Titel: | Von der Deutschen Allgemeinen Ausstellung für Unfallverhütung in Berlin 1889. |
Fundstelle: | Band 275, Jahrgang 1890, S. 342 |
Download: | XML |
Von der Deutschen Allgemeinen Ausstellung für
Unfallverhütung in Berlin 1889.
(Schluſs des Berichtes S. 297 d. Bd.)
Mit Abbildungen auf Tafel
18.
Deutsche Allgemeine Ausstellung für Unfallverhütung in
Berlin.
Müllereimaschinen.
Die allgemeinen Verhältnisse lagen hier ebenso wie bei der eben besprochenen
Industrie. Es wurde die Gesammteinrichtung einer Dampfmühle von Kapler in Berlin im Betriebe vorgeführt und auſserdem
diese und jene Arbeitsmaschine aus dem groſsen Getriebe der heutigen Müllerei
gezeigt.
Der allgemeine Gesichtspunkt der Unfallverhütung tritt in dieser Schaustellung mehr
in den Hintergrund gegenüber dem Bestreben, möglichst staubfrei zu mahlen, also
Staub in der Mühle zu verhindern, um auf diese Weise den gefährlichsten Feind der
Müllerei, die Staubexplosionen, zu verhüten. Diese Staubverhinderung ist denn auch
thatsächlich wohl vollkommen gelungen und auch vortrefflich zur Anschauung gebracht.
Weder in der Kapler'schen Mühle, noch bei den häufig in
Betrieb gezeigten einzelnen Arbeitsmaschinen war eine Staubbildung bemerkbar.
Die bewirkte Staub Verminderung erfolgte durch Staubsammler verschiedenartiger
Construction. Dieselbe geschieht zunächst zur Verhütung von Feuersgefahr, sodann
aber auch zur Herstellung staubfreier Luft im Interesse der Arbeiter.
Die Erzeugung von Feuerfunken kann geschehen, sowohl wenn zwischen die Arbeitsflächen
der Maschinen (namentlich bei Mühlsteinen) harte Körper gelangen, als auch wenn
hochgradige Erwärmung in den Zapfenlagern und auf den Reibungsflächen der Maschinen
stattfindet – oder – es werden Funken von auſserhalb zugeführt. Gegen diese drei
Arten wird man sich zu schützen haben.
Man vermeidet zunächst, daſs harte Körper in die Arbeitsmaschinen gelangen können,
durch vorherige gute Reinigung des Arbeitsgutes,
namentlich Entfernung aller beigemischten Eisentheile mittels Magnetapparates, sowie
Entfernung der Steine durch Steinauslesemaschinen.
Das Warmgehen der Lager und Arbeitsflächen ist zu verhüten, wenn man die Lagerungen
einmal sorgfältigst construirt und hauptsächlich auf Wahl eines passenden
Lagermetalls und genügende Lagerfläche die nöthige Rücksicht nimmt, sowie
selbsthätig wirkende Schmiervorrichtungen anbringt; auch die kühle Luft der
Aspiration wirkt hier vortheilbringend. Der Schutz der Maschinen gegen Eindringen
von Funken von auſsen her kann ziemlich sicher durch luftdichten Abschluſs derselben
und wenn möglich durch Construction solcher aus Eisen bewirkt werden.
Die Beseitigung des Zündmittels, um entstehenden Feuerfunken die Nahrung zu nehmen,
läſst sich erzielen durch Aspiration der
Arbeitsmaschinen. Bei Construction solcher Anlage ist indeſs gar vielerlei
zu beobachten und muſs dabei sehr sorgfältig und mit Sachkenntniſs verfahren werden.
Um das Richtige zu treffen, hat man vor Allem die Beschaffenheit des Arbeitsgutes
ins Auge zu fassen, denn es ist durchaus nicht gleichgültig, welcher Art die aus der
Arbeitsmaschine sich ergebenden Abgänge sind. Diese sind bezüglich ihrer
Feuergefährlichkeit wesentlich verschiedenartig. Gröſse und Beschaffenheit des
Staubsammlers, Stärke des Luftstromes, also Gröſse und Umlaufszahl des Gebläses,
sowie die Stärke der Luftströmung muſs hier entsprechend gewählt sein. Nun ist
bekannt, daſs ein bestimmtes Gemenge von Mehlstaub, Cellulosetheilchen und
atmosphärischer Luft in bestimmter Dichtigkeit explosionsfähig wird, es muſs daher
vermieden werden, daſs solches Gemenge entstehen kann.
Es wird hier zu beachten sein, daſs der Staubsammler möglichst nahe der
stauberzeugenden Maschine angeordnet wird und – ist dies nicht thunlich – daſs die
Verbindung mit derselben so hergestellt werde, daſs in derselben keinerlei Staub
sich ansammeln kann. Muſs diese Verbindung durch wagerecht liegende Rohre angeordnet
werden, so wird man gut thun, solche mit Schnecken zu versehen. Hölzerne
Verbindungsrohre sind hierbei solchen aus Eisen vorzuziehen, da Eisen durch Bildung
von Niederschlagswasser und demnächstige Kleisteransammlung ein Verstopfen und
dessen nicht übersehbare Folgen befördert; auch rosten sie aus demselben Grunde
leicht durch.
