Titel: | Neuerungen in der Tiefbohrtechnik von E. Gad in Darmstadt. |
Autor: | E. Gad |
Fundstelle: | Band 278, Jahrgang 1890, S. 145 |
Download: | XML |
Neuerungen in der Tiefbohrtechnik von E. Gad in
Darmstadt.
Mit Abbildungen auf Tafel
10.
Gad, Neuerungen in der Tiefbohrtechnik.
Der demnächst erscheinende IV. Band der Tiefbohrkunde von Tecklenburg, das Seilbohren behandelnd, wird
als sehr zeitgemäſs zu begrüſsen sein, da die in Teplitz mittels der pennsylvanischen Seilbohrmethode im Betrieb befindliche Tiefbohrung gerade das Interesse
weiter Kreise in Anspruch nimmt. Die bisher in Teplitz erzielten Erfolge stehen
durchaus im Einklang mit den Resultaten, die auf Grund aller bisherigen Erfahrungen
in dem angeführten Werke niedergelegt sind. Die in den wagerecht gelagerten milden
Gebirgsschichten Pennsylvaniens allein herrschende Seilbohrmaschine arbeitet
vorzüglich in gleichartigen Formationen Europas, überwindet aber nur unvollkommen
die Schwierigkeiten, die hartes, geklüftetes und steil einfallendes Gestein ihr
entgegenstellen. Solange die Bohrung durch stark zersetzten Porphyr führte, ging sie
noch ganz befriedigend von Statten, als jedoch Ende Juli bei 204m Teufe fester Porphyr auftrat, mehrten sich in
bedenklicher Weise die Klemmungen, Seilrisse, Meiſselabnutzungen u.s.w., welche
Unfälle nur durch zeitraubende Fangarbeiten und Reparaturen, nebst nothwendigen
Verrohrungen zu heben waren. Da die Bohrung am 6. Mai begonnen ist und zur Zeit
(Oktober 1890) erst die Tiefe von 215m erreicht
hat, so ist das Versprechen des amerikanischen Bohrunternehmers Herrn John Webber, die geforderte Tiefe von 500m in 100 Tagen zu erreichen, nicht erfüllt worden.
Ob er die Tiefe überhaupt erreicht, bezieh. mit welchem Bohrlochsdurchmesser, steht
noch dahin. Uebrigens ist bei dieser Bohrung bisher niemals eine bessere
Tagesleistung als 5m Bohrfortschritt zu
verzeichnen gewesen, was als ganz mittelmäſsiger Erfolg anzusehen ist. Es soll dabei
weder der guten pennsylvanischen Maschine noch dem energischen, gewandten
amerikanischen Bohrmeister ein Vorwurf gemacht werden, denn es handelt sich eben um
die Leistungsfähigkeit der normal ausgeführten und bedienten Maschine. Der Teplitzer
Apparat arbeitet mit einer Schwerstange von 3000k
Gewicht, und es werden mit dem 1m,5 langen
Stahlmeiſsel in der Minute 40 bis 45 Schläge bei 62cm,5 Hubhöhe ertheilt.
Im Anschluſs seien zunächst andere wichtige Bohrarbeiten erwähnt.
Im nördlichen England, bei Middlesborough, hat
neuerdings die dort blühende Salzindustrie einen groſsen Aufschwung genommen, womit
neue Aufschlüsse von Salzlagern durch ausgeführte Tiefbohrungen in Verbindung;
stehen.
Das erste Salz wurde dort 1862 gelegentlich einer Tiefbohrung erschlossen, die in der
Nähe der Docks von Middlesborough 1859 zum Aufsuchen von Wasser für die dortigen
Eisenwerke in Angriff genommen war. Das Salzlager fand sich in einer Mächtigkeit von
etwa 30m in einer Tiefe von 367m,5.
Einzelne Bohrungen, wenn auch in geringer Zahl, sind im Laufe der nächsten Jahre
ausgeführt worden und haben Salz in gröſserer Tiefe von etwa 450m und in 25 bis 26m mächtigen Lagern angetroffen.
Die jüngste Bohrung daselbst bei Lackenby am Teeflusse,
die im November 1889 beendigt ist, wurde von der Firma Mather and Platt aus Manchester mittels deren eigenthümlichen
Seilbohrmaschine ausgeführt. Sie traf das 36m,5
mächtige Salzlager auf einer Tiefe von 514m. Das
Bohrloch beginnt mit einem Durchmesser von 30cm
und ist bis auf 26m,5 Teufe in dieser Weite
verrohrt. Darauf folgt ein auf 25cm verengter
Theil von 48m,8 Länge, und diesem ein wiederum
verengter Theil von 21cm Weite in 106m,7 Länge, ebenfalls mit Verrohrung. Die weitere
Bohrung von 182m Teufe an wurde im Rothsandstein
ohne Verrohrung mit 21cm Durchmesser beendigt. Der
geförderte Bohrschmant gab sehr interessante und überraschende Aufschlüsse über
Störungen der Liasformation in dortiger Gegend.
