichst geringer Entziehung von
Kohlenstoff und Silicium, herbeiführe. Das Eisen werde nicht, wie bei anderen Oefen,
bereits im oberen Theile
des Schachtes tropfbar flüssig, sondern gelange, gut vorgewärmt, in die sehr tief
liegende Schmelzzone und, ohne stark oxydirenden Winden ausgesetzt zu sein, von da
hitzig geschmolzen in den Sammelraum. Der Kohlenverbrauch zur Erzeugung des Dampfes
sei seiner Zeit bei Gebrüder Sulzer in Ludwigshafen auf
das Gewissenhafteste festgesetzt worden, und es seien demnach bei 8 facher
Verdampfung des Kessels 1k,80 Kohlen erforderlich,
um 100k Eisen zu schmelzen, was einem Betriebe mit
gepreſstem Winde annähernd entspreche. Die Leistungsfähigkeit dieses Ofens sei bei
stetigem Betriebe eine unbeschränkte und schmelze gegenwärtig ein Ofen bei der
Isselburger Hütte stündlich 4 bis 5000k Eisen
herunter. Bei den vor kurzem angestellten Versuchen mit erhitzter Luft wurde die
einströmende Luft durch den Ofen selbst auf 400° vorgewärmt, und man war dadurch in
der Lage, nicht nur Stahl, sondern auch Schmiedeeisen ohne jeglichen Zusatz sehr
hitzig und dünnflüssig zu schmelzen.
Auch Frh. v. Manteuffel erwähnt, daſs unter den neueren
Cupolöfen sich ganz besonders die von F. A. Herbertz
und von Greiner und Erpf durch geringeren
Materialverbrauch auszeichnen. Auf dem Eisenwerke Lauchhammer sei neuerdings ein Herbertz-Ofen
mit einer stündlichen Schmelzleistung von 3 bis 4000k im Betriebe und ergebe sehr befriedigende Resultate, er arbeite sehr
gleichmäſsig und das Eisen komme schon nach höchstens 10 Minuten nach Anlassen des
Dampfstrahles geschmolzen in den Herd und tropfe dann ohne Unterbrechung weiter. Es
lassen sich in diesen Oefen auch geringwerthigere Roheisensorten verschmelzen, und
der daraus erzeugte Guſs sei auch in den kleinsten Gegenständen weich, leicht
bearbeitbar und äuſserst scharf in den Conturen.
Auf dem ebenfalls der Actiengesellschaft Lauchhammer
gehörigen Eisenwerke Gröditz bei Riesa sei andererseits seit Januar d. J. ein
Cupolofen, ausgeführt nach dem Systeme Greiner und Erpf
und nach den Angaben des Ingenieurs Lürmann in
Osnabrück, mit bestem Erfolge im Betriebe, so daſs augenblicklich noch ein zweiter
derartiger Ofen eingerichtet werde.
Wenn nun zur Erzielung einer rationellen Ausnutzung des Brennmaterials erforderlich
sei, daſs alle brennbaren Bestandtheile desselben auch wirklich verbrannt werden, so
sei dies bei den Cupolofen älterer Form entschieden nicht der Fall, es gehen bei
diesen im Gegentheile eine groſse Menge brennbarer Gase unverbrannt verloren. Es
habe dies hauptsächlich daran gelegen, daſs diese alten Oefen stets nur eine
benutzte Düsenreihe, oft nur zwei oder sogar nur eine Düse hatten. Gerade diesem
Uebelstande haben die Oefen von Greiner und Erpf ganz
wesentlich abgeholfen, indem sich auſser der unteren Düsenreihe, deren 5 bis 6 im
Kreise rundum angebrachte Oeffnungen eine Weite von 100 bis 125mm haben, am Ofen auſsen eine ganze Spirale von
kleinen sogen.