Ferner muſs der Staubsammler selbst so angeordnet werden, daſs derselbe sich in ganz
kurzen Pausen reinige und das gesammelte Mehl und Staub sofort in Säcken aufgefangen
wird. Graupenmühlen, namentlich die heutzutage nur noch in Frage kommenden sogen.
holländischen Graupenmühlen, sind aus verschiedenen Gründen noch feuergefährlicher
als Mahlmühlen. Einmal ist das daselbst verarbeitete Roherzeugniſs in seinen Theilen
feuergefährlicher, weil die Gerstenschale mehr Cellulosetheile enthält, die bei dem
eigenthümlichen Vergraupungsverfahren durch Abschleifen viel feiner zertheilt werden
als Mahlgut. Dann ist aber auch die Arbeitsmaschine, der sogen. Graupenholländer, zu
Folge seiner schleifsteinartigen Construction und Arbeitsweise unter starker
Pressung, leichter einer Erwärmung ausgesetzt. Endlich aber muſsten diese Maschinen
früher durch Menschenhand bedient werden, wodurch oftmals zu langes Verweilen des
Arbeitsgutes in der Maschine stattfand und in Folge dessen Erhitzungen desselben
ungemein leicht eintreten konnten, wenn der Arbeiter nicht ganz zuverlässig war.
Das Entstehen von Feuerfunken in der Abeitsmaschine ist bei der Graupenmaschine von
Martin in Bitterfeld zu vermeiden gesucht, einmal durch gute
Vorreinigung der Gerste, wodurch verhindert werden soll, daſs harte Körper zwischen
die Arbeitsflächen gelangen, als ferner durch gute Lagerconstruction mit
selbsthätiger Schmierung, sodann durch die Zuführung frischer Luft zwischen die
Arbeitsflächen mittels Aspiration und endlich Anwendung einer selbsthätigen
Beschüttung und Entleerung der Maschine.
Etwaiges Zünden eines Funkens wird durch eine Aspirationsvorrichtung mit Staubsammler
vermieden. Der Staubsammler wird möglichst nahe am Graupenholländer angeordnet, und,
wenn dies nicht direkt über oder neben demselben geschehen kann, durch ein wagerecht
liegendes Holzrohr mit Schnecke mit demselben verbunden. Beste Reinigung, welche den
Filter des Staubsammlers in ganz kurzen Zwischenräumen reinigt, so daſs sich nie
eine gröſsere Menge Staub in diesem Apparate aufsammeln kann, zeichnet denselben als
hier besonders zweckentsprechend aus. Vom Filter fällt bei der Reinigung der Staub
direkt in Säcke. Vom Staubsammler bis zum Exhaustor wendet er hölzerne oder eiserne
Verbindungsrohre an; in diesen läuft nur Luft um.
Der Staubsammler von M. Martin in Bitterfeld besitzt ein
sackartiges Filter, welches durch plötzliche Umsteuerung des Luftstromes umgestülpt
wird, so daſs unter dem Gegenwinde die Reinigung des Filters vollzogen wird.
Der Windstrom geht auf seinem Wege nach dem Gebläse bei einer Anordnung durch ein auf
umlaufender Trommel befestigtes Filter (Fig. 50), bei einer
zweiten Anordnung durch Filter, welche auf einem stillstehenden viereckigen Rahmen
angebracht sind (Fig. 51). Bei der ersteren Ausführung erfolgt das Umstülpen des Filters
durch Zuführung eines Gegenstromwindes durch ein Rohr d
von der Mitte der umlaufenden Trommel (vgl. Fig. 50), bei der anderen
Ausführung tritt der Gegenwindstrom von oben zwischen die aufrecht stehenden
Filterrahmen. Dieses Spiel geht abwechselnd in einzelnen Filterabtheilungen vor
sich, und zwar wird bei dem runden Filter je eine der 6 Abtheilungen stets
gereinigt, während die anderen saugen, bei dem viereckigen dagegen wird stets die
Hälfte Anzahl der Filterrahmen gereinigt, während der andere Theil saugend
arbeitet.
Bei dem runden Filter, welches für kräftigeres Saugen bei kleinerer Filterfläche
bestimmt und construirt ist, sind im Inneren der einzelnen Abtheilungen noch Hebel
m angebracht., die durch lose Fäden mit den
einzelnen Filterfalten, welche das Umstülpen begrenzen, verbunden sind. Diese Hebel
haben den Zweck, während der Reinigung das Durchschlagen oder Umstülpen der Falten
zu wiederholen, wodurch die Reinigung selbstredend vollkommener erfolgt. Dies wird
bewerkstelligt dadurch, daſs die genannten Hebel m
durch die Drehung der Trommel, indem sie auf einem an der feststehenden Wand des
Apparatgehäuses befestigten Zahnkranze n entlang gleiten, die
Filterfalten gegen den Luftstrom heben und unter Pressung der Luft wieder fallen
lassen.
Bei dem viereckigen Filter ist diese Anordnung des öfteren Umstülpens auſser
Anwendung gelassen, dafür aber auf ein öfteres Umsetzen der Reinigungsarbeit Bedacht
genommen. Da auſserdem dabei die Filterflächen viel gröſser sind, so hat sich dies
für die Praxis eben auch gut bewährt und ist es dadurch auch möglich geworden, die
einzelnen Filter, ohne den Betrieb zu stören, herauszunehmen, um etwaige Störungen
leichter beseitigen zu können. Beide Arten der Anordnung, die im Prinzip also gleich
sind, haben sich gut bewährt, und würde die Wahl der einen oder anderen Art in der
Hauptsache nur davon abhängig sein, ob mit stärkerem Luftstrome, d.h. gröſserer
Luftleere hinter dem Filter, zu arbeiten vorzuziehen ist, oder gröſsere Luftmengen
mit geringerer Pressung arbeiten sollen.