In der Schweiz beabsichtigt eine Gesellschaft im ganzen
Gebiet systematisch nach Steinkohlen zu bohren, die nach dem Urtheil
Sachverständiger dort vorhanden sein müssen. Man nimmt an, daſs der Bund 50 Proc.
der auf eine halbe Million Francs veranschlagten Kosten tragen wird. Die
Bohrversuche sollen zunächst längs des Jura beginnen.
Eine Tiefbohrung bei Hermsdorf in der Mark Brandenburg,
die bis 323m Tiefe durchgeführt wurde und bei
320m Teufe stark 3 proc. Salzsoole traf,
welche 1m über Oberfläche ausfloſs, hat auſserdem
sehr interessante geologische Aufschlüsse über die Formationen in der Mark ergeben.
Es wurden dabei z.B. zum ersten Mal die Schichten des Lias S in der norddeutschen Tiefebene nachgewiesen.
In neuerer Zeit hat die amerikanische Bohrfirma Gray, Bros.
and Co. in Milwaukee viele groſsartige artesische Brunnenbohrungen
ausgeführt. So waren z.B. im Staate Dakota im Beginn des Jahres 1890 etwa 25
artesische Brunnen in Tiefen von 300 bis 900m
fertig gestellt. Der ergiebigste dieser Brunnen befindet sich zu Yankton, Dakota,
und wirft einen 3m hohen Wasserstrahl mit einer
Wassermasse von etwa 12000 in der Minute aus. Zwei weitere bedeutende Brunnen sind
von derselben Firma in der Stadt Kaukauna, Wisconsin, und in Milwaukee selbst
abgebohrt.
Der Professor v. Rziha von der k. k. technischen
Hochschule in Wien hat zu akademischen Zwecken nachstehende Zusammenstellung von den
wirklich aufgelaufenen Kosten tiefer Bohrlöcher
gemacht:
Nr.
Namen
Teufem
Kosten1m
inM.
Gebirgsart
1234567891011121314
DiedenhofenRohrPurmallenArternGoslarWersenRheinfeldenSchöningen
I „ IICamminBöhmisch-BrodMondorfSperenbergSchladebach
*
180,0 302,0 303,2 314,0 329,8 404,0 426,0 520,0 574,0 580,0 697,4 730,01271,41748,4
60,0308,1 93,6158,0 70,7154,5356,8 87,0 52,2238,3318,2 73,8136,8121,4
Kalk.Buntsandstein.Schwimmendes und festes
Gebirge.Salzgebirge.Goslarer
Schiefer.Buntsandstein.Buntsandstein (Diamantbohrung).Trias
und Salz.Trias und Salz.Tertiär.Buntsandstein
(Diamantbohrung).Kohlengebirge.Salz.Salz.
Mittelwerth
558,7
148,1
* Derzeit das tiefste menschliche Eingreifen in die Erdrinde;
zwölf Mal so tief, als der Wiener St. Stefansthurm hoch ist.
So interessant diese Angaben sind, so bleibt bezüglich der praktischen Bedeutung doch
zu bedenken, daſs zum angemessenen Vergleich der Kosten noch andere Verhältnisse als
die angegebenen, z.B. Bohrlochsweite, Bohrmethode, vor Allem aber die Jahreszahl der
Bohrausführung maſsgebend sind. Was den letzten Punkt anbetrifft, so sind z.B. die
Bohrungen Nr. 7 bei Rheinfelden und Nr. 11 bei Böhmisch-Brod in den Jahren 1874–75
ausgeführt. Da diese beiden „Diamantbohrungen“ den gröſsten Kostenaufwand von
allen verzeichneten Arbeiten verursacht haben, so könnte man zu der Annahme versucht
sein, die Diamantbohrmethode als die bei weitem theuerste Methode zu betrachten. Dem
gegenüber bleibt aber zu bedenken, daſs die ebenfalls aufgeführte, im J. 1886
beendigte Bohrung von Schladebach – auch eine Diamantbohrung – erheblich geringere
Kosten verursacht hat.
Die Verwendung der Elektricität als Motor von Tiefbohr-
und Gesteinsbohrmaschinen (vgl. 1890 275 317) wird mit
der Zeit sicher an Bedeutung gewinnen. Es sei in dieser Beziehung zunächst der
elektrische Tiefbohr- und Tunnelbohrapparat von R.
Richard und R. Landon in Middlesex (Englisches
Patent Nr. 6690 vom 18. Mai 1886) erwähnt (Fig. 1 bis 3 Taf. 10).