Oberwinddüsen befinde, die 25mm Durchmesser haben
und deren Zahl 12 bis 18 betrage. Dadurch nun, daſs diese Düsen spiralförmig um den
Ofen laufen und derartig in den Ofen einmünden, daſs die Gase von oberhalb der
Schmelzzone an bis zu einer Höhe von etwa 2m,60
von der Sohle ab stets, und zwar rundum, von irgend einer Seite Zufuhr an Luft
erhalten, werde bewirkt, daſs die von unten aufsteigenden Gase fast bis zum
Verlassen der Eisen- und Koksschichten die zum Verbrennen nöthige Luft zugeführt
erhalten, so daſs fast alle brennbaren Gase auch wirklich verbrannt werden. Die Höhe
des in Gröditz aufgestellten Ofens betrage von der Abstichsohle bis zur
Einwurföffnung 4m,50, der Ofen habe eine untere
Düsenreihe von 6 Stück zu 125mm Durchmesser und
eine obere von 15 Stück zu 25mm Durchmesser, diese
letzteren werden, unabhängig vom unteren Gebläse, auf besonderen Winddruck regulirt.
Es werden täglich 24000 bis 32000k Roheisen
durchgeschmolzen, die Maximalleistung betrage 40000k und dabei sei das Eisen stets sehr hitzig und bestens brauchbar. Die
Ersparniſs an Koks betrage etwa 25 Proc.
Wir haben im Vorstehenden die Auslassungen der betreffenden Fachleute dem
wesentlichen Inhalte wiedergegeben, um zu belegen, daſs die Wahl des Ofens
wesentlich von der Oertlichkeit und dem Geschmacke abhängig sein wird.
Weitere erwähnenswerthe Bestrebungen sind darauf gerichtet, eine Verbesserung des
Eisens dadurch zu erzielen, daſs gewisse Zusätze gemacht werden oder auch Luft mit
Pressung eingeführt wird, beides in der Absicht, eine chemische Umwandelung zu bewirken. Dabei wird denn auch mehrfach versucht,
stahlartiges Material zu erzielen. Die nothwendige Folge dieser Bestrebungen ist,
dem Ofen einen höheren Hitzegrad zu ertheilen, wozu in erster Reihe ein Vorwärmen der Gebläseluft sich als wirksam gezeigt
hat.
Nebenher gehen Versuche, die auf den übrigen Gebieten des Hüttenwesens so vielfach
mit Erfolg verwendeten Gasfeuerungen auch im
Cupolofenbetrieb zu benutzen, wozu noch besonders das Bedürfniſs angeregt hat, bei
der Stahlgewinnung das Schmelzgut von der Berührung mit dem Brennmateriale fern zu
halten.
Im Nachstehenden werden wir auf die einzelnen Punkte näher eingehen, wobei sich
ergeben wird, daſs bei den Ausführungen vielfach die gleichzeitige Lösung mehrerer
der angedeuteten Aufgaben angestrebt wird.
Die Zusätze zur chemischen Umwandelung betreffend,
machen wir zunächst auf die Mittheilung F. Gautier's
über das Schmelzen von Schmiedeeisen- oder Stahlabfällen im Cupolofen unter Zusatz
von Siliciumeisen aufmerksam, welche derselbe in der Versammlung des „Iron and Steel Institute“ vorgetragen hat (vgl. Stahl und Eisen, 1888 Nr. 8). Der Vortragende wies auf
die Schwierigkeit hin, durch Schmelzen von schmiedbarem Eisen mit Zusatz von gewöhnlichem Graueisen,
also durch jenes Verfahren, welches bereits seit länger als zwanzig Jahren für
verschiedene Zwecke, neuerdings für die sogen. Temperstahldarstellung, hier und da
versuchsweise zur Anwendung gebracht worden ist, ein gut gieſsbares Material zu
erhalten. Da der Siliciumgehalt beim Cupolofenschmelzen sich verringert, der
Kohlenstoffgehalt kohlenstoffarmen Eisens dagegen eher zu- als abnimmt, so erfolgt
ein weiſses, siliciumarmes, zur Herstellung dichter Güsse wenig brauchbares
Guſseisen. Durch Zusatz von Siliciumeisen statt des gewöhnlichen Graueisens zum
schmiedbaren Eisen läſst sich, wie in Frankreich angestellte Versuche ergeben haben,
ein besserer Erfolg erlangen.