Das Umsteuern der Luftbewegung, welches also in demselben Moment zu erfolgen hat, wo
die Reinigung für jede Filterabtheilung beginnen soll, geschieht bei dem runden
sogen. Trommelfilter dadurch, daſs ein mit der Drehung der Trommel sich bewegender
Gewichtshebel von Zeit zu Zeit frei wird und vermöge seines Eigengewichts plötzlich
in senkrechte Stellung fällt, wodurch das Rohr d und
die zu reinigende Filterabtheilung in Verbindung tritt, während gleichzeitig durch
denselben Vorgang die gereinigte Filterabtheilung wieder abgesperrt wird. Beim
viereckigen sogen. Rahmenfilter geschieht die Umsteuerung durch Verstellen der
oberhalb der Filterbehälter befindlichen Klappen c,
wodurch jedesmal die eine Hälfte der Filterabtheilungen (deren Zahl beliebig groſs
gewählt werden kann) gegen die äuſsere Luft sich öffnet, während die andere
abgeschlossen wird; die Bewerkstelligung dieses Vorganges erfolgt durch Riemen oder
Ketten ohne Ende, welche, von der Exhaustorwelle aus in Bewegung gesetzt, durch
eingeschaltete Knoten oder Stäbe als sogen. Mitnehmer die zeitweise Bewegung der
Klappen vollziehen. Die mit punktirten Linien angedeutete Ausführung dieses
Mechanismus zeigt die betreffende Skizze; ebenso ist aus der entsprechenden Skizze
des runden Filterapparates zu ersehen, in welcher Weise die Bewegung der Trommel und
der von dieser zur Function gebrachte beschriebene Mechanismus der Umsteuerung
geschieht.
Die Buchstaben in Fig. 50 haben folgende Bedeutung: a
Einströmungsrohr von der Arbeitsmaschine, b Filter. c1 bis c6 6 Abtheilungen. d Rohr für frische Luft mit Einströmungsöffnung für die
frische Luft. Das Schluſssegment für die reinigende Abtheilung ist in der Zeichnung
schraffirt. m 6 Hebel zur Filterreinigung. n Zahnstange. o Hebel mit
Gewicht. s Sackstutzen.
In Fig. 51
bedeutet: a1 und a2 Einströmungsrohre
für staubreiche Luft. b2, b3 und b4 Filter
(herausnehmbare), b2
und b4 in Thätigkeit.
c 4 Klappen in den Ausströmungskanälen, d Exhaustor mit Antriebsscheibe, f 2 Einströmungskanäle für frische Luft. s1 und s2 2
Staubtransportschnecken. r1 und r2 2
selbstschlieſsende Sackstutzen.
Die meisten Staubfänger, von welchen eine groſse Anzahl verschiedener Ausführungen
bestehen, beruhen auf dem geschilderten Vorgange. Abweichend ist das Verfahren der
Reinigung der Filtertücher durch Klopfen.
Eine besonders gut durchdachte Ausführung (Patent Jaacks und
Behrens Nr. 38 396) war von Nagel und Kamp in
Hamburg ausgestellt.
Diese Patentfilter bestehen aus einfachen Filtertuchschläuchen von ungefähr der Länge
der jedesmaligen lichten Geschoſshöhe; dieselben sind mit ihren unteren offenen
Enden an den geeigneten Staubraum angeschlossen, während dieselben am oberen Ende
durch Holzdeckel geschlossen und mittels eines an zwei Tauen über Rollen hängenden
Gewichtes hoch und straff gehalten werden. (Vgl. 1889 271
* 538.)
Die Filterschläuche werden in kleineren oder gröſseren Gruppen je nach Ausdehnung der
Anlage gereinigt. Fig. 52 zeigt zwei vierfache Systeme, bei welchen je 4 Schläuche
gleichzeitig wie folgt gereinigt werden:
Eine endlose Kette, in welcher sich ein Mitnehmer (Vorsprung) befindet, wird über
Rollen in geeigneter Weise geleitet und durch ein kleines Kettenvorgelege so langsam
bewegt, daſs der Mitnehmer nach Bedürfniſs alle 5 bis 10 Minuten einen Kreislauf
beendet. Der Mitnehmer hakt beim Vorübergehen des Gewichts unter die gabelförmige
Klinke a desselben und hebt das Gewicht, auch
gleichzeitig mit demselben, mittels des Stellringes b
auf der Stange c, den Verschluſstrichter so lange, bis
die Klinke d in die Kerbe der Stange c fällt und so den Trichter mit darin befindlichem
Sitzventil geschlossen hält. Gleichzeitig wird auch die Klinke a durch die Nase e
ausgelöst und fällt das Gewicht in Folge dessen zurück. Die bis dahin blasebalgartig
in sich zusammengesunkenen Filterschläuche werden dann plötzlich emporgeschnellt und
straff gezogen. Die hierdurch entstehende kräftige Erschütterung der einzelnen
Filtertuchfäden, in Verbindung mit dem in Folge der plötzlichen Raumvergröſserung
von auſsen nach innen strömenden Gegenwind, bewirken eine gründliche Reinigung von
anhaftendem Staube.
Der so abgestoſsene Staub lagert sich nun ruhig auf dem Sitzventil im Trichter ab und
fällt in dem Augenblicke, wo der Mitnehmer der Kette die Klinke d auslöst und der Trichter durch sein Eigengewicht
herunterfällt, durch das dann ebenfalls geöffnete Sitzventil direkt in einen Sack
oder Schnecke.