Zur Ausführung von senkrechten Tiefbohrungen wird der elektrische Bohrapparat an
einem Drahtkabel, das die isolirten Leitungsdrähte enthält, in das Bohrloch
eingelassen. Die äuſsere Metallhülse a umgibt die
innere Motorhülse b. Diese letztere ist auf ihrem
Deckel mit dem Gestell c versehen, in dem die
Schwerstange d beweglich ist. Beim Aufstoſsen des
Bohrgeräthes auf die Bohrsohle sinkt die Schwerstange, deren Belastung durch die
äuſsere Hülse noch durch das Gewicht e Erstarkt ist,
nieder und preſst die vier Klingen f in die
Bohrlochswände, wodurch
die äuſsere Hülse a eine unwandelbare Stellung während
der Bohrarbeit erhält. Beim Aufholen des Instrumentes ziehen sich die Klingen von
selbst wieder ein.
Diese Klingen können indessen auch durch Nachschneiden ersetzt werden, die mittels
Federn oder Elektromagnete zu spannen bezieh. einzuziehen, sowie mittels
elektrischen Motors in Thätigkeit zu setzen sind. Innerhalb der Motorhülse befindet
sich im oberen Theil der elektrische Motor g, im
unteren Theil das Getriebe h, welches durch das
wagerechte Treibrad i die Drehspindel k in Drehung versetzt. Auf letztere ist die hohle
Bohrspindel l aufgesetzt, die durch die Nase der
Drehspindel, welche in eine innere Längsnuth der Bohrspindel eingreift, in der
Drehung mitgenommen wird. Die Auf- und Abbewegung der Bohrspindel bleibt dabei frei,
und diese wird durch Knaggen und Nasen von den lothrechten Triebrädern m aus bewirkt. Die Bohrspindel ragt durch die
Stopfbüchse n aus dem Boden der wasserdichten
Motorhülse heraus und nimmt am Schraubengewinde das Bohrgeräth auf. Dieses kann von
jeder beliebigen Form sein und auch zeitweise durch eine besonders construirte
Ventilbüchse mit archimedischer Schraube zum Auslöffeln des Bohrschmantes ersetzt
werden.
Für den Fall, daſs Diamantbohrung erforderlich ist, wird die Bohrspindel durch zwei
mit Diamanten besetzte Bohrkronen ersetzt, von denen eine innere in
entgegengesetzter Richtung von der umschlieſsenden äuſseren läuft, damit durch diese
gegenläufige Bewegung die Stabilität des Instrumentes bewahrt bleibt.
Die Verwendung des Apparates zur Tunnelbohrung ist in Fig. 2 und 3 dargestellt.
Fig. 4., Bd. 278, S. 148 Der Apparat wird in einem metallenen Schutzcylinder o auf einem Rollwagen p
montirt. Die Stellung der Rollräder q (Fig. 3) gestattet das
Abräumen des Berges vor Ort unter dem Fahrzeug her. Die Bohrung kann mit
verschiedenen Geräthen vor sich gehen, z.B. durch den Schrämmbohrer r. Die starke Schraubenvorrichtung s hinten am Apparat bewirkt den Vorschub. Zwei Mann
bedienen die Maschine beim Tunnelbohren, von denen der eine seine Stellung am
vorderem der andere am hinteren Theile derselben hat.
Eine elektrische Gesteins-Diamantbohrmaschine (Fig. 4) nach J. E. Storey's Patent wird neuerdings von der Sprague Electric Railway and Motor Co. in New York
angefertigt. Die Art des Betriebes ist aus der Darstellung ersichtlich.
Zweckmäſsigerweise wird die elektrische Leitung zugleich zur Beleuchtung
verwandt.
In jüngster Zeit stellt die genannte Fabrik auch elektrische Stoſsbohrapparate
her.
Eine andere amerikanische elektrische Gesteinsbohrmaschine von E. A. Sperry in Chicago hat neuerdings das D. R. P. Nr.
50912 vom 9. Juni 1889 erhalten.
Bei derselben dreht ein Elektromotor mittels einer Zahnräderübersetzung eine Kurbel,
die mittels einer elastischen Lenkstange mit dem Bohrer verbunden ist. Beim
Rückschube desselben wird eine Schraubenfeder zurückgedrückt, die beim Vorschübe des
Bohrers denselben gegen das Gestein wirft, und zwar unabhängig von der
Elektromotorwelle, weil diese mit den Kurbelscheiben durch eine beim Vorschübe sich
lösende Kuppelung verbunden ist. Die Maschine ist mit Umsetz- und
Vorschubvorrichtungen für den Bohrer versehen.
Speciell als Kohlenbohrapparat kommt noch die
elektrische Maschine von P. Arp in Betracht, die auf
der Kohlenzeche des Herrn A. Jackson bei Powelton in
Pennsylvanien in Betrieb ist. Die Elektricität wird durch eine Maschine von 7
erzeugt und durch Drähte etwa eine englische Meile weit nach dem Motor vor
Ort geleitet. Der Motor befindet sich in einem eisernen Rahmen, 60cm hoch, 2m,60
lang, 90cm breit. Unten bohren neun kleine Bohrer
vor, und dazwischen angebrachte stählerne Schneidestangen schneiden die zwischen den
Bohrlöchern stehen gebliebene Kohle nach, während mechanische Schaufeln die gelöste
Kohle abräumen. In 5 Minuten können zwei Räume von 10cm Fortschritt, 90cm breit und 1m,5 tief abgebohrt werden. Der etwa 540k schwere Apparat wird mit Stangen vorgeschoben
und läſst sich auf und ab bewegen, wobei er auch das übrige Gestein der Strecke
auſser dem Kohlenflötz zu schneiden im Stande ist.
