Titel: | Basteiofen mit Gasfeuerung zur Massenproduction von Kalk, Gyps, gebranntem Thon, zum Rösten der Erze &c.; von Ferdinand Steinmann, Civilingenieur in Dresden. |
Autor: | Ferdinand Steinmann |
Fundstelle: | Band 220, Jahrgang 1876, Nr. , S. 151 |
Download: | XML |
Basteiofen mit Gasfeuerung
zur Massenproduction von Kalk, Gyps, gebranntem Thon, zum Rösten der
Erze &c.; von Ferdinand Steinmann, Civilingenieur in Dresden.
Mit Abbildungen auf Taf. II [d/4].
Steinmann's Basteiofen mit
Gasfeuerung.
In richtiger Erkenntniß ihrer außerordentlichen Vortheile hat die
Gasfeuerung zum Zwecke der Kalk- und Kohlensäuregewinnung bei
der Zuckerfabrikation rasch Eingang gefunden, und wird es
wenigstens in Deutschland und Oesterreich nur noch eine geringe
Zahl von Zuckerfabriken geben, welche diese wichtige
Verbesserung an ihren Saturationsöfen noch nicht eingeführt
haben.
Leider kann man dasselbe von den Kalkbrennereien etc. nicht
behaupten, trotzdem gerade für Schachtöfen die Gasfeuerung wegen
der eminent einfachen Constructionselemente die meisten Chancen
bietet. Und doch ist wohl in neuerer Zeit bei keiner
Hüttenbranche das Bedürfniß nach größerer Oekonomie im
Brennstoffverbrauch so sehr in den Vordergrund getreten, als
gerade hier, wo das Rohproduct den relativ geringsten Werth hat,
und die Erzeugung der Waare lediglich nur von dem Preise und der
Qualität des Brennstoffes, welcher obendrein stets der beste
sein soll, abhängig gemacht ist. Die ausschließliche Verwendung
geringwerthiger Brennstoffe verbietet sich von selbst, nicht
allein wegen der erforderlichen großen Mengen, sondern auch
wegen der mit ihrer Benützung verbundenen Gefahr, einen
schlechten Brand zu erzielen. Die mit Holz brennenden
Kalkofenbesitzer vermögen aber wegen der bedeutend gestiegenen
Holzpreise schon seit lange nicht mehr mit denjenigen zu
concurriren, denen Kohle oder Torf zur Verfügung steht. Daher
kommt es auch, daß es jenen Orten, wo Kalkstein und gute Kohle
vereint auftreten, möglich ist, ihr vergängliches, ja für den
Transport gefährliches Product thatsächlich bis auf 50 deutsche
Meilen im Umkreise abzusetzen.
Die Kalkbrennerei ist aber auch eine der größten industriellen
Landplagen; ein einziger Kalkofen mit directer Feuerung
verpestet bekanntlich meilenweit seine Umgebung und stellt
häufig genug den landwirthschaftlichen Betrieb der Anwohner in
Frage.
Alle diese Uebelstände werden durch die Gasfeuerung vollständig
und gründlich beseitigt, denn diese gestattet:
1) die Anwendung eines jeden
Brennstoffes;
2) ist die Rauchverzehrung eine vollständige, woraus auch resultirt,
daß
3) je nach der Qualität des Kalksteines und
des Brennstoffes nur 25 bis 40 Proc. des letztern (auf 100 Th.
Aetzkalk) erfordert werden, während Kalköfen mit directer
Feuerung 60 bis 100 Proc. consumiren;
4) belästigt ein Schachtofen mit
Gasfeuerung die Nachbarschaft in keiner Weise;
5) ist das gewonnene Product vollkommen
frei von Asche und Schlacken; dazu kommt auch, daß der bei
Gasfeuer gebrannte Kalk notorisch transportfähiger, daher sein
Handelswerth ein größerer ist1 ;
6) ist der Betrieb für die Brenner ein weit
weniger anstrengender und gesundheitsnachtheiliger;
7) kommt der Bedarf an Holz gänzlich in
Wegfall, und
8) kann man die maximale Leistung eines
solchen Ofens mindestens auf 30 Proc. ohne jede Benachtheiligung
verringern, ein erheblicher Vortheil für jeden Brenner bei
Beginn oder Beendigung der Bausaison, überhaupt bei jedweder
Schwankung der Conjunctur.