Sollen diese Filter für Saugewind arbeiten, so müssen dieselben mit einer luftdichten
Kammer umgeben werden, aus der dann abgesogen wird. Es wird die beim Reinigen des
Filters dann noch nöthige Schlieſsung und spätere Wiederöffnung des Saugeluftrohrs durch eine Drosselklappe
mittels der Stange c direkt bewirkt.
Die Schlauchlänge beträgt bei 3m Geschoſshöhe etwa
2m,5, und haben vier solche Schläuche eine
dauernd, gleichmäſsig wirksame Fläche von zusammen etwa 11qm,5.
Von den mehrseitig ausgestellten Müllereimaschinen ist wenig Neues zu berichten. Es
sollen deshalb nur die drei vorgeführten
Mischmaschinen
noch besprochen werden, weil durch dieselben das Prinzip einer
völlig staubfreien Mischung sehr scharf zum Ausdrucke gebracht ist. Die
Mischmaschinen dienen bekanntlich nicht nur den Zwecken der Müllerei bezieh.
Bäckerei, um ein möglichst gleichmäſsig gemischtes Mehl aus verschiedenen Mehlsorten
herzustellen, sondern finden auch vielfach Anwendung in der Cement- und
Kunstdüngerfabrikation u.s.w.
Die Mischmaschine, System Weber-Zeidler, welche von R. Mager in Görlitz ausgestellt ist, besteht, wie Fig. 53 Taf.
14 zeigt, aus einem gewöhnlichen Mehlbehälter, an dessen Decke eine Schnecke a ohne Kasten angebracht ist. Am vorderen Ende steht
auf der Schnecke der Einschüttrumpf. Der Behälter ist unten nicht durch einen festen
Boden, sondern durch Walzen b abgeschlossen. Unter
diesen befindet sich in der ganzen Länge derselben eine Schnecke c mit zunehmendem Fassungsraume, welche in den Rumpf
eines Förderwerkes d mündet. Letzteres stellt die
Verbindung zwischen der unteren und der oberen Schnecke her. In dem Behälter sind
über den Walzen Bretter – Flächen e – gegen die Wand
der Kiste schräg stehend, derartig aufgehängt und unter einander verbunden, daſs
sich die Schräge derselben von auſsen beliebig verstellen läſst. Unmittelbar vor dem
Förderwerke ist an dem Boden der unteren Schnecke ein Sackrohr mit Schieber und
Klappe angebracht. Der Einschüttkasten kann auch unten am Förderwerke, das
Absackrohr oben an dem äuſseren Theile der Vertheilungsschnecke angebracht werden,
je nachdem es die Verhältnisse der Mühle erfordern.
Soll Mehl gemischt werden, so wird zuerst die obere Schnecke in Betrieb gesetzt. Die
zu mischenden Sorten werden in den Einschüttrumpf gebracht, von wo die Schnecke das
Mehl nach dem Behälter fördert. Hier fällt es am Ende des kurzen Schneckenbodens
herunter und lagert sich zwischen den schrägen Flächen bis an die Decke hinauf.
Sobald das Mehl die Schnecke erreicht, wird das noch weiter hinzukommende in der
Längsrichtung fortbewegt, bis der Behälter alle zu mischenden Sorten aufgenommen
hat, jedenfalls bleibt es gleichgültig, in welcher Reihenfolge und in welchem
Verhältnisse eingeschüttet wird, ob z.B. das Mehl unmittelbar aus den
Sichtemaschinen oder aus Säcken kommt, es ist nur erforderlich, daſs der Behälter
alle zu mischenden Sorten überhaupt enthält.
Beginnt die Mischung, so wird die untere Schnecke, das Förderwerk und die Walzen
gleichzeitig in Betrieb gesetzt. Sobald letztere sich zu bewegen anfangen, wird das
auf ihnen lagernde Mehl in feinen Strahlen, jedoch auf der ganzen Länge der Walzen
durch den Walzenboden hindurch in die untere Schnecke gestreut. Dadurch kommen aus
jedem Theile der Behältergrundfläche in jedem Augenblicke gleich viel Mehltheilchen
zusammen, so daſs am Ende der Schnecke eine innige Mischung entstanden ist, welche
die einzelnen Sorten in demselben Verhältnisse enthält, wie der Behälter. Etwa
vorhandene Klümpchen werden beim Durchgange durch die Walzen aufgelöst.
Dadurch besonders, daſs die verschiedenen Mehlsorten in feinen Strahlen auf und in
einander gestreut werden, wird die gleichmäſsigste Mischung hergestellt. Das Streuen
geschieht zwangsweise: jedes Körnchen wird auf die bestimmte Stelle gestreut, wo es
sich neben Körnchen anderer Sorten lagern und so auf das innigste mischen muſs. Das
verschiedene specifische Gewicht der einzelnen Mehlkörnchen aus dem Kern und den
äuſseren Schichten des Kornes beeinfluſst die Mischung nicht
Die Mischarbeit, deren Zeitdauer von dem Verhältnisse zwischen Fassungsraum des
Mehlbehälters und Gröſse des Walzenbodens abhängig ist, ergibt nach zwei- bis
dreimaligem Durchgange des Mischgutes ein tadelloses Erzeugniſs.
Da das Förderwerk das Mischgut aus der unteren wieder in die obere Schnecke bringt,
so mischt die Maschine ohne irgend welches Zuthun von auſsen ohne Aufsicht so lange,
bis der Schieber am Sackrohre gezogen wird und das Absacken beginnt. Aus dem
Sackrohre ist die Entnahme von Proben sehr leicht.