Der elektrische Betrieb von Gesteinsbohrmaschinen hat
sich bisher indessen noch keineswegs so billig und einfach bewerkstelligen lassen,
daſs man in der Lage wäre, durchweg die bisher üblichen Betriebe mittels Dampf, Preſsluft oder Hand
durch ihn zu ersetzen. Die an Apparaten letztgenannter Art ausgeführten
Verbesserungen werden mithin wohl auf geraume Zeit hin noch eine wichtige Rolle
spielen.
Mehrfache bemerkenswerthe Verbesserungen hat die ältere Gesteinsstoſsbohrmaschine von
A. W. Daws und T. W. Daws in Laurvig, Norwegen
(altes Englisches Patent Nr. 10738 vom Jahre 1887) neuerdings durch dieselben
Erfinder erfahren, Fig. 5 (neues Englisches Patent Nr. 3691 vom 2. März 1889).
Zunächst sind die Durchlässe a und b in der Kolbenstange c so
lang, daſs sich
stets ein Ende eines jeden auſserhalb der Stopfbüchse d
befindet, wenn das andere Ende in Communication mit einem der Einlasse e öder f des
Ventilcylinders g steht. Dies bewirkt, daſs das
Bewegungsfluidum vom Ventilcylinder sicher erschöpft wird, während am anderen Ende
Bewegungsfluidum zuströmt.
Es ist ferner die Vorschubeinrichtung verbessert. Dieselbe findet selbsthätig dadurch
statt, daſs die Vorschubschraube h mittels des
Klauenrades i gedreht und vorbewegt wird, sobald das
Hebestück k den Rahmen l
und damit eine Sperrklinke anhebt. Das Hebestück k ist
wirbelnd mit der Kolbenstange c verbunden, so daſs die
letztere in der Drehung bei der wagerechten Bewegung nicht gestört wird. Das
Guſsstück m umschlieſst führend die Kolbenstange c und das Hebestück k,
während es sich gleitend in der Hülse n bewegt.
Schlieſslich ist auch die Verbindung des Bohrmechanismus mit dem Gestelle
vervollkommnet.
Eine neue Methode, um enge Tunnels in zweckmäſsiger Weise durch Sprengungen von
Bohrlöchern vorzutreiben, hat W. L. Saunders in New
York (Amerikanisches Patent Nr. 413869 vom 29. Oktober 1889) vorgeschlagen. Mit
einer beliebigen Gesteinsbohrmaschine werden etwa von ⅓ und ⅔ der Höhe des Ortes an
je ein Bohrloch geradeaus, aber das obere in steigender, das untere in fallender
Richtung gebohrt, und zwar bis jedes etwa die Höhe der First bezieh. die Ebene der
Sohle erreicht. Sobald diese Bohrlöcher vollendet sind, stellt man durch stoſsweises
Bohren mit einem breiten Meiſsel eine schlitzartige Verbindung zwischen den beiden
Bohrlöchern her. Es entsteht dadurch ein Schlitz im Gesteine, dessen Durchschnitt in
der Längsrichtung des Tunnels ein Trapez bildet. Kleinere im festen Gesteine in der
Nähe der Tunnelwände angesetzte Bohrlöcher finden alsdann in der Richtung auf den
Schlitz beim Abthun der Schüsse ihre kürzeste Widerstandslinie, wodurch der Tunnel
durch eine möglichst geringe Zahl von Schüssen vorgetrieben werden kann.
Zwei wirksame Gesteinsbohrmaschinen, welche hauptsächlich in offenen Steinbrüchen zum
Abbohren senkrechter Bohrlöcher gebraucht werden, sind in Amerika von J. F. Dittmann in Pittsburg (Amerikanisches Patent Nr.
417004 vom 10. December 1889) und von J. Cody in New
York (Amerikanisches Patent Nr. 418449 vom 31. December 1889) erfunden worden.
Bei dem ersten dieser Apparate (Fig. 6) ist der
Bohrmeiſsel a von beliebiger Form an der runden
Bohrstange b angeschmiedet. Diese sitzt in der
Bohrspindel c und wird durch die Stellschraube d gezwungen, die Drehung der Bohrspindel mitzumachen.
In senkrechter Richtung, also in der Richtung des Stoſses erhält die Bohrstange
festen Halt durch den Splint e, der je nach der
erforderlichen Lauge des Bohrhubes in verschiedene Splintlöcher der Bohrstange
eingesteckt werden kann.