Auf einem Werke zu Havre wurden 79 Th. Fluſseisenblechabfälle mit 21 Th. 13
procentigerm Siliciumeisen zusammengeschmolzen. Der Siliciumgehalt des Einsatzes
betrug demnach 2,60 Proc.; der Siliciumgehalt des geschmolzenen Metalles scheint
nicht ermittelt worden zu sein. Man erhielt Blöcke, deren einer von 40mm Stärke im Quadrat bis auf 30mm Stärke geschmiedet wurde, ohne irgend welche
Risse zu bekommen. Der gehämmerte Block, 30mm
stark, wurde dann einer Schlagprobe unterzogen. Bei einer freien Auflage von 160mm hielt er zwölf Schläge mit einer Fallkugel von
16k Gewicht aus, deren erster aus einer Höhe
von 35cm und jeder folgende aus etwas gröſserer
Höhe geführt wurde, bis schlieſslich bei 1m
Fallhöhe der Bruch erfolgte.
Bei einem anderen zu Terrenoire angestellten Versuche schmolz man 77 Th. Stahlabfälle
mit 23 Th. 9 procentigem Siliciumeisen und goſs daraus einen quadratischen Stab von
30mm Stärke, welcher, ohne geschmiedet zu
sein, bei dem zehnten Schlage einer gleich schweren Fallkugel als bei dem ersten
Versuche aus einer Höhe von 1m,010 zerbrach.
Probestücke, aus schottischem Gieſsereiroheisen gegossen, pflegen, nach Gautier, wenn sie der gleichen Probe unterworfen
werden, bei einer Fallhöhe von durchschnittlich 0m,4 zu zerbrechen, und es ist demnach die bedeutend gröſsere Zähigkeit des aus
Stahlabfällen und Siliciumeisen erzeugten Gieſsmaterials nicht zu verkennen.
Prüft man nun, ob das Verfahren eine gröſsere Bedeutung als die eines lehrreichen
wissenschaftlichen Versuches besitzen kann, so ergibt eine Selbstkostenrechnung –
bekanntlich die empfindlichste Probe auf die Zweckmäſsigkeit eines Verfahrens –
folgendes:
790k Stahlabfalle zu 65
M.
51,35 M.
210k 13 procentiges
Siliciumeisen zu 135 M.
28,35 „
Schmelzkoks
2,– „
Schmelzerlöhne
3,– „
Sonstige Schmelzkosten (Gebläse, Gezäh, Repara- turen
und anderes mehr)
5,– „
–––––––
Zusammen
89,70 M.
Rechnet man 5 Proc. Abbrand, so kosten 1000k
geschmolzenes Metall vor dem Eingieſsen in die Guſsformen 94,20 M. Dabei sind die
Einheitspreise
absichtlich ziemlich niedrig gerechnet. Hieraus folgt zunächst, daſs, wie sich
erwarten lieſs, die Kosten des Verfahrens ziemlich hoch sind. In den meisten Martin-Hütten, wo man aus dem Martin-Ofen Guſswaaren erzeugt, wird man billiger arbeiten können und ein
noch vorzüglicheres Guſsmaterial gewinnen. Ein Martin-Ofen aber erfordert einen ununterbrochenen Betrieb; für eine
gewöhnliche Gieſserei würde er nicht geeignet sein.
Daher kann für besondere Zwecke, wie sie auch in gewöhnlichen Eisengieſsereien nicht
selten vorliegen, das von Gautier empfohlene Verfahren
wohl als brauchbar sich bewähren, zumal wenn es durch fernere Versuche noch weiter
ausgebildet, insbesondere wenn für jeden einzelnen Fall ermittelt wird, welches
Verhältniſs zwischen Siliciumeisen und Stahlabfällen das geeignetste sei.
Ueber die Zusätze von Aluminium, Mangan, Nickel und anderer Metalle werden vielfach
Versuche gemacht, die jedoch zu einem Abschluſs noch nicht gekommen sind. In D. p. J. 1889 273 456
berichteten wir bereits über die vorzüglichen Erfolge, welche Riley mit Nickeleisen erreicht hat. Mit
Aluminiumzusätzen werden vielfach Versuche gemacht, unter anderem auf dem Kruppschen Stahlwerke in Essen (vgl. auch Mitiseisen
1888 267 397).