Die Mischarbeit erfordert keine Handarbeit. Der Behälter wird von den Arbeitern
niemals betreten. Die Maschine bringt sämmtliches Mischgut selbsthätig bis in das
Sackrohr; sie bleibt während der ganzen Arbeit vollständig geschlossen, weshalb kein
Verstauben und keine Verunreinigung des Mischgutes möglich ist.
Die schrägen Flächen, welche den Walzenboden von dem Drucke des Mehles entlasten,
werden für klumpiges, feuchtes Mehl steiler, für sehr trockenes flacher gestellt.
Das Einstellen der Flächen geschieht, während der Kasten gefüllt wird, und wird
durch auſsen an dem Behälter angebrachte Fausträder binnen weniger Minuten erledigt.
Für frisch gemahlene Mehle braucht die einmal erprobte Einstellung überhaupt nicht
mehr verändert zu werden, wie sich an den im Betriebe befindlichen Maschinen gezeigt
hat.
Die Mühlau'sche Mischmaschine (Patent Nr. 41534), welche
von der Maschinenfabrik Aug. Deutloff in Würzen
ausgestellt war, besteht aus einer hölzernen Trommel, welche mit zwei guſseisernen
Laufkränzen auf vier Rollen sich dreht und durch letztere und ein damit verbundenes
Rädervorgelege in Umlauf versetzt wird. Im Inneren der Trommel ist ein feststehender Schaufelrechen
angebracht, an dessen beiden Enden das Einschütt- und das Aussackrohr befestigt
werden. Das Mehl wird beim Umdrehen der Trommel stetig nach oben geführt und durch
den schräg gestellten Rechen geworfen, dabei vertheilt und gemischt.
Die dritte Mischmaschine war von Gebrüder Gawron in
Stettin ausgestellt.
Oberhalb der Kasten a (Fig. 54 und 55 Taf. 14)
liegen in der Längsrichtung eigenthümlich construirte Apparate f1, f2, f3, genannt
„Vertheiler“, weil sie mit groſser Geschwindigkeit auch die kleinsten
Posten (Theile) der zu mischenden Materialien gleichmäſsig auf die ganze Länge der
Kasten vertheilen, so daſs also in jeder Abtheilung gleichmäſsig viel der
verschiedenen zu mischenden Massen ist.
Die Mischung geht nun folgendermaſsen vor sich:
Durch einen Elevator d oder Einschüttrumpf wird das zu
mischende Material unabhängig von der Beschaffenheit und Farbe in beliebiger
Reihenfolge, wie die Säcke zufällig in die Hand kommen, auf die Vertheiler gebracht
und diese vertheilen nun die zu mischenden Materialien gleichmäſsig auf die ganze
Länge der Kasten a, so daſs diese in jedem Fache g in gleichem Verhältnisse über einander zu liegen
kommen, wie dies in zwei der Abtheilungen g durch
verschiedene Schraffirungen gekennzeichnet ist.
Sind die Kasten nun gefüllt bezieh. das zu mischende Material aufgeschüttet, so wird
der Inhalt eines jeden Faches g gemischt und zwar wie
folgt: Man öffnet von irgend einem Fache g die Klappe
oder Schieber c, dann wird der Inhalt desselben durch
die darunter liegende Schnecke b wieder in den Elevator
d und von diesem auf den dritten Vertheiler f3 gebracht, durch
welchen das Material der Länge der Maschine nach in gleichmäſsig über einander
liegende Schichten in den Behälter h gebracht wird und
nach Oeffnen der Klappen i in die darunter liegende,
langsam gehende Schnecke k und von da in den Auslauf
e gelangt, wo es vollständig gemischt abgefangen
wird. Soll nur Mehl gemischt werden, dann wird der Vertheiler f3 mit dem Behälter h und Schnecke k
überflüssig, da das Mehl einer Abtheilung der Kasten a
schon durch die darunter liegende Schnecke und den Elevator genügend gemischt
wird.
Das Prinzip dieser Maschine ist folgendes: Die Materialien werden erst schichtweise
in gleichmäſsigem Verhältnisse über einander gelagert und dann werden die durch die
senkrechten Zwischenwände getrennten gleichmäſsigen Theile einzeln gemischt, wodurch
allein ein gleichmäſsiges Mischproduct des ganzen Quantums erzielt wird.
Kugelmühlen.
Die früher ausschlieſslich von den Kollergängen geleistete Arbeit der feinsten
Zerkleinerung und Vermahlung spröder Stoffe, wie Kohlen. Erden, Farben, Gyps, Cement
u.s.w., wird jetzt zu einem groſsen Theile von den sogen. Kugelmühlen geleistet,
welche in drei Ausführungen auf der Ausstellung vertreten waren. Die Kugelmühlen
haben insofern einen nicht zu unterschätzenden Vorzug vor den Kollergängen, weil sie
nicht, wie diese, Nebenmaschinen benöthigen, welche die zu vermählenden Stoffe auf
Korngröſse verarbeiten; es fallen also die Vorbrecher, Siebvorrichtungen u.s.w.
fort. (Vgl. 1889 274 361 * 397.)
Im Allgemeinen bestehen Kugelmühlen aus einem cylindrischen oder schalenförmigen
eisernen Gefäſse, der Trommel, welche in drehende Bewegung gesetzt wird, wodurch ein
Rollen und theilweises Fallen der in derselben befindlichen Eisenkugeln von
verschiedenem Gewichte bewirkt und auf diese Weise ein Zerkleinern bezieh.