Die stoſsende Auf- und Abwärtsbewegung der Bohrspindel bewirkt die Kurbelscheibe f mit den Daumen g und h, die hebend unter die Reibungsrollen i und k greifen und
dieselben an der Stelle des höchsten Hubes frei geben. Zur Drehung der Kurbelscheibe
f dient die Kurbel l
mittels der Triebräder m und n, sowie das Schwungrad o, die Kraft des
Stoſses wird wesentlich durch die Feder p und eine
andere in der Abbildung verdeckte Feder verstärkt. Die Anspannung der Springfeder
p verursacht der Spannstift q bei der Drehung der Kurbelscheibe f.
Ein Vorschub nach unten wird durch eine in der Zeichnung nicht sichtbare
Federvorrichtung bewirkt, welche die Vorschubschraube r
in Bewegung setzt. Die Vorschubschraube r läſst sich
durch den Handgriff s von der Zahnstange t abziehen, worauf eine ungehinderte Auf- und
Abbewegung des Rahmens u auf der Zahnstange ermöglicht
ist.
Die Bohrspindel erhält dadurch eine umsetzende Bewegung, daſs das auf derselben
festsitzende Zahnrad v über die Führung w gehoben, darauf durch eine Federvorrichtung x um einige Zähne gedreht wird, worauf es in etwas
veränderter Seitenstellung an der Führung w
herabgleitet.
Das Bohrgestell y bietet keine besonderen
Eigenthümlichkeiten.
Bei dem zweiten dieser Apparate (Fig. 7) ist gerade das
Bohrgerüst a durch die daran angebrachte Bühne b von Bedeutung. Die Bühne kann durch das Gegengewicht
c gehoben werden, während die in das Sperrrad d eingreifende Sperrklinke e zu deren Feststellung dient. Durch Senkung der Bühne wird der Vorschub
regulirt. Der Bohrmeiſsel f erhält seine Führung durch
die Bühne und das Führungsstück g. Die Stoſskraft
ertheilt der Hammer h, welcher mit der Hand durch das
Kurbelrad i bewegt wird. Ein Umsatz des Bohrmeiſsels
findet bei jedem Schlage durch die das Sperrrad k
anziehende und drehende Schnur l statt.
Ferner ist noch eine amerikanische Gesteinsbohrmaschine für Handbetrieb in jeder
Bohrrichtung zu erwähnen, und zwar die von J. M. Clark
in Massachusetts (Amerikanisches Patent Nr. 296052 vom 81, December 1889), welche
die Stoſskraft von einer die Bohrspindel in einer Hülse umgebenden Spiralfeder
erhält, deren Spannung ein Getriebe bewirkt, während ein anderes Getriebe den Umsatz
des Bohrmeiſsels verursacht.
Eine bemerkenswerthe amerikanische Kohlenbohrmaschine
hat noch W. N. Symington in Brooklyn, New York,
erfunden (Amerikanisches Patent Nr. 313188 vom 29. Oktober 1889), deren
Eigenthümlichkeit darin besteht, daſs eine Treibscheibe, an der seitwärts ein
Meiſselpaar angebracht ist, mittels eines Seiles ohne Ende von einer anderen in der
Bohrhülse gelagerten Treibscheibe Drehung erhält.
Eine französische Gesteinsbohrmaschine von E. Salendre
in Paris hat das Englische Patent Nr. 4471 vom 14. März 1889 erhalten. Die
Einrichtung beruht darauf, daſs eine auf einem Gestelle bewegliche und stellbare Hülse mit innerem
Schraubengewinde in zwei Theilen angefertigt und mit Charnieren versehen ist, so
daſs die mit äuſserem Schraubengewinde versehene Bohrspindel leicht einzubringen und
herauszunehmen geht. Drehung und Vorschub erhält der an der Bohrspindel befestigte
Bohrmeiſsel durch die Handhabung einer Kurbel.
Eine einfache und zweckmäſsige Tiefbohrmaschine für
Drehung mit Wasserspülung bis zu Tiefen von 150m
(Fig. 8)
hat G. S. Bartholomew in Californien erfunden
(Amerikanisches Patent Nr. 417352 vom 17. December 1889). Die Haupteigenthümlichkeit
dieses Apparates beruht in der Einrichtung des Bohrgeräthes. Der Bohrmeiſsel a ist nämlich auſser mit dem hohlen Bohrgestänge b noch mit der kurzen Schutzhülse c fest verbunden. Die Schutzhülse hat den Hauptzweck,
die Bohrlochswand an der Ausströmungsstelle des Spülwassers, wo also der Wasserdruck
am stärksten ist, gegen Ausspülung zu schützen. In vielen Fällen wird dieser Schutz
genügen, um bei günstigem festem Boden die Spülbohrung ohne Verrohrung durchführen
zu können. Auſserdem gibt die Schutzhülse dem Bohrmeiſsel sichere Führung, schützt
denselben gegen Nachfall und beugt Verbiegungen und Brüchen des Bohrgestänges
vor.