Die chemische Umwandelung im Cupolofen durch Eintreiben atmosphärischer Luft für sich
oder in Verbindung mit anderen Stoffen ist der Zweck des zweitheiligen Ofens zur
Erzeugung von Schmiedeeisen und Stahl von Joseph
Toussaint in Holmes Hall bei Brigg (Lincolnshire) (D. R. P. Nr. 46157 vom
16. Oktober 1887). Bei diesem Ofen ist der untere Theil B (Fig.
1) von dem oberen A durch eine mit Löchern
versehene Scheidewand K getrennt. An der Seite ist ein
Rohr L angeordnet, welches seitlich über dem Boden F einmündet und zum Zuführen von Fett oder Mischung von
Fett und anderen Stoffen dient, welche eine dem Puddelprozeſs ähnliche Wirkung in
dem geschmolzenen Bade hervorbringen sollen. H ist das
Abstichloch. Fig.
2 zeigt die Ausbildung der durchlöcherten Scheidewand K als Ring und die Verbindung des letzteren mit einem
oben und unten offenen, bis zum Boden des Ofens reichenden durchlöcherten Rohr M, welches concentrisch zum Futter J der Kammer B steht, zum
Zweck, einen ringförmigen Raum zu schaffen, in welchen die fettigen Stoffe
eingeführt werden können.
Eine ähnliche Einrichtung zeigt der Boccard'sche Ofen,
welchen Revue industrielle vom 21. Juli 1887 S. 282
beschreibt. Er hat spiralförmige Anordnung der Düsen, wie das System Greiner und Erpf und ist, worauf seine
Eigenthümlichkeit beruht, mit durchlöchertem Boden, in ähnlicher Weise wie die
Bessemerbirne, versehen. Hierdurch soll der Ofen zur Darstellung von Stahl geeignet
sein. Als Gebläse wird eine Gebläsemaschine oder auch ein Ventilator benutzt. In den
Fig. 3 bis
6
bezeichnet a die Luftkammer, b den Herd; durch die Oeffnung c
flieſst das geschmolzene
Metall dem Herde zu. Eine zweite Luftkammer ist bei d,
eine dritte bei e mit Schaulöchern f und den Düsen h. Durch
die Kanäle k gelangt die Gebläseluft auf den Boden des
Herdes. Als gemeinsame Zufuhr des Gebläsewindes dient das Rohr l. Das Abstichloch für den Herd ist bei m, bei m1 befindet sich ein ähnlicher Abstich für den
eigentlichen Schmelzofen. Die Windzuleitungen sind mit Absperrventilen versehen, um
nöthigenfalls den ganzen Winddruck für die Kammer a zur
Verfügung zu haben, wenn der Ofen als Stahlofen benutzt werden soll. Vorsorglich
wird in unserer Quelle bemerkt, daſs man, wenn vermuthet wird, daſs der Wind nicht
kräftig genug sei, um das flüssige Metall am Durchflieſsen nach a zu hindern, den Windraum a nebst den Löchern mit Sand füllt. Das Gebläse wird alsdann
ausschlieſslich durch die sechs Kanäle k geleitet und
tritt am Boden ein. Das Erzeugniſs dieses Ofens soll sich sowohl für die kleinsten
Guſsstücke eignen, die bis jetzt in Schmiedeguſs gemacht wurden, als auch für
Maschinenguſs und für Walzen, welche letztere sich durch besondere Festigkeit
auszeichnen. Oefen dieser Art verwendet die Bugloser Hütte. Wir sind der Meinung,
daſs der Boccard'sche Ofen, um zuverlässig zu sein, von
zu vielen Zufälligkeiten des Betriebes abhängig ist. Ein Einströmen des Gusses in
die Kammer a würde eine sehr schwierige
Wiederherstellung erfordern. Die Verwendung gewöhnlicher Ventilatoren halten wir
geradezu für ausgeschlossen.
Den Zweck des Feinens suchte William Jukes, W. B. Glover
und F. Bosshard in Manchester nach dem D. R. P. Nr.