Pulverisiren des aufgegebenen Mahlgutes bewirkt wird. Wenn auch im Prinzip die
Constructionen der Kugelmühlen einander gleichen, so weichen dennoch ihre
Einzelheiten wesentlich ab, weshalb auch die quantitative und qualitative
Leistungsfähigkeit, wie nicht minder die allgemeinere Verwendungsweise der neueren
Ausführungen bedeutende Unterschiede unter einander aufweisen.
Die bereits 1889 274 * 398 erwähnte Kugelmühle, welche vom
Grusonwerk in Buckau-Magdeburg ausgestellt war,
wird durch einen Schüttrumpf mit Stücken bis etwa zu Fruchtgröſse angefüllt. Die
Stücke gelangen durch die Stirnwand der Trommel auf die im Inneren der letzteren
befindlichen Kugeln, welche, nachdem die Mühle in Umdrehung versetzt ist, die Stücke
allmählich zerkleinern und vermählen.
Was die eben beschriebene Zuführung des Mahlgutes in das Innere der Trommel betrifft,
so machte man die Beobachtung, daſs die Nabenspeichen der letzteren dieselbe
auſserordentlich erschwerten. Wollte man diesem Uebelstande durch Verminderung der
Speichen entgegentreten, so hatte dieses zur Folge, daſs die Kugeln an der Nabe aus
der Trommel hinaussprangen. Namentlich der letztere Uebelstand machte sich in
empfindlichster Weise geltend, indem die Kugeln in den Einlauftrichter geriethen und
dessen Wandung in Folge der durch die rotirende Welle erhaltenen Pressung
zerstörten. Man hat diese Miſsstände in wirksamster Weise dadurch beseitigt, daſs
man die Nabenspeichen auf zwei verminderte und diesen die Form von breiten
Schraubenflügeln gab, welche einerseits das Mahlgut bei Drehung der Trommel sicher
in das Innere der letzteren einführen, andererseits aber verhindern, daſs die Kugeln
herausspringen, indem sie dieselben stets wieder zurückwerfen, wenn sie in den
Schraubengang gerathen. Diese Neuerung ist dem Grusonwerk durch das D. R. P. Nr. 47477 geschützt worden.
Das von den Kugeln zerschlagene und zerriebene Material fällt durch die Zwischenräume
des aus Roststäben zusammengesetzten Trommelmantels hindurch auf ein System von
Siebblechen. Diese Siebbleche umgeben den cylindrischen Rost conachsial und haben den
Zweck, die gröbsten Griese abzusieben und durch einige in den Roststäben befindliche
Kanäle zur nochmaligen Vermahlung in die Trommel zurückzuführen. Das durchgesiebte
feinere Erzeugniſs wird durch die Metallgewebe d in
staubfeines und in etwas gröberes Mehl gesondert. Ersteres bildet das fertige
Mahlgut und fällt in den Auslauftrichter f des
Blechgehäuses, welcher die ganze Mühle staubfrei einhüllt, während letzteres durch
Schlitze in den Siebblechen und die Kanäle zugleich mit den zuerst abgesiebten,
groben Griesen von Neuem auf die Kugeln gelangt. Die zu vermählenden Stoffe
enthalten öfters Beimengungen – so führt beispielsweise die Thomasschlacke Stahl-
oder Eisentheile mit sich – welche, wenngleich sie die Leistungsfähigkeit der
Trommel nicht beeinträchtigen, doch das Innere der letzteren unnöthig beengen.
Derartige Stücke können durch eine Spalte entfernt werden, welche von der
verschlieſsbaren Oeffnung aus geöffnet werden kann; es genügt, die Mühle alsdann
einige wenige Male umgehen zu lassen, um die Trommel von solchen fremden Körpern
sowie etwaigen sonstigen Rückständen zu entleeren.
Um das Innere der Mühle zugänglich zu machen, sind Mannlöcher in den Stirnwänden des
Blechgehäuses bezieh. der Trommel angebracht. Das fertige Product fällt in den am
Auslauftrichter f angebrachten Sackstutzen und kann
somit ohne jede Staubentwickelung in Säcke verpackt Werden.
Alle einer Abnutzung unterworfenen Theile – die Kugeln, die Roststäbe,
Vermahlenes Material
Nummer der angewendeten
Siebgewebe(gleich der Anzahl der Maschen auf den Zoll engl.)
10
20
40
60
70
80
90
130
Leistung in der Stunde in Kilogrammen
Asphalt
900
–
–
–
–
–
–
–
Cement-Klinker
–
–
–
–
650
600
550
–
Cement-Klinker mit Schlacken- Granalien
gemischt
–
–
–
–
–
–
750
–
Cement-Rohmaterial
–
1250
–
–
–
450
–
–
Chamotte
1500
1200
–
–
–
–
–
–
Koks für Gieſsereizwecke
–
–
–
300
–
–
–
–
Guſseisenspäne
1750
750
250
150
–
–
–
–
Gyps, gebrannt
–
1100
800
–
–
–
–
–
Gyps, ungebrannt
–
–
–
–
–
600
–
–
Hochofenschlacke, granulirt
–
–
–
–
–
–
400
–
Holzkohle (Kiefer)
–
–
400
–
–
–
–
–
Kalk, gebrannt
–
–
–
–
1150
–
–
–
Knochenkohle
–
–
–
600
–
–
–
–
Marmor
–
–
–
–
–
–
500
–
Schmirgelsteine, Rohmaterial
325
–
275
–
–
–
–
–
Schwerspat
–
–
1600
–
–
–
–
–
Steinkohlen, feucht
–
–
500
–
–
–
–
–
Thomasschlacke
–
–
–
725
650
550
450
–
Tonschiefer
–
–
825
–
–
–
–
–
sowie die aus einzelnen Segmenten zusammengesetzten
Schutzplatten der Stirnwände, sind aus Stahl oder Hartguſs angefertigt.