Von anderweitigen Einrichtungen ist ferner das Querhaupt d zu erwähnen, das am Seile e hängt, dessen
Ende am Haspel f aufgerollt ist. Durch den Haspel wird
der Vorschub regulirt. Das Querhaupt umfaſst mit den Endflanschen die Führungsbalken
g, wobei die Rollen h
die Reibung mindern. Das Treibrad i nimmt mit einer
inneren Nase bei seiner Drehung den Holländer k, der
sich frei im Spülkopfe l dreht, mit herum. Das Triebrad
m, welches sich auf der viereckigen Welle n frei auf und ab bewegt, wird von dieser gedreht. Die
Welle n erhält die Bewegung durch das Getriebe o, p, q, die Welle r und
die Riemenscheibe s von einer beliebigen
Betriebskraft.
Der Hebel t dient zur Umstellung des Rades p vom Rade q auf das Rad
o, falls eine der Bohrdrehung entgegengesetzte
Bewegung, z.B. zur Befreiung des etwa verklemmten Bohrgeräthes, ausgeführt werden
soll.
Die Druckpumpe u drückt das Spülwasser durch den
Schlauch V nach dem Spülkopfe l und weiter in das Bohrgestänge.
Eine fahrbare Dampf-Seilbohrmaschine für Tiefen bis 200m hat J. W. Miller in Newton Falls, Ohio,
construirt (Amerikanisches Patent Nr. 413407 vom 22. Oktober 1889).
Die Haupteigenthümlichkeit dieser Maschine (Fig. 9), die sich überdies
durch zweckmäſsige und einfache Anordnung aller Theile auszeichnet, liegt in der
besonderen Einrichtung des Vorschubes mittels einer sinnreichen Führung des
Bohrseiles. Das Bohrseil a, an welchem das für das
pennsylvanische Seilbohren übliche Bohrgeräth hängt, ist zunächst über die Rolle b an der Spitze des Bohrgerüstes c, dann unter der Rolle d
her und über die Rolle e nach der Seiltrommel f geleitet. Die Holle d ist excentrisch
an der Scheibe g befestigt, welche auf der Welle h durch die Riemenscheibe i Drehung erhält. Beim Stoſsen wird die Seiltrommel durch Andrücken des
Rades k an den Bremsklotz l mittels des Hebels m festgestellt, während
die Rolle e von selbst in fester Stellung verbleibt.
Die Stöſse erfolgen mit doppelter Geschwindigkeit und mit doppeltem Hube im
Verhältniſs zum Anzüge der Rolle e, weil diese zugleich
auf zwei Theile des Bohrseiles anziehend wirkt und dann die Gesammtlänge beider
Seilstücke gleichzeitig zu Falle bringt. Durch die Rolle e wird das Bohrseil ebenfalls stets in einer für den Anzug durch die Rolle
d günstigen Stellung erhalten.
Zum Nachlassen des Bohrseiles im Verhältnisse zum Bohrfortschritte dient die Schraube
n nebst dem Handgriffe o. Die Annäherung der Rolle e an die
Seiltrommel f bewirkt die doppelte Verlängerung des
Bohrseiles. Sobald die Rolle e den ganzen Weg in der
Richtung zur Seiltrommel ausgeschraubt ist, muſs sie zurückgestellt und ein
entsprechendes Seilstück von der Seiltrommel abgelassen werden.
Zum Fördern des Bohrgeräthes hat man das Rad k von dem Bremsklotze l
mittels des Hebels m abzurücken und an die Stirn der
Frictionsscheibe p anzudrücken.
Zum Löffeln dient der Löffelhaspel q, um welchen das (nicht dargestellte) Löffelseil
gewickelt ist, an dessen äuſserem Ende eine gewöhnliche Sandpumpe hängt. Der Hebel
r stellt nach Bedarf durch Seitwärtsschieben die
auſsere Fläche der Haspelscheibe gegen die Seitenfläche der Frictionsscheibe p an und bewirkt andererseits das Bremsen durch
Andrücken einer Bremsscheibe an einen Bremsklotz. (Beide Theile nicht sichtbar.)
Zwei weitere neue in Amerika erfundene Seilbohrmaschinen zeigen sehr sinnreiche und
brauchbare Einzeleinrichtungen, wenn sie auch keine grundsätzlichen Neuerungen
aufweisen und auch nicht ganz den Ansprüchen an Einfachheit entsprechen. Die eine
ist von V. Wirick in Rochelle, Illinois (Amerikanisches
Patent Nr. 413218 vom 22. Oktober 1889), die andere von F.
B. Peacock in Le Mars, Jowa (Amerikanisches Patent Nr. 416375 vom 3.
December 1889) hergestellt.
Der in Fig. 10
dargestellte Apparat wird von der Firma Merryweather and
Son in Greenwich angefertigt und dient einem besonderen Zwecke. Es kommt
nämlich nicht selten vor, daſs verrohrte Wasserbohrbrunnen, nachdem sie durch einige
wenig ergiebige wasserführende Schichten abgebohrt sind, in gröſserer Tiefe wegen
völligen Wassermangels aufgelassen werden müssen. Es kann dann häufig zweckmäſsig
sein, wenigstens den geringeren Wasservorrath der höheren Schichten zu gewinnen.