44730 vom 24. Januar 1888 dadurch zu erreichen, daſs sie zwei Cupolöfen anordnen,
welche durch einen gemeinschaftlichen Sammelraum verbunden sind (Fig. 7). Mit dem letzteren
ist die Feinvorrichtung verbunden. Der Boden des gemeinschaftlichen Sammelraums ist
nämlich mit einer durchlöcherten Brücke versehen, die durch den Windkasten g Wind empfängt. Das in den Oefen niederschmelzende
Eisen flieſst über die Brücke, wird von den durch dieselbe tretenden Windstrahlen
gefeint und fällt dann an den Seiten der Brücke in den Herd des Sammelraumes
herunter. Der durch die Brücke geblasene Wind tritt durch die Röhren d in die Cupolöfen.
Eine Reihe von Cupolöfen, welche die Zuführung fremder Stoffe zu dem angegebenen
Zwecke – Veränderung der Eisenqualität – ermöglichen, erwähnt A. Gouvy fils in seiner auch als Sonderabdruck (bei Chaix, Paris 1887) erschienenen Studie „Étude sur les cubilots pour la fusion de la fonte“.
Insbesondere sind dies die Oefen von Batty 1877 224 * 105, Voisin-Bichon,
Herliczka 1880 238 * 318, Ibrügger 1882 245 * 14 und
Krupp 1880 235 * 373,
welche jedoch an der angeführten Stelle bereits besprochen sind. Von dem in
Frankreich sehr verbreiteten Voisin-Bichon'schen Ofen
mit Einspritzung von Erdöl oder anderer flüssiger Oele gibt Gouvy
die in Fig. 8 und 9 dargestellte Zeichnung.
Von den beiden Erdölbehältern E aus führen Röhren in
die obere Kante der unteren, kleinen Düsen, wo das Erdöl erfaſst und in den Ofen
gefördert wird. Eine Reihe von weiteren Düsen befindet sich in etwas gröſserer Höhe.
Als Hauptvortheil des Ofens wird angegeben, daſs derselbe eine hohe Temperatur und
ein Niederschmelzen groſser Mengen ermöglicht. Belege dieser Vorzüge, durch
Mittheilung von Betriebsergebnissen, bringt der Verfasser leider nicht. Wie aus der
Figur ersichtlich, sind die oberen Düsen für sich abstellbar. Den nebenbei erwähnten
Umstand, daſs man eine letzte Beschickung von Eisen ohne Brennmaterial aufgeben
könne, halten wir für unwesentlich.
Erwähnt sei noch, daſs nach Gouvy das Stahlwerk von
Longwy bei den Schmelzungen im Cupolofen einen Koks verwendet, welcher durch Mischen
von Steinkohle und Manganerz aus gewöhnlichen Koksöfen erzielt wurde. Durch die
basische Schlacke soll, nach Angabe der Erfinder, jede Spur von Schwefel aus dem
Guſs entfernt worden sein.
(Fortsetzung folgt.)
Tafeln
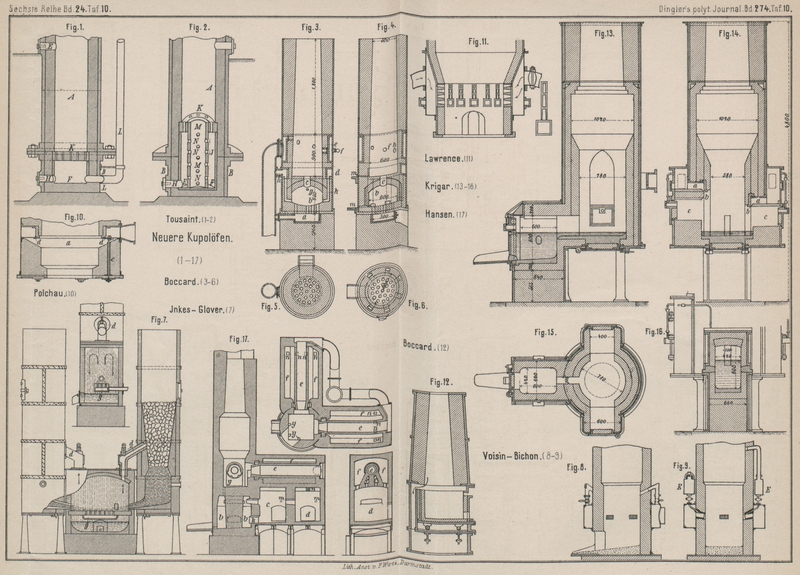