Eine Kugelmühle Nr. 4 liefert umstehende Vermahlungsergebnisse.
Für Thomasschlacke beträgt die stündliche Leistung der Kugelmühle Nr. 4 unter
Anwendung von Siebgewebe Nr. 85 etwa 550k. Das
erhaltene Mehl hinterläſst auf dem 1600 Maschen auf 1qc enthaltenden Normalsiebe Nr. 100 etwa 8 Proc. Rückstand. Gerade bei der
stets zunehmenden Wichtigkeit der Thomasschlacke für die Düngerfabrikation dürfte
sich nach dieser Richtung der Kugelmühle ein weites Gebiet noch erschlieſsen.
Nicht minder wichtig ist die Kugelmühle für die Cementfabrikation. Die bei den
Versuchen zermahlene Rohmasse war thonhaltiger Kalkstein, der mit 12 Proc. reinem
Thon vermischt der Kugelmühle aufgegeben wurde. Das mit Siebgewebe Nr. 20 erhaltene
Ergebniſs hat beim Durchsieben auf dem Normalsiebe Nr. 80 etwa 60 Proc. (750k) fertiges Rohmehl und 40 Proc. (500k) Rückstände, die aufs Neue vermählen werden
müssen. Wird dagegen die Kugelmühle mit Siebgewebe Nr. 80 umspannt, so liefert sie
fertiges Mehl, aber nur 450k in der Stunde gegen
750k nach dem ersten Verfahren. In beiden
Fällen ist die Beschaffenheit des erhaltenen Mehles gleichwerthig, und zwar beträgt
der Rückstand desselben auf dem 5000 Maschen auf 1qc enthaltenden Normalsiebe Nr. 180 etwa 20 Proc., während auf dem
900maschigen Normalsiebe Nr. 80 natürlich gar kein Rückstand verbleibt.
Bei der Kugelmühle nach Patent Jenisch (1889 274 * 397) von Herm. Löhnert
in Bromberg wird die Trommel selbst aus acht einzelnen 13mm starken, mit 25mm starken Stahlpanzern versehenen, gebogenen Auf lauf flächen gebildet,
welche mit 8 bis 10mm groſsen Löchern versehen und
so angeordnet sind, daſs sie sich vom Umfange der Trommel nach innen gegen die Achse
hin erheben; es liegt somit das Ende der einen Platte immer um einige Zoll höher als
der Umfang der folgenden. Diese Erhebung der Auflaufflächen nach innen bezweckt, die
Kugeln vom Kreislaufe abzulenken, sie bei jeder Achteldrehung eine Stufe hinabfallen
zu lassen und dadurch ihre mahlende Wirkung zu erhöhen.
Hinter jeder der Auflaufflächen liegt in gleicher Richtung ein Stahlblechsieb mit 0,5
bis 2mm Löchern:, dasselbe kommt indessen nur bei
sehr hartem Materiale, wie Thomasschlacke, Cement u.s.w. zur Verwendung, und zwar
als Schutzsieb für das darunter liegende feine Sieb. Dieses äuſsere Sieb wird je
nach dem gewünschten Feinheitsgrade des Products aus Messing- oder Stahldrahtgewebe,
geschlitzten oder gelochten Kupfer- bezieh. Stahlblechen hergestellt und besteht
aus, mit dem entsprechenden Siebe bezogenen, acht Stück einzelnen Rahmen.
Das Mahlgut hat demnach zunächst die 8 bis 10mm
groſsen Löcher der inneren Auflaufflächen, dann die 0,5 bis 2mm groſsen Löcher der Schutzsiebe und endlich die
Maschen, Schlitze oder Löcher der feinen äuſseren Siebe zu passiren, fallt während des Betriebes
durch die aus der Erhebung der Auflaufflächen und Schutzsiebe gebildeten Oeffnungen
in die Trommel zurück und wird der fortgesetzten Mahlung unterworfen. Die Trommel
wird mit einer nach unten trichterförmig abschlieſsenden Verkleidung umgeben, welche
die Verstäubung verhindert und das Mahlproduct in angehängten Säcken oder darunter
gestellte Wagen oder Fässer abliefert.
Diese sogen. Kugelfallmühle wird in zwei Gröſsen, und zwar in Trommeldurchmessern von
1600mm bezieh. 1800mm hergestellt und sind zum Betriebe der 1600mm im Durchmesser groſsen Mühle 6 bis 8
(14 indicirte) erforderlich. Die Leistung in Cement und Thomasschlacke beträgt 10
bis 16 Centner in der Stunde, je nach Beschaffenheit des Materials, bei staubfreier
Arbeit.
Das in der Thomasschlacke enthaltene Eisen soll den Betrieb nicht beeinträchtigen;
dasselbe wird je nach Bedürfniſs alle 10 oder 20 Stunden aus der Mühle entfernt.
Zum Vermählen von Gold- und Silbererzen haben die Mühlen mehrfach Verwendung
gefunden, so in den Bergwerken Siebenbürgens, wo beim Mahlen auf nassem Wege eine
Leistung von 40 bis 50 Centnern stündlich erzielt wurde. Beim Mahlen trockener Erze
in Chile werden 12 bis 14 Centner Feingut stündlich verzeichnet.