Dies ist durch den vorstehenden Bohrapparat erreichbar.
Der Schutzcylinder a wird an dem gewöhnlichen
Bohrgestänge b innerhalb der meist guſseisernen
Verrohrung c bis an die wasserführende Schicht
herabgelassen. Die Federn d gewähren den Cylindern den
erforderlichen Halt. Ein
Rädergetriebe innerhalb des Schutzcylinders überträgt die Drehung des Bohrgestänges
b auf die mit den Stahlspitzen d versehenen Bohrspindeln (zwei oder mehr). Eine
entsprechende Anordnung der Zähne der Triebräder bewirkt auſserdem einen
gleichmäſsigen Vorschub der Bohrspitzen. Es können 60 bis 80 Löcher durch
guſseiserne Röhren von 2 bis 3cm Wandstärke
gebohrt werden, ohne daſs eine Schärfung der Spitzen erforderlich wird, und der
Apparat functionirt nach den bisherigen Erfahrungen bis auf 100m Teufe tadellos. Um die Bohrspitzen aus den
Bohrlöchern zurückzuziehen, bedarf es nur der rückläufigen Drehung des
Bohrgestänges.
Der sehr einfache abessinische Brunnen, wie ihn die englische Firma C. Isler and Co. in London für das Kriegsministerium
herstellt, ist in Fig. 11 abgebildet. Auſser dieser leichtesten Form liefert die genannte
Firma auch noch schwerere Brunnenapparate, die dann für das Einrammen besonderer
Bohrgerüste aus Eisenstangen bedürfen. Dieselbe Vorrichtung, die zum Einrammen der
Brunnenröhren bestimmt ist, kann mich vorkommenden Falls zum Ausziehen der Röhren
benutzt werden.
Die französische Bohrfirma Bourdin Ch.-Ls. in Paris fertigt eigenartiges
Bohrgeräth an, von dem die bemerkenswerthesten Formen in Fig. 12 bis 14 dargestellt
sind.
Fig. 12 zeigt
das Führungsstück, welches zwischen Bohrmeiſsel und Gestänge eingefügt ist und den
Zweck hat, zwischen beiden Stücken eine sichere Verbindung herzustellen, die beim
Drehbohren die Drehung nach beiden Richtungen gestattet und beim Stoſsbohren eine
möglichste Entlastung der Verschraubung gewährt. Es wird beides durch die
schraubenförmig geführten Endflächen des Mutterstückes a und des Vaterstückes b erreicht. Sowohl
beim Drehbohren wie beim Stoſsbohren nehmen diese Flächen die ganze Arbeit auf. Die
Zusammenfügung geschieht, indem der Stift c des
Mutterstückes a durch die cubische Auslassung d des Vaterstückes b
hindurch bis in dessen bezügliches Lager durchgesteckt und alsdann durch die auf dem
mit Gewinde versehenen Stift c sitzende Mutterschraube
e so fest angeschraubt wird, daſs die Endflächen
der Stücke a und b fest an
einander stoſsen. Die Mutterschraube e ist alsdann
sowohl beim Drehen wie beim Stoſsen völlig entlastet. Sie kann fast ganz mit der
Hand fest- und losgeschraubt werden, nur für die letzten bezieh. ersten Umdrehungen
ist die Verwendung eines Schraubenschlüssels erforderlich.
Die Ventilbüchse (Fig. 13) zeigt an der Hülse a den Stift b mit dem Haken c und dem
Griffe d. In der dargestellten Stellung des Stiftes
kann sich die Ventilklappe e nur von unten nach oben
bewegen, wie dies beim Löffeln erforderlich ist. Zum Entleeren der Büchse dreht man
den Stift an dem Griffe herum, wodurch der Haken ebenfalls gedreht wird und derselbe
die Klappe nach unten fallen läſst. Der Ring f
verstärkt den Boden der Büchse. Die Schneide g kommt in
Verbindung mit der Büchse in Gebrauch, wenn das Instrument als Schappe beim Bohren in weichem Boden
functioniren soll.
Das Fanggeräth (Fig.
14) besteht aus der Hülse a, in welcher die
Fanghaken f mit den Armen c gelagert sind. In dem oberen trichterartigen Raume zwischen den
Hakenarmen hat die Kugel d ihre Bahn, während die lange
durch die Hülse führende Schraube e die Kugel vorbewegt
oder frei gibt. Beim Fangen eines im Bohrloche stecken gebliebenen Gegenstandes wird
die Kugel d in den trichterförmigen Theil gethan und
die Schraube e lose eingeschraubt. Die Hakenarme führen
sich alsdann beim Herablassen an den Bohrlochswänden, bis die Hakenspitzen den zu
fangenden Gegenstand erreichen. Die Haken halten sich nunmehr an dem zu hebenden
Körper fest, und bei Linksdrehung der Schraube e am
Gestänge wird die Kugel d vorbewegt, und diese drückt
die Hakenarme fest um den zu hebenden Körper.