Der Umstand nun, daß sich bei Schachtöfen die Gasflamme ganz
vorzugsweise in verticaler Richtung entwickelt, so zwar, daß man
sie leicht auf eine Länge von 9 bis 10m
ziehen kann, ergab für mich bei meinen diesbezüglich
angestellten praktischen Untersuchungen für Schachtöfen mit
kreisrundem Querschnitte das Maß von 1m,57
als den größten zulässigen Durchmesser. Solche Kalköfen
entsprechen einer maximalen Ausbeute von 100 Ctr. Aetzkalk in 24
Stunden.2
Hieraus erhellt, daß Oefen mit größerer Leistungsfähigkeit einen
oblongen Querschnitt mit einer constanten kleinen Achse von 1m,57
erhalten müssen; solche Oefen bis zu einer maximalen Production
von 350 Ctr. habe ich selbst in größerer Anzahl erbaut.
Abgesehen von dem sich potenzirenden schädlichen Einflusse der
Winde auf die Breitseiten oblonger Oefen vermehren sich auch mit
zunehmender Größe dieser Oefen die constructiven Schwierigkeiten
besonders wegen der Anlage der Generator-Batterien, und kam ich
daher auf die Construction des in Fig. 19
und 20
dargestellten Basteiofens, welcher
ähnlich wie der Hoffmann-Licht'sche Ringofen ohne wesentliche
Modificationen auf jede Leistungshöhe veranlagt werden kann.
So anerkannt vortreffliche Dienste der letztgenannte Ofen in der
Ziegelfabrikation leistet, so sind seine Schwächen beim Brennen
anderer Materialien hinlänglich bekannt, und ich habe zum
Unterschied und im Hinblick auf eine unverkennbare Aehnlichkeit
meinem Ofen den Namen “Basteiofen„ beigelegt. Zur
Erläuterung der Abbildungen diene Folgendes.
a a ist der ringförmige Schacht, in
welchem der Brand des Rohproductes sich vollzieht, b b die sich anschließende Rast, in
welcher das fertig gebrannte Material liegt, g die Gaserzeuger oder Generatoren, f die Gasableitung, e die Zweigcanäle, d die Ringcanäle, aus denen in
entsprechender Vertheilung die Düsen c aus der ganzen Pheripherie in den Schacht einmünden, i sind die mit einem scharfgebrannten
Chamotteconus verschließbaren Abzüge für das Brenngut. Den Conus
dirigirt man mittels eines Hebels in der Weise, daß man je nach
dem größern oder geringern Bedarf an Verbrennungsluft, welche
eben ihren Weg durch i zu nehmen
hat, denselben mehr oder weniger scharf anpreßt. Um einer
vorzeitigen Abnützung der Passagen i
vorzubeugen, sind diese, wie Figur 19
zeigt, mit starken gußeisernen Trichtern ausgefüttert. Die
Verbrennungsluft nimmt Wärme aus dem in der Rast b stehenden Brenngute auf und vereinigt
sich stürmisch mit dem den Düsen entströmenden Gase zur Flamme.
Sie erfüllt also gleichzeitig zwei Zwecke; sie heizt sich selbst
vor und entzieht damit dem Brenngute die hohe Temperatur, so daß
dieses ohne weiteres verladungsfähig ist.
Unter den 6 Einfahrten h gelangt man
nach dem innern Raume m, welcher als
Stapelplatz für das Rohproduct dienen kann, von wo aus letzteres
durch geeignete, von dem Podium l
aus betriebene Hebevorrichtungen bequem und schnell nach der
Gicht befördert werden kann. Die Passagen oder Trichter i sind übrigens durch sattelförmige
Schiede von einander getrennt, so daß damit ein constantes
Rollen des Brenngutes nach links und rechts ermöglicht wird.
Der abgebildete Ofen ist leicht auf eine Production von 1500 Ctr.
Aetzkalk pro 24 Stunden zu bringen. Da, wo es etwa die
Oertlichkeit erheischt, ist natürlich die kreisrunde Form des
Ofens unbedenklich durch eine elliptische zu ersetzen.