Die Kugeln sind dem Verschleiſs am meisten ausgesetzt; der Verbrauch derselben bei
Thomasschlacke und Cement stellt sich auf fast 1 Pf. für 1 Centner des gewonnenen
Mehles. Dagegen zeigen die Auflaufflächen eine äuſserst geringe Abnutzung; sie sind
ebenso wie die Seitenwände mit stählernen Schutzplatten belegt, welche, jede
einzeln, leicht und ohne groſse Kosten, ersetzt werden können.
Die Drahtgeflechtsiebe sind derselben Abnutzung unterworfen, wie die bei den
bisherigen Mahlsystemen angewandten Cylindersiebe; die Kupferschlitzsiebe sind
indeſs bedeutend widerstandsfähiger.
Die dritte Kugelmühle war in einem besonderen Gebäude sammt einer zugehörigen
Dampfmaschine von Gebr. Sachsenberg in Rosslau
ausgestellt. Die in Fig. 56 und 57 Taf. 18 abgebildete
Mühle besitzt eine aus einem doppelten Mantel gebildete Trommel A, von der der äuſsere aus Schmiedeeisen, der innere,
die eigentliche Mahlfläche, aus Guſsstahl besteht; letztere kann, wenn abgenutzt,
ausgewechselt werden. Die aus Schmiedeeisen bestehenden Seitenwände sind im Inneren
der Trommel ebenfalls mit Stahlplatten gepanzert, so daſs auch sie nach ihrer
Abnutzung durch neue ersetzt werden können. Die Mühle läuft mit ihren Hohlzapfen BB1 in Pockholzlagern.
An den Zapfen B schlieſst sich der mit einem durch Filz
gedichteten Deckel versehene Fülltrichter D an, in
welchen der Rohstoff geworfen und in der Trommel unter der Wirkung der Kugeln
zerkleinert wird. Das Mahlgut geht durch die Löcher des Mantels E, passirt zunächst das aus gelochtem Eisenbleche bestehende Schutzsieb
F1, fällt von hier
durch das eigentliche Feinsieb F, welches das Mahlgut
in dem gewünschten Feinheitsgrade fertig abliefert, indem es auf der schrägen Fläche
des äuſseren Mantels C entlang in den an der
Stirnfläche der Trommel liegenden gekrümmten Kanal G
gleitet, der es bei der Umdrehung der Mühle dem Hohlzapfen B1 zuführt, an welchen sich die mit Filz
abgedichtete Kapsel H anschlieſst. Von dieser zweigt
sich das mit Absperrschieber versehene Ablaufrohr J ab,
durch welches das Mahlgut in einen dicht damit verbundenen Sack abgeführt wird. Die
Siebgröbe läuft über die geneigte Fläche des Siebes F
gleitend in den Kanal G1, mit G parallel laufend, welcher sie in das
Innere der Trommel zurückführt, bis sie hinreichend zerkleinert das Feinsieb
passiren kann. Die Mühle wurde in der Ausstellung durch eine eigens dafür
aufgestellte Dampfmaschine von 220mm
Kolbendurchmesser und 480mm Hub betrieben, welche
100 Umdrehungen in der Minute macht, wobei die Mühle in Folge des angebrachten
Rädervorgeleges mit 24 Umdrehungen in der Minute umläuft. Die Vorgelegewelle der
Mühle ist mit der Kurbelwelle der Dampfmaschine durch Vermittelung einer Addyman'schen Frictionskuppelung verbunden. Um jede
Spur von Staub aus dem Mühlenraume zu entfernen, ist Vorsorge getroffen, daſs auch
der geringe Staub, der beim zeitweisen Oeffnen der Füllöffnung der Mühle und beim
Abhängen des gefüllten Sackes entweicht, durch einen von der Maschine mitbetriebenen
Schraubenventilator mittels der an den betreffenden Stellen von oben herabhängenden
Blechröhren abgesaugt und in die im Dachraum des Gebäudes untergebrachte Staubkammer
geführt wird.
Tafeln
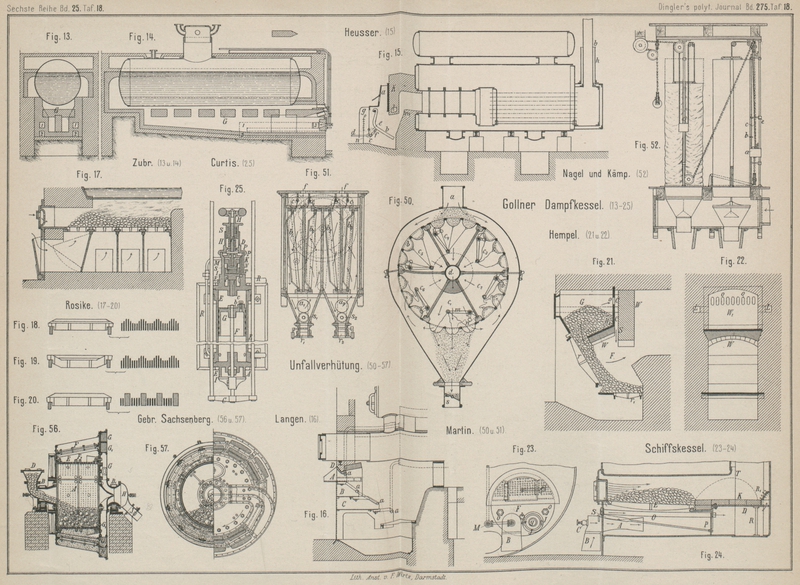