Schlieſslich sind noch kleinere Erfindungen anzuführen, und zwar: drei Erdbohrer zum
Vorbohren von Pfostenlöchern u. dgl., der erste von D. B. Mc
Call in Texas (Amerikanisches Patent Nr. 412857 vom 15. Oktober 1889); der
zweite von G. B. Harris in Texas (Amerikanisches Patent
Nr. 413343 vom 22. Oktober 1889); der dritte von E. G.
Stephenson in Texas (Amerikanisches Patent Nr. 414873 vom 12. November
1889); dazu gehörig ein stellbarer Handgriff zum Drehen eines Erdbohrgestänges von
J. N. Devoy in St. Louis (Amerikanisches Patent Nr.
413037 vom 15. Oktober 1889); ferner zwei Erweiterungsbohrer, der erste von T. Herberg in Minnesota (Amerikanisches Patent Nr.
414411 vom 5. November 1889); der zweite von E. M.
Brown in Jowa (Amerikanisches Patent Nr. 415610 vom 19. November 1889);
auſserdem drei Verbesserungen an Löffelhaspeln, und zwar die erste, die auch mit
anderweitigen Vervollkommnungen der pennsylvanischen Seilbohrmaschine verbunden ist,
von G. Corbett in Pennsylvanien (Amerikanisches Patent
Nr. 412602 vom 8. Oktober 1889), die zweite und dritte von W. Richards in Pennsylvanien (Amerikanische Patente Nr. 413733 vom 29.
Oktober 1889 und Nr. 415925 vom 16. November 1889); dann ein Verrohrungshebeapparat
von J. B. Hill in Chicago (Amerikanisches Patent Nr.
412707 vom 8. Oktober 1889); eine verbesserte Methode zur Einbringung und Abdichtung
verlorener Verrohrungen von A. J. Clark in Olean, New
York (Amerikanisches Patent Nr. 411886 vom 1. Oktober 1889); schlieſslich ein
Brunnenreinigungsapparat von A. M. Taylor in Michigan
(Amerikanisches Patent Nr. 412211 vom 1. Oktober 1889).
Die Saxl-Blumencron'sche Erfindung (vgl. 1889 276 256) hat das D. R. P. Nr. 52337 vom 14. Juni 1889
erhalten.
Ein Bohrdiamant von ungewöhnlicher Gröſse ist im December 1889 von Brasilien nach New
York geliefert, Derselbe wiegt 367⅓ Karat und hat eine Länge von 5cm. Sein Werth stellt sich über 20000 M. Er ist
mattschwarz und unpolirbar, so daſs seine Verwendung als Schmuck ausgeschlossen ist;
leider muſs man ihn in etwa 150 Stückezertheilen, um ihn zum Bohren benutzen zu
können, so daſs auch seine Gröſse nicht zur vollen Geltung kommt.
Zum Schlusse sei noch mitgetheilt, daſs ein deutscher Landsmann Namens Heerdegen in Ruſsland und Amerika mittels eines von ihm
erfundenen, aber geheim gehaltenen und nicht patentirten elektrotechnischen
Apparates Quellen auf 1000m Tiefe von der
Erdoberfläche aus entdeckt haben soll. Das Weitere ist für Interessenten im
The
Engineering and Mining Journal vom 9. März 1890
nachzulesen.
Tafeln
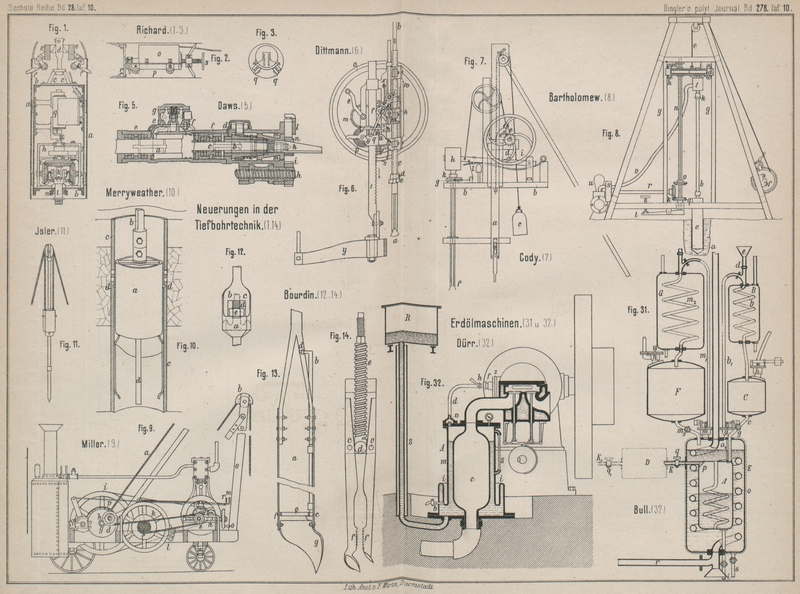