Zur Inbetriebsetzung eines derartigen Basteiofens sei
Nachstehendes bemerkt.
Bevor der Schacht mit Kalkstein gefüllt wird, muß man alle Theile
des Ofens, also Generatoren, Canalsystem und Schacht mehrere
Tage hindurch mittels gelinder Schmauchfeuer behufs Austrocknung
ausheizen. Es ist dies bei Gasfeuerungsanlagen um so
nothwendiger, weil andern Falls die Entzündung des Gasstromes
nicht allein schwierig, sondern unter Umständen
sogar unmöglich wird. Hat man die Ueberzeugung gewonnen, daß das
Mauerwerk auf ungefähr 300mm Tiefe trocken ist, so belegt man
zuvörderst den Boden der Rast, d. h. die Sättel, kreuzweis mit
einer Schicht trockenen Holzes, darauf schüttet man ca. 300 bis
500mm hoch Kohle oder Torf, alsdann die erste Schicht
Kalkstein in gleicher Höhe, und fährt mit dem Wechsel von Kohle
und Kalkstein in gleicher Weise fort, bis etwa 600mm
über die Gasdüsen hinaus, von wo ab der Schacht bis zur
Gichtmündung ausschließlich mit Stein gefüllt werden kann.
Innerhalb dieser Zeit sind auch die Generatoren zu beschicken.
Man breitet zu dem Ende erst eine Schicht Hobelspäne auf den
Planrosten aus, legt darauf eine Lage gespaltenen Scheitholzes
und beschütttet dieselbe bis zum Rande der Zargen mit dem zu
verwendenden Brennmaterial. Bevor man das Feuer in den
Generatoren in Gang bringt, muß die Glut in dem Schachte bereits
die untern Schaubüchsen erreicht haben, denn nur dann wird die
Entzündung des Gases eine zweifellose und constante sein. Das
erste Kalkziehen hat spätestens 3 Stunden nach Zutritt des Gases
zur Gicht zu beginnen und von da an, je nach dem Bedarf an Kalk,
in Pausen von nicht unter 1½ und nicht über 3 Stunden
möglichst rasch nach einem bestimmten Maße zu erfolgen; nach
einem jeden Abzuge ist bei der Gicht sofort wieder an dem ganzen
Umfange des Ofens Kalkstein nachzufüllen.
Nachschrift. Ein in Pirna bei Dresden
nach diesem System errichteter Röstofen
für Magneteisenstein hat sich ebenfalls ganz vorzüglich
bewährt und in Hinsicht auf Leistungsfähigkeit, Ersparniß an
Brennstoff etc. alle Röstöfen mit directer Feuerung übertroffen,
so daß der Basteiofen auch für Eisenhüttenwerke sich empfehlen
würde.
Tafeln
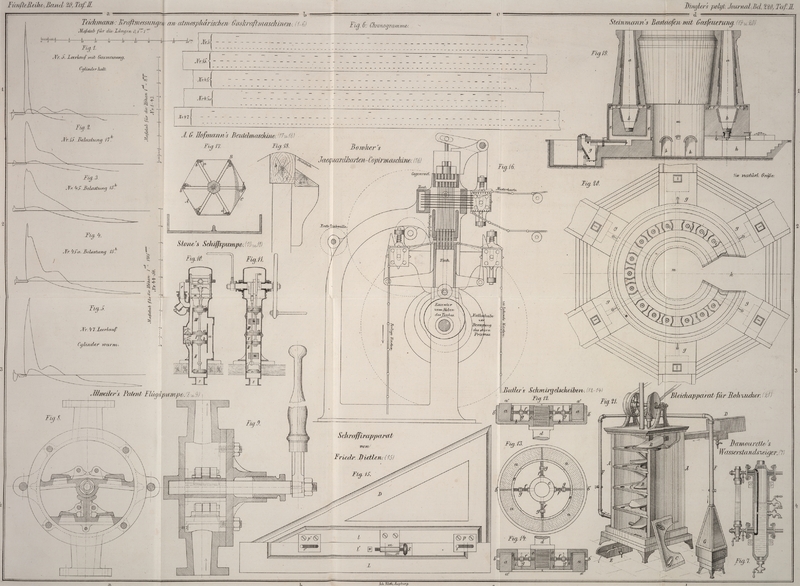